Energy absorption and recoverability of Moore space-filling thin-walled structures
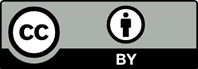
This paper proposes novel thin-walled structures inspired by Moore space-filling curves. Nine designs, featuring three fractal hierarchies (1st, 2nd, and 3rd orders) with three different relative densities (20%, 30%, and 40%), were used as cross-sectional configurations of the thin-walled structures. Specimens were manufactured using a material extrusion additive manufacturing technique, fused filament fabrication, with a carbon fiber-reinforced composite. Quasi-static compression tests from in-plane direction were conducted to investigate the influences of fractal hierarchy and relative density on the energy absorption capacity. Finite element models were developed to compare with the experiments and to further explore the 4th order structures. A certain level of compliance and snap-in instability were observed in all the structures. These properties show great potential for such thin-walled structures to absorb more energy by enduring large strain. Among them, the 2nd order structures exhibited the best energy absorption capacity. Furthermore, loading and unloading compression tests were performed on the 2nd and 3rd order structures (relative density of 20%) to evaluate their resilience toward displacement and damages. The residual strain and dissipated energy ratio demonstrated that the 2nd order structure outperformed the 3rd order structure owing to its less compliant feature. The integration of Moore curves with thin-walled structures contributes to great compliance and snap-in instability, offering a new approach to designing lightweight energy absorption structures.
Phuong Tran serves as the Editorial Board Member of the journal, but did not in any way involve in the editorial and peer-review process conducted for this paper, directly or indirectly.
Ma Y, Sugahara T, Yang Y, et al., 2015, A study on the energy absorption properties of carbon/aramid fiber filament winding composite tube. Compos Struct, 123: 301–311.
Nguyen-Van V, Liu J, Peng C, et al., 2022, Dynamic responses of bioinspired plastic-reinforced cementitious beams. Cement Concrete Compos, 133: 104682.
Nguyen-Van V, Wickramasinghe S, Ghazlan A, et al., 2020, Uniaxial and biaxial bioinspired interlocking composite panels subjected to dynamic loadings. Thin Walled Struct, 157: 107023.
Nguyen-Van V, Peng C, Hazell PJ, et al., 2023, Performance of meta concrete panels subjected to explosive load: Numerical investigations. In: Structural Concrete. United States: Wiley.
Sun G, Chen D, Zhu G, et al., 2022, Lightweight hybrid materials and structures for energy absorption: A state-of-the-art review and outlook. Thin Walled Struct, 172: 108760.
Mohsenizadeh M, Gasbarri F, Munther M, et al., 2018, Additively-manufactured lightweight Metamaterials for energy absorption. Mater Des, 139: 521–530.
Nguyen-Van V, Tran J, Peng C, et al., 2020, Bioinspired cellular cementitious structures for prefabricated construction: Hybrid design & performance evaluations. Autom Constr, 119: p. 103324.
Dang BL, Nguyen-Van V, Tran P, et al., 2022, Mechanical and hydrodynamic characteristics of emerged porous Gyroid breakwaters based on triply periodic minimal surfaces. Ocean Eng, 254: 111392.
Meredith J, Ebsworth R, Coles SR, et al., 2012, Natural fibre composite energy absorption structures. Compos Sci Technol, 72: 211–217.
Yang H, Lei H, Lu G, et al., 2020, Energy absorption and failure pattern of hybrid composite tubes under quasi-static axial compression. Compos B Eng, 198: 108217.
Tarlochan F, AlKhatib S, 2017, Energy Absorption Capabilities of Complex Thin Walled Structures. In: IOP Conference Series: Materials Science and Engineering. United Kingdom: IOP Publishing.
Nguyen-Van V, Choudhry NK, Panda B, et al., 2022, Performance of concrete beam reinforced with 3D printed Bioinspired primitive scaffold subjected to three-point bending. Autom Constr, 134: 104060.
Fu J, Liu Q, Kangmin L, et al., 2019, Design of bionic-bamboo thin-walled structures for energy absorption. Thin Walled Struct, 135: 400–413.
Nia AA, Hamedani JH, 2010, Hamedani, Comparative analysis of energy absorption and deformations of thin walled tubes with various section geometries. Thin Walled Struct, 48: 946–954.
Nia AA, Parsapour M, 2014, Comparative analysis of energy absorption capacity of simple and multi-cell thin-walled tubes with triangular, square, hexagonal and octagonal sections. Thin Walled Struct, 74: 155–165.
Wang S, Xia H, Liu YJ, 2022, Energy absorption characteristics of polygonal bio-inspired honeycomb column thin-walled structure under quasi-static uniaxial compression loading. Biomimetics (Basel), 7: 201.
Zhang XW, Su H, Yu TX, 2009, Energy absorption of an axially crushed square tube with a buckling initiator. Int J Impact Eng, 36: 402–417.
Xing BF, Dayong H, Sun YX, et al., 2015, Effects of hinges and deployment angle on the energy absorption characteristics of a single cell in a deployable energy absorber. Thin Walled Struct, 94: 107–119.
Ali M, Ohioma E, Kraft F, et al., 2015, Theoretical, numerical, and experimental study of dynamic axial crushing of thin walled pentagon and cross-shape tubes. Thin Walled Struct, 94: 253–272.
Liu YJ, 2008, Crashworthiness design of multi-corner thin-walled columns. Thin Walled Struct, 46: 1329–1337.
Wang J, Liu Y, Wang K, et al., 2022, Progressive collapse behaviors and mechanisms of 3D printed thin-walled composite structures under multi-conditional loading. Thin Walled Struct, 171: 108810.
Vinayagar K, Kumar AS, 2017, Crashworthiness analysis of double section bi-tubular thin-walled structures. Thin Walled Struct, 112: 184–193.
Zhang Y, Wang J, Wang C, et al., 2018, Crashworthiness of bionic fractal hierarchical structures. Mater Des, 158: 147–159.
Wang J, Zhang Y, He N, et al., 2018, Crashworthiness behavior of Koch fractal structures. Mater Des, 144: 229–244.
Gao Q, Liao W, 2021, Energy absorption of thin walled tube filled with gradient auxetic structures-theory and simulation. Int J Mech Sci, 201: 106475.
Huang J, Zheng Z, Deng X, et al., 2022, Crashworthiness analysis of gradient fractal thin-walled structure. Thin Walled Struct, 181: 110102.
Hao P, Du J, 2018, Energy absorption characteristics of bio-inspired honeycomb column thin-walled structure under impact loading. J Mech Behav Biomed Mater, 79: 301–308.
Nguyen-Van V, Wu C, Vogel F, et al., 2021, Mechanical performance of fractal-like cementitious lightweight cellular structures: Numerical investigations. Compos Struct, 269: 114050.
Li Z, Shen L, Wei K, et al., 2021, Compressive behaviors of fractal-like honeycombs with different array configurations under low velocity impact loading. Materials (Basel), 163: 107759. https://doi.org/10.3390/ma14175040
San Ha N, Pham TM, Chen W, et al., 2021, Crashworthiness analysis of bio-inspired fractal tree-like multi-cell circular tubes under axial crushing. Thin Walled Struct, 169: 108315. https://doi.org/10.1016/j.tws.2021.108315
He Q, Wang Y, Gu H, et al., 2022, The dynamic behavior of fractal-like tubes with Sierpinski hierarchy under axial loading. Eng Comput, 38: 1285–1298.
Li K, Feng Y, Gao Y, et al., 2020, Crashworthiness optimization design of aluminum alloy thin-walled triangle column based on bioinspired strategy. Materials, 13: 666.
Chen W, Wierzbicki T, 2001, Relative merits of single-cell, multi-cell and foam-filled thin-walled structures in energy absorption. Thin Walled Struct, 39: 287–306.
Dadrasi A, Beynaghi M, Fooladpanjeh S, 2019, Crashworthiness of thin-walled square steel columns reinforced based on fractal geometries. Trans Indian Inst Met, 72: 215–225.
Fan ZG, Lu LX, Wang J, 2015, Effect of fatigue damage on energy absorption properties of honeycomb paperboard. Shock Vib, 2015: 1–7.
Van Vuong N, Quan MH, 2019, Fatigue analysis of jacket support structure for offshore wind turbines. J Sci Technol Civil Eng, 13: 46–59.
Zou Q, Zhou X, Wang R, et al., 2022, Load-carrying and energy-absorbing performance of honeycombs with different cross sections under cyclic loading. Mat Today Commun, 33: 104582.
Wu C, Do TT, Tran PJ, 2021, Mechanical properties of polyjet 3d-printed composites inspired by space-filling peano curves. Polymers (Basel), 13: 3516. https://doi.org/10.3390/polym13203516
Wickramasinghe S, Do T, Tran P, 2022, Flexural behavior of 3D printed bio-inspired interlocking suture structures. MSAM, 1: 9.
Nguyen-Van V, Panda B, Zhang K, et al., 2021, Digital design computing and modelling for 3-D concrete printing. Autom Constr, 123: 103529.
Liu J, Nguyen-Van V, Panda B, et al., 2022, Additive manufacturing of sustainable construction materials and form-finding structures: A review on recent progresses. 3D Print Addit Manuf, 2022. 9: 12–34.
Nguyen-Van V, Li S, Liu J, et al., 2022, Modelling of 3D concrete printing process: A perspective on material and structural simulations. Addit Manuf, 2022: 103333.
Peng C, Tran P, Mouritz A, 2022, Compression and buckling analysis of 3D printed carbon fibre-reinforced polymer cellular composite structures. Compos Struct, 300: 116167.
Zhang Y, Wei Y, Bai J, et al., 2022, A novel seawater and sea sand concrete-filled FRP-carbon steel composite tube column: Cyclic axial compression behaviour and modelling. Compos Struct, 252: 113531.
Alhyari O, Newaz G, 2021, Energy absorption in carbon fiber composites with holes under quasi-static loading. C J Carbon Res, 7: 16.
Zhang Y, Lu Z, Yang Z, et al., Resilient carbon fiber network materials under cyclic compression. Carbon, 155: 344–352.
Peng C, Tran P, Nguyen-Xuan H, et al., 2020, Mechanical performance and fatigue life prediction of lattice structures: Parametric computational approach. Compos Struct, 235: 111821.
Bunsell AR, 2018, Handbook of Properties of Textile and Technical Fibres. United Kingdom: Woodhead Publishing.
Wickramasinghe S, Do T, Tran P, 2020, FDM-based 3D printing of polymer and associated composite: A review on mechanical properties, defects and treatments. Polymers, 12: 1529.
Zhao B, Chen W, Hu J, et al., 2015, An innovative methodology for measurement of stress distribution of inflatable membrane structures. Meas Sci Technol, 27: 025002.
Alderson A, Alderson K, 2007, Auxetic Materials. Proceedings of the Institution of Mechanical Engineers Part G, J Aerospace Eng, 221: 565–575.