Inconel 718-CoCrMo bimetallic structures through directed energy deposition-based additive manufacturing
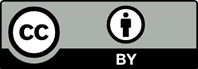
Bimetallic structures and coatings through additive manufacturing (AM) have demonstrated a high degree of freedom for tailoring properties depending on the application. In this study, Inconel 718 and CoCrMo were used as both are common alloys and exhibit unique properties, such as high-temperature oxidation, wear, and fatigue resistance. Using directed energy deposition-based metal AM, bimetallic structures containing these two alloys were manufactured, and the resulting structures exhibited no intermetallic phase formation, cracking, or porosity. Scanning electron microscopy and energy dispersive spectroscopy revealed a smooth elemental transition between the two compositions. Hardness testing showed a linear transition in the interfacial zone, validating no brittle intermetallic phase formation. Compression testing and fracture surface analysis revealed that the failures were not dependent on the interface properties. High-temperature oxidation showed no distinct effect on the interface, a firmly attached chromium oxide layer on the Inconel 718 side and a loosely attached chromium oxide layer on the CoCrMo side. There was also evidence of pit formation on the Inconel 718 surface, but not on the CoCrMo. These findings confirm a stable bimetallic system in which one of the two alloys can be used on the other material to improve the structure’s high-temperature oxidation or wear/corrosion resistance.
Kim IH, Jung YI, Kim HG, et al., 2021, Oxidation-resistant coating of FeCrAl on Zr-alloy tubes using 3D printing direct energy deposition. Surf Coat Technol, 411: 126915. https://doi.org/10.1016/j.surfcoat.2021.126915
Shang F, Chen S, Zhou L, et al., 2021, Effect of laser energy volume density on wear resistance and corrosion resistance of 30Cr15MoY alloy steel coating prepared by laser direct metal deposition. Surf Coat Technol, 421: 127382. https://doi.org/10.1016/j.surfcoat.2021.127382
Groden C, Traxel KD, Afrouzian A, et al., 2022, Inconel 718-W7Ni3Fe bimetallic structures using directed energy deposition-based additive manufacturing. Virtual Phys Prototyp 17: 170–180. https://doi.org/10.1080/17452759.2022.2025673
Onuike B, Heer B, Bandyopadhyay A, 2018, Additive manufacturing of inconel 718-copper alloy bimetallic structure using laser engineered net shaping (LENSTM). Addit Manuf, 21: 133–140. https://doi.org/10.1016/j.addma.2018.02.007
Traxel KD, Bandyopadhyay A, 2021, Modeling and experimental validation of additively manufactured tantalum-titanium bimetallic interfaces. Mater Des, 207: 109793. https://doi.org/10.1016/j.matdes.2021.109793
Bandyopadhyay A, Zhang Y, Onuike B, 2022, Additive manufacturing of bimetallic structures. Virtual Phys Prototyp, 17: 256–294. https://doi.org/10.1080/17452759.2022.2040738
Zhang Y, Bandyopadhyay A, 2019, Direct fabrication of bimetallic Ti6Al4V+Al12Si structures via additive manufacturing. Addit Manuf, 29: 100783. https://doi.org/10.1016/j.addma.2019.100783
Afrouzian A, Groden CJ, Field DP, et al., 2022, Additive manufacturing of Ti-Ni bimetallic structures. Mater Des, 215: 110461. https://doi.org/10.1016/j.matdes.2022.110461
Yao L, Huang S, Ramamurty U, et al., 2021, On the formation of “Fish-Scale” morphology with curved grain interfacial microstructures during selective laser melting of dissimilar alloys. Acta Mater, 220: 117331. https://doi.org/10.1016/j.actamat.2021.117331
Sing SL, Huang S, Goh GD, et al., 2021, Emerging metallic systems for additive manufacturing: In-situ alloying and multi-metal processing in laser powder bed fusion. Prog Mater Sci, 119: 100795. https://doi.org/10.1016/j.pmatsci.2021.100795
Wang Z, Wang J, Xu S, et al., 2022, Influence of powder characteristics on microstructure and mechanical properties of inconel 718 superalloy manufactured by direct energy deposition. Appl Surf Sci, 583: 152545. https://doi.org/10.1016/j.apsusc.2022.152545
Hosseini E, Popovich VA, 2019, A review of mechanical properties of additively manufactured inconel 718. Addit Manuf, 30: 100877. https://doi.org/10.1016/j.addma.2019.100877
Cao GH, Sun TY, Wang CH, et al., 2018, Investigations of Γ’, Γ” and δ precipitates in heat-treated inconel 718 alloy fabricated by selective laser melting. Mater Charact, 136: 398–406. https://doi.org/10.1016/j.matchar.2018.01.006
Wan HY, Zhou ZJ, Li CP, et al., 2018, Enhancing fatigue strength of selective laser melting-fabricated inconel 718 by tailoring heat treatment route. Adv Eng Mater 20: 1800307. https://doi.org/10.1002/adem.201800307
Ling LS, Yin Z, Hu Z, et al., 2019, Effects of the Γ”-Ni(3)Nb phase on mechanical properties of inconel 718 superalloys with different heat treatments. Materials (Basel, Switzerland), 13: 151. https://doi.org/10.3390/ma13010151
Teixeira Ó, Silva FJ, Atzeni E, 2021, Residual stresses and heat treatments of inconel 718 parts manufactured via metal laser beam powder bed fusion: An overview. Int J Adv Manuf Technol, 113: 3139–3162. https://doi.org/10.1007/s00170-021-06835-8
Zhang B, Xiu M, Tan YT, et al., 2019, Pitting corrosion of SLM inconel 718 sample under surface and heat treatments. Appl Surf Sci, 490: 556–567. https://doi.org/10.1016/j.apsusc.2019.06.043
Li L, Gong X, Ye X, et al., 2018, Influence of building direction on the oxidation behavior of inconel 718 alloy fabricated by additive manufacture of electron beam melting. Materials (Basel), 11: 2549. https://doi.org/10.3390/ma11122549
Hedberg YS, Qian B, Shen Z, et al., 2014, In vitro biocompatibility of CoCrMo dental alloys fabricated by selective laser melting. Dent Mater, 30: 525–534. https://doi.org/10.1016/j.dental.2014.02.008
Wang Q, Parry M, Masri BA, et al., 2017, Failure mechanisms in CoCrMo modular femoral stems for revision total hip arthroplasty. J Biomedl Mater Res B Appl Biomater, 105: 1525–1535. https://doi.org/10.1002/jbm.b.33693
Mantrala KM, Das M, Balla VK, et al., 2014, Laser-deposited CoCrMo alloy: Microstructure, wear, and electrochemical properties. J Mater Res, 29: 2021–2027. https://doi.org/10.1557/jmr.2014.163
Girão DC, Béreš M, Jardini AL, et al., 2020, An assessment of biomedical CoCrMo alloy fabricated by direct metal laser sintering technique for implant applications. Mater Sci Eng C, 107: 110305. https://doi.org/10.1016/j.msec.2019.110305
Dijmarescu MR, Popovici TD, Tarba IC, et al., 2018, An experimental study on cutting forces when machining a CoCrMo alloy. IOP Conf Mater Sci Eng, 400: 022019. https://doi.org/10.1088/1757-899X/400/2/022019
Fernandez-Zelaia P, Nguyen V, Zhang H, et al., 2019, The effects of material anisotropy on secondary processing of additively manufactured CoCrMo. Addit Manuf, 29: 100764. https://doi.org/10.1016/j.addma.2019.06.015
Bettini E, Eriksson T, Boström M, et al., 2011, Influence of metal carbides on dissolution behavior of biomedical CoCrMo alloy: SEM, TEM and AFM studies. Electrochim Acta, 56: 9413–9419. https://doi.org/10.1016/j.electacta.2011.08.028
Bawane KK, Srinivasan D, Banerjee D, 2018, Microstructural evolution and mechanical properties of direct metal laser-sintered (DMLS) CoCrMo after heat treatment. Metallurgical Mater Trans A, 49: 3793–3811. https://doi.org/10.1007/s11661-018-4771-4
Cornacchia G, Cecchel S, Battini D, et al., 2022, Microstructural, mechanical, and tribological characterization of selective laser melted CoCrMo alloy under different heat treatment conditions and hot isostatic pressing. Adv Eng Mater, 24: 2100928. https://doi.org/10.1002/adem.202100928
Wen Y, Zhang B, Narayan RL, et al., 2021, Laser powder bed fusion of compositionally graded CoCrMo-inconel 718. Addit Manuf, 40: 101926. https://doi.org/10.1016/j.addma.2021.101926
Khanna AS, 2018, High-temperature oxidation. In: Kutz M, editor. Handbook of Environmental Degradation of Materials. 3rd ed., Ch. 6. William Andrew Publishing, Norwich, NY, p117–132. https://doi.org/10.1016/B978-0-323-52472-8.00006-X
Oje AM, Ogwu AA, 2017, Chromium oxide coatings with the potential for eliminating the risk of chromium ion release in orthopaedic implants. R Soc Open Sci, 4: 170218. https://doi.org/10.1098/rsos.170218
Tsai SC, Huntz AM, Dolin C, 1996, Growth mechanism of Cr2O3 scales: Oxygen and chromium diffusion, oxidation kinetics and effect of yttrium. Mater Sci Eng A, 212: 6–13. https://doi.org/10.1016/0921-5093(96)10173-8
Mayrhofer PH, Rachbauer R, Holec D, et al., 2014, 4.14-protective transition metal nitride coatings. In: Hashmi S, Editor-in-Chief. Comprehensive Materials Processing. Elsevier, Oxford, p355–388. https://doi.org/10.1016/B978-0-08-096532-1.00423-4