Cold spray additive manufacturing of copper-based materials: Review and future directions
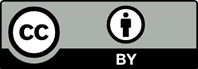
The cold gas dynamic spray process is a manufacturing process strategically designed for coatings. The conditions for the deposition of materials to form coatings have evolved over several decades. Copper and copper-based cold spray coatings are an interesting field for investigation, as it has substantial commercial demand and acceptance. Several important works have already been performed in this regard that shows the immense popularity of its applications in power industries. Cold gas dynamic spray, being an economic process, can produce coatings with superior quality and low oxidation. In this paper, a particular focus has been given to copper-based cold spray coatings along with their deposition parameters. The various mechanical, electrical, corrosion, and tribological properties of these copper-based cold spray coatings are commendable and economically lucrative. A good amount of experimental data has also been included in this review article to provide comprehensive information and future scope of research about copper-based cold spray coatings.
Clodualdo Aranas Jr. serves as the Editorial Board Member of the journal, but did not in any way involve in the editorial and peer-review process conducted for this paper, directly or indirectly.
Alkhimov AP, Papyrin AN, Kosarev VF, et al., 1994, Gas-dynamic spraying method for applying a coating (United States Patent No. US5302414A). Available from: https://patents.google.com/patent/US5302414A/en [Last accessed on 2022 May 31].
Tokarev AO, 1996, Structure of aluminum powder coatings prepared by cold gasdynamic spraying. Metal Sci Heat Treat, 38: 136–139. https://doi.org/10.1007/BF01401446
Sripada J, Gallant M, Saha G, 2019, Study on the effect of milling parameters on HE-MA nanostructured Al-graphene cermet particles. Proceedings of 1st Coatings and Interfaces Web Conference, 2019, 6160. https://doi.org/10.3390/ciwc2019-06160
McCune RC, Donlon WT, Popoola OO, et al., 2000, Characterization of copper layers produced by cold gas-dynamic spraying. J Therm Spray Technol, 9: 73–82. https:// doi.org/10.1361/105996300770350087
Woo DJ, Heer FC, Brewer LN, et al., 2015, Synthesis of nanodiamond-reinforced aluminum metal matrix composites using cold-spray deposition. Carbon, 86: 15–25. https://doi.org/10.1016/j.carbon.2015.01.010
Popovich A, Sufiiarov V, 2016. Metal powder additive manufacturing. In: Shishkovsky IV, editor. New Trends in 3D Printing. InTech, London. https://doi.org/10.5772/63337
Raoelison RN, Xie Y, Sapanathan T, et al., 2018, Cold gas dynamic spray technology: A comprehensive review of processing conditions for various technological developments till to date. Addit Manuf, 19: 134–159. https:// doi.org/10.1016/j.addma.2017.07.001
Stoltenhoff T, Kreye H, Richter HJ, 2002, An analysis of the cold spray process and its coatings. J Therm Spray Technol, 11: 542–550. https://doi.org/10.1361/105996302770348682
Suryanarayana C, 2001, Mechanical alloying and milling. Prog Mater Sci, 46: 1–184. https://doi.org/10.1016/S0079-6425(99)00010-9
Zhang DL, 2004, Processing of advanced materials using high-energy mechanical milling. Prog Mater Sci, 3–4: 537–560. https://doi.org/10.1016/S0079-6425(03)00034-3
Sripada JV, Saha DC, Saha GC, et al., 2021, Study the effect of milling parameters on HE-MA nanostructured Al6061-graphene cermet feedstock particles. J Alloys Comp, 859: 157759. https://doi.org/10.1016/j.jallcom.2020.157759
Hu Z, Chen F, Xu J, et al., 2018, 3D printing graphene-aluminum nanocomposites. J Alloys Comp, 746: 269–276. https://doi.org/10.1016/j.jallcom.2018.02.272
Toozandehjani M, Matori KA, Ostovan F, et al., 2017, Effect of milling time on the microstructure, physical and mechanical properties of Al-Al2O3 nanocomposite synthesized by ball milling and powder metallurgy. Materials, 10: 1232. https://doi.org/10.3390/ma10111232
Nouri A, Wen C, 2014, Surfactants in mechanical alloying/ milling: A catch-22 situation. Crit Rev Solid State Mater Sci, 39: 81–108. https://doi.org/10.1080/10408436.2013.808985
Kollo L, Leparoux M, Bradbury CR, et al., 2010, Investigation of planetary milling for nano-silicon carbide reinforced aluminium metal matrix composites. J Alloys Comp, 489: 394–400. https://doi.org/10.1016/j.jallcom.2009.09.128
Lu L, Zhang YF, 1999, Influence of process control agent on interdiffusion between Al and Mg during mechanical alloying. J Alloys Comp, 290: 279–283. https://doi.org/10.1016/S0925-8388(99)00221-2
Shaw L, Villegas J, Luo H, et al., 2003, Effects of process-control agents on mechanical alloying of nanostructured aluminum alloys. Metallurgical Mater Trans A Phys Metallurgy Mater Sci, 34: 159–170. https://doi.org/10.1007/s11661-003-0217-7
Legoux JG, Irissou E, Desaulniers S, et al., n.d., Characterization and Performance Evaluation of a Helium Recovery System Designed for Cold Spraying. National Research Council Canada, Canada.
Cao K, Yu M, Liang CM, et al., 2020, Study on thermal conductivity of cold sprayed Cu coating. Surface Eng, 36: 1058–1066. https://doi.org/10.1080/02670844.2020.1790170
Yin S, Xie Y, Cizek J, et al., 2017, Advanced diamond-reinforced metal matrix composites via cold spray: Properties and deposition mechanism. Compos B Eng, 113: 44–54. https://doi.org/10.1016/j.compositesb.2017.01.009
Imbriglio SI, Chromik RR., 2021, Factors affecting adhesion in metal/ceramic interfaces created by cold spray. J Therm Spray Technol, 30: 1703–1723. https://doi.org/10.1007/s11666-021-01229-4
Pathak S, Saha GC., 2017, Development of sustainable cold spray coatings and 3D additive manufacturing components for repair/manufacturing applications: A critical review. Coatings, 7: 122. https://doi.org/10.3390/coatings7080122
Fukumoto M, Wada H, Tanabe K, et al., 2007, Effect of substrate temperature on deposition behavior of copper particles on substrate surfaces in the cold spray process. J Therm Spray Technol, 16: 643–650. https://doi.org/10.1007/s11666-007-9121-9
Borchers C, Stoltenhoff T, Gärtner F, et al., 2001, Deformation microstructure of cold gas sprayed coatings. Mater Res Soc Symp Proc, 674: P7.10.1–P.10.6. https://doi.org/10.1557/proc-673-p7.10
Assadi H, Kreye H, Gärtner F, et al., 2016, Cold spraying a materials perspective. Acta Materi, 116: 382–407. https://doi.org/10.1016/j.actamat.2016.06.034
Moridi A, Hassani-Gangaraj SM, Guagliano M, et al., 2014, Cold spray coating: Review of material systems and future perspectives. Surface Eng, 30: 369–395. https://doi.org/10.1179/1743294414Y.0000000270
Winnicki M, Małachowska A, Piwowarczyk T, et al., 2016, The bond strength of Al + Al2O3 cermet coatings deposited by low-pressure cold spraying. Arch Civil Mech Eng, 16: 743–752. https://doi.org/10.1016/j.acme.2016.04.014
Koivuluoto H, Vuoristo P, 2010, Effect of powder type and composition on structure and mechanical properties of Cu + Al2O3 coatings prepared by using low-pressure cold spray process. J Therm Spray Technol, 19: 1081–1092. https://doi.org/10.1007/s11666-010-9491-2
Phani PS, Vishnukanthan V, Sundararajan G, 2007, Effect of heat treatment on properties of cold sprayed nanocrystalline copper alumina coatings. Acta Mater, 55: 4741–4751. https://doi.org/10.1016/j.actamat.2007.04.044
Winnicki M, Baszczuk A, Jasiorski M, et al., 2017, Corrosion resistance of copper coatings deposited by cold spraying. J Therm Spray Technol, 26: 1935–1946. https://doi.org/10.1007/s11666-017-0646-2
Chen W, Yu Y, Cheng J, et al., 2018, Microstructure, mechanical properties and dry sliding wear behavior of Cu-Al2O3-graphite solid-lubricating coatings deposited by low-pressure cold spraying. J Therm Spray Technol, 27: 1652–1663. https://doi.org/10.1007/s11666-018-0773-4
Zhan GD, Kuntz JD, Wan J, et al., 2003, Single-wall carbon nanotubes as attractive toughening agents in alumina-based nanocomposites. Nat Mater, 2: 38–42. https://doi.org/10.1038/nmat793
Coleman JN, Khan U, Blau WJ, et al., 2006, Small but strong: A review of the mechanical properties of carbon nanotube-polymer composites. Carbon, 44: 1624–1652. https://doi.org/10.1016/j.carbon.2006.02.038
Ajayan PM, Tour JM, 2007, Nanotube composites. Nature, 447: 1066–1068. https://doi.org/10.1038/4471066a
Kwon H, Estili M, Takagi K, et al., 2009, Combination of hot extrusion and spark plasma sintering for producing carbon nanotube reinforced aluminum matrix composites. Carbon, 47: 570–577. https://doi.org/10.1016/j.carbon.2008.10.041
Cha SI, Kim KT, Arshad SN, et al., 2005, Extraordinary strengthening effect of carbon nanotubes in metal-matrix nanocomposites processed by molecular-level mixing. Adv Mater, 17: 1377–1381. https://doi.org/10.1002/adma.200401933
Bakshi SR, Lahiri D, Agarwal A, 2010, Carbon nanotube reinforced metal matrix composites a review. Int Mater Rev, 55: 41–64. https://doi.org/10.1179/095066009X12572530170543
Shukla AK, Nayan N, Murty SV, et al., 2013, Processing of copper-carbon nanotube composites by vacuum hot pressing technique. Mater Sci Eng A, 560: 365–371. https://doi.org/10.1016/j.msea.2012.09.080
Kang K, Bae G, Won J, et al., 2012, Mechanical property enhancement of kinetic sprayed Al coatings reinforced by multi-walled carbon nanotubes. Acta Mater, 60: 5031–5039. https://doi.org/10.1016/j.actamat.2012.05.034
Xie X, Chen C, Ji G, et al., 2019, A novel approach for fabricating a CNT/AlSi composite with the self-aligned nacre-like architecture by cold spraying. Nano Mater Sci, 1: 137–141. https://doi.org/10.1016/j.nanoms.2019.04.002
Cho S, Takagi K, Kwon H, et al., 2012, Multi-walled carbon nanotube-reinforced copper nanocomposite coating fabricated by low-pressure cold spray process. Surf Coat Technol, 206: 3488–3494. https://doi.org/10.1016/j.surfcoat.2012.02.021
Kim P, Shi L, Majumdar A, et al., 2001, Thermal transport measurements of individual multiwalled nanotubes. Phys Rev Lett, 87: 215502. https://doi.org/10.1103/PhysRevLett.87.215502
Cho S, Kikuchi K, Miyazaki T, et al., 2010, Multiwalled carbon nanotubes as a contributing reinforcement phase for the improvement of thermal conductivity in copper matrix composites. Sci Mater, 63: 375–378. https://doi.org/10.1016/j.scriptamat.2010.04.024
Pialago EJ, Park C. Cold spray deposition characteristics of mechanically alloyed Cu-CNT composite powders. Appl Surf Sci, 308: 63–74. https://doi.org/10.1016/J.APSUSC.2014.04.096
Pialago EJ, Kwon OK, Park CW, 2015, Cold spray deposition of mechanically alloyed ternary Cu-CNT-SiC composite powders. Ceram Int, 41: 6764–6775. https://doi.org/10.1016/j.ceramint.2015.01.123
Pialago EJ, Kwon OK, Kim MS, et al., 2015, Ternary Cu-CNT-AlN composite coatings consolidated by cold spray deposition of mechanically alloyed powders. J Alloys Comp, 650: 199–209. https://doi.org/10.1016/j.jallcom.2015.08.007
Chen Q, Yu M, Cao K, et al., 2022, Thermal conductivity and wear resistance of cold sprayed Cu-ceramic phase composite coating. Surf Coat Technol, 434: 128135. https://doi.org/10.1016/j.surfcoat.2022.128135
Novoselov KS, Geim AK, Morozov SV, et al., 2004, Electric field effect in atomically thin carbon films. Science, 306: 666–669. https://doi.org/10.1126/science.1102896
Warner JH, Schaffel F, Rummeli M, et al., 2012, Graphene: Fundamentals and Emergent Applications. Elsevier, Amsterdam, Netherlands, p61-125.
Reina A, Jia X, Ho J, et al., 2009, Large area, few-layer graphene films on arbitrary substrates by chemical vapor deposition. Nano Lett, 9: 30–35. https://doi.org/10.1021/nl801827v
Kotov NA, 2006, Carbon sheet solutions. Nature, 442: 254–255. https://doi.org/10.1038/442254a
Yin S, Zhang Z, Ekoi EJ, et al., 2017, Novel cold spray for fabricating graphene-reinforced metal matrix composites. Mater Lett, 196: 172–175. https://doi.org/10.1016/j.matlet.2017.03.018
Choi J, Okimura N, Yamada T, et al., 2021, Deposition of graphene-copper composite film by cold spray from particles with graphene grown on copper particles. Diam Relat Mater, 116: 108384. https://doi.org/10.1016/j.diamond.2021.108384
Chromik R, Alidokht S, Shockley JM, et al., 2018, Tribological coatings prepared by cold spray. In: Cold-Spray Coatings. Springer, Berlin, p321–348. https://doi.org/10.1007/978-3-319-67183-3_11
Wu Y, Wang F, Cheng Y, et al., 1997, A study of the optimization mechanism of solid lubricant concentration in NiMoS2 self-lubricating composite. Wear, 205: 64–70. https://doi.org/10.1016/S0043-1648(96)07299-7
Miracle DB, 2005, Metal matrix composites from science to technological significance. Comp Sci Technol, 65: 2526–2540. https://doi.org/10.1016/j.compscitech.2005.05.027
Suresha S, Sridhara BK, 2010b, Wear characteristics of hybrid aluminium matrix composites reinforced with graphite and silicon carbide particulates. Comp Sci Technol, 70: 1652–1659. https://doi.org/10.1016/j.compscitech.2010.06.013
Narayanasamy P, Selvakumar N, Balasundar P, 2015, Effect of hybridizing MoS2 on the tribological behaviour of Mg-TiC composites. Trans Indian Inst Metals, 68:911–925. https://doi.org/10.1007/s12666-015-0530-z
Xu J, Liu W, Zhong M, 2006, Microstructure and dry sliding wear behavior of MoS2/TiC/Ni composite coatings prepared by laser cladding. Surf Coat Technol, 200: 4227–4232. https://doi.org/10.1016/j.surfcoat.2005.01.036
Rajkumar K, Aravindan S, 2011, Tribological performance of microwave sintered copper-TiC-graphite hybrid composites. Tribol Int, 44: 347–358. https://doi.org/10.1016/j.triboint.2010.11.008
Suresha S, Sridhara BK, 2010a, Effect of addition of graphite particulates on the wear behaviour in aluminium-silicon carbide-graphite composites. Mater Des, 31: 1804–1812. https://doi.org/10.1016/j.matdes.2009.11.015
Kato H, Takama M, Iwai Y, et al., 2003, Wear and mechanical properties of sintered copper-tin composites containing graphite or molybdenum disulfide. Wear, 225: 573–578. https://doi.org/10.1016/S0043-1648(03)00072-3
Zhang Y, Epshteyn Y, Chromik RR, 2018, Dry sliding wear behaviour of cold-sprayed Cu-MoS2 and Cu-MoS2-WC composite coatings: The influence of WC. Tribol Int, 123: 296–306. https://doi.org/10.1016/j.triboint.2017.12.015
Tu J, Rong W, Guo S, et al., 2003, Dry sliding wear behavior of in situ Cu-TiB2 nanocomposites against medium carbon steel. Wear, 255: 832–835. https://doi.org/10.1016/S0043-1648(03)00115-7
Valero ML, Corredor D, Camurri C, et al., 2005, Performance and characterization of dispersion strengthened Cu-TiB2 composite for electrical use. Mater Characterization, 55: 252–262. https://doi.org/10.1016/j.matchar.2005.04.006
Kim JS, Kwon YS, Dudina DV, et al., 2005, Nanocomposites TiB2-Cu: Consolidation and erosion behavior. J Mater Sci, 40: 3491–3495. https://doi.org/10.1007/s10853-005-2854-2
Agarwal A, Dahotre NB, Sudarshan TS, 1999, Evolution of interface in pulsed electrode deposited titanium diboride on copper and steel. Surf Eng, 15: 27–32. https://doi.org/10.1179/026708499322911601
Tu J, Wang NY, Yang YZ, et al., 2002, Preparation and properties of TiB2 nanoparticle reinforced copper matrix composites by in situ processing. Mater Lett, 52: 448–452. https://doi.org/10.1016/S0167-577X(01)00442-6
Munro RG, 2000, Material properties of titanium diboride. J Res Natl Inst Stand Technol, 105: 709. https://doi.org/10.6028/jres.105.057
Kim JS, Kwon YS, Lomovsky OI, et al., 2007, Cold spraying of in situ produced TiB2-Cu nanocomposite powders. Comp Sci Technol, 67: 2292–2296. https://doi.org/10.1016/j.compscitech.2007.01.019
Calli C, Tazegul O, Kayali ES, 2017, Wear and corrosion characteristics of copper-based composite coatings. Ind Lubr Tribol, 69: 300–305. https://doi.org/10.1108/ILT-07-2016-0146