Evaluation of microstructure, tensile, and fatigue testing on angled walls of NASA HR-1 using laser powder direct energy deposition
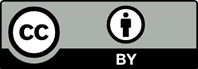
This study investigates the influence of varying deposition angles on the tensile strength and low cycle fatigue (LCF) performance of National Aeronautics and Space Administration (NASA) HR-1 alloy using laser powder-directed energy deposition. This study investigates the influence of varying deposition angles on the tensile strength and LCF performance of NASA HR-1 alloy using laser powder-directed energy deposition. Two sets of build parameters, 1,070 W and 2,620 W, were employed alongside three different build angles to assess their influence on mechanical properties following a uniform heat treatment regimen. This heat treatment encompassed stress relief, homogenization, solution annealing, and double aging. Samples deposited at 1,070 W showed a slightly lower porosity percentage compared to those produced at 2,620 W. All samples displayed similar grain sizes and a homogenized microstructure, indicating the effectiveness of the heat treatment in achieving a uniform microstructure across samples deposited at different build angles and laser power settings. The varying deposition angles did not significantly affect the microstructure or mechanical properties of the alloy. Fractography analysis revealed that all samples fractured through transgranular micro-void coalescence, with fracture initiation predominately occurring at the edges of both tensile and fatigue samples.
- Soltani-Tehrani A, Chen P, Katsarelis C, Gradl P, Shao S, Shamsaei N. Laser powder directed energy deposition (LP-DED) NASA HR-1 alloy: Laser power and heat treatment effects on microstructure and mechanical properties. Addit Manuf Lett. 2022;3:100097. doi: 10.1016/j.addlet.2022.100097
- Chen PS, Mitchell M. Alloy NASA HR-1. Aerospace Structural Metals Handbook; 2005. Available from: https://ntrs.nasa. gov/api/citations/20050182936/downloads/20050182936. pdf [Last accessed on 2023 Mar 20].
- Lee JA, Woods S. Hydrogen Embrittlement; 2016. p. 1-62. Available from: https://ntrs.nasa.gov/api/ citations/20160005654/downloads/20160005654.pdf [Last accessed on 2024 Dec 08].
- Birken A, Noel D. Metallurgical and thermal processing investigation of additively manufactured superalloys JBK-75 and NASA-HR-1. In: Materials Engineering; 2021. Available from: https://digitalcommons.calpoly.edu/matesp/233 [Last accessed on 2023 Mar 20].
- Lu X, Ma Y, Wang D. On the hydrogen embrittlement behavior of nickel-based alloys: Alloys 718 and 725. Mater Sci Eng A. 2020;792:139785. doi: 10.1016/j.msea.2020.139785
- Singh A, Kapil S, Das M. A comprehensive review of the methods and mechanisms for powder feedstock handling in directed energy deposition. Addit Manuf. 2020;35:101388. doi: 10.1016/j.addma.2020.101388
- Su J, Ng WL, An J, Yeong WY, Chua CK, Sing SL. Achieving sustainability by additive manufacturing: A state-of-the-art review and perspectives. Virtual Phys Prototyp. 2024;19(1):e2438899. doi: 10.1080/17452759.2024.2438899
- Ehmsen S, Glatt M, Aurich JC. Influence of process parameters on the power consumption of high-speed laser directed energy deposition. Procedia CIRP. 2023;116:89-94. doi: 10.1016/j.procir.2023.02.016
- Svetlizky D, Das M, Zheng B, et al. Directed energy deposition (DED) additive manufacturing: Physical characteristics, defects, challenges and applications. Mater Today. 2021;49:271-295. doi: 10.1016/j.mattod.2021.03.020
- Meng G, Gong Y, Zhang J, Jiang Z, Ren Q, Zhao J. Microstructure and mechanical properties of Inconel 718 thin walls prepared by laser direct energy deposition and selective laser melting. Thin-Walled Struct. 2023;193:111284. doi: 10.1016/j.tws.2023.111284
- Gamon A, Arrieta E, Gradl PR, et al. Microstructure and hardness comparison of as-built inconel 625 alloy following various additive manufacturing processes. Results Mater. 2021;12:100239. doi: 10.1016/j.rinma.2021.100239
- Zhi’En ET, Pang JH, Kaminski J. Directed energy deposition build process control effects on microstructure and tensile failure behaviour. J Mater Process Tech. 2021;294:117139. doi: 10.1016/j.jmatprotec.2021.117139
- Aversa A, Marchese G, Bassini E. Directed energy deposition of AISI 316L stainless steel powder: Effect of process parameters. Metals. 2021;11(6):932. doi: 10.3390/met11060932
- Li Z, Sui S, Ma X, et al. High deposition rate powder- and wire-based laser directed energy deposition of metallic materials: A review. Int J Mach Tools Manuf. 2022;181:103942. doi: 10.1016/j.ijmachtools.2022.103942
- Hassan B, Corney J. Grain boundary precipitation in Inconel 718 and ATI 718Plus. Mater Sci Technol. 2017;33(16):1879- 1889. doi: 10.1080/02670836.2017.1333222
- StandardTestMethodforSieveAnalysisofMetalPowders. Available from: https://compass.astm.org/document/?contentcode=ast m%7cb0214-16%7cen-us&proxycl=https%3a%2f%2fsecure. astm.org&fromlogin=true [Last accessed on 2024 Jan 11].
- Standard Test Methods for Flow Rate of Metal Powders Using the Hall Flowmeter Funnel. Available from: https://compass. astm.org/document/?contentCode=ASTM%7CB0213- 20%7Cen-US&proxycl=https%3A%2F%2Fsecure.astm. org&fromLogin=true [Last accessed on 2024 Feb 29].
- Schneider CA, Rasband WS, Eliceiri KW. NIH Image to ImageJ: 25 years of image analysis. Nat Methods. 2012;9(7):671-675. doi: 10.1038/nmeth.2089
- Standard Test Methods for Determining Average Grain Size. Available from: https://www.astm.org/e0112-13r21.html [Last accessed on 2024 Jan 10].
- Standard Test Methods for Tension Testing of Metallic Materials. Available from: https://compass.astm. org/document/?contentCode=ASTM%7CE0008- 04%7Cen-US&proxycl=https%3A%2F%2Fsecure.astm. org&fromLogin=true [Last accessed on 2024 Jan 11].
- Standard Test Method for Strain-Controlled Fatigue Testing. Available from: https://compass.astm.org/ document/?contentCode=ASTM%7CE0606_E0606M- 21%7Cen-US&proxycl=https%3A%2F%2Fsecure.astm. org&fromLogin=true [Last accessed on 2024 Jan 11].
- E28 Committee. Practice for Instrumented Indentation Testing. ASTM International; 2023. Available from: https://www. astm.org/e2546-15.html [Last accessed on 2024 Jan 11].
- Grima Cintas P, Marco-Almagro L, Tort-Martorell Llabres J. Industrial Statistics with Minitab. United States: Wiley; 2012.
- Brennan MC, Keist JS, Palmer TA. Defects in metal additive manufacturing processes. J Mater Eng Perform. 2021;30(7):4808-4818. doi: 10.1007/s11665-021-05919-6
- Ahn DG. Directed energy deposition (DED) process: State of the art. Int J Precis Eng Manuf-Green Technol. 2021;8(2):703-742. doi: 10.1007/s40684-020-00302-7
- Layer J, Adler T, Ahmed R, et al. Failure analysis and prevention. In: ASM INTERNATIONAL® Publication Information and Contributors. Vol 11. Ohio: ASM International® The MaterialsInformation Society; 2002.
- Lasalmonie A, Strudel JL. Influence of grain size on the mechanical behaviour of some high strength materials. J Mater Sci. 1986;21(6):1837-1852. doi: 10.1007/BF00547918
- Du Plessis A, Yadroitsava I, Yadroitsev I. Effects of defects on mechanical properties in metal additive manufacturing: A review focusing on X-ray tomography insights. Mater Des. 2020;187:108385. doi: 10.1016/j.matdes.2019.108385
- Frölich F, Bechtloff L, Scheuring BM, et al. Evaluation of mechanical properties characterization of additively manufactured components. Prog Addit Manuf. 2024;10:1217-1229. doi: 10.1007/s40964-024-00700-2
- Bagnoli DL, Banerji K, Boardman B, et al. Fractography. In: ASM INTERNATIONAL ® The Materials Information Company. Vol 12. Ohio: ASM International® The MaterialsInformation Society; 1987.
- Komarasamy M, Shukla S, Williams S, Kandasamy K, Kelly S, Mishra RS. Microstructure, fatigue, and impact toughness properties of additively manufactured nickel alloy 718. Addit Manuf. 2019;28:661-675. doi: 10.1016/j.addma.2019.06.009
- Zhao B, Song J, Xie L, Hu Z, Chen J. Surface roughness effect on fatigue strength of aluminum alloy using revised stress field intensity approach. Sci Rep. 2021;11(1):19279. doi: 10.1038/s41598-021-98858-0
- Javidi A, Rieger U, Eichlseder W. The effect of machining on the surface integrity and fatigue life. Int J Fatigue. 2008;30(10-11):2050-2055. doi: 10.1016/j.ijfatigue.2008.01.005