Process optimization and mechanical property investigation of Inconel 718 manufactured by selective electron beam melting
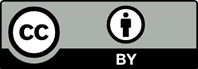
To accelerate the optimization of selective electron-beam melting (SEBM) processing parameters, two machine learning models, Gaussian process regression, and support vector regression were applied in this work to predict the relative density of Inconel 718 from experimental data. The experimental validation indicated that the trained algorithms can precisely predict the relative density of SEBM samples. Moreover, the effects of different parameters on surface integrity, internal defects, and mechanical properties are discussed in this paper. The Inconel 718 samples with high density (>99.5%) prepared by the same SEBM energy density exhibit different mechanical properties, which are related to the existence of the unmelted powder, Laves phase, and grain structure. Finally, Inconel 718 sample with superior strength and plasticity was fabricated using the optimized processing parameters.
Herzog D, Seyda V, Wycisk E, et al., 2016, Additive manufacturing of metals. Acta Materialia, 117: 371–392. https://doi.org/10.1016/j.actamat.2016.07.019
Sanchez S, Smith P, Xu Z, et al., 2021, Powder Bed Fusion of nickel–based superalloys: A review. Int J Mach Tools Manuf, 165: 103729. https://doi.org/10.1016/j.ijmachtools.2021.103729
Ang YT, Sing SL, Lim JC, 2022, Process study for directed energy deposition of 316L stainless steel with TiB2 metal matrix composites. Mater Sci Addit Manuf, 1: 13. https://doi.org/10.18063/msam.v1i2.13
Körner C, 2016, Additive manufacturing of metallic components by selective electron beam melting–a review. Int Mater Rev, 61: 361–377. https://doi.org/10.1080/09506608.2016.1176289
He M, Ni Y, Wang S, 2021, On the microstructure and tensile properties of Inconel 718 alloy fabricated by selective laser melting and conventional casting. J Micromech Mol Phys, 6: 2141003. https://doi.org/10.1142/s2424913021410034
Hashemi SM, Parvizi S, Baghbanijavid H, et al., 2021, Computational modelling of process–structure–property– performance relationships in metal additive manufacturing: A review. Int Mater Rev, 67: 1–46. https://doi.org/10.1080/09506608.2020.1868889
Sochalski–Kolbus LM, Payzant EA, Cornwell PA, et al., 2015, Comparison of residual stresses in inconel 718 simple parts made by electron beam melting and direct laser metal sintering. Metall Mater Trans A, 46: 1419–1432. https://doi.org/10.1007/s11661–014–2722–2
Leung CL, Tosi R, Muzangaza E, et al., 2019, Effect of preheating on the thermal, microstructural and mechanical properties of selective electron beam melted Ti-6Al-4V components. Mater Des 174: 107792. https://doi.org/10.1016/j.matdes.2019.107792
Liu S, Shin YC, 2019, Additive manufacturing of Ti6Al4V alloy: A review. Mater Des, 164: 107552. https://doi.org/10.1016/j.matdes.2018.107552
Hosseini E, Popovich VA, 2019, A review of mechanical properties of additively manufactured Inconel 718. Addit Manuf, 30: 100877. https://doi.org/10.1016/j.addma.2019.100877
Raab SJ, Guschlbauer R, Lodes MA, et al., 2016, Thermal and electrical conductivity of 99.9% pure copper processed via selective electron beam melting. Adv Eng Mater, 18: 1661– 1666. https://doi.org/10.1002/adem.201600078
Yang G, Yang P, Yang K, et al., 2019, Effect of processing parameters on the density, microstructure and strength of pure tungsten fabricated by selective electron beam melting. Int J Refract Metals Hard Mater, 84: 105040. https://doi.org/10.1016/j.ijrmhm.2019.105040
Bond DM, Zikry MA, 2020, Effects of electron beam manufacturing induced defects on fracture in Inconel 718. Addit Manuf, 32: 101059. https://doi.org/10.1016/j.addma.2020.101059
Cunningham R, Narra SP, Ozturk T, et al., 2016, Evaluating the effect of processing parameters on porosity in electron beam melted Ti-6Al-4V via synchrotron X-ray microtomography. J Miner Metals Mater Soc, 68: 765–771. https://doi.org/10.1007/s11837-015-1802-0
Ding X, Koizumi Y, Aoyagi K, et al., 2019, Microstructural control of alloy 718 fabricated by electron beam melting with expanded processing window by adaptive offset method. Mater Sci Eng A, 764: 138058. https://doi.org/10.1016/j.msea.2019.138058
Chandra S, Tan X, Narayan RL, et al., 2021, A generalised hot cracking criterion for nickel-based superalloys additively manufactured by electron beam melting. Addit Manuf, 37:101633. https://doi.org/10.1016/j.addma.2020.101633
Deng D, Peng RL, Söderberg H, et al., 2018, On the formation of microstructural gradients in a nickel-base superalloy during electron beam melting. Mater Des, 160: 251–261. https://doi.org/10.1016/j.matdes.2018.09.006
Deng D, Peng RL, Brodin H, et al., 2018, Microstructure and mechanical properties of Inconel 718 produced by selective laser melting: Sample orientation dependence and effects of post heat treatments. Mater Sci Eng A, 713: 294–306. https://doi.org/10.1016/j.msea.2017.12.043
Chandra S, Tan X, Narayan RL, et al., 2021, Nanometer-scale precipitations in a selective electron beam melted nickel-based superalloy. Scr Mater, 194: 113661. https://doi.org/10.1016/j.scriptamat.2020.113661
Polonsky AT, Echlin MP, Lenthe WC, et al., 2018, Defects and 3D structural inhomogeneity in electron beam additively manufactured Inconel 718. Mater Char, 143: 171–181. https://doi.org/10.1016/j.matchar.2018.02.020
Goel S, Zaninelli E, Gårdstam J, et al., 2020, Microstructure evolution-based design of thermal post-treatments for EBM-built Alloy 718. J Mater Sci, 56: 5250–5268. https://doi.org/10.1007/s10853-020-05595-2
Peng H, Shi Y, Gong S, et al., 2018, Microstructure, mechanical properties and cracking behaviour in a y’-precipitation strengthened nickel-base superalloy fabricated by electron beam melting. Mater Des, 159: 155–169. https://doi.org/10.1016/j.matdes.2018.08.054
Gong H, Rafi K, Gu H, et al., 2014, Analysis of defect generation in Ti-6Al-4V parts made using powder bed fusion additive manufacturing processes. Addit Manuf, 1–4: 87–98. https://doi.org/10.1016/j.addma.2014.08.002
Moussaoui K, Rubio W, Mousseigne M, et al., 2018, Effects of Selective Laser Melting Additive manufacturing parameters of Inconel 718 on porosity, microstructure and mechanical properties. Mater Sci Eng A, 735: 182–190. https://doi.org/10.1016/j.msea.2018.08.037
Helmer HE, Körner C, Singer RF, 2014, Additive manufacturing of nickel-based superalloy Inconel 718 by selective electron beam melting: Processing window and microstructure. J Mater Res, 29: 1987–1996. https://doi.org/10.1557/jmr.2014.192
Rankouhi B, Agrawal AK, Pfefferkorn FE, et al., 2021, A dimensionless number for predicting universal processing parameter boundaries in metal powder bed additive manufacturing. Manuf Lett, 27: 13–17. https://doi.org/10.1016/j.mfglet.2020.12.002
Yan W, Qian Y, Ge W, et al., 2018, Meso-scale modeling of multiple-layer fabrication process in Selective Electron Beam Melting: Inter-layer/track voids formation. Mater Des, 141: 210–219. https://doi.org/10.1016/j.matdes.2017.12.031
Ammer R, Markl M, Ljungblad U, et al., 2014, Simulating fast electron beam melting with a parallel thermal free surface lattice Boltzmann method. Comput Math Appl, 67: 318–330. https://doi.org/10.1016/j.camwa.2013.10.001
Adhitan RK, Raghavan N, 2017, Transient thermo-mechanical modeling of stress evolution and re-melt volume fraction in electron beam additive manufacturing process. Proc Manuf, 11: 571–583. https://doi.org/10.1016/j.promfg.2017.07.151
Liu F, Wang Z, Wang Z, et al., 2022, High-throughput method-accelerated design of Ni-based superalloys. Adv Funct Mater, 32: 2109367. https://doi.org/10.1002/adfm.202109367
Wang Z, Zhang L, Li W, et al., 2020, High throughput experiment assisted discovery of new Ni-base superalloys. Scr Mater, 178: 134–138. https://doi.org/10.1016/j.scriptamat.2019.11.019
Wen C, Zhang Y, Wang C, et al., 2019, Machine learning assisted design of high entropy alloys with desired property. Acta Mater, 170: 109–117. https://doi.org/10.1016/j.actamat.2019.03.010
Liu P, Huang H, Antonov S, et al., 2020, Machine learning assisted design of γ’-strengthened Co-base superalloys with multi-performance optimization. NPJ Comput Mater, 6: 62. https://doi.org/10.1038/s41524-020-0334-5
Liu F, Xiao X, Huang L, et al., 2022, Design of NiCoCrAl eutectic high entropy alloys by combining machine learning with CALPHAD method. Mater Today Commun, 30: 103172. https://doi.org/10.1016/j.mtcomm.2022.103172
Liu F, Wang Z, Wang Z, et al., 2020, Evaluating yield strength of Ni-based superalloys via high throughput experiment and machine learning. J Micromech Mol Phys, 5: 2050015. https://doi.org/10.1142/s2424913020500150
Gong X, Zeng D, Groeneveld-Meijer W, et al., 2022, Additive manufacturing: A machine learning model of process-structure-property linkages for machining behavior of Ti-6Al-4V. Mater Sci Addit Manuf, 1: 6. https://doi.org/10.18063/msam.v1i1.6
Liu Q, Wu H, Paul MJ, et al., 2020, Machine-learning assisted laser powder bed fusion process optimization for AlSi10Mg: New microstructure description indices and fracture mechanisms. Acta Mater, 201: 316–328. https://doi.org/10.1016/j.actamat.2020.10.010
Aoyagi K, Wang H, Sudo H, et al., 2019, Simple method to construct process maps for additive manufacturing using a support vector machine. Addit Manuf, 27: 353–362. https://doi.org/10.1016/j.addma.2019.03.013
Lei Y, Aoyagi K, Cui Y, et al., 2020, Process optimization and mechanical property investigation of non-weldable superalloy Alloy713ELC manufactured with selective electron beam melting. Mater Sci Eng A, 787: 139485. https://doi.org/10.1016/j.msea.2020.139485
Lei Y, Aoyagi K, Aota K, et al., 2021, Critical factor triggering grain boundary cracking in non-weldable superalloy Alloy713ELC fabricated with selective electron beam melting. Acta Mater, 208: 116695. https://doi.org/10.1016/j.actamat.2021.116695
Sah AK, Agilan M, Dineshraj S, et al., 2022, Machine learning-enabled prediction of density and defects in additively manufactured Inconel 718 alloy. Mater Today Commun, 30: 103193. https://doi.org/10.1016/j.mtcomm.2022.103193
Smola AJ, Schölkopf B, 2004, A tutorial on support vector regression. Stat Comput, 14: 199–222. https://doi.org/10.1023/b: stco.0000035301.49549.88
Luu DN, Zhou W, Nai SM, 2022, Mitigation of liquation cracking in selective laser melted Inconel 718 through optimization of layer thickness and laser energy density. J Mater Process Technol, 299: 117374. https://doi.org/10.1016/j.jmatprotec.2021.117374
Balbaa M, Mekhiel S, Elbestawi M, et al., 2020, On selective laser melting of Inconel 718: Densification, surface roughness, and residual stresses. Mater Design, 193: 108818. https://doi.org/10.1016/j.matdes.2020.108818
Im SY, Jun SY, Lee JW, et al., 2020, Unidirectional columnar microstructure and its effect on the enhanced creep resistance of selective electron beam melted Inconel 718. J Alloys Comp, 817: 153320. https://doi.org/10.1016/j.jallcom.2019.153320
Zhang L, Li Y, Zhang S, et al., 2021, Selective laser melting of IN738 superalloy with a low Mn+Si content: Effect of energy input on characteristics of molten pool, metallurgical defects, microstructures and mechanical properties. Mater Sci Eng A, 826: 141985. https://doi.org/10.1016/j.msea.2021.141985
Pedregosa F, Varoquaux G, Gramfort A, et al., 2011, Scikit-learn: Machine learning in python. JMLR, 12: 2825–2830.
Lee HJ, Kim HK, Hong HU, et al., 2019, Influence of the focus offset on the defects, microstructure, and mechanical properties of an Inconel 718 superalloy fabricated by electron beam additive manufacturing. J Alloys Comp, 781: 842–856. https://doi.org/10.1016/j.jallcom.2018.12.070
Zhao Y, Aoyagi K, Daino Y, et al., 2020, Significance of powder feedstock characteristics in defect suppression of additively manufactured Inconel 718. Addit Manuf, 34: 101277. https://doi.org/10.1016/j.addma.2020.101277
Chauvet E, Kontis P, Jägle EA, et al., 2018, Hot cracking mechanism affecting a non-weldable Ni-based superalloy produced by selective electron Beam Melting. Acta Mater, 142: 82–94. https://doi.org/10.1016/j.actamat.2017.09.047
Sun SH, Koizumi Y, Saito T, et al., 2018, Electron beam additive manufacturing of Inconel 718 alloy rods: Impact of build direction on microstructure and high-temperature tensile properties. Addit Manuf, 23: 457–470. https://doi.org/10.1016/j.addma.2018.08.017
Gui Y, Aoyagi K, Bian H, et al., 2022, Detection, classification and prediction of internal defects from surface morphology data of metal parts fabricated by powder bed fusion type additive manufacturing using an electron beam. Addit Manuf, 54: 102736. https://doi.org/10.1016/j.addma.2022.102736
Bauereiß A, Scharowsky T, Körner C, 2014, Defect generation and propagation mechanism during additive manufacturing by selective beam melting. J Mater Process Technol, 214: 2522–2528. https://doi.org/10.1016/j.jmatprotec.2014.05.002
Strondl A, Palm M, Gnauk J, et al., 2011, Microstructure and mechanical properties of nickel based superalloy IN718 produced by rapid prototyping with electron beam melting (EBM). Mater Sci Technol, 27: 876–883. https://doi.org/10.1179/026708309x12468927349451
Deng D, Moverare J, Peng RL, et al., 2017, Microstructure and anisotropic mechanical properties of EBM manufactured Inconel 718 and effects of post heat treatments. Mater Sci Eng A, 693: 151–163. https://doi.org/10.1016/j.msea.2017.03.085
Kirka MM, Medina F, Dehoff R, et al., 2017, Mechanical behavior of post-processed Inconel 718 manufactured through the electron beam melting process. Mater Sci Eng A, 680: 338–346. https://doi.org/10.1016/j.msea.2016.10.069
Goel S, Zaninelli E, Gundgire T, et al., 2021, Microstructure evolution and mechanical response–based shortening of thermal post-treatment for electron beam melting (EBM) produced Alloy 718. Mater Sci Eng A, 820: 141515. https://doi.org/10.1016/j.msea.2021.141515