Microstructure and wear characteristics of austenitic stainless steel coatings fabricated through various directed energy deposition
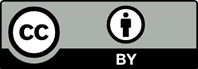
Austenitic stainless steels are widely used in automotive and marine environments because of their high toughness, corrosion resistance, and wear resistance. The present comparative study focuses on the microstructure and wear resistance of double-layer austenitic stainless-steel coatings prepared on a ductile iron substrate using circular spot high-speed laser-directed energy deposition (DED) and broad-beam laser-DED. The results indicate that while the deposition process does not alter the physical phase of coating, it does influence the preferred orientation of surface grains. Both coatings exhibit characteristics of hypoeutectic alloys, where the harder eutectic structure serves as a skeleton to resist external pressure. The high-speed laser-DED coating demonstrates higher hardness and wears resistance due to its denser eutectic structure. In addition, its finer microstructure produces smaller wear debris, contributing to the formation of a denser oxide film, thereby enhancing wear resistance.
- Wei R, Ouyang C, Wang R, et al. Effect of chromic acid anodization on the corrosion resistance of Fe-based alloy coatings by high-speed laser cladding. Mater Lett. 2023;350:134887. doi: 10.1016/j.matlet.2023.134887
- Wei R, Mao M, Liang J, et al. Repair feasibility and performance enhancement analysis of Fe-based alloy coating on ductile iron surface by high-speed laser cladding. Mater Today Commun. 2024;39:108638. doi: 10.1016/j.mtcomm.2024.108638
- Luo X, Smith G, Sampath S. On the interplay between adhesion strength and tensile properties of thermal spray coated laminates-part I: High velocity thermal spray coatings. J Therm Spray Tech. 2018;27:296-307. doi: 10.1007/s11666-018-0695-1
- Li M, Li C, Li B, et al. Comparison of Fe30Co20Cr20Ni20Mo3.5 high entropy alloy coatings prepared using plasma cladding. High-speed laser cladding, and deep laser cladding. Coatings. 2023;13:1819. doi: 10.3390/coatings13111819
- Doll G, Mensah B, Mohseni H, et al. Chemical vapor deposition and atomic layer deposition of coatings for mechanical applications. J Therm Spray Tech. 2009;19: 510-516. doi: 10.1007/s11666-009-9364-8
- Liu G, Su Y, Pi S, et al. Achieving high strength 316L stainless steel by laser directed energy deposition-ultrasonic rolling hybrid process. Mat Sci Eng A Struct. 2024;903:146665. doi: 10.1016/j.msea.2024.146665
- Aggarwal A, Pandiyan V, Leinenbach C, et al. Investigating laser beam shadowing and powder particle dynamics in directed energy deposition through high-fidelity modelling and high-speed imaging. Addit Manuf. 2024;91:104344. doi: 10.1016/j.addma.2024.104344
- Sun Z, Tan X, Tor S, et al. Selective laser melting of stainless steel 316L with low porosity and high build rates. Mater Des. 2016;104:197-204. doi: 10.1016/j.matdes.2016.05.035
- Antony K, Arivazhagan N, Senthilkumaran K. Numerical and experimental investigations on laser melting of stainless steel 316L metal powders. J Manuf Process. 2014;16:345-355. doi: 10.1016/j.jmapro.2014.04.001
- Buford A, Goswami T. Review of wear mechanisms in hip implants: Paper I-general. Mater Des. 2004;25:385-393. doi: 10.1016/j.matdes.2003.11.010
- Mahathanabodee S, Palathai T, Raadnui S, et al. Dry sliding wear behavior of SS316L composites containing h-BN and MoS2 solid lubricants. Wear. 2014;316:37-48. doi: 10.1016/j.wear.2014.04.015
- Zeng Y, Li K, Hughes R, et al. Corrosion mechanisms and materials selection for the construction of flue gas component in advanced heat and power systems. Ind Eng Chem Res. 2017;56:14141-14154. doi: 10.1021/acs.iecr.7b03664
- Zhu Y, Zou J, Chen X, et al. Tribology of selective laser melting processed parts: Stainless steel 316 L under lubricated conditions. Wear. 2016;350-351:46-55. doi: 10.1016/j.wear.2016.01.004
- Liang Y, Liao Z, Zhang L, et al. A review on coatings deposited by extreme high-speed laser cladding: processes, materials, and properties. Opt Laser Technol. 2023;164:109472. doi: 10.1016/j.optlastec.2023.109472
- Yang J, Bai B, Ke H, et al. Effect of metallurgical behavior on microstructure and properties of FeCrMoMn coatings prepared by high-speed laser cladding. Opt Laser Technol. 2021;144:107431. doi: 10.1016/j.optlastec.2021.107431
- Tuominen J, Kiviö J, Balusson C, et al. High-speed laser cladding of chromium carbide reinforced Ni-based coatings. Weld World. 2023;67:2175-2186. doi: 10.1007/s40194-023-01557-9
- Yuan W, Li R, Chen Z, et al. A comparative study on microstructure and properties of traditional laser cladding and high-speed laser cladding of Ni45 alloy coatings. Surf Coat Tech. 2021;405:126582. doi: 10.1016/j.surfcoat.2020.126582
- Zhang Z, Yang Q, Yu Z, et al. Influence of Y2O3 addition on the microstructure of TiC reinforced Ti-based composite coating prepared by laser cladding. Mater Charact. 2022;189:111962. doi: 10.1016/j.matchar.2022.111962
- Liu H, Qin X, Huang S, et al. Geometry characteristics prediction of single track cladding deposited by high power diode laser based on genetic algorithm and neural network. Int J Precis Eng Man. 2018;19:1061-1070.
- Liu H, Qin X, Huang S, et al. Geometry modeling of single track cladding deposited by high power diode laser with rectangular beam spot. Opt Laser Eng. 2018;100:38-46. doi: 10.1016/j.optlaseng.2017.07.008
- Sun B, Cheng J, Cai Z, et al. Formation and wear property of broad-beam laser clad Fe-based coatings. Surf Coat Tech. 2021;405:126598. doi: 10.1016/j.surfcoat.2020.126598
- Lei K, Qin X, Liu H, et al. Analysis and modeling of melt pool morphology for high power diode laser cladding with a rectangle beam spot. Opt Laser Eng. 2018;110:89-99. doi: 10.1016/j.optlaseng.2018.05.022
- Wang R, Ouyang C, Zhao C, et al. Effect of high-temperature heat treatment on electrochemical corrosion behavior of laser cladding Fe-based alloy coating in H2SO4 solution. Mater Lett. 2023;346:134560. doi: 10.1016/j.matlet.2023.134560
- Deng R, Mao M, Zhao C, et al. Effect of laser remelting scanning speed on microstructure and abrasion resistance of laser cladded Fe based alloy coatings. Mater Lett. 2024;366:136562. doi: 10.1016/j.matlet.2024.136562
- Deng R, Li H, Zhao C, et al. Study on the effect of laser remelting energy density on the microstructure and wear resistance of Fe-based alloy coatings fabricated by laser cladding. J Therm Spray Tech. 2024;33:1455-1471. doi: 10.1007/s11666-024-01795-3
- Xu P, Zhu L, Xue P, et al. Microstructure and properties of IN718/WC-12Co composite coating by laser cladding. Ceram Int. 2022;48:9218-9228. doi: 10.1016/j.ceramint.2021.12.108
- Wei R, Mao M, Liang J, et al. Study of the effect of overlap rate on the failure form, microstructure and wear resistance of multilayer laser cladding on grey cast iron surfaces. Tribo Int. 2024;194:109568. doi: 10.1016/j.triboint.2024.109568
- Sun B, Wang Q, Chen Y, et al. Dendrite refinement and wear performance enhancement in laser-cladded Fe-based coatings after multi-step laser remelting. Surf Coat Tech. 2022;447:128794. doi: 10.1016/j.surfcoat.2022.128794
- Wang Y, Xu L, Zhao L, et al. Friction and tribocorrosion behavior of Fe-Cr-B alloys manufactured by laser directed energy deposition. Tribo Int. 2023;189:108932. doi: 10.1016/j.triboint.2023.108932
- Li Y, Dong S, Yan S, et al. Phase evolution of ductile iron during laser cladding processing. Surf Coat Tech. 2018;339:37-47.
- Li Y, Dong S, Yan S, et al. Surface remanufacturing of ductile cast iron by laser cladding Ni-Cu alloy coatings. Surf Coat Tech. 2018;347:20-28. doi: 10.1016/j.surfcoat.2018.04.065
- Sohi M, Ebrahimi M, Ghasemi H, et al. Microstructural study of surface melted and chromium surface alloyed ductile iron. Appl Surf Sci. 2012;258:7348-7353. doi: 10.1016/j.apsusc.2012.04.014
- Deng R, Mao M, Zhao C, et al. A review of recent advances in integrated laser remelting and laser cladding processes. Metall Res Technol. 2024;121:402. doi: 10.1051/metal/2024038
- Li Q, Bai Q, Zhao C, et al. Microstructure evolution of laser cladding coatings treated by multi-pass power spinning. Mater Charact. 2023;199:112819. doi: 10.1016/j.matchar.2023.112819
- Zhu L, Liu Y, Li Z, et al. Microstructure and properties of Cu-Ti-Ni composite coatings on gray cast iron fabricated by laser cladding. Opt Laser Technol. 2020;122:105879. doi: 10.1016/j.optlastec.2019.105879