Functionally graded TPMS gyroid structures for additive manufacturing of non-pneumatic tires
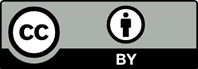
Non-pneumatic tires (NPTs) have been of interest for extreme environmental applications involving uneven surfaces, such as military reconnaissance and space exploration. Despite the advantages over pneumatic tires, NPTs are unsuitable for mass production due to higher cost, increased weight, and more importantly, design and manufacturing complexities through traditional manufacturing methods. In this work, we present a novel NPT design that overcomes these challenges by incorporating additively manufactured (AM) minimal surface lattices in the elastic structure of the tire to provide structural stability in radial and lateral directions. More importantly, minimal surface lattices can be additively manufactured without the need for support materials. This enables on-demand manufacturing under extreme environments without the need for complicated machinery and human involvement. This study thoroughly examines the deformed shape and force-displacement behavior of spokes featuring cylindrically designed gyroid triply periodic minimal surface (TPMS) under vertical compression through both numerical simulations and experimental testing. The research evaluates three sub-scale NPTs with varying sheet thicknesses in the minimal surface layers, focusing on both global stiffness and local deformation. Digital image correlation (DIC) was used to provide detailed insights into the deformation behavior and local deformation characteristics of these lattices, laying design guidelines for designing variable stiffness in NPT that can be used for extreme conditions. Finite element analysis (FEA) is conducted to validate the experimental findings, demonstrating that the functionally graded TPMS with varying sheet thicknesses exhibits a 20 – 53% increase in stiffness compared to uniform thickness designs. This confirms the superior performance of the graded lattices over uniform-thickness NPTs. Findings from this study can be leveraged to further develop a design-AM workflow for tire performance of NPTs that could be deployed in uneven terrains through remote AM manufacturing.

- Alkadi F, Lee J, Yeo JS, Hwang SH, Choi JW. 3D printing of ground tire rubber composites. Int J Precis Eng Manuf Green Technol. 2019;6(2):211-222. doi: 10.1007/s40684-019-00023-6
- Pentakota LK, Albertelli P, Strano M. Energy efficiency of the vulcanization process of a bicycle tyre. Int J Precis Eng Manuf Green Technol. 2023;10(4):979-998. doi: 10.1007/s40684-023-00507-6
- Moon B, Lee J, Kim S, Park S, Seok CS. Methodology for predicting the durability of aged tire sidewall under actual driving conditions. Int J Precis Eng Manuf. 2022;23(8):881-893. doi: 10.1007/s12541-022-00644-z
- Park H. Vibratory electromagnetic induction energy harvester on wheel surface of mobile sources. Int J Precis Eng Manuf. 2017;4(1):59-66. doi: 10.1007/s40684-017-0008-z
- Sardinha M, Fátima Vaz M, Ramos TR, Reis L. Design, properties, and applications of non-pneumatic tires: A review. Proc Inst Mech Eng Part L J Mater Design Appl. 2023;237(11):2277-2297. doi: 10.1177/14644207231177302.
- Jafferson JM, Sharma H. Design of 3D printable airless tyres using NTopology. Mater Today Proc. 2021;46:1147-1160. doi: 10.1016/j.matpr.2021.02.058
- Genovese A, Garofano D, Sakhnevych A, Timpone F, Farroni F. Static and dynamic analysis of non-pneumatic tires based on experimental and numerical methods. Appl Sci. 2021;11(23):11232. doi: 10.3390/app112311232
- Hryciów Z, Jackowski J, Żmuda M. The influence of non-pneumatic tyre structure on its operational properties. Int J Automot Mech Eng. 2020;17(3):8168-8178. doi: 10.15282/ijame.17.3.2020.10.0614
- Rugsaj R, Suvanjumrat C. Proper radial spokes of non-pneumatic tire for vertical load supporting by finite element analysis. Int J Automot Technol. 2019;20(4):801-812. doi: 10.1007/s12239-019-0075-y
- Veeramurthy M, Ju J, Thompson LL, Summers JD. Optimisation of geometry and material properties of a non-pneumatic tyre for reducing rolling resistance. Int J Veh Design. 2014;66(2):193. doi: 10.1504/IJVD.2014.064567
- Aboul-Yazid AM, Emam MAA, Shaaban S, El-Nashar MA. Effect of spokes structures on characteristics performance of non-pneumatic tires. Int J Automot Mech Eng. 2015;11:2212-2223. doi: 10.15282/ijame.11.2015.4.0185
- Kucewicz M, Baranowski P, Małachowski J. Airless Tire Conceptions Modeling and Simulations. Cham: Springer; 2017. p. 293-301. doi: 10.1007/978-3-319-50938-9_30
- Mathew NJ, Sahoo DK, Chakravarthy EM. Design and static analysis of airlesstyre to reduce deformation. IOP Conf Ser Mater Sci Eng. 2017;197:012042. doi: 10.1088/1757-899X/197/1/012042
- Jin X, Hou C, Fan X, Sun Y, Lv J, Lu C. Investigation on the static and dynamic behaviors of non-pneumatic tires with honeycomb spokes. Compos Struct. 2018;187:27-35. doi: 10.1016/j.compstruct.2017.12.044
- Ju J, Kim DM, Kim K. Flexible cellular solid spokes of a non-pneumatic tire. Compos Struct. 2012;94(8):2285-2295.doi: 10.1016/j.compstruct.2011.12.022
- Yoo S, Uddin MS, Heo H, Ju J, Choi SJ. Thermoviscoelastic modeling of a non-pneumatic tire with a lattice spoke. Proc Inst Mech Eng Part D J Automobile Eng. 2017;231(2):241-252. doi: 10.1177/0954407016656287
- Michelin USA. Michelin Uptis: The First Airless Mobility Solution for Passenger Vehicles. Available from: https:// michelinmedia.com/michelin-uptis [Last accessed on 2024 Jul 11].
- Airless Tire For Your Car: Michelin Says 2024, Here’s What They’re Up Against. Hackaday. Available from: https:// hackaday.com/2019/07/25/airless-tire-for-your-car-michelin-says-2024-heres-what-theyre-up-against [Last accessed on 2022 Jan 31].
- Wang J, Yang B, Lin X, et al. Research of TPU materials for 3D printing aiming at non-pneumatic tires by FDM method. Polymers (Basel). 2020;12(11):2492. doi: 10.3390/polym12112492
- Faisal MF, Akbar NI, Zayed AHH. Development and analysis of additively manufactured non-pneumatic tires for mars rover. IOP Conf Ser Mater Sci Eng. 2024;1305(1):012026. doi: 10.1088/1757-899X/1305/1/012026
- Ishfaq K, Asad M, Mahmood MA, Abdullah M, Pruncu C. Opportunities and challenges in additive manufacturing used in space sector: A comprehensive review. Rapid Prototyp J. 2022;28(10):2027-2042. doi: 10.1108/RPJ-05-2022-0166
- Mitchell A, Lafont U, Hołyńska M, Semprimoschnig C. Additive manufacturing-a review of 4D printing and future applications. Addit Manuf. 2018;24:606-626. doi: 10.1016/j.addma.2018.10.038
- Westerweel B, Basten R, DenBoer J, VanHoutum G. Printing spare parts at remote locations: Fulfilling the promise of additive manufacturing. Prod Oper Manag. 2021;30(6):1615-1632. doi: 10.1111/poms.13298
- Hoffmann M, Elwany A. In-space additive manufacturing: A review. J Manuf Sci Eng. 2023;145(2):020801. doi: 10.1115/1.4055603
- Hedayati R, Stulova V. 3D printing for space habitats: Requirements, challenges, and recent advances. Aerospace. 2023;10:653. doi: 10.3390/aerospace10070653
- Yoo DJ. New paradigms in cellular material design and fabrication. Int J Precis Eng Manuf. 2015;16(12):2577-2589. doi: 10.1007/s12541-015-0330-8
- Al-Ketan O, Rezgui R, Rowshan R, Du H, Fang NX, Abu Al-Rub RK. Microarchitected stretching-dominated mechanical metamaterials with minimal surface topologies. Adv Eng Mater. 2018;20(9):1-15. doi: 10.1002/adem.201800029
- Yánez A, Cuadrado A, Martel O, Afonso H, Monopoli D. Gyroid porous titanium structures: A versatile solution to be used as scaffolds in bone defect reconstruction. Mater Des. 2018;140:21-29. doi: 10.1016/j.matdes.2017.11.050
- Bobbert FSL, Lietaert K, Eftekhari AA, et al. Additively manufactured metallic porous biomaterials based on minimal surfaces: A unique combination of topological, mechanical, and mass transport properties. Acta Biomater. 2017;53:572-584. doi: 10.1016/j.actbio.2017.02.024
- Sreedhar N. Mass transfer analysis of ultrafiltration using spacers based on triply periodic minimal surfaces: Effects of spacer design, directionality and voidage. J Memb Sci. 2018;561:89-98. doi: 10.1016/j.memsci.2018.05.028
- Tilton M, Borjali A, Griffis JC, Varadarajan KM, Manogharan GP. Fatigue properties of Ti-6Al-4V TPMS scaffolds fabricated via laser powder bed fusion. Manuf Lett. 2023;37:32-38. doi: 10.1016/j.mfglet.2023.06.005
- Thomas N, Sreedhar N, Al-Ketan O, Rowshan R, Abu Al-Rub RK, Arafat H. 3D printed triply periodic minimal surfaces as spacers for enhanced heat and mass transfer in membrane distillation. Desalination. 2018;443:256-271. doi: 10.1016/j.desal.2018.06.009
- Afshar M, Anaraki AP, Montazerian H, Kadkhodapour J. Additive manufacturing and mechanical characterization of graded porosity scaffolds designed based on triply periodic minimal surface architectures. J Mech Behav Biomed Mater. 2016;62:481-494. doi: 10.1016/j.jmbbm.2016.05.027
- Feng J, Fu J, Yao X, He Y. Triply periodic minimal surface (TPMS) porous structures: From multi-scale design, precise additive manufacturing to multidisciplinary applications. Int J Extrem Manuf. 2022;4(2):022001. doi: 10.1088/2631-7990/ac5be6
- Yu S, Sun J, Bai J. Investigation of functionally graded TPMS structures fabricated by additive manufacturing. Mater Des. 2019;182:108021. doi: 10.1016/j.matdes.2019.108021
- Ren Y, Li Y, Yang L, et al. Compressive properties and fatigue performance of NiTi lattice structures optimized by TPMS. Mater Sci Addit Manuf. 2024;3(2):3380. doi: 10.36922/msam.3380
- Kapfer SC, Hyde ST, Mecke K, Arns CH, Schröder-Turk GE. Minimal surface scaffold designs for tissue engineering. Biomaterials. 2011;32(29):6875-6882. doi: 10.1016/j.biomaterials.2011.06.012
- Kladovasilakis N, Tsongas K, Kostavelis I, Tzovaras D, Tzetzis D. Effective mechanical properties of additive manufactured triply periodic minimal surfaces: Experimental and finite element study. Int J Adv Manuf Technol. 2022;121(11-12):7169-7189. doi: 10.1007/s00170-022-09651-w
- Shaikh A, Griffis J, Stebbins R, et al. Towards gradient design of TPMS lattices and laser powder bed fusion processing-role of laser strategies and lattice thickness. Manuf Lett. 2024;41:1046-1054. doi: 10.1016/j.mfglet.2024.09.129
- Zhao M, Zhang DZ, Liu F, Li Z, Ma Z, Ren Z. Mechanical and energy absorption characteristics of additively manufactured functionally graded sheet lattice structures with minimal surfaces. Int J Mech Sci. 2020;167:105262. doi: 10.1016/j.ijmecsci.2019.105262
- Ejeh CJ, Barsoum I, Abu Al-Rub RK. Flexural properties of functionally graded additively manufactured AlSi10Mg TPMS latticed-beams. Int J Mech Sci. 2022;223:107293. doi: 10.1016/j.ijmecsci.2022.107293
- Al-Ketan O, Lee DW, Rowshan R, Abu Al-Rub RK. Functionally graded and multi-morphology sheet TPMS lattices: Design, manufacturing, and mechanical properties. J Mech Behav Biomed Mater. 2020;102:103520. doi: 10.1016/j.jmbbm.2019.103520
- Yang L, Mertens R, Ferrucci M, Yan C, Shi Y, Yang S. Continuous graded Gyroid cellular structures fabricated by selective laser melting: Design, manufacturing and mechanical properties. Mater Des. 2019;162:394-404. doi: 10.1016/j.matdes.2018.12.007
- Zhang X, Jiang L, Yan X, Wang Z, Li X, Fang G. Revealing the apparent and local mechanical properties of heterogeneous lattice: A multi-scale study of functionally graded scaffold. Virtual Phys Prototyp. 2023;18(1):e2120406. doi: 10.1080/17452759.2022.2120406
- Kim HS, Kim DY, Choi JW, Park SH. High stability in compressive and shear behavior of airless tire using primitive TPMS-based cylindrical spoke. Int J Precis Eng Manufac Green Technol. 2024;11(4):1247-1262. doi: 10.1007/s40684-023-00587-4
- Kim DY, Kim HS, Kamath SS, Hou X, Choi JW, Park SH. TPMS-based auxetic structure for high-performance airless tires with variable stiffness depending on deformation. Sci Rep. 2024;14(1):11419. doi: 10.1038/s41598-024-62101-3
- Al Rashid A, Ahmed W, Khalid MY, Koç M. Vat photopolymerization of polymers and polymer composites: Processes and applications. Addit Manuf. 2021;47:102279. doi: 10.1016/j.addma.2021.102279
- Chaudhary R, Fabbri P, Leoni E, Mazzanti F, Akbari R, Antonini C. Additive manufacturing by digital light processing: A review. Prog Addit Manuf. 2023;8(2):331-351. doi: 10.1007/s40964-022-00336-0
- Hornbeck LJ. In: Wu MH, editor. Digital Light Processing for High-brightness High-Resolution Applications. Berlin: Springer; 1997. p. 27-40. doi: 10.1117/12.273880
- U. 3D Systems. Material Properties, Flex BLK 20. 3D Systems, USA. Available from: https://www.3dsystems.com/ materials/figure-4-flex-blk-20 [Last accessed on 2024 Jul 11].
- ASTM D695. Standard Test Method for Compressive Properties of Rigid Plastics. United States: ASTM International; 2010. p. 1-8. doi: 10.1520/D0695-15.2
- Panesar A, Abdi M, Hickman D, Ashcroft I. Strategies for functionally graded lattice structures derived using topology optimisation for additive manufacturing. Addit Manuf. 2018;19:81-94. doi: 10.1016/j.addma.2017.11.008
- Yoon H, Lee K, Lee J, Kwon J, Seo T. The stiffness adjustable wheel mechanism based on compliant spoke deformation. Sci Rep. 2024;14(1):773. doi: 10.1038/s41598-024-51493-x
- Viet NV, Zaki W. Free vibration and buckling characteristics of functionally graded beams with triply periodic minimal surface architecture. Compos Struct. 2021;274:114342. doi: 10.1016/j.compstruct.2021.114342
- Shah GJ, Nazir A, Lin SC, Jeng JY. Design for additive manufacturing and investigation of surface-based lattice structures for buckling properties using experimental and finite element methods. Materials (Basel). 2022;15(11):4037. doi: 10.3390/ma15114037
- Zhao W, Wang G, Cheng T, Liu Y. Review of space manufacturing technique and developments. Sci Sin Phys Mech Astron. 2020;50(4):047006. doi: 10.1360/SSPMA-2019-0416
- Liu M, Tang W, Duan W, et al. Digital light processing of lunar regolith structures with high mechanical properties. Ceram Int. 2019;45(5):5829-5836. doi: 10.1016/j.ceramint.2018.12.049
- Wang W, Jin Y, Mu Y, Zhang M, Du J. A novel tubular structure with negative Poisson’s ratio based on gyroid-type triply periodic minimal surfaces. Virtual Phys Prototyp. 2023;18(1):e2203701. doi: 10.1080/17452759.2023.2203701
- Li H, Zhao Y, Lin F, Zhu M. Nonlinear dynamics modeling and rollover control of an off-road vehicle with mechanical elastic wheel. J Braz Soc Mech Sci Eng. 2018;40(2):51. doi: 10.1007/s40430-018-1009-8
- Zhang Z, Fu H, Zhao Q, Tan D, Yang K. Pattern design and performance analysis of a flexible spoke bionic non-pneumatic tire. J Braz Soc Mech Sci Eng. 2021;43(1):41. doi: 10.1007/s40430-020-02743-2
- Deng Y, Wang Z, Liu T, Liang W, Shen H, Xiao Z. Static and dynamic mechanical characteristics of honeycomb non-pneumatic tire under structural damage condition. Eur J Mech A/Solids. 2023;102:105120. doi: 10.1016/j.euromechsol.2023.105120
- Zhao Y, Zang L, Chen Y, Li B, Wang J. Non-pneumatic mechanical elastic wheel natural dynamic characteristics and influencing factors. J Cent S Univ. 2015;22(5):1707-1715. doi: 10.1007/s11771-015-2689-1