Investigation of reversibility and bi-stability of 3D-printed compliant structures with double curved beams
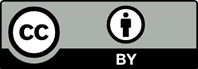
Compliant mechanisms have been widely found in nature. Instead of using rigid joints in conventional mechanisms, compliant mechanisms transfer motions through their flexible members. This work employs the buckling of double curved beam element to design compliant structures. Three groups of structures were proposed to investigate the influence of three different design parameters on their compliant behaviors under quasi-static compression: h’ (the ratio of beam apex height to beam thickness), l’ (the ratio of beam span length to thickness), and g’ (the ratio of membrane length to thickness). The proposed structures were fabricated by fused filament fabrication with a composite material. Experimental data, numerical simulations, and analytical results were compared and evaluated. It was demonstrated that the positive structural stiffness and peak force were correlated to the design parameter l’. The higher h’ value resulted in a more pronounced negative stiffness phase. In addition, the larger g’ could provide the beams with more constraint of buckling Mode 2 by transferring the rotational motion of either beam center to the axial motion of the other beam more effectively. The discrepancies between theoretical predictions and experimental results demonstrate the importance of fixed-end boundary conditions in achieving bi-stability. The transitions from reversibility to bi-stability by varying different design parameters provide insight into the design of compliant mechanisms. Herein, two approaches are evident to be effective in increasing the bi-stability of the curved beams with manufacturing defects and under undesired boundary conditions: (i) designing with a higher ‘g’’ value and (ii) increasing the number of coupling beams.
- Hesselbach J, Raatz A. Pseudoelastic Flexure Hinges in Robots for Microassembly. United States: SPIE; 2000. p. 157-167.
- Howell LL, Magleby SP, Olsen BM. Handbook of Compliant Mechanisms. United States: John Wiley & Sons; 2013.
- Chen Q, Zhang X, Zhu B. Design of buckling-induced mechanical metamaterials for energy absorption using topology optimization. Struct Multidiscipl Optimiz. 2018;58(4):1395-1410. doi: 10.1007/s00158-018-1970-y
- Wu C, Peng C, Le TC, Das R, Tran P. Tunable 3D printed composite metamaterials with negative stiffness. Smart Mater Struct. 2023;32(12):125010. doi: 10.1088/1361-665X/ad06df
- Yang H, Ma L. Multi-stable mechanical metamaterials with shape-reconfiguration and zero Poisson’s ratio. Mater Des. 2018;152:181-190. doi: 10.1016/j.matdes.2018.04.064
- Lehto M, Bodén R. A Multi-Stable Miniature Paraffin Actuator. In: Proceedin Actuator 11th International Conference on New Actuators; 2008. p. 864-867.
- Bertoldi K, Vitelli V, Christensen J, van Hecke M. Flexible mechanical metamaterials. Nat Rev Mater. 2017;2(11):1-11. doi: 10.1038/natrevmats.2017.66
- Correa DM, Klatt T, Cortes S, Haberman M, Kovar D, Seepersad C. Negative stiffness honeycombs for recoverable shock isolation. Rapid Prototyp J. 2015;21(2):193-200. doi: 10.1108/rpj-12-2014-0182
- Peng C, Marzocca P, Tran P. Triply periodic minimal surfaces based honeycomb structures with tuneable mechanical responses. Virtual Phys Prototyp. 2022;18(1):e2125879. doi: 10.1080/17452759.2022.2125879
- Peng C, Tran P, Rutz E. Accelerating hybrid lattice structures design with machine learning. Mater Sci Addit Manuf. 2024;3(2):3430. doi: 10.36922/msam.3430
- Correa DM, Seepersad CC, Haberman MR. Mechanical design of negative stiffness honeycomb materials. Integr Mater Manuf Innov. 2015;4(1):165-175. doi: 10.1186/s40192-015-0038-8
- Debeau D, Seepersad C. Additively Manufactured Conformal Negative Stiffness Honeycombs. United States: University of Texas at Austin; 2017.
- Chen S, Wang B, Zhu S, et al. A novel composite negative stiffness structure for recoverable trapping energy. Compos Part A Appl Sci Manuf. 2020;129:105697. doi: 10.1016/j.compositesa.2019.105697
- Restrepo D, Mankame ND, Zavattieri PD. Phase transforming cellular materials. Extreme Mech Lett. 2015;4:52-60. doi: 10.1016/j.eml.2015.08.001
- Rafsanjani A, Akbarzadeh A, Pasini D. Snapping mechanical metamaterials under tension. Adv Mater. 2015; 27(39):5931-5935. doi: 10.1002/adma.201502809
- Shan S, Kang SH, Raney JR, et al. Multistable architected materials for trapping elastic strain energy. Adv Mater. 2015;27(29):4296-4301. doi: 10.1002/adma.201501708
- Haghpanah B, Salari-Sharif L, Pourrajab P, Hopkins J, Valdevit L. Multistable shape-reconfigurable architected materials. Adv Mater. 2016;28(36):7915-7920. doi: 10.1002/adma.201601650
- Diaconu CG, Weaver PM, Mattioni F. Concepts for morphing airfoil sections using bi-stable laminated composite structures. Thin-Walled Struct. 2008;46(6):689-701. doi: 10.1016/j.tws.2007.11.002
- Hu N, Burgueño R. Buckling-induced smart applications: Recent advances and trends. Smart Mater Struct. 2015;24(6):063001. doi: 10.1088/0964-1726/24/6/063001
- Pontecorvo ME, Barbarino S, Murray GJ, Gandhi FS. Bistable arches for morphing applications. J Intell Mater Syst Struct. 2012;24(3):274-286. doi: 10.1177/1045389x12457252
- Cao Y, Derakhshani M, Fang Y, Huang G, Cao C. Bistable structures for advanced functional systems. Adv Funct Mater. 2021;31(45):2106231. doi: 10.1002/adfm.202106231
- Peng C, Tran P, Lalor S, Tirosh O, Rutz E. Tuning the mechanical responses of 3D-printed ankle-foot orthoses: A numerical study. Int J Bioprinting. 2024;10(3):3390. doi: 10.36922/ijb.3390
- Vangbo M. An analytical analysis of a compressed bistable buckled beam. Sensors Actuat A Phys. 1998;69(3):212-216. doi: 10.1016/s0924-4247(98)00097-1
- Qiu J, Lang JH, Slocum AH. A curved-beam bistable mechanism. J Microelectromechanical Syst. 2004;13(2):137-146. doi: 10.1109/jmems.2004.825308
- Mehreganian N, Fallah AS, Sareh P. Structural mechanics of negative stiffness honeycomb metamaterials. J Appl Mechan. 2021;88(5):1-18. doi: 10.1115/1.4049954
- Cazottes P, Fernandes A, Pouget J, Hafez M. Bistable buckled beam: Modeling of actuating force and experimental validations. J Mechan Des. 2009;131(10):10100. doi: 10.1115/1.3179003
- Cleary J, Su HJ. Modeling and experimental validation of actuating a bistable buckled beam via moment input. J Appl Mechan. 2015;82(5):051005. doi: 10.1115/1.4030074
- Yan W, Yu Y, Mehta A. Analytical modeling for rapid design of bistable buckled beams. Theor Appl Mechan Lett. 2019;9(4):264-272. doi: 10.1016/j.taml.2019.04.006
- Beharic J, Lucas TM, Harnett CK. Analysis of a compressed bistable buckled beam on a flexible support. J Appl Mechan. 2014;81(8):081011. doi: 10.1115/1.4027463
- Tissot-Daguette L, Schneegans H, Thalmann E, Henein S. Analytical modeling and experimental validation of rotationally actuated pinned–pinned and fixed-pinned buckled beam bistable mechanisms. Mechan Machine Theory. 2022;174:104874. doi: 10.1016/j.mechmachtheory.2022.104874
- Gan J, Li F, Li K, Li E, Li B. Dynamic failure of 3D printed negative-stiffness meta-sandwich structures under repeated impact loadings. Composites Sci Technol. 2023;234:109928. doi: 10.1016/j.compscitech.2023.109928
- Hussein H, Le Moal P, Bourbon G, Haddab Y, Lutz P. Modeling and stress analysis of a pre-shaped curved beam: Influence of high modes of buckling. Int J Appl Mechan. 2015;07(04):1550055. doi: 10.1142/s1758825115500556
- Hussein H, Le Moal P, Younes R, Bourbon G, Haddab Y, Lutz P. On the design of a preshaped curved beam bistable mechanism. Mechan Machine Theory. 2019;131:204-217. doi: 10.1016/j.mechmachtheory.2018.09.024
- Liu F, Jiang X, Wang X, Wang L. Machine learning-based design and optimization of curved beams for multistable structures and metamaterials. Extreme Mechan Lett. 2020;41:101002. doi: 10.1016/j.eml.2020.101002
- Timoshenko SP, Gere JM. Theory of Elastic Stability. United States: Courier Corporation; 2009.
- Yang H, Ma L. Multi-stable mechanical metamaterials by elastic buckling instability. J Mater Sci. 2018;54(4):3509-3526. doi: 10.1007/s10853-018-3065-y
- Peng C, Tran P, Mouritz AP. Compression and buckling analysis of 3D printed carbon fibre-reinforced polymer cellular composite structures. Compos Struct. 2022;300:116167. doi: 10.1016/j.compstruct.2022.116167
- Markforged. Micro Carbon Fiber Filled Nylon that Forms the Foundation of Markforged Composite Parts; 2023. Available from: https://markforged.com/materials/plastics/onyx [Last accessed on 2024 Sep 26].
- Imbalzano G, Tran P, Ngo TD, Lee PVS. A numerical study of auxetic composite panels under blast loadings. Compos Struct. 2016;135:339-352. doi: 10.1016/j.compstruct.2015.09.038
- Peng C, Tran P, Nguyen-Xuan H, Ferreira AJM. Mechanical performance and fatigue life prediction of lattice structures: Parametric computational approach. Compos Struct. 2020;235:111821. doi: 10.1016/j.compstruct.2019.111821
- Wu C, Nguyen-Van V, Tran P. Energy absorption and recoverability of Moore space-filling thin-walled structures. Mater Sci Addit Manuf. 2023;2(1):53. doi: 10.36922/msam.53