Proposing a novel mathematical model for hospital pneumatic system
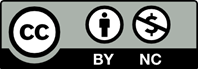
Hospital Pneumatic Systems, specializing in pneumatic systems, are among the most essential components for hospitals. It offers efficient and cost-effective solutions to problems related to the transportation of various materials in hospitals. However, in existing systems, the need for compressed air is met without worrying about cost control and without depending on the sample transported, and this not only makes the system inefficient but also may cause sample degradation. The main purpose of this study is to provide speed/pressure control according to the type of material transported to eliminate the disadvantages of existing systems such as energy use and sample degradation. In this study, a new mathematical model is presented that can be used to make more energy-efficient hospital pneumatic systems. Although there are many studies on various pneumatic systems in the literature, there is not enough for the control of hospital pneumatic systems. According to the results obtained in this study, the system parameters were determined and the mathematical model of the system was obtained by using the Multivariate nonlinear regression method. A genetic algorithm was used to test the validity of the obtained mathematical model and to optimize the coefficient of the input parameters of the model. It is expected that this proposed model will contribute to the use of hospital pneumatic systems and provide a scientific and practical solution to the proposed mathematical model. The proposed mathematical model provides up to %43 more efficient transportation over the currently used system that has been tested.
[1] Beater, P. (2007). Pneumatic Drives: System De- sign and Modelling. Springer-Verlag, Berlin.
[2] Wang, J., Pu, J. & Moore, P. (1999). A prac- tical control strategy for servo-pneumatic actua- tor systems. Control Engineering Practice, 7(12), 1483-1488.
[3] Chin, J. C. & Gray, J. S. (2015). Open-source con- ceptual sizing models for the hyperloop passenger pod. In 56th AIAA/ASCE/AHS/ASC Structures, Structural Dynamics, and Materials Conference, p. 15870.
[4] Chen, W. A., De Koster, R. B. & Gong, Y. (2021).Performance evaluation of automated medicine delivery systems. Transportation Research Part E: Logistics and Transportation Review, 147, 102242.
[5] Schl¨uter, M. S. & Perondi, E. A. (2018). Mathe- matical modeling of pneumatic semi-rotary actu- ator with friction. Journal of the Brazilian Society of Mechanical Sciences and Engineering, 40(11), 1-17.
[6] Kara, H., Bayir, A., Ak, A., Degirmenci, S., Akinci, M., Agacayak, A., & Azap, M. (2014). Hemolysis associated with pneumatic tube system transport for blood samples. Pakistan Journal of Medical Sciences, 30(1), 50.
[7] Farnsworth C. W., Webber D. M., Krekeler J.A, Budelier M. M., Bartlett N. L. & Gronowski A. M. (2019). Parameters for Validating a Hospi- tal Pneumatic Tube System. Clinical Chemistry. 65(5), 694–702.
[8] Abry, F., Brun, X., Sesmat, S.,& Bideaux, E.(2013). Non-linear position control of a pneumatic actuator with closed-loop stiffness and damping tuning. In 2013 European Control Conference (ECC), 1089-1094.
[9] Cukla, A. R. (2012). Arquitetura microcontro- lada program´avel aplicada ao controle de um ser- voposicionadorpneum´atico. Porto Alegre (in Por- tuguese).
[10] Mao, X. T., Yang, Q. J., Wu, J. J., & Bao, G. (2009). Control strategy for pneumatic ro- tary position servo systems based on feed forward compensation pole-placement self-tuning method. Journal of Central South University of Technol- ogy, 16(4), 608-613.
[11] Perondi E. A. (2002) Controle N˜ao-Linear em Cascata de um Servoposicionador Pneum´atico com Compensa¸c˜ao do Atrito. Thesis (PhD in Me- chanical Engineering), Technological Center, Fed- eral University of Santa Catarina, Florian´opoli (in Portuguese).
[12] Perondi, E. A. & Guenther, R. (2003). Mode- lagem de um servoposicionador pneum´atico com atrito. Science & Engineering. Uberlˆandia, 12(1), 43–52 (in Portuguese).
[13] Wamba, S. F., Anand, A., & Carter, L. (2013). A literature review of RFID-enabled healthcare applications and issues. International Journal of Information Management, 33(5), 875-891.
[14] Lee, J., Kim, B. I., Johnson, A. L., & Lee, K.(2014). The nuclear medicine production and de- livery problem. European Journal of Operational Research, 236(2), 461-472.
[15] Ruan, J. H., Wang, X. P., Chan, F. T. S., & Shi, Y. (2016). Optimizing the intermodal transporta- tion of emergency medical supplies using balanced fuzzy clustering. International Journal of Produc- tion Research, 54(14), 4368-4386.
[16] Abhinandu, K., Kumar, K. P., Srikanth, T., & Prashanth, B. N. (2019). Design and development of pneumatic drug delivery system. In IOP Con- ference Series: Materials Science and Engineer- ing, 577(1), 012128.
[17] Zhu, S. X., & Ursavas, E. (2018). Design and anal- ysis of a satellite network with direct delivery in the pharmaceutical industry. Transportation Re- search Part E: Logistics and Transportation Re- view, 116, 190-207.
[18] Campbell, A. M., & Jones, P. C. (2011). Preposi- tioning supplies in preparation for disasters. Eu- ropean Journal of Operational Research, 209(2), 156-165.
[19] Erbeyo˘glu, G., & Bilge, U(¨) . (2020). A robust disas-ter preparedness model for effective and fair dis- aster response. European Journal of Operational Research, 280(2), 479-494.
[20] Turkowski, M., & Szudarek, M. (2019). Pipeline system for transporting consumer goods, parcels and mail in capsules. Tunnelling and Underground Space Technology, 93, 103057.
[21] Pandian, S. R., Takemura, F., Hayakawa, Y., & Kawamura, S. (1999). Control performance of an air motor-can air motors replace electric motors. In Proceedings 1999 IEEE International Confer- ence on Robotics and Automation. 1, 518-524.
[22] Richer, E., & Hurmuzlu, Y. (2000). A high performance pneumatic force actuator system: Part I—Nonlinear mathematical model. Journal of Dynamic Systems: Measurement and Control, 122(3), 416-425.
[23] Ko¸cak, F. E., Y¨ontem, M., Y¨ucel, O(¨)., C¸ilo, M.,Gen¸c, O(¨)., & Meral, A. (2013). The effects of transport by pneumatic tube system on blood cell count, erythrocyte sedimentation and coagulation tests. Biochemia Medica, 23(2), 206-210.
[24] Isken, M. W., & Littig, S. J. (2002). Simulation analysis of pneumatic tube systems. Journal of Medical Systems, 26(1), 9-19.
[25] Mavaji, A. S., Kantipudi, S., & Somu, G.(2013). Innovative methods to improve hospital efficiency-study of pneumatic transport systems (Pts). IOSR Journal of Business and Manage- ment, 9(6), 10-15.
[26] Mills, D. (2003). Pneumatic Conveying Design Guide. Elsevier, London.
[27] Cakici, M., O˘guzhan, A. & O(¨)zdil, T. (2015). Is-tatistik, Ekin Basım Yayın Da˘gıtım, Bursa. (In Turkish).
[28] Swinscow, T. D. V., & Campbell, M. J. (2002). Statistics at Square One. Elsevier, London
[29] Fleischer, H. (1995). Manual of Pneumatic Systems Optimization. McGraw-Hill Companies, London.
[30] Wang, J., Wang, J. D., Daw, N., & Wu, Q. H. (2004). Identification of pneumatic cylin- der friction parameters using genetic algorithms. IEEE/ASME transactions on Mechatronics, 9(1), 100-107.
[31] Ratkowsky D. A. (1983). Nonlinear Regression Modeling. Marcel Dekker, New York.
[32] Kutner, M. H., Nachtsheim, C. J., Neter, J., & Wasserman, W. (2004). Applied linear regression models. 4, 563-568.
[33] Blum, W., & Ferri, R. B. (2009). Mathematical modelling: Can it be taught and learnt?. Journal of Mathematical Modelling and Application, 1(1), 45-58.
[34] Andersen, B. W., & Binder, R. C. (1967). The analysis and design of pneumatic systems. Jour- nal of Applied Mechanics, 34(4), 1055