Experimental and numerical studies on the acoustic performance of simple cubic structure lattices fabricated by digital light processing
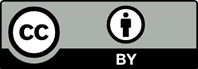
Sound absorption is one of the important properties of porous materials such as foams and lattices. Many mathematical models in the literature are capable of modeling the acoustic properties of lattices. However, appropriate models need to be chosen for specific lattice structures on a case-by-case basis and require significant experience in acoustic modeling. This work aims to provide simplified insights into different mathematical models for the simple cubic lattice. The strut lengths and radii of the unit cells were varied, and the sound absorption properties were measured using an impedance tube. The sound absorption coefficients of the lattices generally increased and exhibited more resonant-like behavior as the strut radius increased. The Delany-Bazley (DB) model and the multi-layered micropore-cavity (MMC) model were used to simulate the acoustic properties of the lattices. The correction factors in the MMC were calculated based on empirical relations fitted using experimental data of the design geometry parameters. Results show that the DB model was able to model the sound absorption coefficients for lattice samples with porosities as low as 0.7, while the MMC with resonator theory is a more appropriate acoustics approach for lattices with porosities lower than 0.7. This work will be highly useful for materials researchers who are studying the acoustic properties of novel porous materials, as well as manufacturers of acoustic materials interested in the additive manufacturing of lattice structures for sound absorption and insulation applications.
Cao L, Fu Q, Si Y, et al., 2018, Porous materials for sound absorption. Composites Commun, 10: 25–35 https://doi.org/10.1016/j.coco.2018.05.001
Jia C, Li L, Liu Y, et al., 2020, Highly compressible and anisotropic lamellar ceramic sponges with superior thermal insulation and acoustic absorption performances. Nat Commun, 11: 3732. https://doi.org/10.1038/s41467-020-17533-6
Yu X, Lu Z, Zhai W, 2021, Enhancing the flow resistance and sound absorption of open-cell metallic foams by creating partially-open windows. Acta Mater, 206: 116666. https://doi.org/10.1016/j.actamat.2021.116666
Yang W, An J, Chua CK, et al., 2020, Acoustic absorptions of multifunctional polymeric cellular structures based on triply periodic minimal surfaces fabricated by stereolithography. Virtual Phys Prototyp, 15: 242–249. https://doi.org/10.1080/17452759.2020.1740747
Zieliński TG, Opiela KC, Pawłowski P, et al., 2020, Reproducibility of sound-absorbing periodic porous materials using additive manufacturing technologies: Round robin study. Additive Manuf, 36: 101564. https://doi.org/10.1016/j.addma.2020.101564
Cheng Y, Xu Z, Chen S, et al., 2021, The influence of closed pore ratio on sound absorption of plant-based polyurethane foam using control unit model. Appl Acoust, 180: 108083. https://doi.org/10.1016/j.apacoust.2021.108083
Doutres O, Atalla N, Dong K, 2011, Effect of the microstructure closed pore content on the acoustic behavior of polyurethane foams. J Appl Phys, 110: 064901. https://doi.org/10.1063/1.3631021
Delany ME, Bazley EN, 1970, Acoustical properties of fibrous absorbent materials. Appl Acoust, 3: 105–116. https://doi.org/10.1016/0003-682X(70)90031-9
Kino N, 2015, Further investigations of empirical improvements to the Johnson-Champoux-Allard model. Appl Acoust, 96: 153–170. https://doi.org/10.1016/j.apacoust.2015.03.024
Biot MA, 1956, Theory of propagation of elastic waves in a fluid‐saturated porous solid. II. Higher frequency range. J Acoust Soc Am, 28: 179–191. https://doi.org/10.1121/1.1908241
Dib L, Bouhedja S, Amrani H, 2015, Mechanical parameters effects on acoustic absorption at polymer foam. Adv Mater Sci Eng, 2015: 1–10. https://doi.org/10.1155/2015/896035
Allard JF, Atalla N, 2009, Propagation of Sound in Porous media: Modelling Sound Absorbing Materials. 2nd ed. Wiley, Hoboken, N.J. p358.
Verdiere K, Panneton R, Elkoun S, et al., Transfer matrix method applied to the parallel assembly of sound absorbing materials. J Acoust Soc Am, 134: 4648. https://doi.org/10.1121/1.4824839
Niskanen M, Groby JP, Duclos A, et al., 2017, Deterministic and statistical characterization of rigid frame porous materials from impedance tube measurements. J Acoust Soc Am, 142: 2407. https://doi.org/10.1121/1.5008742
Boulvert J, Cavalieri T, Costa-Baptista J, et al., Optimally graded porous material for broadband perfect absorption of sound. J Appl Phys, 126: 175101. https://doi.org/10.1063/1.5119715
Chen S, Lei S, Zhu J, et al., 2021, The influence of microstructure on sound absorption of polyurethane foams through numerical simulation. Macromol Theory Simul, 30: 2000075. https://doi.org/10.1002/mats.202000075
Zhai W, Yub X, Song X, et al., 2018, Microstructure-based experimental and numerical investigations on the sound absorption property of open-cell metallic foams manufactured by a template replication technique. Mater Design, 137: 108–116. https://doi.org/10.1016/j.matdes.2017.10.016
Chua JW, Li X, Li T, et al., 2022, Customisable sound absorption properties of functionally graded metallic foams. J Mater Sci Technol, 108: 196–207. https://doi.org/10.1016/j.jmst.2021.07.056
Gai XL, Xing T, Li XY, et al., 2016, Sound absorption of microperforated panel mounted with helmholtz resonators. Appl Acoust, 114: 260–265. https://doi.org/10.1016/j.apacoust.2016.08.001
Komkin AI, Mironov MA, Bykov AI, 2017, Sound absorption by a Helmholtz resonator. Acoust Phys, 63: 385–392. https://doi.org/10.1134/s1063771017030071
Maa DY, 1998, Potential of microperforated panel absorber. J Acoust Soc Am, 104: 2861–2866. https://doi.org/10.1121/1.423870
Morse PM, Ingard KU, 1968, Theoretical Acoustics (International Series in Pure and Applied Physics). McGraw- Hill, New York.
Li X, Yu X, Chua JW, et al., 2021, Microlattice metamaterials with simultaneous superior acoustic and mechanical energy absorption. Small, 17: e2100336. https://doi.org/10.1002/smll.202100336
Doutres O, Atalla N, Osman H, 2015, Transfer matrix modeling and experimental validation of cellular porous material with resonant inclusions. J Acoust Soc Am, 137: 3502–3513. https://doi.org/10.1121/1.4921027
Jiménez N, Umnova O, Groby JP, 2021, Acoustic Waves in Periodic Structures, Metamaterials, and Porous Media (Topics in Applied Physics). Springer, Germany.
Fourie JG, Du Plessis JP, 2002, Pressure drop modelling in cellular metallic foams. Chem Eng Sci, 57: 2781–2789. https://doi.org/10.1016/s0009-2509(02)00166-5
Verdière K, Panneton R, Elkoun S, et al., 2013, Transfer matrix method applied to the parallel assembly of sound absorbing materials. J Acoust Soc Am, 134: 4648–4658. https://doi.org/10.1121/1.4824839
Ashby M, Evans T, Fleck NA, 2000, Metal Foams: A Design Guide. Elsevier, Burlington.
Okuzono T, Nitta T, Sakagami K, 2019, Note on microperforated panel model using equivalent-fluid-based absorption elements. Acoust Sci Technol, 40: 221–224. https://doi.org/10.1250/ast.40.221
Li X, Yu X, Zhai W, 2021, Additively manufactured deformation-recoverable and broadband sound-absorbing microlattice inspired by the concept of traditional perforated panels. Adv Mater, 33: e2104552. https://doi.org/10.1002/adma.202104552
Li X, Yu X, Zhai W, 2022, Less is more: Hollow-truss microlattice metamaterials with dual sound dissipation mechanisms and enhanced broadband sound absorption. Small, 18: e2204145. https://doi.org/10.1002/smll.202204145
Rahimabady M, Statharas EC, Yao K, et al., Hybrid local piezoelectric and conductive functions for high performance airborne sound absorption. Appl Phys Lett, 111: 241601. https://doi.org/10.1063/1.5010743
Egab L, Wang X, Fard M, 2014, Acoustical characterisation of porous sound absorbing materials: A review. Int J Veh Noise Vib 10: 129–149. https://doi.org/10.1504/IJVNV.2014.059634
Institution BS, 1993, Acoustics. Materials for Acoustical Applications. Determination of Airflow Resistance. British Standards Institution, United Kingdom.
Khosravani MR, Reinicke T, 2021, Experimental characterization of 3D-printed sound absorber. Eur J Mech A Solids, 89: 104304. https://doi.org/10.1016/j.euromechsol.2021.104304