Laser additive manufacturing of magnesium alloys and its biomedical applications
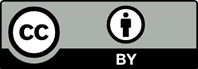
Biomedical magnesium (Mg) alloy with unique biodegradability and excellent biocompatibility is one of the most sought after materials in medical field for orthopedics applications. Nevertheless, the high corrosion rate and inadequate mechanical properties hinder its development. Apart from that, to obtain the best surgical result, the size and shape of the fixation implant need to be adapted to the individual case. Thus, additive manufacturing (AM) processes, such as laser powder bed fusion (LPBF), are used to overcome these issues. This work reviews the recent advancements in biodegradable Mg-based alloys prepared by LPBF for biomedical applications. The influence of feedstock features and manufacturing parameters on the formability and quality is delineated in detail. The mechanical performances, degradation behaviors, and biological behavior of the LPBF-processed parts are discussed. Furthermore, we also made some suggestions for the challenges of Mg alloys in LPBF processing and applications in biomedical.
Cijun Shuai serves as the Editorial Board Member of the journal, but did not in any way involve in the editorial and peer-review process conducted for this paper, directly or indirectly.
Xing F, Li S, Yin D, et al., 2022, Recent progress in Mg-based alloys as a novel bioabsorbable biomaterials for orthopedic applications. J Magnes Alloys, 10: 1428–1456. https://doi.org/10.1016/j.jma.2022.02.013
Tschon M, Boanini E, Sartori M, et al., 2022, Antiosteoporotic nanohydroxyapatite zoledronate scaffold seeded with bone marrow mesenchymal stromal cells for bone regeneration: A 3d in vitro model. Int J Mol Sci, 23: 5988. https://doi.org/10.3390/ijms23115988
Xia B, Chen G, 2022, Research progress of natural tissue-derived hydrogels for tissue repair and reconstruction. Int J Biol Macromol, 214: 480–491. https://doi.org/10.1016/j.ijbiomac.2022.06.137
Ni J, Ling H, Zhang S, et al., 2019, Three-dimensional printing of metals for biomedical applications. Mater Today Bio, 3: 100024. https://doi.org/10.1016/j.mtbio.2019.100024
Li J, Qin L, Yang K, et al., 2020, Materials evolution of bone plates for internal fixation of bone fractures: A review. J Mater Sci Technol, 36: 190–208. https://doi.org/10.1016/j.jmst.2019.07.024
Zhang B, Su Y, Zhou J, et al., 2021, Toward a better regeneration through implant-mediated immunomodulation: Harnessing the immune responses. Adv Sci, 8: 2100446. https://doi.org/10.1002/advs.202100446
Bairagi D, Mandal S 2022, A comprehensive review on biocompatible Mg-based alloys as temporary orthopaedic implants: Current status, challenges, and future prospects. J Magnes Alloys, 10: 627–669. https://doi.org/10.1016/j.jma.2021.09.005
Venezuela JJ, Johnston S, Dargusch MS, 2019, The prospects for biodegradable zinc in wound closure applications. Adv Healthc Mater, 8: 1900408. https://doi.org/10.1002/adhm.201900408
Kabir H, Munir K, Wen C, et al., 2021, Recent research and progress of biodegradable zinc alloys and composites for biomedical applications: Biomechanical and biocorrosion perspectives. Bioact Mater, 6: 836–879. https://doi.org/10.1016/j.bioactmat.2020.09.013
Qin Y, Wen P, Guo H, et al., 2019, Additive manufacturing of biodegradable metals: Current research status and future perspectives. Acta Biomater, 98: 3–22. https://doi.org/10.1016/j.actbio.2019.04.046
Venezuela J, Dargusch MS, 2019, The influence of alloying and fabrication techniques on the mechanical properties, biodegradability and biocompatibility of zinc: A comprehensive review. Acta Biomater, 87: 1–40. https://doi.org/10.1016/j.actbio.2019.01.035
Shahin M, Wen C, Munir K, et al., 2022, Mechanical and corrosion properties of graphene nanoplatelet-reinforced Mg-Zr and Mg-Zr-Zn matrix nanocomposites for biomedical applications. J Magnes Alloys, 10: 458–477. https://doi.org/10.1016/j.jma.2021.05.011
Bommala VK, Krishna MG, Rao CT, 2019, Magnesium matrix composites for biomedical applications: A review. J Magnes Alloys, 7: 72–79. https://doi.org/10.1016/j.jma.2018.11.001
Wang JL, Xu JK, Hopkins C, et al., 2020, Biodegradable magnesium-based implants in orthopedics-a general review and perspectives. Adv Sci, 7: 1902443. https://doi.org/10.1002/advs.201902443
Chandra G, Pandey A, 2020, Biodegradable bone implants in orthopedic applications: A review. Biocybern Biomed Eng, 40: 596–610. https://doi.org/10.1016/j.bbe.2020.02.003
Wu CL, Xie WJ, Man HC, 2022, Laser additive manufacturing of biodegradable Mg-based alloys for biomedical applications: A review. J Magnes Alloys, 10: 915–937. https://doi.org/10.1016/j.jma.2021.12.014
Wu S, Liu X, Yeung KW, et al., 2014, Biomimetic porous scaffolds for bone tissue engineering. Mater Sci Eng R Rep, 80: 1–36. https://doi.org/10.1016/j.mser.2014.04.001
Yang Y, He C, Dianyu E, et al., 2020, Mg bone implant: Features, developments and perspectives. Mater Design, 185: 108259. https://doi.org/10.1016/j.matdes.2019.108259
Li X, Liu X, Wu S, et al., 2016, Design of magnesium alloys with controllable degradation for biomedical implants: From bulk to surface. Acta Biomater, 45: 2–30. https://doi.org/10.1016/j.actbio.2016.09.005
Yazdimamaghani M, Razavi M, Vashaee D, et al., 2017, Porous magnesium-based scaffolds for tissue engineering. Mater Sci Eng C, 71: 1253–1266. https://doi.org/10.1016/j.msec.2016.11.027
Li C, Guo C, Fitzpatrick V, et al., 2020, Design of biodegradable, implantable devices towards clinical translation. Nat Rev Mater, 5: 61–81. https://doi.org/10.1038/s41578-019-0150-z
Malladi L, Mahapatro A, Gomes AS, 2018, Fabrication of magnesium-based metallic scaffolds for bone tissue engineering. Mater Technol, 33: 173–182. https://doi.org/10.1080/10667857.2017.1404278
Payr E, 1900, Beitrage zur Technik der Blutgesfass und Nervennaht nebst Mittheilungen die Verwendung eines Resorbierharen Metalles in der Chirurgie. Arch Klin Chir, 62: 67–71.
Lambotte A, 1909, Technique et indication des protheses dans le traitement des fractures. Presse Med, 17: 321.
Mcbride ED, 1938, Absorbable metal in bone surgery: A further report on the use of magnesium alloys. J Am Med Assoc, 111: 2464–2467. https://doi.org/10.1001/jama.1938.02790530018007
Witte F, 2010, The history of biodegradable magnesium implants: A review. Acta Biomater, 6: 1680–1692. https://doi.org/10.1016/j.actbio.2010.02.028
Biber R, Pauser J, Geßlein M, et al., 2016, Magnesium-based absorbable metal screws for intra-articular fracture fixation. Case Rep Orthop, 2016: 9673174. https://doi.org/10.1155/2016/9673174
Chaya A, Yoshizawa S, Verdelis K, et al., 2015, In vivo study of magnesium plate and screw degradation and bone fracture healing. Acta Biomater, 18: 262–269. https://doi.org/10.1016/j.actbio.2015.02.010
Zhao D, Huang S, Lu F, et al., 2016, Vascularized bone grafting fixed by biodegradable magnesium screw for treating osteonecrosis of the femoral head. Biomaterials, 81: 84–92. https://doi.org/10.1016/j.biomaterials.2015.11.038
Wang Z, Sun Z, Han B, et al., 2020, Biological behavior exploration of a paclitaxel-eluting poly-l-lactide-coated Mg-Zn-Y-Nd alloy intestinal stent in vivo. RSC Adv, 10: 15079–15090. https://doi.org/10.1039/C9RA10156J
Sing SL, 2022, Perspectives on additive manufacturing enabled beta-titanium alloys for biomedical applications. Int J Bioprint, 8: 478. https://doi.org/10.18063/ijb.v8i1.478
Chen Z, Han C, Gao M, et al., 2022, A review on qualification and certification for metal additive manufacturing. Virtual Phys Prototyp, 17: 382–405. https://doi.org/10.1080/17452759.2021.2018938
Ng CC, Savalani M, Man HC, 2011, Fabrication of magnesium using selective laser melting technique. Rapid Prototyp J, 17: 479–490. https://doi.org/10.1108/13552541111184206
Irrinki H, Nath SD, Alhofors M, et al., 2019, Microstructures, properties, and applications of laser sintered 17-4PH stainless steel. J Am Ceram Soc, 102: 5679–5690. https://doi.org/10.1111/jace.16372
Hoeges S, Zwiren A, Schade C, 2017, Additive manufacturing using water atomized steel powders. Metal Powder Rep, 72: 111–117. https://doi.org/10.1016/j.mprp.2017.01.004
Moghimian P, Poirié T, Habibnejad-Korayem M, et al., 2021, Metal powders in additive manufacturing: A review on reusability and recyclability of common titanium, nickel and aluminum alloys. Addit Manuf, 43: 102017. https://doi.org/10.1016/j.addma.2021.102017
Zheng D, Li Z, Jiang Y, et al., 2022, Effect of multiple thermal cycles on the microstructure evolution of GA151K alloy fabricated by laser-directed energy deposition. Addit Manuf, 57: 102957. https://doi.org/10.1016/j.addma.2022.102957
Aboulkhair NT, Simonelli M, Parry L, et al., 2019, 3D printing of aluminium alloys: Additive manufacturing of aluminium alloys using selective laser melting. Prog Mater Sci, 106: 100578. https://doi.org/10.1016/j.pmatsci.2019.100578.
Ji X, Mirkoohi E, Ning J, et al., 2020, Analytical modeling of post-printing grain size in metal additive manufacturing. Opt Lasers Eng, 124: 105805. https://doi.org/10.1016/j.optlaseng.2019.105805
He C, Bin S, Wu P, et al., 2017, Microstructure evolution and biodegradation behavior of laser rapid solidified Mg-Al-Zn alloy. Metals, 7: 105. https://doi.org/10.3390/met7030105
Shuai C, Yang Y, Wu P, et al., 2017, Laser rapid solidification improves corrosion behavior of Mg-Zn-Zr alloy. J Alloys Compd, 691: 961–969. https://doi.org/10.1016/j.jallcom.2016.09.019
Spierings AB, Dawson K, Dumitraschkewitz P, et al., 2018, Microstructure characterization of SLM-processed Al-Mg- Sc-Zr alloy in the heat treated and HIPed condition. Addit Manuf, 20: 173–181. https://doi.org/10.1016/j.addma.2017.12.011
Buhairi MA, Foudzi FM, Jamhari FI, et al., 2022, Review on volumetric energy density: Influence on morphology and mechanical properties of Ti6Al4V manufactured via laser powder bed fusion. Prog Addit Manuf, https://doi.org/10.1007/s40964-022-00328-0
Liang J, Lei Z, Chen Y, et al., 2022, Formability, microstructure, and thermal crack characteristics of selective laser melting of ZK60 magnesium alloy. Mater Sci Eng A, 839: 142858. https://doi.org/10.1016/j.msea.2022.142858
Esmaily M, Zeng Z, Mortazavi AN, et al., 2020, A detailed microstructural and corrosion analysis of magnesium alloy WE43 manufactured by selective laser melting. Addit Manuf, 35: 101321. https://doi.org/10.1016/j.addma.2020.101321
Wei K, Gao M, Wang Z, Zeng X, 2014, Effect of energy input on formability, microstructure and mechanical properties of selective laser melted AZ91D magnesium alloy. Mater Sci Eng A, 611: 212–222. https://doi.org/10.1016/j.msea.2014.05.092
Yang Y, Wu P, Lin X, et al., 2016, System development, formability quality and microstructure evolution of selective laser-melted magnesium. Virtual Phys Prototyp, 11: 173–181. https://doi.org/10.1080/17452759.2016.1210522
Sezer N, Evis Z, Koç M, 202, Additive manufacturing of biodegradable magnesium implants and scaffolds: Review of the recent advances and research trends. J Magnes Alloys, 9: 392–415. https://doi.org/10.1016/j.jma.2020.09.014
Liu S, Yang W, Shi X, et al., 2019, Influence of laser process parameters on the densification, microstructure, and mechanical properties of a selective laser melted AZ61 magnesium alloy. J Alloys Compd, 808: 151160. https://doi.org/10.1016/j.jallcom.2019.06.261
Liu C, Zhang M, Chen C, 2017, Effect of laser processing parameters on porosity, microstructure and mechanical properties of porous Mg-Ca alloys produced by laser additive manufacturing. Mater Sci Eng A, 703: 359-371. https://doi.org/10.1016/j.msea.2017.07.031
Yang Y, Lu C, Peng S, et al., 2020, Laser additive manufacturing of Mg-based composite with improved degradation behaviour. Virtual Phys Prototyp, 15: 278–293. https://doi.org/10.1080/17452759.2020.1748381
Zhang M, Chen C, Liu C, et al., Study on porous Mg-Zn-Zr ZK61 alloys produced by laser additive manufacturing. Metals, 8: 635. https://doi.org/10.3390/met8080635
Deng Q, Wu Y, Wu Q, et al., 2022, Microstructure evolution and mechanical properties of a high-strength Mg-10Gd-3Y- 1Zn-0.4Zr alloy fabricated by laser powder bed fusion. Addit Manuf, 49: 102517. https://doi.org/10.1016/j.addma.2021.102517
Wang T, Meng Q, Araby S, et al., 2021, Non-oxidized graphene/metal composites by laser deposition additive manufacturing. J Alloys Compd, 882: 160724. https://doi.org/10.1016/j.jallcom.2021.160724
Cao X, Jahazi M, Immarigeon JP, et al., 2006, A review of laser welding techniques for magnesium alloys. J Mater Process Technol, 171: 188–204. https://doi.org/10.1016/j.jmatprotec.2005.06.068
Manakari V, Parande G, Gupta M, 2017, Selective laser melting of magnesium and magnesium alloy powders: A review. Metals, 7: 2. https://doi.org/10.3390/met7010002
Gangireddy S, Gwalani B, Liu K, et al., 2019, Microstructure and mechanical behavior of an additive manufactured (AM) WE43-Mg alloy. Addit Manuf, 26: 53–64. https://doi.org/10.1016/j.addma.2018.12.015
Hosseini E, Popovich VA, 2019, A review of mechanical properties of additively manufactured Inconel 718. Addit Manuf, 30: 100877. https://doi.org/10.1016/j.addma.2019.100877
Wang Y, Fu P, Wang N, et al., 2020, Challenges and solutions for the additive manufacturing of biodegradable magnesium implants. Engineering, 6: 1267–1275. https://doi.org/10.1016/j.eng.2020.02.015
Dou Y, Cai S, Ye X, et al., 2013, 45S5 bioactive glass-ceramic coated AZ31 magnesium alloy with improved corrosion resistance. Surf Coat Technol, 228: 154–161. https://doi.org/10.1016/j.surfcoat.2013.04.022
Rojaee R, Fathi M, Raeissi K 2013, Electrophoretic deposition of nanostructured hydroxyapatite coating on AZ91 magnesium alloy implants with different surface treatments. Appl Surf Sci, 285: 664–673. https://doi.org/10.1016/j.apsusc.2013.08.108
Razavi M, Fathi M, Savabi O, et al., 2014, Controlling the degradation rate of bioactive magnesium implants by electrophoretic deposition of akermanite coating. Ceram Int, 40: 3865–3872. https://doi.org/10.1016/j.ceramint.2013.08.027
Kopp A, Derra T, Müther M, et al., 2019, Influence of design and postprocessing parameters on the degradation behavior and mechanical properties of additively manufactured magnesium scaffolds. Acta Biomater, 98: 23–35. https://doi.org/10.1016/j.actbio.2019.04.012
Han J, Chen J, Peng L, et al., 2017, Microstructure, texture and mechanical properties of friction stir processed Mg-14Gd alloys. Mater Design, 130: 90–102. https://doi.org/10.1016/j.matdes.2017.05.046
Huang C, Yan X, Zhao L, et al., 2019, Ductilization of selective laser melted Ti6Al4V alloy by friction stir processing. Mater Sci Eng A, 755: 85–96. https://doi.org/10.1016/j.msea.2019.03.133
Macías JG, Elangeswaran C, Zhao L, et al., 2019, Ductilisation and fatigue life enhancement of selective laser melted AlSi10Mg by friction stir processing. Scr Mater, 170: 124–128. https://doi.org/10.1016/j.scriptamat.2019.05.044
Deng Q, Wu Y, Su N, et al., 2021, Influence of friction stir processing and aging heat treatment on microstructure and mechanical properties of selective laser melted Mg-Gd-Zr alloy. Addit Manuf, 44: 102036. https://doi.org/10.1016/j.addma.2021.102036
Alfieri V, Argenio P, Caiazzo F, et al., 2017, Reduction of surface roughness by means of laser processing over additive manufacturing metal parts. Materials. 10: 30. https://doi.org/10.3390/ma10010030
Basha SM, Bhuyan M, Basha MM, et al., 2020, Laser polishing of 3D printed metallic components: A review on surface integrity. Mater Today Proc, 26: 2047–2054. https://doi.org/10.1016/j.matpr.2020.02.443
Zhang X, Li XW, Li JG, et al., 2014, Preparation and mechanical property of a novel 3D porous magnesium scaffold for bone tissue engineering. Mater Sci Eng C, 42: 362–367. https://doi.org/10.1016/j.msec.2014.05.044
Hyer H, Zhou L, Benson G, et al., 2020, Additive manufacturing of dense WE43 Mg alloy by laser powder bed fusion. Addit Manuf, 33: 101123. https://doi.org/10.1016/j.addma.2020.101123
Fang X, Yang J, Wang S, et al., 2022, Additive manufacturing of high performance AZ31 magnesium alloy with full equiaxed grains: Microstructure, mechanical property, and electromechanical corrosion performance. J Mater Proc Technol, 300: 117430. https://doi.org/10.1016/j.jmatprotec.2021.117430
Wang Y, Huang H, Jia G, et al., 2021, Fatigue and dynamic biodegradation behavior of additively manufactured Mg scaffolds. Acta Biomater, 135: 705–722. https://doi.org/10.1016/j.actbio.2021.08.040
Chen J, Wu P, Wang Q, et al., 2016, Influence of alloying treatment and rapid solidification on the degradation behavior and mechanical properties of Mg. Metals, 6: 259. https://doi.org/10.3390/met6110259
Liu J, Liu B, Min S, et al., 2022, Biodegradable magnesium alloy WE43 porous scaffolds fabricated by laser powder bed fusion for orthopedic applications: Process optimization, in vitro and in vivo investigation. Bioact Mater, 16: 301–319. https://doi.org/10.1016/j.bioactmat.2022.02.020
Hyer H, Zhou L, Liu Q, et al., 2021, High strength WE43 microlattice structures additively manufactured by laser powder bed fusion. Materialia, 16: 101067. https://doi.org/10.1016/j.mtla.2021.101067
Zhang WN, Wang LZ, Feng ZX, et al., 2020, Research progress on selective laser melting (SLM) of magnesium alloys: A review. Optik, 207: 163842. https://doi.org/10.1016/j.ijleo.2019.163842
Shuai C, Li S, Peng S, et al., 2019, Biodegradable metallic bone implants. Mater Chem Front, 3: 544–562. https://doi.org/10.1039/C8QM00507A
Liu J, Lin Y, Bian D, et al., 2019, In vitro and in vivo studies of Mg-30Sc alloys with different phase structure for potential usage within bone. Acta Biomater, 98: 50–66. https://doi.org/10.1016/j.actbio.2019.03.009
Han HS, Loffredo S, Jun I, et al., 2019, Current status and outlook on the clinical translation of biodegradable metals. Mater Today, 23: 57–71. https://doi.org/10.1016/j.mattod.2018.05.018
Cao F, Shi Z, Song GL, et al., 2013, Corrosion behaviour in salt spray and in 3.5% NaCl solution saturated with Mg(OH)2 of as-cast and solution heat-treated binary Mg-X alloys: X=Mn, Sn, Ca, Zn, Al, Zr, Si, Sr. Corros Sci, 76: 60–97. https://doi.org/10.1016/j.corsci.2013.06.030
Peng Q, Huang Y, Zhou L, et al., 2010, Preparation and properties of high purity Mg-Y biomaterials. Biomaterials, 31: 398–403. https://doi.org/10.1016/j.biomaterials.2009.09.065
Shuai S, Guo E, Zheng Q, et al., 2016, Three-dimensional α-Mg dendritic morphology and branching structure transition in Mg-Zn alloys. Mater Charact, 118: 304–308. https://doi.org/10.1016/j.matchar.2016.06.009
Li J, Xie D, Yu H, et al., 2020, Microstructure and mechanical property of multi-pass low-strain rolled Mg-Al-Zn-Mn alloy sheet. J Alloys Compd, 835: 155228. https://doi.org/10.1016/j.jallcom.2020.155228
Luo Q, Guo Y, Liu B, et al., 2020, Thermodynamics and kinetics of phase transformation in rare earth-magnesium alloys: A critical review. J Mater Sci Technol, 44: 171–190. https://doi.org/10.1016/j.jmst.2020.01.022
Leleu S, Rives B, Bour J, et al., 2018, On the stability of the oxides film formed on a magnesium alloy containing rare-earth elements. Electrochim Acta, 290: 586–594. https://doi.org/10.1016/j.electacta.2018.08.093
Willbold E, Gu X, Albert D, et al., 2015, Effect of the addition of low rare earth elements (lanthanum, neodymium, cerium) on the biodegradation and biocompatibility of magnesium. Acta Biomater, 11: 554–562. https://doi.org/10.1016/j.actbio.2014.09.041
Wang C, Shuai Y, Yang Y, et al., 2022, Amorphous magnesium alloy with high corrosion resistance fabricated by laser powder bed fusion. J Alloys Compd, 897: 163247. https://doi.org/10.1016/j.jallcom.2021.163247
Chen S, Tu J, Hu Q, et al., 2017, Corrosion resistance and in vitro bioactivity of Si-containing coating prepared on a biodegradable Mg-Zn-Ca bulk metallic glass by micro-arc oxidation. J Non Cryst Solids, 456: 125–131. https://doi.org/10.1016/j.jnoncrysol.2016.11.011
Zhang D, Qin Y, Feng W, et al., 2019, Microstructural evolution of the amorphous layers on Mg-Zn-Ca alloy during laser remelting process. Surf Coat Technol, 363: 87–94. https://doi.org/10.1016/j.surfcoat.2019.02.051
Zberg B, Arata ER, Uggowitzer PJ, et al., 2009, Tensile properties of glassy MgZnCa wires and reliability analysis using Weibull statistics. Acta Mater, 57: 3223–3231. https://doi.org/10.1016/j.actamat.2009.03.028
Shuai C, Liu L, Zhao M, et al., 2018, Microstructure, biodegradation, antibacterial and mechanical properties of ZK60-Cu alloys prepared by selective laser melting technique. J Mater Sci Technol, 34: 1944–1952. https://doi.org/10.1016/j.jmst.2018.02.006
Spriano S, Yamaguchi S, Baino F, et al., 2018, A critical review of multifunctional titanium surfaces: New frontiers for improving osseointegration and host response, avoiding bacteria contamination. Acta Biomater, 79: 1–22. https://doi.org/10.1016/j.actbio.2018.08.013
Ouyang P, Dong H, He X, et al., 2019, Hydromechanical mechanism behind the effect of pore size of porous titanium scaffolds on osteoblast response and bone ingrowth. Mater Design, 183: 108151.https://doi.org/10.1016/j.matdes.2019.108151
Rojaee R, Fathi M, Raeissi K, 2013, Controlling the degradation rate of AZ91 magnesium alloy via sol-gel derived nanostructured hydroxyapatite coating. Mater Sci Eng C, 33: 3817–3825. https://doi.org/10.1016/j.msec.2013.05.014
Tian M, Cai S, Ling L, et al., 2022, Superhydrophilic hydroxyapatite/hydroxypropyltrimethyl ammonium chloride chitosan composite coating for enhancing the antibacterial and corrosion resistance of magnesium alloy. Prog Org Coat, 165: 106745. https://doi.org/10.1016/j.porgcoat.2022.106745
Roshan NR, Hassannejad H, Nouri A, 2021, Corrosion and mechanical behaviour of biodegradable PLA-cellulose nanocomposite coating on AZ31 magnesium alloy. Surf Eng, 37: 236–245. https://doi.org/10.1080/02670844.2020.1776093
Dutta S, Devi KB, Mandal S, et al., 2019, In vitro corrosion and cytocompatibility studies of hot press sintered magnesium-bioactive glass composite. Materialia, 5: 100245. https://doi.org/10.1016/j.mtla.2019.100245
Kang YG, Wei J, Shin JW, et al., 2018, Enhanced biocompatibility and osteogenic potential of mesoporous magnesium silicate/polycaprolactone/wheat protein composite scaffolds. Int J Nanomed, 13: 1107–1117. https://doi.org/10.2147/ijn.S157921
Gong X, Zeng D, Groeneveld-Meijer W, et al., 2022, Additive manufacturing: A machine learning model of process-structure-property linkages for machining behavior of Ti-6Al-4V. Mater Sci Addit Manuf, 1: 6. https://doi.org/10.18063/msam.v1i1.6
Sing SL, Kuo CN, Shih CT, et al., 2021, Perspectives of using machine learning in laser powder bed fusion for metal additive manufacturing. Virtual Phys Prototyp, 16: 372– 386. https://doi.org/10.1080/17452759.2021.1944229