Layer porosity in powder-bed fusion prediction using regression machine learning models and time-series features
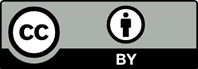
Additive manufacturing (AM) using laser powder-bed fusion (L-PBF) has become a common industrial process for high-end component production. The uptake of the process has been accelerated through the broad acceptance of the L-PBF process toward achieving high-quality parts with complex geometry. However, the L-PBF process faces challenges from the process’s sensitivity to the process build parameters, which, when incorrectly set, can cause defects such as porosity, which in turn have a detrimental effect on the produced part properties. On the other hand, the AM processing equipment generates a vast amount of data captured through in situ sensors such as pyrometers and imaging cameras. Having such an abundance of process data facilitates the employment of advanced machine learning (ML) tools to understand and extract patterns and information about the underlying AM process and gain “predictive control.” Driven by this idea, we aimed to employ ML tools over pyrometer time-series data from an L-PBF process to predict the porosity percentage of layers of an AM-built part. Sensor data are naturally modeled by time series; however, most ML algorithms work with tabular data (i.e., one single vector describes a feature). In the work presented here, feature engineering tools were used to transform the time-series data into informative features. These features were fed into the tabular ML algorithms for evaluation, broadening the selection of ML algorithms available in the literature. It was hypothesized that the time-series summary features would capture the interaction of melt-pool temperature with resulting porosity, from which the resulting models could better predict porosity occurrence. The dataset contains layer porosity values in the range of 0.00175 – 7.160%, to which we divide the data into “low” and “high” porous layers using a splitting threshold value of 1%. From evaluating these algorithms, it was concluded that classifying “low” versus “high” porosity layers is relatively easier than predicting the layer’s porosity percentage.

- Mahato V, Obeidi MA, Brabazon D, Cunningham P. Detecting voids in 3D printing using melt pool time series data. J Intell Manuf. 2022;33:842-852. doi: 10.1007/s10845-020-01694-8
- Herzog T, Brandt M, Trinchi A, Sola A, Molotnikov A. Process monitoring and machine learning for defect detection in laser-based metal additive manufacturing. J Intell Manuf. 2024;35(4):1407-1437. doi: 10.1007/s10845-023-02119-y
- Gradl P, Tinker DC, Park A, et al. Robust metal additive manufacturing process selection and development for aerospace components. J Mater Eng Perform. 2022;31(8):6013-6044. doi: 10.1007/s11665-022-06850-0
- Mahale RS, Shamanth V, Hemanth K, et al. Processes and applications of metal additive manufacturing. Mater Today Proc. 2022;54:228-233. doi: 10.1016/j.matpr.2021.08.298
- Hehr A, Norfolk M, Kominsky D, Boulanger A, Davis M, Boulware P. Smart build-plate for metal additive manufacturing processes. Sensors (Basel). 2020;20(2):360. doi: 10.3390/s20020360
- Huang WB, Zhang LW, Li WL, et al. Various types and applications of additive manufacturing. DEStech Trans Comput Sci Eng. 2019:377-381. doi: 10.12783/dtcse/ammso2019/30160
- Papy K, Jean-Marc S, Alexey S, Andras B. Additive manufacturing feasibility of WC-17Co cermet parts by laser powder bed fusion. Procedia CIRP. 2022;111:153-157. doi: 10.1016/j.procir.2022.08.049
- Dejene ND, Lemu HG. Current status and challenges of powder bed fusion-based metal additive manufacturing: Literature review. Metals. 2023;13(2):424. doi: 10.3390/met13020424
- Hussain SZ, Kausar Z, Koreshi ZU, Shah MF, Abdullah A, Farooq MU. Linear active disturbance rejection control for a laser powder bed fusion additive manufacturing process. Electronics. 2023;12(2):471. doi: 10.3390/electronics12020471
- Pan T, Li L, Zhang X, et al. Investigation of significant factors on deformation with powder bed fusion system. Proc Inst Mech Eng B J Eng Manuf. 2021;235(5):902-911. doi: 10.1177/0954405420970088
- Ford S, Despeisse M. Additive manufacturing and sustainability: An exploratory study of the advantages and challenges. J Clean Prod. 2016;137:1573-1587. doi: 10.1016/j.jclepro.2016.04.150
- Gradl PR, Tinker DC, Ivester J, Skinner SW, Teasley T, Bili JL. Geometric feature reproducibility for laser powder bed fusion (L-PBF) additive manufacturing with Inconel 718. Addit Manuf. 2021;47:102305. doi: 10.1016/j.addma.2021.102305
- Kayacan MY, Özsoy K, Duman B, Yilmaz N, Kayacan MC. A study on elimination of failures resulting from layering and internal stresses in Powder Bed Fusion (PBF) additive manufacturing. Mater Manuf Processes. 2019;34(13):1467-1475. doi: 10.1080/10426914.2019.1655151
- Zieliński TG, Opiela KC, Pawłowski P, et al. Reproducibility of sound-absorbing periodic porous materials using additive manufacturing technologies: Round robin study. Addit Manuf. 2020;36:101564. doi: 10.1016/j.addma.2020.101564
- Faragasso A, Bonsignorio F. Reproducibility challenges in robotic surgery. Front Robot AI. 2023;10:1127972. doi: 10.3389/frobt.2023.1127972
- Li X, Zhang M, Zhou M, et al. Qualify assessment for extrusion-based additive manufacturing with 3D scan and machine learning. J Manuf Processes. 2023;90:274-285. doi: 10.1016/j.jmapro.2023.01.025
- Gu Z, Mani Krishna KV, Parsazadeh M, et al. Deep learning-based melt pool and porosity detection in components fabricated by laser powder bed fusion. Prog Addit Manuf. 2024:1-18. doi: 10.1007/s40964-024-00603-2
- Atwya M, Panoutsos G. In-situ porosity prediction in metal powder bed fusion additive manufacturing using spectral emissions: A prior-guided machine learning approach. J Intell Manuf. 2024;35(6):2719-2742. doi: 10.1007/s10845-023-02170-9
- Satterlee N, Torresani E, Olevsky E, Kang JS. Comparison of machine learning methods for automatic classification of porosities in powder-based additive manufactured metal parts. Int J Adv Manuf Technol. 2022;120(9):6761-6776. doi: 10.1007/s00170-022-09141-z
- Wang W, Ning J, Liang SY. Analytical prediction of keyhole porosity in laser powder bed fusion. Int J Adv Manuf Technol. 2022;119(11):6995-7002. doi: 10.1007/s00170-021-08276-9
- Liu R, Liu S, Zhang X. A physics-informed machine learning model for porosity analysis in laser powder bed fusion additive manufacturing. Int J Adv Manuf Technol. 2021;113(7):1943-1958. doi: 10.1007/s00170-021-06640-3
- Ero O, Taherkhani K, Hemmati Y, Toyserkani E. An integrated fuzzy logic and machine learning platform for porosity detection using optical tomography imaging during laser powder bed fusion. Int J Extrem Manuf. 2024;6(6):065601. doi: 10.1088/2631-7990/ad65cd
- Mohammed AS, Almutahhar M, Sattar K, Alhajeri A, Nazir A, Ali U. Deep learning based porosity prediction for additively manufactured laser powder-bed fusion parts. J Mater Res Technol. 2023;27:7330-7335. doi: 10.1016/j.jmrt.2023.11.130
- Estalaki SM, Lough CS, Landers RG, Kinzel EC, Luo T. Predicting defects in laser powder bed fusion using in-situ thermal imaging data and machine learning. Addit Manuf. 2022;58:103008. doi: 10.1016/j.addma.2022.103008
- Gordon JV, Narra SP, Cunningham RW, et al. Defect structure process maps for laser powder bed fusion additive manufacturing. Addit Manuf. 2020;36:101552. doi: 10.1016/j.addma.2020.101552
- Du Plessis A. Effects of process parameters on porosity in laser powder bed fusion revealed by X-ray tomography. Addit Manuf. 2019;30:100871. doi: 10.1016/j.addma.2019.100871
- Kan WH, Nadot Y, Foley M, Ridosz L, Proust G, Cairney JM. Factors that affect the properties of additively-manufactured AlSi10Mg: Porosity versus microstructure. Addit Manuf. 2019;29:100805. doi: 10.1016/j.addma.2019.100805
- Hojjatzadeh SMH, Parab ND, Guo Q, et al. Direct observation of pore formation mechanisms during LPBF additive manufacturing process and high energy density laser welding. Int J Mach Tools Manuf. 2020;153:103555. doi: 10.1016/j.ijmachtools.2020.103555
- Vastola G, Pei QX, Zhang YW. Predictive model for porosity in powder-bed fusion additive manufacturing at high beam energy regime. Addit Manuf. 2018;22:817-822. doi: 10.1016/j.addma.2018.05.042
- Sun S, Brandt M, Easton MJL. Powder bed fusion processes: An overview. Laser Additive Manufacturing. Sawston, UK: Woodhead Publishing; 2017. p. 55-77.
- Mahato V, Obeidi MA, Brabazon D, Cunningham P. An evaluation of classification methods for 3d printing time-series data. IFAC-PapersOnLine. 2020;53(2):8211-8216. doi: 10.1016/j.ifacol.2020.12.1992
- Grasso M, Colosimo BM. Process defects and in situ monitoring methods in metal powder bed fusion: A review. Meas Sci Technol. 2017;28(4):044005. doi: 10.1088/1361-6501/aa5c4f
- Li Y, Gu D. Thermal behavior during selective laser melting of commercially pure titanium powder: Numerical simulation and experimental study. Addit Manuf. 2014;1:99-109. doi: 10.1016/j.addma.2014.09.001
- Yadav P, Rigo O, Arvieu C, Le Guen E, Lacoste E. In situ monitoring systems of the SLM process: On the need to develop machine learning models for data processing. Crystals. 2020;10(6):524. doi: 10.3390/cryst10060524
- Chawla NV, Bowyer KW, Hall LO, Kegelmeyer WP. SMOTE: Synthetic minority over-sampling technique. J Artif Intell Res. 2002;16:321-357. doi: 10.1613/jair.953
- Wilson DL. Asymptotic properties of nearest neighbor rules using edited data. IEEE Trans Syst Man Cybern. 1972;2(3):408-421. doi: 10.1109/TSMC.1972.4309137
- Torgo L, Ribeiro RP, Pfahringer B, Branco P. Smote for regression. In: Portuguese Conference on Artificial Intelligence. Berlin, Heidelberg: Springer Berlin Heidelberg; 2013. p. 378-389.
- Christ M, Braun N, Neuffer J, Kempa-Liehr AW. Time series feature extraction on basis of scalable hypothesis tests (tsfresh-a python package). Neurocomputing. 2018;307:72-77. doi: 10.1016/j.neucom.2018.03.067
- Peng CYJ, Lee KL, Ingersoll GM. An introduction to logistic regression analysis and reporting. J Educ Res. 2002;96(1):3-14. doi: 10.1080/00220670209598786
- Mahato V, Cunningham P. A Case-study on the Impact of Dynamic Time Warping in Time Series Regression. In: 3rd ECML/PKDD Workshop on Advanced Analytics and Learning on Temporal Data. 2018. doi: 10.48550/arXiv.2010.05270
- Mahato V, Obeidi MA, Brabazon D, Cunningham P. An evaluation of classification methods for 3d printing time-series data. IFAC-PapersOnLine. 2020;53(2):8211-8216. doi: 10.1016/j.ifacol.2020.12.1992
- Badiane M, Cunningham P. An empirical evaluation of kernels for time series. Artif Intell Rev. 2022;55(3):1803-1820. doi: 10.1007/s10462-021-10050-y
- Safavian SR, Landgrebe D. A survey of decision tree classifier methodology. IEEE Trans Syst Man Cybern. 1991;21(3): 660-674. doi: 10.1109/21.97458
- Breiman L. Random forests. Mach Learn. 2001;45:5-32. doi: 10.1023/A:1010950718922
- Biau G, Scornet E. A random forest guided tour. Test. 2016;25:197-227. doi: 10.1007/s11749-016-0481-7
- Geurts P, Ernst D, Wehenkel L. Extremely randomized trees. Mach Learn. 2006;63:3-42. doi: 10.1007/s10994-006-6226-1
- Freund Y, Schapire RE. A decision-theoretic generalization of on-line learning and an application to boosting. J Comput Syst Sci. 1997;55(1):119-139. doi: 10.1007/3-540-59119-2_166
- Wang L, Sugiyama M, Yang C, Zhou ZH, Feng J. On the Margin Explanation of Boosting Algorithms. In: 21st Annual Conference on Learning Theory - COLT 2008. Helsinki, Finland; 2008. p. 479-490.
- Friedman JH. Greedy function approximation: A gradient boosting machine. Ann Stat. 2001;1:1189-1232. doi: 10.1214/aos/1013203451
- Chen T, Guestrin C. Xgboost: A Scalable Tree Boosting System. In: Proceedings of the 22nd Acm Sigkdd International Conference on Knowledge Discovery and Data Mining. 2016. p. 785-794. doi: 10.1145/2939672.2939785
- Ogunleye A, Wang QG. XGBoost model for chronic kidney disease diagnosis. IEEE/ACM Trans Comput Biol Bioinform. 2019;17(6):2131-2140. doi: 10.1109/TCBB.2019.2911071
- Gumus M, Kiran MS. Crude Oil Price Forecasting Using XGBoost. In: 2017 International Conference on Computer Science and Engineering (UBMK). IEEE; 2017. p. 1100-1103.
- Deng J, Xu Y, Zuo Z, Hou Z, Chen S. Bead geometry prediction for multi-layer and multi-bead wire and arc additive manufacturing based. In: Transactions on Intelligent Welding Manufacturing. Vol. 2. Singapore: Springer; 2019. p. 125-135.
- Monu MC, Ekoi EJ, Hughes C, Kumar S, Brabazon D. Resultant physical properties of as-built nitinol processed at specific volumetric energy densities and correlation with in-situ melt pool temperatures. J Mater Res Technol. 2022;21:2757-2777. doi: 10.1016/j.jmrt.2022.10.073
- McCann R, Obeidi MA, Hughes C, et al. In-situ sensing, process monitoring and machine control in laser powder bed fusion: A review. Addit Manuf. 2021;45:102058. doi: 10.1016/j.addma.2021.102058
- Blum AL, Langley P. Selection of relevant features and examples in machine learning. Artif Intell. 1997;97(1-2):245-271. doi: 10.1016/S0004-3702(97)00063-5
- Ho S, Zhang W, Young W, et al. DLAM: Deep learning based real-time porosity prediction for additive manufacturing using thermal images of the melt pool. IEEE Access. 2021;9:115100-115114. doi: 10.1109/ACCESS.2021.3105362
- Dilip JJS, Zhang S, Teng C, et al. Influence of processing parameters on the evolution of melt pool, porosity, and microstructures in Ti-6Al-4V alloy parts fabricated by selective laser melting. Prog Addit Manuf. 2017;2:157-167. doi: 10.1007/s40964-017-0030-2