Influence of powder morphology on laser absorption behavior and printability of nanoparticle-coated 90W-Ni-Fe powder during laser powder bed fusion
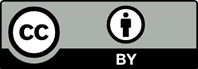
In this work, mesoscopic simulation and experimental studies were applied to investigate the influence of powder morphology and characteristics on laser absorption behavior and printability of nanoparticle-coated 90W-Ni-Fe powder during laser powder bed fusion (LPBF). The mechanism of laser-material interaction and the thermal behavior of molten fluid during LPBF were revealed, thereby optimizing the powder preparation parameters. It showed that when the powder preparation parameters were optimized (i.e., ball-to-powder weight ratio of 1:2, milling speed of 250 rpm, and milling time of 6 h), the Ni and Fe nanoparticles were uniformly dispersed on W particles and, meanwhile, the sufficiently high sphericity of the W matrix particles was maintained. The nanoparticle-coated 90W-Ni-Fe powder had a sound laser absorption behavior with laser absorptivity of 93.51%, leading to the high LPBF printing quality with a smooth surface free of balling phenomenon and microcracks. Specimen fabricated using optimally prepared powder has a high density of 98% and a low surface roughness of 7.91 μm. The LPBF-processed 90W-Ni-Fe alloys had a uniform hardness distribution with an average value of 439.47 HV1 and significantly enhanced compression properties with compressive strength of 1255.35 MPa and an elongation of 24.74%. The results in this work provided a physical understanding of complex and interdependent laser-powder interaction and melt pool formation mechanisms during LPBF of W-based alloys that are governed by powder characteristics.
Dongdong Gu serves as the Editorial Board Member of the journal, but did not in any way involve in the editorial and peer-review process conducted for this paper, directly or indirectly.
Ivekovic A, Montero-Sistiaga ML, Vanmeensel K, et al., 2019, Effect of processing parameters on microstructure and properties of tungsten heavy alloys fabricated by SLM. Int J Refract Met Hard Mater, 82: 23–30. http://doi.org/10.1016/j.ijrmhm.2019.03.020
Li JF, Wei ZY, Zhou BK, et al., 2019, Densification, microstructure and properties of 90W-7Ni-3Fe fabricated by selective laser melting. Metals Basel, 9: 884. http://doi.org/10.3390/met9080884
Thompson MK, Moroni G, Vaneker T, et al., 2016, Design for additive manufacturing: Trends, opportunities, considerations, and constraints. Cirp Ann-Manuf Techn, 65: 737–760. http://doi.org/10.1016/j.cirp.2016.05.004
Gu DD, Shi XY, Poprawe R, et al., 2021, Material-structure-performance integrated laser-metal additive manufacturing. Science, 372: eabg1487. http://doi.org/10.1126/science.abg1487
Bourell DL, Rosen DW, Leu MC, 2014, The roadmap for additive manufacturing and its impact. 3D Print Addit Manuf, 1: 6–9. http://doi.org/10.1089/3dp.2013.0002
Schmidt M, Merklein M, Bourell D, et al., 2017, Laser based additive manufacturing in industry and academia. Cirp Ann-Manuf Techn, 66: 561–583. http://doi.org/10.1016/j.cirp.2017.05.011
Field AC, Carter LN, Adkins NJ, et al., 2020, The effect of powder characteristics on build quality of high-purity tungsten produced via laser powder bed fusion (LPBF). Metall Mater Trans A, 51: 1367–1378. http://doi.org/10.1007/s11661-019-05601-6
Zhang JY, Gu DD, Yang Y, et al., 2019, Influence of particle size on laser absorption and scanning track formation mechanisms of pure tungsten powder during selective laser melting. Engineering, 5: 736–745. http://doi.org/10.1016/j.eng.2019.07.003
Braun J, Kaserer L, Stajkovic J, et al., 2019, Molybdenum and tungsten manufactured by selective laser melting: Analysis of defect structure and solidification mechanisms. Int. J Refract Met Hard Mater, 84: 104999. http://doi.org/10.1016/j.ijrmhm.2019.104999
AlMangour B, Grzesiak D, Yang JM, 2017, Selective laser melting of TiB2/316L stainless steel composites: The roles of powder preparation and hot isostatic pressing post-treatment. Powder Technol, 309: 37–48. http://doi.org/10.1016/j.powtec.2016.12.073
AlMangour B, Grzesiak D, Yang JM, 2018, In situ formation of TiC-particle-reinforced stainless steel matrix nanocomposites during ball milling: Feedstock powder preparation for selective laser melting at various energy densities. Powder Technol, 326: 467–478. http://doi.org/10.1016/j.powtec.2017.11.064
Hu ZP, Zhao YN, Guan K, et al., 2020, Pure tungsten and oxide dispersion strengthened tungsten manufactured by selective laser melting: Microstructure and cracking mechanism. Addit Manuf, 36: 101579. http://doi.org/10.1016/j.addma.2020.101579
Khairallah SA, Martin AA, Lee JR, et al., 2020, Controlling interdependent meso-nanosecond dynamics and defect generation inmetal 3D printing. Science, 368: 660–665. http://doi.org/10.1126/science.aay7830
Ge Q, Gu DD, Dai DH, et al., 2021, Mechanisms of laser energy absorption and melting behavior during selective laser melting of titanium-matrix composite: role of ceramic addition. J Phys D Appl Phys, 54: 115103. http://doi.org/10.1088/1361-6463/abcdce
Ren ZH, Zhang DZ, Fu G, et al., 2021, High-fidelity modelling of selective laser melting copper alloy: Laser reflection behavior and thermal-fluid dynamics. Mater Design, 207: 109857. http://doi.org/10.1016/j.matdes.2021.109857
Boley CD, Mitchell SC, Rubenchik AM, et al., 2016, Metal powder absorptivity: Modeling and experiment. Appl Opt, 55: 6496–6500. http://doi.org/10.1364/ao.55.006496
Mosallanejad MH, Niroumand B, Aversa A, et al., 2021, In-situ alloying in laser-based additive manufacturing processes: A critical review. J Alloys Compd, 872: 159567. http://doi.org/10.1016/j.jallcom.2021.159567
Huang S, Narayan RL, Tan JH, et al., 2021, Resolving the porosity-unmelted inclusion dilemma during in-situ alloying of Ti34Nb via laser powder bed fusion. Acta Mater, 204: 116522. http://doi.org/10.1016/j.actamat.2020.116522
Zhang XH, Xiao Z, Yu WH, et al., 2022, Influence of erbium addition on the defects of selective laser-melted 7075 aluminium alloy. Virtual Phys Prototyping, 17: 406–418. http://doi.org/10.1080/17452759.2021.1990358
Sing SL, Huang S, Goh GD, et al., 2021, Emerging metallic systems for additive manufacturing: In-situ alloying and multi-metal processing in laser powder bed fusion. Prog Mater Sci, 119: 100795. http://doi.org/10.1016/j.pmatsci.2021.100795
Guo M, Gu DD, Xi LX, et al., 2019, Selective laser melting additive manufacturing of pure tungsten: Role of volumetric energy density on densification, microstructure and mechanical properties. Int J Refract Met Hard Mater, 84: 105025. http://doi.org/10.1016/j.ijrmhm.2019.105025
Yang Y, Gu DD, Dai DH, et al., 2018, Laser energy absorption behavior of powder particles using ray tracing method during selective laser melting additive manufacturing of aluminum alloy. Mater Design, 143: 12–19. http://doi.org/10.1016/j.matdes.2018.01.043
Xia MJ, Gu DD, Yu GQ, et al., 2016, Selective laser melting 3D printing of Ni-based superalloy: Understanding thermodynamic mechanisms. Sci Bull, 61: 1013–1022. http://doi.org/10.1007/s11434-016-1098-7
Dai DH, Gu DD, Ge Q, et al., 2020, Mesoscopic study of thermal behavior, fluid dynamics and surface morphology during selective laser melting of Ti-based composites. Comput Mater Sci, 177: 109598. http://doi.org/10.1016/j.commatsci.2020.109598
Lin KJ, Fang YM, Gu DD, et al., 2021, Selective laser melting of graphene reinforced titanium matrix composites: Powder preparation and its formability. Adv Powder Technol, 32: 1426–1437. http://doi.org/10.1016/j.apt.2021.03.003
Zhuang J, Gu DD, Xi LX, et al., 2020, Preparation method and underlying mechanism of MWCNTs/Ti6Al4V nanocomposite powder for selective laser melting additive manufacturing. Powder Technol, 368: 59–69. http://doi.org/10.1016/j.powtec.2020.04.041
Attar H, Prashanth KG, Zhang LC, et al., 2015, Effect of powder particle shape on the properties of In Situ Ti-TiB composite materials produced by selective laser melting. J Mater Sci Technol, 31: 1001–1005. http://doi.org/10.1016/j.jmst.2015.08.007
Mio H, Kano J, Saito F, et al., 2004, Optimum revolution and rotational directions and their speeds in planetary ball milling. Int J Miner Process, 74: S85–S92. http://doi.org/10.1016/j.minpro.2004.07.002
Gu DD, Shen YF, 2009, Effects of processing parameters on consolidation and microstructure of W-Cu components by DMLS. J Alloys Compd, 473: 107–115. http://doi.org/10.1016/j.jallcom.2008.05.065
Paradis PF, Ishikawa T, Yoda S, 2005, Viscosity of liquid undercooled tungsten. J Appl Phys, 97: 106101. http://doi.org/10.1063/1.1896432
Zhou X, Liu XH, Zhang DD, et al., 2015, Balling phenomena in selective laser melted tungsten. J Mater Process Technol, 222: 33–42. http://doi.org/10.1016/j.jmatprotec.2015.02.032
Zhang DQ, Cai QZ, Liu JH, et al., 2011, Research on process and microstructure formation of W-Ni-Fe alloy fabricated by selective laser melting. J Mater Eng Perform, 20: 1049–1054. http://doi.org/10.1007/s11665-010-9720-3
DebRoy T, Wei HL, Zuback JS, et al., 2018, Additive manufacturing of metallic components process, structure and properties. Prog Mater Sci, 92: 112–224. http://doi.org/10.1016/j.pmatsci.2017.10.001
Martin JH, Yahata BD, Hundley JM, et al., 2017, 3D printing of high-strength aluminium alloys. Nature, 549: 365–369. http://doi.org/10.1038/nature23894
Li C, Liu ZY, Fang XY, et al., 2018, Residual stress in metal additive manufacturing. Procedia CIRP, 71: 348–353. http://doi.org/10.1016/j.procir.2018.05.039
Abbas MA, Yan AR, Wang ZY, 2021, On the use of EBSD and microhardness to study the microstructure properties of tungsten samples prepared by selective laser melting. Materials, 14: 1215. http://doi.org/10.3390/ma14051215
Zhu HH, Lu L, Fuh JY, 2004, Influence of binder’s liquid volume fraction on direct laser sintering of metallic powder. Mat Sci Eng A-Struct, 371: 170–177. http://doi.org/10.1016/j.msea.2003.11.048
Gu DD, Guo M, Zhang HM, et al., 2020, Effects of laser scanning strategies on selective laser melting of pure tungsten. Int J Extrem Manuf, 2: 025001. http://doi.org/10.1088/2631-7990/ab7b00