Manufacturing evaluation of seven medical device companies during the production of a 3D-printed titanium pelvic implant
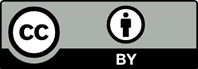
Powder bed fusion (PBF) technology has become a popular manufacturing method to fabricate custom metallic implants. This trend has generated some regulatory concerns because traditional developing guidelines are not suitable for three-dimensional (3D)-printed implants. This is due to the layered microstructure of additive manufactured parts that produces mechanical properties different than those of traditionally manufactured parts. The inappropriate choice of the process parameters and postprocessing methods can lead to fabrication errors that could negatively affect mechanical properties and dimensional accuracy. The objective of the study was to perform a preliminary evaluation of the quality of manufacturing provided by the medical device industry and identify the best 3D printing practices. We designed a pelvic bone reconstructing implant and asked seven companies to manufacture it in Ti6Al4V with PBF technology. We inspected some important aspects of the manufacturing quality of the prototypes received by evaluating geometrical precision and microstructural integrity in the surface and in the matrix, including a qualitative assessment of voids and grain morphology. Results demonstrated a great difference among the implant prototypes. Two companies proved to be superior and provided defect-free implants. The other five produced evidence of some defects including: geometrical deviations (maximum values of up to 5 mm); heterogeneous acicular grain morphologies; broken sections of lattice structures; and internal and superficial voids and cracks that could potentially compromise functional and clinical performance. To our knowledge, this is the first study analyzing the production of several custom implant additive manufacturers based on a geometrical and microstructural evaluation of the same pelvic implant fabrication. The imperfections found in some prototypes produced by companies certified to commercialize personalized implants highlight the urgent need for technical standards that regulate the safe development of 3D-printed implants. Further analyses are required to determine the actual clinical and mechanical consequences of such imperfections. The results also show that when additive manufacturing is adequately managed, it can be a valid manufacturing method to fabricate defect-free implants.
- Villapún VM, Carter LN, Avery S, González-Álvarez A, Andrews JW, Cox S. Stakeholder perspectives on the current and future of additive manufacturing in healthcare. Int J Bioprint. 2022;8(3):586. doi: 10.18063/ijb.v8i3.586
- Food and Drug Administration. Technical Considerations for Additive Manufactured Medical Devices: Guidance for Industry and Food and Drug Administration Staff Document. Center for Devices and Radiological Health. New Hampshire: USA. 2017;1-30. https://www.fda.gov/regulatory-information/search-fda-guidance-documents/technical-considerations-additive-manufactured-medical-devices (accessed on 16 January 2024).
- Gong H, Rafi K, Gu H, Janaki Ram GD, Starr T, Stucker B. Influence of defects on mechanical properties of Ti–6Al– 4V components produced by selective laser melting and electron beam melting. Mater Des. 2015;86:545-554. doi: 10.1016/j.matdes.2015.07.147
- Regulation (EU) 2017/745 of the European Parliament and of the Council of 5 April 2017 on Medical Devices. https://eur-lex.europa.eu/legal-content/EN/TXT/ PDF/?uri=CELEX:32017R0745 (accessed on 6 March 2023).
- ISO 13485:2016, Quality Management Systems. International Organization for Standardization, Geneva, Switzerland. https://www.iso.org/standard/59752.html (accessed on March 6, 2023).
- Chiarini A. Effect of ISO 9001 non-conformity process on cost of poor quality in capital-intensive sectors. Int J Qual Reliab Manag. 2015;32(2):144-155. doi: 10.1108/IJQRM-03-2013-0041
- Wong K-C, Scheinemann P. Additive manufactured metallic implants for orthopaedic applications. Sci China Mater. 2018;61(4):440-454. doi: 10.1007/s40843-017-9243-9
- Hothi H, Henckel J, Bergiers S, Laura AD, Schlueter-Brust K, Hart A. The analysis of defects in custom 3D-printed acetabular cups: A comparative study of commercially available implants from six manufacturers. J Orthop Res. 2022;(October):1-12. doi: 10.1002/jor.25483
- Martinez-Marquez D, Delmar Y, Sun S, Stewart RA. Exploring macroporosity of additively manufactured titanium metamaterials for bone regeneration with quality by design: A systematic literature review. Materials (Basel). 2020;13(21):1-44. doi: 10.3390/ma13214794
- Liu X, Chu PK, Ding C. Surface modification of titanium, titanium alloys, and related materials for biomedical applications. Mater Sci Eng R Rep. 2004;47(3): 49-121. doi: 10.1016/j.mser.2004.11.001
- Gonzalez Alvarez A, Dearn KD, Lawless BM, et al. Design and mechanical evaluation of a novel dynamic growing rod to improve the surgical treatment of early onset scoliosis. Mater Des. 2018;155:334-345. doi: 10.1016/j.matdes.2018.06.008
- Tammas-Williams S, Withers PJ, Todd I, Prangnell PB. The effectiveness of hot isostatic pressing for closing porosity in titanium parts manufactured by selective electron beam melting. Metall Mater Trans A Phys Metall Mater Sci. 2016;47(5):1939-1946. doi: 10.1007/s11661-016-3429-3
- Barrère F, Mahmood TA, de Groot K, van Blitterswijk CA. Advanced biomaterials for skeletal tissue regeneration: Instructive and smart functions. Mater Sci Eng R Rep. 2008;59(1):38-71. doi: 10.1016/j.mser.2007.12.001
- Suska F, Kjeller G, Tarnow P, et al. Electron beam melting manufacturing technology for individually manufactured jaw prosthesis: A case report. J Oral Maxillofac Surg. 2016;74(8):1706.e1-1706.e15. doi: 10.1016/j.joms.2016.03.046
- Martinez-Marquez D, Mirnajafizadeh A, Carty CP, Stewart RA. Application of quality by design for 3D printed bone prostheses and scaffolds. PLoS ONE. 2018;13(4):1-47. doi: 10.1371/journal.pone.0195291
- Van Hooreweder B, Moens D, Boonen R, Kruth JP, Sas P. Analysis of fracture toughness and crack propagation of Ti6Al4V produced by selective laser melting. Adv Eng Mater. 2012;14(1–2):92-97. doi: 10.1002/adem.201100233
- Vrancken B, Thijs L, Kruth JP, Humbeeck JV. Heat treatment of Ti6Al4V produced by selective laser melting: microstructure and mechanical properties. J Alloys Compd. 2012;541:177-185. doi: 10.1016/j.jallcom.2012.07.022
- Vilaro T, Colin C, Bartout D. As-fabricated and heat-treated microstructures of the Ti-6Al-4V alloy processed by selective laser melting. Metall Mater Trans A. 2011;42(10):3190-3199. doi: 10.1007/s11661-011-0731-y
- Li SJ, Murr LE, Cheng XY, et al. Compression fatigue behavior of Ti-6Al-4V mesh arrays fabricated by electron beam melting. Acta Mater. 2012;60(3):793-802. doi: 10.1016/j.actamat.2011.10.051
- Fotovvati B, Namdari N, Dehghanghadikolaei A. Fatigue performance of selective laser melted Ti6Al4V components: State of the art. Mater Res Express. 2019;6(1):012002. doi: 10.1088/2053-1591/aae10e
- Vaneker T, Bernard A, Moroni G, Gibson I, Zhang Y. Design for additive manufacturing: Framework and methodology. CIRP Ann. 2020;69(2):578-599. doi: 10.1016/j.cirp.2020.05.006
- Coelho PG, Hollister SJ, Flanagan CL, Fernandes PR. Bioresorbable scaffolds for bone tissue engineering: Optimal design, fabrication, mechanical testing and scale-size effects analysis. Med Eng Phys. 2015;37(3):287-296. doi: 10.1016/j.medengphy.2015.01.004
- Kingsak M, Maturavongsadit P, Jiang H, Wang Q. Cellular responses to nanoscale substrate topography of TiO2 nanotube arrays: cell morphology and adhesion. Biomater Transl. 2022;3(3):221-233. doi: 10.12336/biomatertransl.2022.03.006
- Liu QC, Elambasseril J, Sun SJ, Leary M, Brandt M, Sharp PK. The effect of manufacturing defects on the fatigue behaviour of Ti-6Al-4V specimens fabricated using selective laser melting. Adv Mater Res. 2014;891–892:1519-1524. doi: 10.4028/www.scientific.net/AMR.891-892.1519
- Seth P, Jha JS, Alankar A, Mishra SK. Alpha-case formation in Ti–6Al–4V in a different oxidizing environment and its effect on tensile and fatigue crack growth behavior. Oxid Met. 2022;97(1–2):77-95. doi: 10.1007/s11085-021-10079-y
- Lee YS, Cho S, Ji C, Jo I, Choi M. Impact of morphology on the high cycle fatigue behavior of Ti-6Al-4V for aerospace. Metals (Basel). 2022;12(10):1722. doi: 10.3390/met12101722
- Xu W, Sun S, Elambasseril J, Liu Q, Brandt M, Qian M. Ti- 6Al-4V additively manufactured by selective laser melting with superior mechanical properties. JOM. 2015;67(3): 668-673. doi: 10.1007/s11837-015-1297-8
- Bertsch KM, Voisin T, Forien JB, et al. Critical differences between electron beam melted and selective laser melted Ti- 6Al-4 V. Mater Des. 2022;216:110533. doi: 10.1016/j.matdes.2022.110533
- Wu GQ, Shi CL, Sha W, Sha AX, Jiang HR. Effect of microstructure on the fatigue properties of Ti-6Al-4V titanium alloys. Mater Des. 2013;46:668-674. doi: 10.1016/j.matdes.2012.10.059
- Frkan M, Konecna R, Nicoletto G, Kunz L. Microstructure and fatigue performance of SLM-fabricated Ti6Al4V alloy after different stress-relief heat treatments. Transp Res Procedia. 2019;40(1):24-29. doi: 10.1016/j.trpro.2019.07.005
- Ran J, Jiang F, Sun X, Chen Z, Tian C, Zhao H. Microstructure and mechanical properties of ti-6al-4v fabricated by electron beam melting. Crystals. 2020;10(11):1-18. doi: 10.3390/cryst10110972
- Gonzalez Alvarez A, Dovgalski L, Evans PL, Key S. Development and surgical application of a custom implant that enables a vertical vector of mandibular distraction. Proc Inst Mech Eng H. 2020;234(10):1172-1180. doi: 10.1177/0954411920940848
- Gonzalez Alvarez A, Evans PL, Dovgalski L, Goldsmith I. Design, additive manufacture and clinical application of a patient-specific titanium implant to anatomically reconstruct a large chest wall defect. Rapid Prototyp J. 2021;27(2): 304-310. doi: 10.1108/RPJ-08-2019-0208
- Gonzalez Alvarez A, Ananth S, Dovgalski L, Evans PL. Custom three-dimensional printed orbital plate composed of two joined parts with variable thickness for a large orbital floor reconstruction after post-traumatic zygomatic fixation. Br J Oral Maxillofac Surg. 2020;58(10):e341-e342. doi: 10.1016/j.bjoms.2020.08.082
- Contaldi V, Corrado P, Del Re F, et al. Direct metal laser sintering of Ti-6Al-4V parts with reused powder. Int J Adv Manuf Technol. 2022;120(1–2):1013-1021. doi: 10.1007/s00170-022-08807-y
- Emminghaus N, Bernhard R, Hermsdorf J, Kaierle S. Residual oxygen content and powder recycling: Effects on microstructure and mechanical properties of additively manufactured Ti-6Al-4V parts. Int J Adv Manuf Technol. 2022; 121(5–6):3685-3701. doi: 10.1007/s00170-022-09503-7