The role of graded layers in interfacial characteristics and mechanical properties of Ti6Al4V/AlMgScZr-graded multi-material parts fabricated using laser powder bed fusion
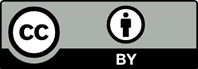
Graded multi-material parts achieve a compositionally graded transition between two different materials, mitigating undesirable consequences such as cracking and delamination due to property mismatch and significantly improving the comprehensive performance of parts. In this study, the Ti6Al4V/AlMgScZr-graded multi-material parts were fabricated using laser powder bed fusion technology, introducing a composition-graded layer with 25 wt.% Ti6Al4V and 75 wt.% AlMgScZr at the interface to reduce the mismatch between the two materials. The effect of the graded layer’s laser scanning speed on the densification behavior, microstructure evolution, and mechanical properties of the Ti6Al4V/AlMgScZr-graded multi-material parts was investigated. It was revealed that the crack area at the interface reduced from 0.325 to 0.067 mm2 as the scanning speed increased from 2400 to 2800 mm/s and then increased to 0.161 mm2 at 3000 mm/s. A smooth, continuous-graded layer with good metallurgical bonding was fabricated at 2800 mm/s. The TiAl3 intermetallic compound was formed at the interface and underwent a transition from rod-like to coarse dendritic and finally to finer dendritic structure along the building direction. The Ti6Al4V/AlMgScZr-graded multi-material parts exhibited a graded decrease in microhardness from 374 HV0.2 on the Ti6Al4V side to 122 HV0.2 on the AlMgScZr side, and an excellent compressive strength of 1531 MPa was obtained at the optimal parameter of 2800 mm/s.
Dongdong Gu serves as the Editorial Board Member of the journal, but did not in any way involve in the editorial and peer-review process conducted for this paper, directly or indirectly.
- Tyagi SA, Manjaiah M. Laser additive manufacturing of titanium-based functionally graded materials: A review. J Mater Eng Perform. 2022;31(8):6131-6148. doi: 10.1007/s11665-022-07149-w
- Yan L, Chen Y, Liou F. Additive manufacturing of multi-material structures. Mater Sci Eng R Rep. 2018;129:1-16. doi: 10.1016/j.mser.2018.04.001
- Yao L, Xiao Z, Huang S, et al. The formation mechanism of metal-ceramic interlayer interface during laser powder bed fusion. Virtual Phys Prototy. 2023;18:2235324. doi: 10.1080/17452759.2023.2235324
- Mehrpouya M, Tuma D, Vaneker T, Afrasiabi M, Bambach M, Gibson I. Multimaterial powder bed fusion techniques. Rapid Prototyp J. 2022;28(11):1-19. doi: 10.1108/RPJ-01-2022-0014
- Heidarzadeh A, Mironav S, Kaibyshev R, et al. Friction stir welding/processing of metals and alloys: A comprehensive review on microstructural evolution. Prog Mater Sci. 2021;117:100752. doi: 10.1016/j.pmatsci.2020.100752
- Gu D, Shi X, Poprawe R, Bourell DL, Setchi R, Zhu J. Material-structure-performance integrated laser-metal additive manufacturing. Science. 2021;372(6545):eabg1487. doi: 10.1126/science.abg1487
- Zhai X, Jin L, Jiang J. A survey of additive manufacturing reviews. Mater Sci Addit Manuf. 2022;1(4):21. doi: 10.18063/msam.v1i4.21
- Wei C, Li L, Zhang X, et al. 3D printing of multiple metallic materials via modified selective laser melting. CIRP Ann. 2018;67(1):245-248. doi: 10.1016/j.cirp.2018.04.096
- Sing SL, Huang S, Goh GD. Emerging metallic systems for additive manufacturing: In-situ alloying and multi-metal processing in laser powder bed fusion. Prog Mater Sci. 2021;119:100795. doi: 10.1016/j.pmatsci.2021.100795
- Liu Y, Sing SL. A review of advances in additive manufacturing and the integration of high-performance polymers, alloys, and their composites. Mater Sci Addit Manuf. 2023;2(3):1587. doi: 10.36922/msam.1587
- Zhang C, Chen F, Huang ZF, et al. Additive manufacturing of functionally graded materials: A review. Mat Sci Eng A Struct. 2019;764:138209. doi: 10.1016/j.msea.2019.138209
- Yan L, Chen Y, Liou F. Additive manufacturing of functionally graded metallic materials using laser metal deposition. Addit Manuf. 2020;21:100901. doi: 10.1016/j.addma.2019.100901
- Chen WY, Zhang X, Li M. Laser powder bed fusion of Inconel 718 on 316 stainless steel. Addit Manuf. 2020;36:101500. doi: 10.1016/j.addma.2020.101500
- Chen J, Yang Y, Song C. Interfacial microstructure and mechanical properties of 316L/CuSn10 multi-material bimetallic structure fabricated by selective laser melting. Mater Sci Eng A Struct. 2019;752:75-85. doi: 10.1016/j.msea.2019.02.097
- Zhang Y, Bandyopadhyay A. Direct fabrication of compositionally graded Ti-Al2O3 multi-material structures using Laser Engineered Net Shaping. Addit Manuf. 2018;21:104-111. doi: 10.1016/j.addma.2018.03.001
- Wei C, Liu L, Cao H, et al. Cu10Sn to Ti6Al4V bonding mechanisms in laser-based powder bed fusion multiple material additive manufacturing with different build strategies. Addit Manuf. 2022;51:102588. doi: 10.1016/j.addma.2021.102588
- Sing SL, Huang S, Goh GD. Additive manufacturing of multiple materials by selective laser melting: Ti alloy to stainless steel via a Cu-alloy interlayer. Addit Manuf. 2020;31:100970. doi: 10.1016/j.addma.2019.100970
- Zhang J, Wang X, Gao J. Additive manufacturing of Ti-6Al-4V/Al-Cu-Mg multi-material structures with a Cu interlayer. Int J Mech Sci. 2023;256:108477. doi: 10.1016/j.ijmecsci.2023.108477
- Tan C, Chew Y, Bi G, et al. Additive manufacturing of steel-copper functionally graded material with ultrahigh bonding strength. J Mater Sci Technol. 2021;72:217-222. doi: 10.1016/j.jmst.2020.07.044
- Wei C, Zhao Z, Tang J, et al. Effect of interface-layer process parameters on forming quality of 316L/CuSn10 bimetals fabricated via laser powder bed fusion. Mater Lett. 2023;336:133896. doi: 10.1016/j.matlet.2023.133896
- Demir AG, Kim J, Caltabissetta F, et al. Enabling multi-material gradient structure in laser powder bed fusion. J Mater Process Technol. 2022 301: 117439. doi: 10.1016/j.jmatprotec.2021.117439
- Huang S, Kumar P, Yeong WY, Narayan RL, Ramamurty U. Fracture behavior of laser powder bed fusion fabricated Ti41Nb via in-situ alloying. Acta Mater. 2022;225:117593. doi: 10.1016/j.actamat.2021.117593
- Blakey-Milner B, Gradl P, Snedden G, et al. Metal additive manufacturing in aerospace: A review. Mater Des. 2021;209:110008. doi: 10.1016/j.matdes.2021.110008
- Kagerer S, Hudak OE, Schloffer M, Riedl H, Mayrhofer PH. TGO formation and oxygen diffusion in Al-rich gamma-TiAl PVD-coatings on TNM alloys. Scr Mater. 2022;210:114455. doi: 10.1016/j.scriptamat.2021.114455
- Hotz H, Zimmermann M, Gerco S, Kirsch B, Aurich JC. Additive manufacturing of functionally graded Ti-Al structures by laser-based direct energy deposition. J Manuf Process. 2021;68:1524-1534. doi: 10.1016/j.jmapro.2021.06.068
- Jing Z, Liu X, Li L, Wang W, Xu G, Chang L. Microstructure and mechanical properties of transition zone in laser additive manufacturing of TC4/AlSi12 bimetal structure. Mater Res Express. 2022;9(1):016513. doi: 10.1088/2053-1591/ac47c8
- Wu X, Zhang D, Yi D, et al. Interfacial characterization and reaction mechanism of Ti/Al multi-material structure during laser powder bed fusion process. Mater Charact. 2022;192:112195. doi: 10.1016/j.matchar.2022.112195
- Liu Y, Liu C, Liu W, et al. Microstructure and properties of Ti/Al lightweight graded material by direct laser deposition. Mater Sci Technol. 2018;34(8):945-951. doi: 10.1080/02670836.2017.1412042
- Kothari K, Radhakrishnan R, Wereley NM. Advances in gamma titanium aluminides and their manufacturing techniques. Prog Aerosp Sci. 2012;55:1-16. doi: 10.1016/j.paerosci.2012.04.001
- Kattner UR, Lin JC, Chang YA. Thermodynamic assessment and calculation of the Ti-Al system. Metall Trans A. 1992;23(8):2081-2090. doi: 10.1007/BF02646001
- Tian Y, Shen J, Hu S, et al. Effect of deposition layer on microstructure of Ti-Al bimetallic structures fabricated by wire and arc additive manufacturing. Sci Technol Weld Join. 2022;27(1):22-32. doi: 10.1080/13621718.2021.1996850
- Cook PS, Ritchie DJ. Determining the laser absorptivity of Ti-6Al-4V during laser powder bed fusion by calibrated melt pool simulation. Opt Laser Technol. 2023;162:109247. doi: 10.1016/j.optlastec.2023.109247
- Li Y, Tang X, Lu F, et al. Dual beam laser fusion-brazed Ti6Al4V/AA7075 dissimilar lap joint: Crack inhibition via inoculation with TiC nanoparticles. Mater Charact. 2022;191:112127. doi: 10.1016/j.matchar.2022.112127
- Gerold U, Herzig C. Titanium self-diffusion and chemical diffusion in bcc Ti-Al alloys. Defect Diffus Forum. 1997;143:437-442. doi: 10.4028/www.scientific.net/DDF.143-147.437
- Shi Q, Zhong G, Sun Y, Politis C, Yang S. Effects of laser melting plus remelting on interfacial macrosegregation and resulting microstructure and microhardness of laser additive manufactured H13/IN625 bimetals. J Manuf Process. 2021;71:345-355. doi: 10.1016/j.jmapro.2021.09.036
- Yao L, Huang S, Ramamurty U, Xiao Z. On the formation of “Fish-scale” morphology with curved grain interfacial microstructures during selective laser melting of dissimilar alloys. Acta Mater. 2021;220:117331. doi: 10.1016/j.actamat.2021.117331
- Xie H, Lv J. Precipation of TiAl3 in remelting Al-5Ti-1B and the grain refinement of 7050 alloy. Mater Res Express. 2021;8(6):066513. doi: 10.1088/2053-1591/ac0559
- Liu ZQ, Zhu XO, Yin GL, Zhou Q. Direct bonding of bimetallic structure from Ti6Al4V to Ti48Al2Cr2Nb alloy by laser additive manufacturing. Mater Sci Technol. 2022;38(1):39-44. doi: 10.1080/02670836.2021.2023287
- Xi L, Ding K, Zhang H, Gu D. In-situ synthesis of aluminum matrix nanocomposites by selective laser melting of carbon nanotubes modified Al-Mg-Sc-Zr alloys. J Alloy Compd. 2022; 891:162047. doi: 10.1016/j.jallcom.2021.162047
- Huang S, Kumar P, Lim CWJ, Radhakrishnan J, Ramamurty U. Fracture behavior of PH15-5 stainless steel manufactured via directed energy deposition. Mater Des. 2023;235:112421. doi: 10.1016/j.addma.2019.100970
- Karimi J, Antonov M, Kollo L, Prashanth KG. Role of laser remelting and heat treatment in mechanical and tribological properties of selective laser melted Ti6Al4V alloy. J Alloy Compd. 2022;897:163207. doi: 10.1016/j.jallcom.2021.163207
- Jiao Z, Ma C, Fu J, et al. The effects of Zr contents on microstructure and properties of laser additive manufactured Ti-6.5Al-3.5Mo-0.3Si-xZr alloys. J Alloy Compd. 2018;745:592-598. doi: 10.1016/j.jallcom.2018.02.079
- Bi J, Lei Z, Chen Y, et al. Microstructure and mechanical properties of a novel Sc and Zr modified 7075 aluminum alloy prepared by selective laser melting. Mat Sci Eng A Struct. 2019;768:138478. doi: 10.1016/j.msea.2019.138478
- Casati R, Lemke JN, Alarcon AZ, Vedani M. Aging behavior of high-strength Al alloy 2618 produced by selective laser melting. Metall Mater Trans A. 2017;48(2):575-579. doi: 10.1007/s11661-016-3883-y
- Zhang Y, Bandyopadhyay A. Direct fabrication of bimetallic Ti6Al4V+Al12Si structures via additive manufacturing. Addit Manuf. 2019;29:100783. doi: 10.1016/j.addma.2019.100783
- Zhang Y, Groden C, Nyberg E, et al. W7Ni3Fe-Ti6Al4V bimetallic layered structures via directed energy deposition. Virtual Phys Prototyp. 2023;18(1):e2137048. doi: 10.1080/17452759.2022.2137048
- Onuike B, Bandyopadhyay A. Functional bimetallic joints of Ti6Al4V to SS410. Addit Manuf. 2020;31:100931. doi: 10.1016/j.addma.2019.100931
- Zhang Y, Bandyopadhyay A. Influence of compositionally graded interface on microstructure and compressive deformation of 316L stainless steel to Al12Si aluminum alloy bimetallic structures. ACS Appl Mater Interfaces. 2021;13(7):9174-9185. doi: 10.1021/acsami.0c21478