A review on development of eco-friendly natural fiber-reinforced composite filaments for 3D printing: Fabrication and characteristics
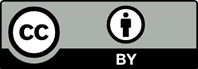
Additive manufacturing (AM), commonly referred to as 3D printing, has revolutionized the modern manufacturing world by providing comprehensive benefits in terms of mass customization, automation, design optimization, quick prototyping, and reduced lead times among other factors. Given the increased popularity, rapid development, and implementation of AM technologies in numerous engineering applications, new methods to enhance the AM process for improved efficiency and to attain sustainability goals are being considered. One approach to achieve sustainability in AM is by considering greener input materials such as natural fiber-reinforced composite filaments (NFRCFs) with lower embodied energy. This review focuses on the latest advancements made in the research and development of advanced NFRCFs for the AM process. In the first section, the rationale of using natural fibers in modern NFRCFs is outlined, followed by a description of the key stages of their fabrication process involving the pre-processing of fibers and the addition of plasticizer to enhance their performance. In the second part of this review, a detailed overview of the typical fibers and matrices used in the development of NFRCFs is provided, and some of the typical challenges encountered when utilizing natural fibers, such as their lack of homogeneity, are highlighted. The fiber-matrix interaction and corresponding properties are further discussed, and means to achieve homogeneous NFRC filament are outlined. Finally, the degradability characteristics and recycling methods for NFRCF are discussed, and further means to optimize their performance for increased usage in AM and related applications are presented. To address and overcome the foregoing limitations posed by present-day NFRCF, further research for breakthrough solutions is still required. Further research and development in this area is a prerequisite to attain sustainability in AM, which will also promote the usage and integration of sustainable AM parts into a wider range of engineering applications in our modern society.

- Sangkert S, Kamolmatyakul S, Gelinsky M, Meesane J. 3D printed scaffolds of alginate/polyvinylalcohol with silk fibroin based on mimicked extracellular matrix for bone tissue engineering in maxillofacial surgery. Mater Today Commun. 2021;26:102140. doi: 10.1016/j.mtcomm.2021.102140
- Aati S, Akram Z, Ngo H, Fawzy AS. Development of 3D printed resin reinforced with modified ZrO2 nanoparticles for long-term provisional dental restorations. Dent Mater. 2021;37(6):e360-e374. doi: 10.1016/j.dental.2021.02.010
- Alshaer AW, Harland DJ. An investigation of the strength and stiffness of weight-saving sandwich beams with CFRP face sheets and seven 3D printed cores. Compos Struct. 2021;257:113391. doi: 10.1016/j.compstruct.2020.113391
- Berde NN, Sanap SB, Thorat SG. Study of impact and fatigue on 3D printed composites. Mater Today Proc. 2021;47:2376-2378. doi: 10.1016/j.matpr.2021.04.330
- Schuldt SJ, Jagoda JA, Hoisington AJ, Delorit JD. A systematic review and analysis of the viability of 3D-printed construction in remote environments. Autom Constr. 2021;125:103642. doi: 10.1016/j.autcon.2021.103642
- Ramful R. A Paradigm shift towards sustainable production with additive manufacturing in the industry 4.0 era. In: Fowdur TP, Milovanovic DA, Bojkovic ZS, editors. Intelligent and Sustainable Engineering Systems for Industry 4.0 and Beyond. United States: CRC Press; 2025. p. 92-116.
- Sun Y, Tian W, Zhang T, Chen P, Li M. Strength and toughness enhancement in 3d printing via bioinspired tool path. Mater Des. 2020;185:108239. doi: 10.1016/j.matdes.2019.108239
- Compton BG, Lewis JA. 3D‐printing of lightweight cellular composites. Adv Mater. 2014;26(34):5930-5935. doi: 10.1002/adma.201401804
- Gu GX, Takaffoli M, Hsieh AJ, Buehler MJ. Biomimetic additive manufactured polymer composites for improved impact resistance. Extreme Mech Lett. 2016;9:317-323. doi: 10.1016/j.eml.2016.09.006
- Gu GX, Takaffoli M, Buehler MJ. Hierarchically enhanced impact resistance of bioinspired composites. Adv Mater. 2017;29(28):1700060. doi: 10.1002/adma.201700060
- Podroužek J, Marcon M, Ninčević K, Wan-Wendner R. Bio-inspired 3d infill patterns for additive manufacturing and structural applications. Materials (Basel). 2019;12(3):499.doi: 10.3390/ma12030499
- Chen BC, Zou M, Liu GM, Song JF, Wang HX. Experimental study on energy absorption of bionic tubes inspired by bamboo structures under axial crushing. Int J Impact Eng. 2018;115:48-57. doi: 10.1016/j.ijimpeng.2018.01.005
- Zhang T, Wang A, Wang Q, Guan F. Bending characteristics analysis and lightweight design of a bionic beam inspired by bamboo structures. Thin Walled Struct. 2019;142:476-498. doi: 10.1016/j.tws.2019.04.043
- Jiang H, Ziegler H, Zhang Z, Meng H, Chronopoulos D, Chen Y. Mechanical properties of 3D printed architected polymer foams under large deformation. Mater Des. 2020;194:108946. doi: 10.1016/j.matdes.2020.108946
- Xu Y, Zhang H, Šavija B, Chaves Figueiredo S, Schlangen E. Deformation and fracture of 3D printed disordered lattice materials: Experiments and modeling. Mater Des. 2019;162:143-153. doi: 10.1016/j.matdes.2018.11.047
- Chen Y, Li T, Jia Z, Scarpa F, Yao CW, Wang L. 3D printed hierarchical honeycombs with shape integrity under large compressive deformations. Mater Des. 2018;137:226-234. doi: 10.1016/j.matdes.2017.10.028
- Martens P, Mathot M, Bos F, Coenders J. Optimising 3D printed concrete structures using topology optimisation. In: High Tech Concrete: Where Technology and Engineering Meet. Berlin, Germany: Springer International Publishing; 2018. p. 301-309. doi: 10.1007/978-3-319-59471-2_37
- Chen Y, Veer F, Çopuroğlu O. A critical review of 3D concrete printing as a low Co2 concrete approach. Heron. 2017;62:167-194.
- Wolfs RJM, Bos FP, Salet TAM. Hardened properties of 3D printed concrete: The influence of process parameters on interlayer adhesion. Cem Concr Res. 2019;119:132-140. doi: 10.1016/j.cemconres.2019.02.017
- Nerella VN, Hempel S, Mechtcherine V. Effects of layer-interface properties on mechanical performance of concrete elements produced by extrusion-based 3D-printing. Constr Build Mater. 2019;205:586-601. doi: 10.1016/j.conbuildmat.2019.01.235
- Heras Murcia D, Genedy M, Reda Taha MM. Examining the significance of infill printing pattern on the anisotropy of 3D printed concrete. Constr Build Mater. 2020;262:120559. doi: 10.1016/j.conbuildmat.2020.120559
- Nurhudan AI, Supriadi S, Whulanza Y, Saragih AS. Additive manufacturing of metallic based on extrusion process: A review. J Manuf Process. 2021;66:228-237. doi: 10.1016/j.jmapro.2021.04.018
- Lvov VA, Senatov FS, Stepashkin AA, Veveris AA, Pavlov MD, Komissarov AA. Low-cycle fatigue behavior of 3D-printed metallic auxetic structure. Mater Today Proc. 2020;33:1979-1983. doi: 10.1016/j.matpr.2020.06.130
- Shahrubudin N, Lee TC, Ramlan R. An overview on 3D printing technology: Technological, materials, and applications. Procedia Manuf. 2019;35:1286-1296. doi: 10.1016/j.promfg.2019.06.089
- Caminero M, Chacón J, García-Plaza E, Núñez P, Reverte J, Becar J. Additive manufacturing of PLA-based composites using fused filament fabrication: Effect of graphene nanoplatelet reinforcement on mechanical properties, dimensional accuracy and texture. Polymers (Basel). 2019;11(5):799. doi: 10.3390/polym11050799
- Cicala G, Giordano D, Tosto C, Filippone G, Recca A, Blanco I. Polylactide (PLA) filaments a biobased solution for additive manufacturing: Correlating rheology and thermomechanical properties with printing quality. Materials (Basel). 2018;11(7):1191. doi: 10.3390/ma11071191
- Camargo JC, Machado ÁR, Almeida EC, Silva EFMS. Mechanical properties of PLA-graphene filament for FDM 3D printing. Int J Adv Manuf Technol. 2019;103(5-8):2423-2443. doi: 10.1007/s00170-019-03532-5
- Novaković D, Kašiković N, Vladić G, Pál M. Screen printing. In: Printing on Polymers. Amsterdam, Netherlands: Elsevier; 2016. p. 247-261. doi: 10.1016/B978-0-323-37468-2.00015-4
- Srivatsan TS, Sudarshan TS, editors. Additive Manufacturing: Innovations, Advances, and Applications. United States: CRC Press; 2015. doi: 10.1201/b19360
- Wojtyła S, Klama P, Baran T. Is 3D printing safe? Analysis of the thermal treatment of thermoplastics: ABS, PLA, PET, and nylon. J Occup Environ Hyg. 2017;14(6):D80-D85. doi: 10.1080/15459624.2017.1285489
- El Magri A, Ouassil S, Vaudreuil S. Effects of printing parameters on the tensile behavior of 3D-printed Acrylonitrile Styrene Acrylate (ASA) material in Z direction. Polym Eng Sci. 2022;62(3):848-860. doi: 10.1002/pen.25891
- Harris CG, Jursik NJS, Rochefort WE, Walker TW. Additive manufacturing with soft TPU - adhesion strength in multimaterial flexible joints. Front Mech Eng. 2019;5:37. doi: 10.3389/fmech.2019.00037
- Rohde S, Cantrell J, Jerez A, et al. Experimental characterization of the shear properties of 3D-printed abs and polycarbonate parts. Exp Mech. 2018;58(6):871-884. doi: 10.1007/s11340-017-0343-6
- Ekinci A, Johnson AA, Gleadall A, Engstrøm DS, Han X. Layer-dependent properties of material extruded biodegradable polylactic acid. J Mech Behav Biomed Mater. 2020;104:103654. doi: 10.1016/j.jmbbm.2020.103654
- Lee CY, Liu CY. The influence of forced-air cooling on a 3D printed PLA part manufactured by fused filament fabrication. Addit Manuf. 2019;25:196-203. doi: 10.1016/j.addma.2018.11.012
- Mazurchevici SN, Pricop B, Istrate B, et al. Technological parameters effects on mechanical properties of biodegradable materials using FDM. Mater Plast. 2019;57(2):215-227. doi: 10.37358/MP.20.2.5368
- Montalvão GR, Moshrefi-Torbati M, Hamilton A, Machado R, João A. Behaviour of 3D printed PLA and PLA-PHA in marine environments. IOP Conf Ser Earth Environ Sci. 2020;424(1):012013. doi: 10.1088/1755-1315/424/1/012013
- Candal MV, Calafel I, Aranburu N, et al. Thermo-rheological effects on successful 3D printing of biodegradable polyesters. Addit Manuf. 2020;36:101408. doi: 10.1016/j.addma.2020.101408
- Backes EH, Harb SV, Beatrice CAG, et al. Polycaprolactone usage in additive manufacturing strategies for tissue engineering applications: A review. J Biomed Mater Res B Appl Biomater. 2022;110(6):1479-1503. doi: 10.1002/jbm.b.34997
- Suiker ASJ. Mechanical performance of wall structures in 3D printing processes: Theory, design tools and experiments. Int J Mech Sci. 2018;137:145-170. doi: 10.1016/j.ijmecsci.2018.01.010
- Paul SC, Tay YWD, Panda B, Tan MJ. Fresh and hardened properties of 3D printable cementitious materials for building and construction. Arch Civil Mech Engineering. 2018;18(1):311-319. doi: 10.1016/j.acme.2017.02.008
- Ramful R. Mechanical performance and durability attributes of biodegradable natural fibre-reinforced composites-a review. J Mater Sci Mater Eng. 2024;19(1):50. doi: 10.1186/s40712-024-00198-0
- Kabir MM, Wang H, Lau KT, Cardona F. Chemical treatments on plant-based natural fibre reinforced polymer composites: An overview. Compos B Eng. 2012;43(7):2883-2892. doi: 10.1016/j.compositesb.2012.04.053
- Ho MP, Wang H, Lee JH, et al. Critical factors on manufacturing processes of natural fibre composites. Compos B Eng. 2012;43(8):3549-3562. doi: 10.1016/j.compositesb.2011.10.001
- Shao Z, Wang F. Mechanical characteristics of bamboo structure and its components. In: The Fracture Mechanics of Plant Materials. Singapore: Springer; 2018. p. 125-146. doi: 10.1007/978-981-10-9017-2_7
- Shao Z, Wang F. Transverse fracture of wood. In: The Fracture Mechanics of Plant Materials. Singapore: Springer; 2018. p. 63-86. doi: 10.1007/978-981-10-9017-2_4
- Siakeng R, Jawaid M, Ariffin H, Sapuan SM, Asim M, Saba N. Natural fiber reinforced polylactic acid composites: A review. Polym Compos. 2019;40(2):446-463. doi: 10.1002/pc.24747
- Al Faruque MA, Salauddin M, Raihan MM, Chowdhury IZ, Ahmed F, Shimo SS. Bast fiber reinforced green polymer composites: A review on their classification, properties, and applications. J Nat Fiber. 2022;19(14):8006-8021. doi: 10.1080/15440478.2021.1958431
- Aida HJ, Nadlene R, Mastura MT, Yusriah L, Sivakumar D, Ilyas RA. Natural fibre filament for Fused Deposition Modelling (FDM): A review. Int J Sustain Eng. 2021; 14(6):1988-2008. doi: 10.1080/19397038.2021.1962426
- Dittenber DB, GangaRao HVS. Critical review of recent publications on use of natural composites in infrastructure. Compos A Appl Sci Manuf. 2012;43(8):1419-1429. doi: 10.1016/j.compositesa.2011.11.019
- Awais H, Nawab Y, Amjad A, Anjang A, Md Akil H, Zainol Abidin MS. Environmental benign natural fibre reinforced thermoplastic composites: A review. Compos C Open Access. 2021;4:100082. doi: 10.1016/j.jcomc.2020.100082
- Reddy MSB, Ponnamma D, Choudhary R, Sadasivuni KK. A comparative review of natural and synthetic biopolymer composite scaffolds. Polymers (Basel). 2021;13(7):1105. doi: 10.3390/polym13071105
- Ghori SW, Siakeng R, Rasheed M, Saba N, Jawaid M. The role of advanced polymer materials in aerospace. In: Sustainable Composites for Aerospace Applications. Amsterdam, Netherlands: Elsevier; 2018. p. 19-34. doi: 10.1016/B978-0-08-102131-6.00002-5
- Dorigato A. Recycling of thermosetting composites for wind blade application. Adv Ind Eng Polym Res. 2021;4(2):116-132. doi: 10.1016/j.aiepr.2021.02.002
- Hubbe MA, Lavoine N, Lucia LA, Dou C. Formulating bioplastic composites for biodegradability, recycling, and performance: A review. Bioresources. 2020;16(1):2021-2083. doi: 10.15376/biores.16.1.Hubbe
- Mtibe A, Motloung MP, Bandyopadhyay J, Ray SS. Synthetic biopolymers and their composites: Advantages and limitations-an overview. Macromol Rapid Commun. 2021;42(15):e2100130. doi: 10.1002/marc.202100130
- Moore CJ. Synthetic polymers in the marine environment: A rapidly increasing, long-term threat. Environ Res. 2008;108(2):131-139. doi: 10.1016/j.envres.2008.07.025
- Krauklis AE, Karl CW, Gagani AI, Jørgensen JK. Composite material recycling technology-state-of-the-art and sustainable development for the 2020s. J Compos Sci. 2021;5(1):28. doi: 10.3390/jcs5010028
- Gu JD, Wang YS. Coastal and marine pollution and ecotoxicology. Ecotoxicology. 2015;24(7-8):1407-1410. doi: 10.1007/s10646-015-1528-3
- Muneer Ahmed M, Dhakal HN, Zhang ZY, Barouni A, Zahari R. Enhancement of impact toughness and damage behaviour of natural fibre reinforced composites and their hybrids through novel improvement techniques: A critical review. Compos Struct. 2021;259:113496. doi: 10.1016/j.compstruct.2020.113496
- Dharani Kumar S, Aravindh M, Manoj VK, Madhumithra C, Kaviya P, Yaswanth S. Fracture toughness of bio-fiber reinforced polymer composites- a review. Mater Today Proc. 2023;1-8. doi: 10.1016/j.matpr.2023.01.334
- El-Sayegh S, Romdhane L, Manjikian S. A critical review of 3D printing in construction: Benefits, challenges, and risks. Arch Civil Mech Eng. 2020;20(2):34. doi: 10.1007/s43452-020-00038-w
- Stoof D, Pickering K, Zhang Y. Fused deposition modelling of natural fibre/polylactic acid composites. J Compos Sci. 2017;1(1):8. doi: 10.3390/jcs1010008
- Menčík P, Přikryl R, Stehnová I, et al. Effect of selected commercial plasticizers on mechanical, thermal, and morphological properties of poly (3-hydroxybutyrate)/poly (Lactic Acid)/plasticizer biodegradable blends for three-dimensional (3D) print. Materials (Basel). 2018;11(10):1893. doi: 10.3390/ma11101893
- Singh R, Ranjan N. Experimental investigations for preparation of biocompatible feedstock filament of Fused Deposition Modeling (FDM) using twin screw extrusion process. J Thermoplast Compos Mater. 2018;31(11):1455-1469. doi: 10.1177/0892705717738297
- Wang Q, Ji C, Sun L, Sun J, Liu J. Cellulose nanofibrils filled poly (Lactic Acid) biocomposite filament for FDM 3D printing. Molecules. 2020;25(10):2319. doi: 10.3390/molecules25102319
- Manoj A, Panda RC. Biodegradable filament for 3D printing process: A review. Eng Sci. 2022;18:11-19. doi: 10.30919/es8d616
- Morales MA, Maranon A, Hernandez C, Porras A. Development and characterization of a 3D printed cocoa bean shell filled recycled polypropylene for sustainable composites. Polymers (Basel). 2021;13(18):3162. doi: 10.3390/polym13183162
- Gkartzou E, Koumoulos EP, Charitidis CA. Production and 3D printing processing of bio-based thermoplastic filament. Manuf Rev. 2017;4:1. doi: 10.1051/mfreview/2016020
- Chacón JM, Caminero MÁ, Núñez PJ, García-Plaza E, Bécar JP. Effect of nozzle diameter on mechanical and geometric performance of 3D printed carbon fibre-reinforced composites manufactured by fused filament fabrication. Rapid Prototyp J. 2021;27(4):769-784. doi: 10.1108/RPJ-10-2020-0250
- Xie G, Zhang Y, Lin W. Plasticizer combinations and performance of wood flour-poly (Lactic Acid) 3D printing filaments. Bioresources. 2017;12(3):6736-6748. doi: 10.15376/biores.12.3.6736-6748
- Pakkanen J, Manfredi D, Minetola P, Iuliano L. About the Use of Recycled or Biodegradable Filaments for Sustainability of 3D Printing. In: Sustainable Design and Manufacturing: Proceedings of the 8th International Conference on Sustainable Design and Manufacturing (KES-SDM 2021). Cham: Springer; 2017. p. 776-785. doi: 10.1007/978-3-319-57078-5_73
- Rajendran Royan NR, Leong JS, Chan WN, Tan JR, Shamsuddin ZSB. Current state and challenges of natural fibre-reinforced polymer composites as feeder in FDM-based 3D printing. Polymers (Basel). 2021;13(14):2289. doi: 10.3390/polym13142289
- Tserki V, Panayiotou C, Zafeiropoulos NE. A study of the effect of acetylation and propionylation on the interface of natural fibre biodegradable composites. Adv Compos Lett. 2005;14(2):65-71. doi: 10.1177/096369350501400202
- Ganguly A, Shankar S, Das A, Shukla M, Swaroop C, Bhardwaj T. Natural fibre reinforced composites: A review based on additive manufacturing routes and biodegradability perspective. Mater Today Proc. 2022;62:131-135. doi: 10.1016/j.matpr.2022.02.607
- Zhao DX, Cai X, Shou GZ, Gu YQ, Wang PX. Study on the preparation of bamboo plastic composite intend for additive manufacturing. Key Eng Mater. 2015;667:250-258. doi: 10.4028/www.scientific.net/KEM.667.250
- Gao X, Qi S, Yang B, Su Y, Li J, Wang D. Synergistic effect of plasticizer and nucleating agent on crystallization behavior of polylactide during fused filament fabrication. Polymer. 2021;215:123426. doi: 10.1016/j.polymer.2021.123426
- Osman MA, Atia MRA. Investigation of ABS-rice straw composite feedstock filament for FDM. Rapid Prototyp J. 2018;24(6):1067-1075. doi: 10.1108/RPJ-11-2017-0242
- Depuydt D, Balthazar M, Hendrickx K, et al. Production and characterization of bamboo and flax fiber reinforced polylactic acid filaments for fused deposition modeling (FDM). Polym Compos. 2019;40(5):1951-1963. doi: 10.1002/pc.24971
- Liu H, He H, Peng X, Huang B, Li J. Three‐dimensional printing of poly(lactic acid) bio‐based composites with sugarcane bagasse fiber: Effect of printing orientation on tensile performance. Polym Adv Technol. 2019;30(4):910-922. doi: 10.1002/pat.4524
- Ahmad MN, Wahid MK, Maidin NA, Ab Rahman MH, Osman MH, Alis@Elias IF. Mechanical characteristics of oil palm fiber reinforced thermoplastics as filament for Fused Deposition Modeling (FDM). Adv Manuf. 2020;8(1):72-81. doi: 10.1007/s40436-019-00287-w
- Torrado Perez AR, Roberson DA, Wicker RB. Fracture surface analysis of 3D-Printed tensile specimens of novel ABS-based materials. J Fail Anal Preven. 2014;14(3):343-353. doi: 10.1007/s11668-014-9803-9
- Jahangir MN, Billah KMM, Lin Y, Roberson DA, Wicker RB, Espalin D. Reinforcement of material extrusion 3D printed polycarbonate using continuous carbon fiber. Addit Manuf. 2019;28:354-364. doi: 10.1016/j.addma.2019.05.019
- Bi X, Huang R. 3D printing of natural fiber and composites: A state-of-the-art review. Mater Des. 2022;222:111065. doi: 10.1016/j.matdes.2022.111065
- Xu W, Pranovich A, Uppstu P, et al. Novel biorenewable composite of wood polysaccharide and polylactic acid for three dimensional printing. Carbohydr Polym. 2018;187:51-58. doi: 10.1016/j.carbpol.2018.01.069
- Petchwattana N, Channuan W, Naknaen P, Narupai B. 3D printing filaments prepared from modified poly (Lactic Acid)/teak wood flour composites: An investigation on the particle size effects and silane coupling agent compatibilisation. J Phys Sci. 2019;30(2):169-188. doi: 10.21315/jps2019.30.2.10
- Panda B, Paul SC, Hui LJ, Tay YWD, Tan MJ. Additive manufacturing of geopolymer for sustainable built environment. J Clean Prod. 2017;167:281-288. doi: 10.1016/j.jclepro.2017.08.165
- Xiao J, Liu H, Ding T. Finite element analysis on the anisotropic behavior of 3D printed concrete under compression and flexure. Addit Manuf. 2021;39:101712. doi: 10.1016/j.addma.2020.101712
- Zareiyan B, Khoshnevis B. Interlayer adhesion and strength of structures in contour crafting - effects of aggregate size, extrusion rate, and layer thickness. Autom Constr. 2017;81:112-121. doi: 10.1016/j.autcon.2017.06.013
- Sundar D, Narasimalu S, Yaowen Y, Sharma S. Opportunities for Natural Fiber Reinforced Composites towards Tropical wind Turbine Material Needs. In: 2017 Asian Conference on Energy, Power and Transportation Electrification (ACEPT). IEEE; 2017. p. 1-7. doi: 10.1109/ACEPT.2017.8168549
- Venkateshwaran N, Elayaperumal A, Sathiya GK. Prediction of tensile properties of hybrid-natural fiber composites. Compos B Eng. 2012;43(2):793-796. doi: 10.1016/j.compositesb.2011.08.023
- Filgueira D, Holmen S, Melbø JK, Moldes D, Echtermeyer AT, Chinga-Carrasco G. Enzymatic-assisted modification of thermomechanical pulp fibers to improve the interfacial adhesion with poly(lactic acid) for 3D printing. ACS Sustain Chem Eng. 2017;5(10):9338-9346. doi: 10.1021/acssuschemeng.7b02351
- Nguyen NA, Bowland CC, Naskar AK. A general method to improve 3D-printability and inter-layer adhesion in lignin-based composites. Appl Mater Today. 2018;12:138-152. doi: 10.1016/j.apmt.2018.03.009
- Wang X, Jiang M, Zhou Z, Gou J, Hui D. 3D printing of polymer matrix composites: A review and prospective. Compos B Eng. 2017;110:442-458. doi: 10.1016/j.compositesb.2016.11.034
- Le Duigou A, Barbé A, Guillou E, Castro M. 3D printing of continuous flax fibre reinforced biocomposites for structural applications. Mater Des. 2019;180:107884. doi: 10.1016/j.matdes.2019.107884
- Mazzanti V, Malagutti L, Mollica F. FDM 3D printing of polymers containing natural fillers: A review of their mechanical properties. Polymers (Basel). 2019;11(7):1094. doi: 10.3390/polym11071094
- Ramful R, Shoaib Casseem M. Improving the Flexural Behaviour of Small Clear 3D-Printed PLA Specimens through Generative Design. In: 2023 International Conference on Sustainable Technology and Engineering (i-COSTE). IEEE; 2023. p. 1-5. doi: 10.1109/i-COSTE60462.2023.10500778
- Mukherjee T, Kao N. PLA based biopolymer reinforced with natural fibre: A review. J Polym Environ. 2011;19(3):714-725. doi: 10.1007/s10924-011-0320-6
- Badouard C, Traon F, Denoual C, Mayer-Laigle C, Paës G, Bourmaud A. Exploring mechanical properties of fully compostable flax reinforced composite filaments for 3D printing applications. Ind Crops Prod. 2019;135:246-250. doi: 10.1016/j.indcrop.2019.04.049
- Shalom H, Kapishnikov S, Brumfeld V, Naveh N, Tenne R, Lachman N. Strong, tough and bio-degradable polymer-based 3D-ink for Fused Filament Fabrication (FFF) using WS2 nanotubes. Sci Rep. 2020;10(1):8892. doi: 10.1038/s41598-020-65861-w
- Daver F, Lee KPM, Brandt M, Shanks R. Cork -PLA composite filaments for fused deposition modelling. Compos Sci Technol. 2018;168:230-237. doi: 10.1016/j.compscitech.2018.10.008
- Le Duigou A, Castro M, Bevan R, Martin N. 3D printing of wood fibre biocomposites: From mechanical to actuation functionality. Mater Des. 2016;96:106-114. doi: 10.1016/j.matdes.2016.02.018
- Wu CS, Liao HT, Cai YX. Characterisation, biodegradability and application of palm fibre-reinforced polyhydroxyalkanoate composites. Polym Degrad Stab. 2017;140:55-63. doi: 10.1016/j.polymdegradstab.2017.04.016
- Kim DJ, Yu MH, Lim J, Nam B, Kim HS. Prediction of the mechanical behavior of fiber-reinforced composite structure considering its shear angle distribution generated during thermo-compression molding process. Compos Struct. 2019;220:441-450. doi: 10.1016/j.compstruct.2019.04.043
- Lee J, Ruckdashel R, Patil N, Pugatch M, Joshi K, Park JH. Highly filled coextruded dual-layer polymer/ceramic filament for material extrusion additive manufacturing. ACS Appl Polym Mater. 2023;5(4):2867-2876. doi: 10.1021/acsapm.3c00089
- Haryńska A, Janik H, Sienkiewicz M, Mikolaszek B, Kucińska-Lipka J. PLA -potato thermoplastic starch filament as a sustainable alternative to the conventional PLA filament: Processing, characterization, and FFF 3D printing. ACS Sustain Chem Eng. 2021;9(20):6923-6938. doi: 10.1021/acssuschemeng.0c09413
- Çanti E, Aydın M, Yıldırım F. Production and characterization of composite filaments for 3D printing. J Polytech. 2018;21:397-402. doi: 10.2339/politeknik.389591
- Deb D, Jafferson JM. Natural fibers reinforced FDM 3D printing filaments. Mater Today Proc. 2021;46:1308-1318. doi: 10.1016/j.matpr.2021.02.397
- Yu S, Hwang YH, Hwang JY, Hong SH. Analytical study on the 3D-printed structure and mechanical properties of basalt fiber-reinforced PLA composites using X-ray microscopy. Compos Sci Technol. 2019;175:18-27. doi: 10.1016/j.compscitech.2019.03.005
- Satyanarayana KG, Arizaga GGC, Wypych F. Biodegradable composites based on lignocellulosic fibers-An overview. Prog Polym Sci. 2009;34(9):982-1021. doi: 10.1016/j.progpolymsci.2008.12.002
- Nandi P, Das D. Mechanical, thermo-mechanical and biodegradation behaviors of green-composites prepared from woven structural nettle (Girardinia diversifolia) reinforcement and poly (Lactic acid) fibers. Ind Crops Prod. 2022;175:114247. doi: 10.1016/j.indcrop.2021.114247
- Ji M, Li F, Li J, et al. Enhanced mechanical properties, water resistance, thermal stability, and biodegradation of the starch-sisal fibre composites with various fillers. Mater Des. 2021;198:109373. doi: 10.1016/j.matdes.2020.109373
- Hasan MR, Davies IJ, Pramanik A, John M, Biswas WK. Potential of recycled PLA in 3D printing: A review. Sustain Manuf Serv Econ. 2024;3:100020. doi: 10.1016/j.smse.2024.100020
- Oladapo BI, Bowoto OK, Adebiyi VA, Ikumapayi OM. Net zero on 3D printing filament recycling: A sustainable analysis. Sci Total Environ. 2023;894:165046. doi: 10.1016/j.scitotenv.2023.165046
- Mikula K, Skrzypczak D, Izydorczyk G, et al. 3D printing filament as a second life of waste plastics-a review. Environ Sci Pollut Res. 2021;28(10):12321-12333. doi: 10.1007/s11356-020-10657-8
- Zhao P, Rao C, Gu F, Sharmin N, Fu J. Close-looped recycling of polylactic acid used in 3D printing: An experimental investigation and life cycle assessment. J Clean Prod. 2018;197:1046-1055. doi: 10.1016/j.jclepro.2018.06.275
- Shah DU, Schubel PJ, Clifford MJ, Licence P. Fatigue Characterisation of Natural Fibre Composites for Small- Scale Wind Turbine Blade Applications. In: ECCM15- 15th European Conference; 2012. p. 24-28.
- Bhardwaj D, Gupta A, Chaudhary V, Gupta S. Hybridization of natural fibers to develop the polymeric composite materials: A review. In: Advances in Engineering Materials. Lecture Notes in Mechanical Engineering. Singapore: Springer; 2021. p. 355-363. doi: 10.1007/978-981-33-6029-7_33
- Nurazzi NM, Asyraf MRM, Fatimah Athiyah S, et al. A review on mechanical performance of hybrid natural fiber polymer composites for structural applications. Polymers (Basel). 2021;13(13):2170. doi: 10.3390/polym13132170
- Jani SP, Kumar AS, Khan MA, Kumar MU. Machinablity of hybrid natural fiber composite with and without filler as reinforcement. Mater Manuf Processes. 2016;31(10):1393-1399. doi: 10.1080/10426914.2015.1117633