Triply periodic minimal surfaces lattice structures: Functional graded and hybrid designs for engineering applications
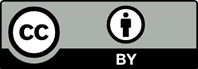
In this work, we propose the strategies for designing radial graded sheet-based gyroid lattice and the approach to hybridizing solid-network-based gyroid lattice and primitive lattice. The elastic property of triply periodic minimal surfaces (TPMS) sheet-based gyroid lattice structures was explored. We also conducted numerical analysis to investigate the effect of functionally graded sheet-based gyroid lattices on the implant application, and explored the elastic properties of the uniform gyroid lattice parametrically with different relative densities based on the representative volume element model. Analytical equations based on the Gibson-Ashby model were generated to predict the elastic properties. Compressive tests on the samples fabricated by the Stratasys J750 were conducted to validate the feasibility of applying hybridization of different types of lattices. A comparison between radial hybrid primitive-gyroid and gyroid-primitive lattices revealed that the compressive behavior of gyroid-primitive was strengthened. We also found that the gyroid-primitive lattice could achieve auxetic compressive behavior. In conclusion, the numerical analysis illustrates that the application of the functional graded gyroid lattices can relieve the stress shielding effect as well as protects the bone from damage. The hybridization of different lattices can not only strengthen the mechanical properties of TPMS structures but also create a counter-intuitive deformation response.
Phuong Tran serves as the Editorial Board Member of the journal, but did not in any way involve in the editorial and peer-review process conducted for this paper, directly or indirectly.
- Pan C, Han Y, Lu J, 2020, Design and optimization of lattice structures: A review. Appl Sci, 10: 6374. https://doi.org/10.3390/app10186374
- Nazir A, Abate KM, Kumar A, et al., 2019, A state-of-the-art review on types, design, optimization, and additive manufacturing of cellular structures. Int J Adv Manufact Technol, 104: 3489–3510. https://doi.org/10.1007/s00170-019-04085-3
- Xu F, Zhang X, Zhang H, 2018, A review on functionally graded structures and materials for energy absorption. Eng Struct, 171: 309–325. https://doi.org/10.1016/j.engstruct.2018.05.094
- Wickramasinghe S, Do T, Tran P, 2020, FDM-based 3D printing of polymer and associated composite: A review on mechanical properties, defects and treatments. Polymers (Basel), 12: 1529. https://doi.org/10.3390/polym12071529
- Tran P, Ngo TD, Ghazlan A, et al., 2017, Bimaterial 3D printing and numerical analysis of bio-inspired composite structures under in-plane and transverse loadings. Compos Part B Eng, 108: 210–223. https:/doi.org//10.1016/j.compositesb.2016.09.083
- Tee YL, Tran P, Leary M, et al., 2020, 3D Printing of polymer composites with material jetting: Mechanical and fractographic analysis. Addit Manuf, 36: 101558. https://doi.org/10.1016/j.addma.2020.101558
- Han XH, Wang Q, ParkYG, et al., 2012, A review of metal foam and metal matrix composites for heat exchangers and heat sinks. Heat Transfer Eng, 33: 991–1009. https://doi.org/10.1080/01457632.2012.659613
- Dixit T, Nithiarasu P, Kumar S, 2021, Numerical evaluation of additively manufactured lattice architectures for heat sink applications. Int J Therm Sci, 159: 106607. https://doi.org/10.1016/j.ijthermalsci.2020.106607
- Samson S, Tran P, Marzocca, 2018, Design and modelling of porous gyroid heatsinks: Influences of cell size, porosity and material variation. Appl Therm Eng, 235: 121296. https://doi.org/10.1016/j.applthermaleng.2023.121296
- Attarilar S, Ebrahimi M, Djavanroodi F, et al., 2021, 3D printing technologies in metallic implants: A thematic review on the techniques and procedures. Int J Bioprint, 7: 306. https://doi.org/10.18063/ijb.v7i1.306
- Depboylu FN, Yasa E, Poyraz Ö, et al., 2022, Titanium based bone implants production using laser powder bed fusion technology. J Mater Res Techn, 17: 1408–1426. https://doi.org/10.1016/j.jmrt.2022.01.087
- Yin H, Zhang W, Zhu L, et al., 2022, Review on lattice structures for energy absorption properties. Compos Struct, 304: 16397. https://doi.org/10.1016/j.compstruct.2022.116397
- Maconachie T, Leary M, Lozanovski B, et al., 2019, SLM lattice structures: Properties, performance, applications and challenges. Mater Des, 183: 10813. https://doi.org/10.1016/j.matdes.2019.108137
- Crook C, Bauer J, Izard AG, et al., 2020, Plate-nanolattices at the theoretical limit of stiffness and strength. Nat Commun, 11: 1579. https://doi.org/10.1038/s41467-020-15434-2
- Novak N, Al-Ketan O, Krstulović-Opara L, et al., 2021, Quasi-static and dynamic compressive behaviour of sheet TPMS cellular structures. Compos Struct, 266: 113801. https://doi.org/10.1016/j.compstruct.2021.113801
- Peng C, Tran P, 2020, Bioinspired functionally graded gyroid sandwich panel subjected to impulsive loadings. Compos Part B Eng, 188: 107773. https://doi.org/10.1016/j.compositesb.2020.107773
- Peng C, Tran P, Mouritz AP, 2022, Compression and buckling analysis of 3D printed carbon fibre-reinforced polymer cellular composite structures. Compos Struct, 300: 116167. https://doi.org/10.1016/j.compstruct.2022.116167
- Al-Ketan O, Lee DW, Rowshan R, et al., 2020, Functionally graded and multi-morphology sheet TPMS lattices: Design, manufacturing, and mechanical properties. J Mech Behav Biomed Mater, 102: 103520. https://doi.org/10.1016/j.jmbbm.2019.103520
- Novak N, Al-Ketan O, Borovinšek M, et al., 2021, Development of novel hybrid TPMS cellular lattices and their mechanical characterisation. J Mater Res Techn, 15: 1318–1329. https://doi.org/10.1016/j.jmrt.2021.08.092
- Al-Ketan O, Abu Al-Rub RK, 2019, Multifunctional mechanical-metamaterials based on triply periodic minimal surface lattices: A review. Adv Eng Mater, 21: 1900524. https://doi.org/10.1002/adem.201900524
- Du Plessis A, Yadroitsava I, Yadroitsev I, et al., 2018, Numerical comparison of lattice unit cell designs for medical implants by additive manufacturing. Virtual Phys Prototyp, 13: 266–281. https://doi.org/10.1080/17452759.2018.1491713
- Han C, Li Y, Wang Q, et al., 2018, Continuous functionally graded porous titanium scaffolds manufactured by selective laser melting for bone implants. J Mech Behav Biomed Mater, 80: 119–127. https://doi.org/10.1016/j.jmbbm.2018.01.013
- Ren F, Zhang C, Liao W, et al., 2021 Transition boundaries and stiffness optimal design for multi-TPMS lattices. Mater Des, 210: 110062. https://doi.org/10.1016/j.matdes.2021.110062a
- Yang N, Quan Z, Zhang D, 2014, Multi-morphology transition hybridization CAD design of minimal surface porous structures for use in tissue engineering. Comput Aided Des, 56: 11–21. https://doi.org/10.1016/j.cad.2014.06.006
- Dong G, Tang Y, Zhao YF, 2019, A 149 line homogenization code for three-dimensional cellular materials written in matlab. J Eng Mater Technol, 141: 011005. https://doi.org/10.1115/1.4040555
- Peng C, Tran P, Nguyen-Xuan H, et al., 2020, Mechanical performance and fatigue life prediction of lattice structures: Parametric computational approach. Compos Struct, 235: 111821. https://doi.org/10.1016/j.compstruct.2019.111821
- Ashby MF, 2006, The properties of foams and lattices. Philos Trans A Math Phys Eng Sci, 364: 15–30. https://doi.org/10.1098/rsta.2005.1678
- Wu C, Do TT, Tran P, 2021, Mechanical properties of polyjet 3d-printed composites inspired by space-filling peano curves. Polymers, 13: 3516. https://doi.org/10.3390/polym13203516
- Tee YL, Peng C, Pille P, et al., 2020, PolyJet 3D printing of composite materials: Experimental and modelling approach. Jom, 72: 1105–1117. https://doi.org/10.1007/s11837-020-04014-w
- Ren X, Das R, Tran P, et al., 2018, Auxetic metamaterials and structures: A review. Smart Mater Struct, 27: 23001. https://doi.org/10.1088/1361-665X/aaa61c