Design criteria and energy absorption prediction empirical rule for deformation-induced densification of gradient porous materials
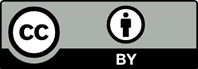
Additive manufacturing is an excellent process for complex shapes, porous structures, and bionic structures. Recently, Ti-6Al-4V alloy has been used to fabricate these porous structures and perform well in terms of mechanical properties. In addition, compared with single porosity materials, functionally graded cellular materials have attracted increasing attention due to their good mechanical properties. Compared with single porosity materials, deformation causes the gradient porous materials to be densified layer by layer, leading to better specific energy absorption. However, not all of the gradient porosity materials present the deformation-induced densification phenomenon. Hence, the design criteria for deformation-induced densification of gradient porosity materials must be explored for further application. To explore the design criteria for deformation-induced densification and establish an empirical rule for estimating energy absorption, two types of porous/bionic structures, Schon-Gyroid sheet and Schwarz-Diamond sheet, were investigated in this study. The tendency of the deformation-induced densification phenomenon was evaluated using porous materials with two layers (two porosity changes), and the empirical rule for estimating energy absorption was developed with porous materials with three layers (three porosity changes). As a result, the energy absorption of gradient porosity materials can be estimated through the mechanical properties of single porosity materials with the same porous structure. The energy absorption of the gradient porosity materials with different designs can be predicted by the empirical rule, and the difference between calculated and experimental energy absorption is only 1 – 2%. In the empirical rule, the porosity, aspect ratio, and yield stress are designed as changeable values. Other factors, such as material’s nature, surface issues, and unit cell design, can be corrected by C value. Furthermore, the deformation-induced densification can be applied by following two design criteria: (1) the aspect ratio of the layers should be <1; and (2) the yield stress of the lower-porosity layer should be 9.8% higher than the maximum stress of the higher-porosity layer.
- Lou CW, Huang SY, Huang CH, et al. Effects of structure design on resilience and acoustic absorption properties of porous flexible-foam based perforated composites. Fibers Polym. 2015;16:2652-2662. doi: 10.1007/s12221-015-5164-6
- Du Plessis P, Montillet A, Comiti J, Legrand J. Pressure drop prediction for flow through high porosity metallic foams. Chem Eng Sci. 1994;49(21):3545-3553. doi: 10.1016/0009-2509(94)00170-7
- Berman B. 3-D printing: The new industrial revolution. Bus Horiz. 2012;55(2):155-162. doi: 10.1016/j.bushor.2011.11.003
- Chua CK, Leong KF. 3D Printing and Additive Manufacturing: Principles and Applications (With Companion Media Pack)-of Rapid Prototyping. Singapore: World Scientific Publishing Company; 2014.
- Kuo C, Chua CK, Peng P, et al. Microstructure evolution and mechanical property response via 3D printing parameter development of Al-Sc alloy. Virtual Phys Prototyp. 2020;15(1):120-129. doi: 10.1080/17452759.2019.1698967
- Mussatto A, UI Ahad I, Mousavian RT, Delaure Y, Brabazon D. Advanced production routes for metal matrix composites. Eng Rep. 2021;3(5):e12330. doi: 10.1002/eng2.12330
- Zhu Y, Wu X. Heterostructured materials. Prog Mater Sci. 2023;131:101019. doi: 10.1016/j.pmatsci.2022.101019
- Donachie MJ. Titanium: A Technical Guide. United States: ASM International; 2000.
- Chua CK, Leong KF, Lim CS. Rapid Prototyping: Principles and Applications (With Companion CD-ROM). Singapore: World Scientific Publishing Company; 2010. doi: 10.1142/9789812778994_0002
- Wu YC, Kuo CN, Chung YC, Ng CH, Huang JC. Effects of electropolishing on mechanical properties and bio-corrosion of Ti6Al4V fabricated by electron beam melting additive manufacturing. Materials (Basel). 2019;12(9):1466. doi: 10.3390/ma12091466
- Chen D, Kitipornchai S, Yang J. Dynamic response and energy absorption of functionally graded porous structures. Mater Des. 2018;140:473-487. doi: 10.1016/j.matdes.2017.12.019
- Ataee A, Li Y, Fraser D, Song G, Wen C. Anisotropic Ti-6Al-4V gyroid scaffolds manufactured by Electron Beam Melting (EBM) for bone implant applications. Mater Des. 2018;137:345-354. doi: 10.1016/j.matdes.2017.10.040
- Burton HE, Eisenstein NM, Lawless BM, et al. The design of additively manufactured lattices to increase the functionality of medical implants. Mater Sci Eng C Mater Biol Appl. 2019;94:901-908. doi: 10.1016/j.msec.2018.10.052
- Sudarmadji N, Tan JY, Leong KF, Chua CK, Loh YT. Investigation of the mechanical properties and porosity relationships in selective laser-sintered polyhedral for functionally graded scaffolds. Acta Biomater. 2011;7(2): 530-537. doi: 10.1016/j.actbio.2010.09.024
- Choy SY, Sun CN, Leong KF, Wei J. Compressive properties of Ti-6Al-4V lattice structures fabricated by selective laser melting: Design, orientation and density. Addit Manuf. 2017;16:213-224. doi: 10.1016/j.addma.2017.06.012
- Xiao L, Song W, Hu M, Li P. Compressive properties and micro-structural characteristics of Ti-6Al-4V fabricated by electron beam melting and selective laser melting. Mater Sci Eng A. 2019;764:138204. doi: 10.1016/j.msea.2019.138204
- Ahmadi SM, Yavari SA, Wauthle R, et al. Additively manufactured open-cell porous biomaterials made from six different space-filling unit cells: The mechanical and morphological properties. Materials (Basel). 2015;8(4): 1871-1896. doi: 10.3390/ma8041871
- Noronha J, Dash J, Rogers J, Leary M, Brandt M, Qian M. Titanium multi‐topology metamaterials with exceptional strength. Adv Mater. 2024;36:e2308715. doi: 10.1002/adma.202308715
- Noronha J, Leary M, Brandt M, Qian M. AlSi10Mg hollow-strut lattice metamaterials by laser powder bed fusion. Mater Adv. 2024;5(9):3751-3770. doi: 10.1039/D3MA00813D
- Abdullahi HS, Zhuo S, Fu D, Gao S. Design of multi-topology lattice structures based on a high-quality unit cell library. Mech Based Des Struct Mach. 2024:1-16. doi: 10.1080/15397734.2024.2353323
- Wu ZY, Liu YJ, Bai HW, et al. Microstructure and mechanical behavior of rhombic dodecahedron-structured porous β-Ti composites fabricated via laser powder bed fusion. J Mater Res Technol. 2024;31:298-310. doi: 10.1016/j.jmrt.2024.06.077
- Bernard AR, Yalcin MM, ElSayed MS. Crashworthiness investigations for 3D printed multi-layer multi-topology carbon fiber nylon lattice materials. J Reinf Plast Compos. 2024;52. doi: 10.1177/07316844241226834
- Bernard AR, ElSayed MS. Design, manufacturing, and analysis of periodic three-dimensional cellular materials for energy absorption applications: A critical review. Materials (Basel). 2024;17(10):2181. doi: 10.3390/ma17102181
- Tancogne-Dejean T, Spierings AB, Mohr D. Additively-manufactured metallic micro-lattice materials for high specific energy absorption under static and dynamic loading. Acta Mater. 2016;116:14-28. doi: 10.1016/j.actamat.2016.05.054
- Al-Saedi DS, Masood S, Faizan-Ur-Rab M, Alomarah A, Ponnusamy P. Mechanical properties and energy absorption capability of functionally graded F2BCC lattice fabricated by SLM. Mater Des. 2018;144:32-44. doi: 10.1016/j.matdes.2018.01.059
- Gibson IJ, Ashby MF. The mechanics of three-dimensional cellular materials. Proc R Soc Lond A Math Phys Sci. 1982;382(1782):43-59. doi: 10.1098/rspa.1982.0088
- Wang Y, Kuo C. Research on energy absorption of gradient porosity structural materials. Mater Today Proc. 2022;70: 578-582. doi: 10.1016/j.matpr.2022.09.594
- Chen S, Kuo C, Su Y, et al. Microstructure and fracture properties of open-cell porous Ti-6Al-4V with high porosity fabricated by electron beam melting. Mater Charact. 2018;138:255-262. doi: 10.1016/j.matchar.2018.02.016
- Yu S, Sun J, Bai J. Investigation of functionally graded TPMS structures fabricated by additive manufacturing. Mater Des. 2019;182:108021. doi: 10.1016/j.matdes.2019.108021
- Song K, Wang Z, Lan J, Ma S. Porous structure design and mechanical behavior analysis based on TPMS for customized root analogue implant. J Mech Behav Biomed Mater. 2021;115:104222. doi: 10.1016/j.jmbbm.2020.104222
- Zhong M, Zhou W, Xi H, Liang Y, Wu Z. Double-level energy absorption of 3d printed tpms cellular structures via wall thickness gradient design. Materials (Basel). 2021;14(21):6262. doi: 10.3390/ma14216262
- Wang Y, Ren X, Chen Z, et al. Numerical and experimental studies on compressive behavior of Gyroid lattice cylindrical shells. Mater Des. 2020;186:108340. doi: 10.1016/j.matdes.2019.108340
- Dai R, Li D, Liao W, Sun H, Tang Y, Nian Q. Molecular dynamics simulations to understand the mechanical behavior of functional gradient nano-gyroid structures. J Appl Phys. 2022;132(13):135109. doi: 10.1063/5.0102297
- Chen J, Song C, Deng Z, et al. Functional gradient design of additive manufactured gyroid tantalum porous structures: Manufacturing, mechanical behaviors and permeability. J Manuf Processes. 2024;125:202-216. doi: 10.1016/j.jmapro.2024.07.054