Influence of Y2O3 reinforcement particles during heat treatment of IN718 composite produced by laser powder bed fusion
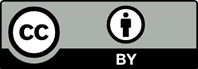
A metal matrix composite with Inconel 718 as the base metal and yttrium oxide (Y2O3) as the reinforcement particles was fabricated by the laser powder bed fusion technology. This paper presents a comprehensive study on the influence of the Y2O3 reinforcement particles on the microstructures and mechanical properties of the heat-treated printed composite. Complex precipitates formation between the Y2O3 nanoparticles and the carbonitride precipitates were shown. The complex precipitates separated into individual Y2O3 and titanium nitride (TiN) nanoparticles after heat treatment. Nano-sized Y-Ti-O precipitates were observed after solutionization due to the release of supersaturated Y in the metal matrix. Grain refinement was also observed in the heat-treated composites due to the high number of nano-sized precipitates. After solutionizing and aging, the grain size of the Y2O3-reinforced sample is 28.2% and 33.9% smaller, respectively, than that of the monolithic Inconel 718 sample. This effectively reduced the segregation of Nbat the grain boundaries and thus, γ′ and γ′′ precipitates were distributed in the metal matrix more homogeneously. Combined with the increased Orowan strengthening from a significantly higher number of nano-sized precipitates and grain boundary strengthening, the composite achieved higher yield strength, and ultimate tensile strength (1099.3 MPa and 1385.5 MPa, respectively) than those of the monolithic Inconel 718 (1015.5 MPa and 1284.3 MPa, respectively).
Sharon Mui Ling Nai serves as the Editorial Board Member of the journal, but did not in any way involve in the editorial and peer-review process conducted for this paper, directly or indirectly.
Ibrahim IA, Mohamed FA, Lavernia EJ, 1991, Particulate reinforced metal matrix composites-a review. J Mater Sci, 26: 1137–1156. https://doi.org/10.1007/BF00544448
Gu DD, Meiners W, Wissenbach K, et al., 2012, Laser additive manufacturing of metallic components: Materials, processes and mechanisms. Int Mater Rev, 57: 133–164. https://doi.org/10.1179/1743280411Y.0000000014
Zhang YC, Li ZG, Nie PL, et al., 2013, Effect of ultrarapid cooling on microstructure of laser cladding IN718 coating. Surf Eng, 29: 414–418. https://doi.org/10.1179/1743294413Y.0000000142
Singh L, Singh B, Saxena KK, 2020, Manufacturing techniques for metal matrix composites (MMC): An overview. Adv Mater Process Technol, 6: 224–240. https://doi.org/10.1080/2374068X.2020.1729603
Sharma V, Prakash U, Kumar BV, 2015, Surface composites by friction stir processing: A review. J Mater Process Technol, 224: 117–134. https://doi.org/10.1016/j.jmatprotec.2015.04.019
Akbari M, Asadi P, Asiabaraki HR, 2022, Investigation of wear and microstructural properties of A356/TiC composites fabricated by FSP. Surf Rev Lett, 29: 1–10. https://doi.org/10.1142/S0218625X2250130X
Akbari M, Asadi P, 2021, Simulation and experimental investigation of multi-walled carbon nanotubes/aluminum composite fabrication using friction stir processing. Proc Inst Mech Eng Part E J Process Mech Eng, 235: 2165–2179. https://doi.org/10.1177/09544089211034029
Rohatgi PK, Asthana R, Das S, 1986, Solidification, structures, and properties of cast metal-ceramic particle composites. Int Met Rev, 31: 115–139. https://doi.org/10.1179/imtr.1986.31.1.115
Shi Z, Han F, 2015, Microstructures and properties of cast T91-ODS alloys. Mater Res Innov, 19: S5832–S5835. https://doi.org/10.1179/1432891714Z.0000000001202
Etemadi R, Wang B, Pillai KM, et al., 2018, Pressure infiltration processes to synthesize metal matrix composites-A review of metal matrix composites, the technology and process simulation. Mater Manuf Process, 33: 1261–1290. https://doi.org/10.1080/10426914.2017.1328122
S-De-la-muela AM, Cambronero LE, Ruiz-Román JM, 2020, Molten metal infiltration methods to process metal matrix syntactic foams. Metals (Basel), 10: 149. https://doi.org/10.3390/met10010149
Kong D, Dong C, Ni X, et al., 2019, Effect of TiC content on the mechanical and corrosion properties of Inconel 718 alloy fabricated by a high-throughput dual-feed laser metal deposition system. J Alloys Compd, 803: 637–648. https://doi.org/10.1016/j.jallcom.2019.06.317
Gu D, Zhang H, Dai D, et al., 2019, Laser additive manufacturing of nano-TiC reinforced Ni-based nanocomposites with tailored microstructure and performance. Compos Part B Eng, 163: 585–597. https://doi.org/10.1016/j.compositesb.2018.12.146
Tang B, Tan Y, Zhang Z, et al., 2020, Effects of process parameters on geometrical characteristics, microstructure and tribological properties of TiB2 reinforced Inconel 718 alloy composite coatings by laser cladding. Coatings, 10: 76. https://doi.org/10.3390/coatings10010076
Dhanya MS, Shukla AK, Dineshraj S, et al., 2019, Processing and characterization of yttria-dispersed Inconel 718 ODS alloy. Trans Indian Inst Met, 72: 1395–1398. https://doi.org/10.1007/s12666-019-01649-5
Khalaj O, Mašek B, Jirková H, et al., 2017, Experimental study on thermomechanical properties of new-generation ODS alloys. Zenodo, 11: 501–504. https://doi.org/10.5281/zenodo.1131439
Wang G, Huang L, Zhao P, et al., 2020, Effect of heat treatment on microstructure and mechanical properties of ODS nickel-based superalloy via strengthening mechanism. JOM, 72: 3279–3287. https://doi.org/10.1007/s11837-020-04220-6
Chun YB, Mao X, Han CH, et al., 2017, Microstructural evolution and tensile properties of oxide dispersion strengthened Alloy 617 at elevated temperatures. Mater Sci Eng A, 706: 161–171. https://doi.org/10.1016/j.msea.2017.09.009
Auger MA, Leguey T, Muñoz A, et al., 2011, Microstructure and mechanical properties of ultrafine-grained Fe-14Cr and ODS Fe-14Cr model alloys. J Nucl Mater, 417: 213–216. https://doi.org/10.1016/j.jnucmat.2010.12.060
Fintová S, Kuběna I, Luptáková N, et al., 2020, Development of advanced Fe-Al-O ODS alloy microstructure and properties due to heat treatment. J Mater Res, 35: 2789–2797. https://doi.org/10.1557/jmr.2020.278
De Sanctis M, Fava A, Lovicu G, et al., 2017, Mechanical characterization of a nano-ODS steel prepared by low-energy mechanical alloying. Metals (Basel), 7: 283. https://doi.org/10.3390/met7080283
Luu DN, Zhou W, Nai SM, 2022, Mitigation of liquation cracking in selective laser melted Inconel 718 through optimization of layer thickness and laser energy density. J Mater Process Technol, 299: 117374. https://doi.org/10.1016/j.jmatprotec.2021.117374
Luu DN, Zhou W, Nai SM, 2022, Influence of nano-Y₂O₃ addition on the mechanical properties of selective laser melted Inconel 718. Mater Sci Eng A, 845: 143233. https://doi.org/10.1016/j.msea.2022.143233
Yeh AC, Lu KW, Kuo CM, et al., 2011, Effect of serrated grain boundaries on the creep property of Inconel 718 superalloy. Mater Sci Eng A, 530: 525–529. https://doi.org/10.1016/j.msea.2011.10.014
Deng DW, Wang CG, Liu QQ, et al., 2015, Effect of standard heat treatment on microstructure and properties of borided Inconel 718. Trans Nonferrous Met Soc China, 25: 437–443. https://doi.org/10.1016/S1003-6326(15)63621-4
Zhang Y, Li Z, Nie P, et al., 2013, Effect of heat treatment on niobium segregation of laser-cladded IN718 alloy coating. Metall Mater Trans A Phys Metall Mater Sci, 44: 708–716. https://doi.org/10.1007/s11661-012-1459-z
Sui S, Chen J, Ma L, et al., 2019, Microstructures and stress rupture properties of pulse laser repaired Inconel 718 superalloy after different heat treatments. J Alloys Compd, 770: 125–135. https://doi.org/10.1016/j.jallcom.2018.08.063
Zhao Y, Li K, Gargani M, et al., 2020, A comparative analysis of Inconel 718 made by additive manufacturing and suction casting: Microstructure evolution in homogenization. Addit Manuf, 36: 101404. https://doi.org/10.1016/j.addma.2020.101404
Kumara C, Balachandramurthi AR, Goel S, et al., 2020, Toward a better understanding of phase transformations in additive manufacturing of Alloy 718. Materialia, 13: 100862. https://doi.org/10.1016/j.mtla.2020.100862
Mills WJ, 1984, Effect of heat treatment on the tensile and fracture toughness behavior of Alloy 718 weldments. Weld J, 63(8): 237s-245s.
Cao Y, Bai P, Liu F, et al., 2019, Investigation on the precipitates of IN718 alloy fabricated by selective laser melting. Metals (Basel), 9: 1128. https://doi.org/10.3390/met9101128
Li X, Chu H, Chen Y, et al., 2019, Microstructure and properties of the laser cladding ODS layers on CLAM steel. Surf Coatings Technol, 357: 172–179. https://doi.org/10.1016/j.surfcoat.2018.10.006
Guo Y, Li M, Chen C, et al., 2020, Oxide dispersion strengthened FeCoNi concentrated solid-solution alloys synthesized by mechanical alloying. Intermetallics, 117: 106674. https://doi.org/10.1016/j.intermet.2019.106674
Shi Y, Lu Z, Yu L, et al., 2020, Microstructure and tensile properties of Zr-containing ODS-FeCrAl alloy fabricated by laser additive manufacturing. Mater Sci Eng A, 774: 138937. https://doi.org/10.1016/j.msea.2020.138937
Wilms MB, Streubel R, Frömel F, et al., 2018, Laser additive manufacturing of oxide dispersion strengthened steels using laser-generated nanoparticle-metal composite powders. Procedia CIRP, 74: 196–200. https://doi.org/10.1016/j.procir.2018.08.093
Zöllner D, 2022, Impact of a strong temperature gradient on grain growth in films. Model Simul Mater Sci Eng, 30: 025010. https://doi.org/10.1088/1361-651X/ac44a8
Rao GA, Kumar M, Srinivas M, et al., 2003, Effect of standard heat treatment on the microstructure and mechanical properties of hot isostatically pressed superalloy Inconel 718. Mater Sci Eng A, 355: 114–125. https://doi.org/10.1016/S0921-5093(03)00079-0
Gladman T, 1999, Precipitation hardening in metals. Mater Sci Technol, 15: 30–36. https://doi.org/10.1179/026708399773002782
Sabelkin VP, Cobb GR, Doane BM, et al., 2020, Torsional behavior of additively manufactured nickel alloy 718 under monotonic loading and low cycle fatigue. Mater Today Commun, 24: 101256. https://doi.org/10.1016/j.mtcomm.2020.101256
Roper CM, Heczel A, Bhattiprolu VS, et al., 2022, Effect of laser heating on microstructure and deposition properties of cold sprayed SS304L. Materialia, 22: 101372. https://doi.org/10.1016/j.mtla.2022.101372
Amato KN, Gaytan SM, Murr LE, et al., 2012, Microstructures and mechanical behavior of Inconel 718 fabricated by selective laser melting. Acta Mater, 60: 2229–2239. https://doi.org/10.1016/j.actamat.2011.12.032
Wang Y, Shi J, Deng X, et al., 2012, Contribution of Different Strengthening effects in Particulate-reinforced Metal Matrix Nanocomposites Prepared by Additive Manufacturing. In: Proceeding Advanced Manufacturing. American Society of Mechanical Engineers. Vol. 2; 2016. p1–7. Available from: https://www.asmedigitalcollection.asme.org/IMECE/ proceedings/IMECE2016/50527phoenix,arizona, USA/265241 [Last accessed on 2017 Mar 22].
Zhang Z, Chen DL, 2006, Consideration of Orowan strengthening effect in particulate-reinforced metal matrix nanocomposites: A model for predicting their yield strength. Scr Mater, 54: 1321–1316. https://doi.org/10.1016/j.scriptamat.2005.12.017
EOS NickelAlloy IN718 Material Data Sheet; 2020.
Martienssen W, Warlimont H, 2005, Springer Handbook of Condensed Matter and Materials Data. Berlin: Springer. https://doi.org/10.1007/3-540-30437-1
Ferguson JB, Schultz BF, Venugopalan D, et al., 2014, On the superposition of strengthening mechanisms in dispersion strengthened alloys and metal-matrix nanocomposites: Considerations of stress and energy. Met Mater Int, 20: 375–388. https://doi.org//10.1007/s12540-014-2017-6
Ferguson JB, Sheykh-Jaberi F, Kim CS, et al., 2012, On the strength and strain to failure in particle-reinforced magnesium metal-matrix nanocomposites (Mg MMNCs). Mater Sci Eng A, 558: 193–204. https://doi.org/10.1016/j.msea.2012.07.111
Vogt R, Zhang Z, Li Y, et al., 2009, The absence of thermal expansion mismatch strengthening in nanostructured metal-matrix composites. Scr Mater, 61: 1052–1055. https://doi.org/10.1016/j.scriptamat.2009.08.025
Nardone VC, Prewo KM, 1986, On the strength of discontinuous silicon carbide reinforced aluminum composites. Scr Metall, 20: 43–48. https://doi.org/10.1016/0036-9748(86)90210-3
Kim CS, Sohn I, Nezafati M, et al., 2013, Prediction models for the yield strength of particle-reinforced unimodal pure magnesium (Mg) metal matrix nanocomposites (MMNCs). J Mater Sci, 48: 4191–4204. https://doi.org/10.1007/s10853-013-7232-x
Redsten AM, Klier EM, Brown AM, et al., 1995, Mechanical properties and microstructure of cast oxide-dispersion-strengthened aluminum. Mater Sci Eng A, 201: 88–102. https://doi.org/10.1016/0921-5093(94)09741-0
Chawla N, Habel U, Shen YL, et al., 2000, The effect of matrix microstructure on the tensile and fatigue behavior of SiC particle-reinforced 2080 Al matrix composites. Metall Mater Trans A, 31: 531–540. https://doi.org//10.1007/s11661-000-0288-7
Wang S, Zheng Y, Zhang G, et al., 2019, Effect of NbC addition on the microstructure, mechanical properties and thermal shock resistance of Ti(C,N)-based cermets. Mater Res Express, 6: 056557. https://doi.org/10.1088/2053-1591/ab07e9
Ceschini L, Dahle A, Gupta M, et al., 2017, Aluminum and Magnesium Metal Matrix Nanocomposites. Singapore: Springer Singapore. https://doi.org/10.1007/978-981-10-2681-2
Patil RV, Kale GB, 1996, Chemical diffusion of niobium in nickel. J Nucl Mater, 230: 57–60. https://doi.org/10.1016/0022-3115(96)80010-9
Rohrer GS, 1948, Introduction to grains, phases, and interfaces-an interpretation of microstructure. Metall Mater Trans A Phys Metall Mater Sci, 175: 15–51. https://doi.org/10.1007/s11661-010-0215-5
Cozar R, Pineau A, 1973, Morphology of γ’ and γ’’ precipitates and thermal stability of Inconel 718 type alloys. Metall Trans, 4: 47–59. https://doi.org/10.1007/BF02649604
Burke MG, Miller MK, 2012, Precipitation in Alloy 718: A Combined AEM and APFIM Investigation. Tennessee: Oak Ridge National Laboratory. p337–50.