Effects of heat treatment on microstructure and mechanical properties of 17-4PH/IN625 bimetallic parts fabricated through extrusion-based sintering-assisted additive manufacturing
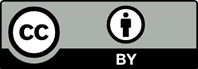
The mechanical properties of bimetallic composites are significantly influenced by their interfacial morphologies. This study delves into the impact of various heat treatment conditions on the microstructure and mechanical attributes of steel/nickel bimetallic (17-4PH/IN625) components produced through extrusion-based sintering-assisted additive manufacturing (ES-AM). The bimetallic composites were annealed at 1150°C for 1, 4, and 8 h, followed by an aging treatment at 482°C for samples annealed for 8 h. After annealing, microstructural heterogeneities, including variations in grain size and elemental distribution within the transition zone close to the interface, were observed. It was found that in the diffusion transition zone between the two alloy layers, the diffusion of iron (Fe) and nickel (Ni) elements increased with longer holding times, as corroborated by microhardness tests and quantified through theoretical parabolic diffusion law. The transition zone exhibited two distinct areas: an Fe-predominant zone and a Ni-predominant zone, with the latter containing oxides and molybdenum (Mo)- and niobium (Nb)-rich precipitates. No new phases emerged post-heat treatment; however, shifts in peak due to stress relaxation and the emergence of precipitates were identified through X-ray diffraction (XRD) observations. Microhardness within the transition zone increased following heat treatment, peaking at 186 HV1.0 after a 4-h annealing. The optimal heat treatment condition was identified as 1150°C for 4 h, which facilitated the development of uniform microstructures and improved bonding strength. This study demonstrates an enhanced interfacial bonding strength in 17-4PH and IN625 bimetallic parts manufactured through ES-AM, suggesting their wide-ranging potential applications in industry.
- Bandyopadhyay A, Zhang Y, Onuike B. Additive manufacturing of bimetallic structures. Virtual Phys Prototyp. 2022;17(2):256-294. doi: 10.1080/17452759.2022.2040738
- Zhang B, Zhang W, Xiao H, Yang H, Wang Y, Chen B. QCr0. 8 Cu alloy/S06 stainless steel bimetal structure via In718 multi-interlayer fabricated by laser powder hybrid additive manufacturing. J Mater Res Technol. 2023;24:1034-1042. doi: 10.1016/j.jmrt.2023.03.073
- Jiménez A, Bidare P, Hassanin H, Tarlochan F, Dimov S, Essa K. Powder-based laser hybrid additive manufacturing of metals: A review. Int J Adv Manuf Technol. 2021;114:63-96. doi: 10.1007/s00170-021-06855-4
- Sahasrabudhe H, Harrison R, Carpenter C, Bandyopadhyay A. Stainless steel to titanium bimetallic structure using LENSTM. Addit Manuf. 2015;5:1-8. doi: 10.1016/j.addma.2014.10.002
- Wu H, Xie X, Liu S, et al. Bonding behavior of Bi-metal-deposits produced by hybrid cold spray additive manufacturing. J Mater Process Technol. 2022;299:117375. doi: 10.1016/j.jmatprotec.2021.117375
- Jiang D, Ning F. Physical-mechanical behaviors of stainless steel plate-lattice built by material extrusion additive manufacturing. J Mater Process Technol. 2022;309:117739. doi: 10.1016/j.jmatprotec.2022.117739
- Jiang D, Ning F. Reprint of: Bi-metal structures fabricated by extrusion-based sintering-assisted additive manufacturing. J Manuf Process. 2023;100:20-26. doi: 10.1016/j.jmapro.2023.05.101
- Zhang Y, Bandyopadhyay A. Influence of compositionally graded interface on microstructure and compressive deformation of 316L stainless steel to Al12Si aluminum alloy bimetallic structures. ACS Appl Mater Interfaces. 2021;13(7):9174-9185. doi: 10.1021/acsami.0c21478
- Wei C, Liu L, Gu Y, et al. Multi-material additive-manufacturing of tungsten-copper alloy bimetallic structure with a stainless-steel interlayer and associated bonding mechanisms. Addit Manuf. 2022;50:102574. doi: 10.1016/j.addma.2021.102574
- Ergene B, Yalçın B. Investigation on mechanical performances of various cellular structures produced with fused deposition modeling (FDM). J Fac Eng Archit Gazi Univ. 2023;38:201-207. doi: 10.17341/gazimmfd.945650
- Mousapour M, Salmi M, Klemettinen L, Partanen J. Feasibility study of producing multi-metal parts by Fused Filament Fabrication (FFF) technique. J Manuf Process. 2021;67:438-446. doi: 10.1016/j.jmapro.2021.05.021
- Seleznev M, Roy-Mayhew JD. Bi-metal composite material for plastic injection molding tooling applications via fused filament fabrication process. Addit Manuf. 2021;48:102375. doi:10.1016/j.addma.2021.102375
- Sun Y, Hebert RJ, Aindow M. Effect of heat treatments on microstructural evolution of additively manufactured and wrought 17-4PH stainless steel. Mater Des. 2018;156:429-440. doi: 10.1016/j.matdes.2018.07.015
- Karmuhilan M, Kumanan S. A review on additive manufacturing processes of inconel 625. J Mater Eng Perform. 2021;31:2583-2592. doi: 10.1007/s11665-021-06427-3
- Jagtap BM, Kakandikar GM, Jawade SA. Mechanical behavior of inconel 625 and 17-4 PH stainless steel processed by atomic diffusion additive manufacturing. In: Dave HK, Dixit US, Nedelcu D, editors. Recent Advances in Manufacturing Processes and Systems. Berlin: Springer Nature Singapore; 2022. p. 583-594. doi: 10.1007/978-981-16-7787-8
- Mattli MR, Khan A, Matli PR, et al. Effect of Inconel625 particles on the microstructural, mechanical, and thermal properties of Al-Inconel625 composites. Mater Today Commun. 2020;25:101564. doi: 10.1016/j.mtcomm.2020.101564
- Dash A, Bandyopadhyay A. 17-4 PH and SS316L bimetallic structures via additive manufacturing. Virtual Phys Prototyp. 2024;19(1):e2292695. doi: 10.1080/17452759.2023.2292695
- Du Plessis A, Razavi N, Benedetti M, et al. Properties and applications of additively manufactured metallic cellular materials: A review. Prog Mater Sci. 2022;125:100918. doi: 10.1016/j.pmatsci.2021.100918
- Li G, Jiang W, Guan F, Zhu J, Yu Y, Fan Z. Effect of different Ni interlayers on interfacial microstructure and bonding properties of Al/Mg bimetal using a novel compound casting. J Manuf Process. 2020;50:614-628. doi: 10.1016/j.jmapro.2020.01.017
- Wu B, Qiu Z, Pan Z, et al. Enhanced interface strength in steel-nickel bimetallic component fabricated using wire arc additive manufacturing with interweaving deposition strategy. J Mater Sci Technol. 2020;52:226-234. doi: 10.1016/j.jmst.2020.04.019
- Li P, Gong Y, Xu Y, Qi Y, Sun Y, Zhang H. Inconel-steel functionally bimetal materials by hybrid directed energy deposition and thermal milling: Microstructure and mechanical properties. Arch Civ Mech Eng. 2019;19:820-831. doi: 10.1016/j.acme.2019.03.002
- Dang X, Li Y, Chen K, Luo S, Liang X, He W. Insight into the interfacial architecture of a hybrid additively-manufactured stainless steel/Ni-based superalloy bimetal. Mater Des. 2022;216:110595. doi: 10.1016/j.matdes.2022.110595
- Chen N, Khan HA, Wan Z, et al. Microstructural characteristics and crack formation in additively manufactured bimetal material of 316L stainless steel and Inconel 625. Addit Manuf. 2020;32:101037. doi: 10.1016/j.addma.2020.101037
- Fan H, Shi Q, Wang C, Tian Y, Zhou K, Yang S. Laser powder bed fusion of bimetallic stainless steel/Nickel-based superalloy: Interface and mechanical properties. Mater Sci Eng A. 2023;877:145193. doi: 10.1016/j.msea.2023.145193
- Ferro P, Fabrizi A, Elsayed H, Berto F, Savio G. Creating IN718-high carbon steel Bi-metallic parts by fused deposition modeling and sintering. Procedia Struct Integr. 2023;47:535-544. doi: 10.1016/j.prostr.2023.07.071
- Ahsan MR, Fan X, Seo GJ, et al. Microstructures and mechanical behavior of the bimetallic additively-manufactured structure (BAMS) of austenitic stainless steel and Inconel 625. J Mater Sci Technol. 2021;74:176-188. doi: 10.1016/j.jmst.2020.10.001
- Kosturek R, Wachowski M, Śnieżek L, Gloc M. The influence of the post-weld heat treatment on the microstructure of inconel 625/carbon steel bimetal joint obtained by explosive welding. Metals. 2019;9(2):246. doi: 10.3390/met9020246
- Gope DK, Chattopadhyaya S. Dissimilar welding of nickel based superalloy with stainless steel: Influence of post weld heat treatment. Mater Manuf Process. 2022;37(2):136-142. doi: 10.1080/10426914.2021.1945095
- Liu J, Miao Y, Wang Z, Zhao Y, Wu Y, Li C. Effect of heat treatment on microstructure and properties of additively manufactured aluminum bronze-steel bimetallic structures. Mater Charact. 2024;207:113462. doi: 10.1016/j.matchar.2023.113462
- Miriyev A, Levy A, Kalabukhov S, Frage N. Interface evolution and shear strength of Al/Ti bi-metals processed by a spark plasma sintering (SPS) apparatus. J Alloys Compd. 2016;678:329-336. doi: 10.1016/j.jallcom.2016.03.137
- Wang Y, Song R, Yanagimoto J, Li H. Effect of heat treatment on bonding mechanism and mechanical properties of high strength Cu/Al/Cu clad composite. J Alloys Compd. 2019;801:573-580. doi: 10.1016/j.jallcom.2019.06.132
- Li Z, Zhao J, Jia F, et al. Interfacial characteristics and mechanical properties of duplex stainless steel bimetal composite by heat treatment. Mater Sci Eng A. 2020;787:139513. doi: 10.1016/j.msea.2020.139513
- Ahsan MR, Tanvir ANM, Seo GJ, et al. Heat-treatment effects on a bimetallic additively-manufactured structure (BAMS) of the low-carbon steel and austenitic-stainless steel. Addit Manuf. 2020;32:101036. doi: 10.1016/j.addma.2020.101036
- Li K, Zhan J, Yang T, et al. Homogenization timing effect on microstructure and precipitation strengthening of 17-4PH stainless steel fabricated by laser powder bed fusion. Addit Manuf. 2022;52:102672. doi: 10.1016/j.addma.2022.102672
- Parizia S, Marchese G, Rashidi M, et al. Effect of heat treatment on microstructure and oxidation properties of Inconel 625 processed by LPBF. J Alloys Compd. 2020;846:156418. doi: 10.1016/j.jallcom.2020.156418
- Zhang Q, Liang S, Zou J, Yang Q. Interfacial microstructure of CuCr/1Cr18Ni9Ti bi-metal materials and its effect on bonding strength. Sci China Technol Sci. 2015;58(5):825-831. doi: 10.1007/s11431-015-5791-6
- Lashgari H, Adabifiroozjaei E, Kong C, Molina-Luna L, Li S. Heat treatment response of additively manufactured 17-4PH stainless steel. Mater Charact. 2023;197:112661. doi: 10.1016/j.matchar.2023.112661
- Gonzalez J, Mireles J, Stafford S, Perez M, Terrazas C, Wicker R. Characterization of Inconel 625 fabricated using powder-bed-based additive manufacturing technologies. J Mater Process Technol. 2019;264:200-210. doi: 10.1016/j.jmatprotec.2018.08.031
- Jiang D, Ning F. Bi-metal structures fabricated by extrusion-based sintering-assisted additive manufacturing. J Manuf Process. 2023;98:216-222. doi: 10.1016/j.jmapro.2023.05.025
- Kumar N, Pandey C, Kumar P. Dissimilar welding of Inconel alloys with austenitic stainless-steel: A review. J Press Vessel Technol. 2023;145(1):011506. doi: 10.1115/1.4055329
- Bina MH, Dehghani F, Salimi M. Effect of heat treatment on bonding interface in explosive welded copper/stainless steel. Mater Des. 2013;45:504-509. doi: 10.1016/j.matdes.2012.09.037
- Liu X, Fan J, Zhang P, et al. Influence of heat treatment on Inconel 625 superalloy sheet: Carbides, γ’’, δ phase precipitation and tensile deformation behavior. J Alloys Compd. 2023;930:167522. doi: 10.1016/j.jallcom.2022.167522
- Jiang W, Li G, Wu Y, Liu X, Fan Z. Effect of heat treatment on bonding strength of aluminum/steel bimetal produced by a compound casting. J Mater Process Technol. 2018;258:239-250. doi: 10.1016/j.jmatprotec.2018.04.006
- Marchese G, Lorusso M, Parizia S, et al. Influence of heat treatments on microstructure evolution and mechanical properties of Inconel 625 processed by laser powder bed fusion. Mater Sci Eng A. 2018;729:64-75. doi: 10.1016/j.msea.2018.05.044
- Floreen S, Fuchs GE, Yang WJ. The metallurgy of alloy 625. Superalloys. 1994;718(625):13-37.
- Hu Y, Lin X, Li Y, et al. Influence of heat treatments on the microstructure and mechanical properties of Inconel 625 fabricated by directed energy deposition. Mater Sci Eng A. 2021;817:141309. doi: 10.1016/j.msea.2021.141309
- Sabooni S, Chabok A, Feng SC, et al. Laser powder bed fusion of 17–4 PH stainless steel: A comparative study on the effect of heat treatment on the microstructure evolution and mechanical properties. Addit Manuf. 2021;46:102176. doi: 10.1016/j.addma.2021.102176
- Wen Y, Gao J, Narayan RL, et al. Microstructure-property correlations in as-built and heat-treated compositionally graded stainless steel 316L-Inconel 718 alloy fabricated by laser powder bed fusion. Mater Sci Eng A. 2023;862:144515. doi: 10.1016/j.msea.2022.144515
- Carrozza A, Lorenzi S, Carugo F, et al. A comparative analysis between material extrusion and other additive manufacturing techniques: Defects, microstructure and corrosion behavior in nickel alloy 625. Mater Des. 2023;225:111545. doi: 10.1016/j.matdes.2022.111545
- Li C, White R, Fang XY, Weaver M, Guo YB. Microstructure evolution characteristics of Inconel 625 alloy from selective laser melting to heat treatment. Mater Sci Eng A. 2017;705:20-31. doi: 10.1016/j.msea.2017.08.058
- An S, Eo DR, Sohn I, Choi K. Homogenization on solution treatment and its effects on the precipitation-hardening of selective laser melted 17-4PH stainless steel. J Mater Sci Technol. 2023;166:47-57. doi: 10.1016/j.jmst.2023.04.055
- Vinod A, Warghane S, Murugan A, Balashanmugam N, Venkaiah N. Microstructure and interfacial characteristics of inconel 625-Ti6Al4V bimetallic structures produced by directed energy deposition. J Mater Eng Perform. 2023; 33:1-12. doi: 10.1007/s11665-023-08250-4