Cellulose Nanocrystal-Enhanced Thermal-Sensitive Hydrogels of Block Copolymers for 3D Bioprinting
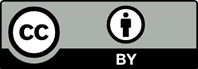
The hydrogel formed by polyethylene glycol-aliphatic polyester block copolymers is an ideal bioink and biomaterial ink for three-dimensional (3D) bioprinting because of its unique temperature sensitivity, mild gelation process, good biocompatibility, and biodegradability. However, the gel forming mechanism based only on hydrophilichydrophobic interaction renders the stability and mechanical strength of the formed hydrogels insufficient, and cannot meet the requirements of extrusion 3D printing. In this study, cellulose nanocrystals (CNC), which is a kind of rigid, hydrophilic, and biocompatible nanomaterial, were introduced to enhance the hydrogels so as to meet the requirements of extrusion 3D printing. First, a series of poly(ε-caprolactone/lactide)-b-poly(ethylene glycol)-b-poly(ε-caprolactone/ lactide) (PCLA-PEG-PCLA) triblock copolymers with different molecular weights were prepared. The thermodynamic and rheological properties of CNC-enhanced hydrogels were investigated. The results showed that the addition of CNC significantly improved the thermal stability and mechanical properties of the hydrogels, and within a certain range, the enhancement effect was directly proportional to the concentration of CNC. More importantly, the PCLA-PEG-PCLA hydrogels enhanced by CNC could be extruded and printed through temperature regulation. The printed objects had high resolution and fidelity with effectively maintained structure. Moreover, the hydrogels have good biocompatibility with a high cell viability. Therefore, this is a simple and effective strategy. The addition of the hydrophilic rigid nanoparticles such as CNC improves the mechanical properties of the soft hydrogels which made it able to meet the requirements of 3D bioprinting.
1. Ng WL, Chua CK, Shen YF, 2019, Print Me An Organ! Why We Are Not There Yet. Prog Polym Sci, 97:101145. https://doi.org/10.1016/j.progpolymsci.2019.101145
2. Matai I, Kaur G, Seyedsalehi A, et al., 2020, Progress in 3D Bioprinting Technology for Tissue/Organ Regenerative Engineering. Biomaterials, 226:119536. https://doi.org/10.1016/j.biomaterials.2019.119536
3. Murphy SV, Atala A, 2014, 3D Bioprinting of Tissues and Organs. Nat Biotechnol, 32:773–85. https://doi.org/10.1038/nbt.2958
4. Malda J, Visser J, Melchels FP, et al., 2013, 25th Anniversary Article: Engineering Hydrogels for Biofabrication. Adv Mater, 25:5011–28. https://doi.org/10.1002/adma.201302042
5. Bedell ML, Navara AM, Du Y, et al., 2020, Polymeric Systems for Bioprinting. Chem Rev, 120:10744–92.
6. Li X, Liu B, Pei B, et al., 2020, Inkjet Bioprinting of Biomaterials. Chem Rev, 120:10793–833.
7. Valot L, Martinez J, Mehdi A, et al., 2019, Chemical Insights Into Bioinks for 3D Printing. Chem Soc Rev, 48:4049–86. https://doi.org/10.1039/c7cs00718c
8. Zhang M, Vora A, Han W, et al., 2015, Dual-Responsive Hydrogels for Direct-Write 3D Printing. Macromolecules, 48:6482–8.
9. Hoffman AS, 2012, Hydrogels for Biomedical Applications. Adv Drug Deliv Rev, 64:18–23.
10. Sponchioni M, Palmiero UC, Moscatelli D, 2019, Thermo-Responsive Polymers: Applications of Smart Materials in Drug Delivery and Tissue Engineering. Mater Sci Eng C, 102:589–605. https://doi.org/10.1016/j.msec.2019.04.069
11. Jungst T, Smolan W, Schacht K, et al., 2016, Strategies and Molecular Design Criteria for 3D Printable Hydrogels. Chem Rev, 116:1496–539. https://doi.org/10.1021/acs.chemrev.5b00303
12. Nikolova MP, Chavali MS, 2019, Recent Advances in Biomaterials for 3D Scaffolds: A review. Bioact Mater, 4:271–92.
13. Zarrintaj P, Jouyandeh M, Ganjali MR, et al., 2019, Thermo-Sensitive Polymers in Medicine: A Review. Eur Polym J, 117:402–23.
14. Drzewiecki KE, Parmar AS, Gaudet ID, et al., 2014, Methacrylation Induces Rapid, Temperature-Dependent, Reversible Self-Assembly of Type-I Collagen. Langmuir, 30:11204–11. https://doi.org/10.1021/la502418s
15. Kajave NS, Schmitt T, Nguyen TU, et al., 2020, Dual Crosslinking Strategy to Generate Mechanically Viable Cell-Laden Printable Constructs using Methacrylated Collagen Bioinks. Mater Sci Eng C, 107:110290. https://doi.org/10.1016/j.msec.2019.110290
16. Cui Y, Jin R, Zhou Y, et al., 2021, Crystallization Enhanced Thermal-Sensitive Hydrogels of PCL-PEG-PCL Triblock Copolymer for 3D Printing. Biomed Mater, 16:035006. https://doi.org/10.1088/1748-605x/abc38e
17. Wang Z, An G, Zhu Y, et al., 2019, 3D-Printable Self-Healing and Mechanically Reinforced Hydrogels With Host-Guest Non-Covalent Interactions Integrated into Covalently Linked Networks. Mater Horiz, 6:733–42. https://doi.org/10.1039/c8mh01208c
18. Yue K, Trujillo-de Santiago G, Alvarez MM, et al., 2015, Synthesis, Properties, and Biomedical Applications of Gelatin Methacryloyl (GelMA) Hydrogels. Biomaterials, 73:254–71. https://doi.org/10.1016/j.biomaterials.2015.08.045
19. van den Bulcke AI, Bogdanov B, de Rooze N, et al., 2000, Structural and Rheological Properties of Methacrylamide Modified Gelatin Hydrogels. Biomacromolecules, 1:31–8. https://doi.org/10.1021/bm990017d
20. Heinrich MA, Bansal R, Lammers T, et al., 2019, 3D-Bioprinted Mini-Brain: A Glioblastoma Model to Study Cellular Interactions and Therapeutics. Adv Mater, 31:1806590. https://doi.org/10.1002/adma.201806590
21. Lim KS, Galarraga JH, Cui X, et al., 2020, Fundamentals and Applications of Photo-Cross-Linking in Bioprinting. Chem Rev, 120:10662–94.
22. Billiet T, Gevaert E, de Schryver T, et al., 2014, The 3D Printing of Gelatin Methacrylamide Cell-Laden Tissue-Engineered Constructs with High Cell Viability. Biomaterials, 35:49–62. https://doi.org/10.1016/j.biomaterials.2013.09.078
23. Colosi C, Shin SR, Manoharan V, et al., 2016, Microfluidic Bioprinting of Heterogeneous 3D Tissue Constructs Using Low-Viscosity Bioink. Adv Mater, 28:677–84. https://doi.org/10.1002/adma.201503310
24. Moon RJ, Martini A, Nairn J, et al., 2011, Cellulose Nanomaterials Review: Structure, Properties and Nanocomposites. Chem Soc Rev, 40:3941–94. https://doi.org/10.1039/c0cs00108b
25. Kargarzadeh H, Mariano M, Gopakumar D, et al., 2018, Advances in Cellulose Nanomaterials. Cellulose, 25:2151–89. https://doi.org/10.1007/s10570-018-1723-5
26. Kontturi E, Laaksonen P, Linder MB, et al., 2018, Advanced Materials through Assembly of Nanocelluloses. Adv Mater, 30:1703779. https://doi.org/10.1002/adma.201703779
27. Almeida AP, Canejo JP, Fernandes SN, et al., 2018, Cellulose-Based Biomimetics and Their Applications. Adv Mater, 30:1703655. https://doi.org/10.1002/adma.201703655
28. Yang J, Han CR, Duan JF, et al., 2012, Studies on the Properties and Formation Mechanism of Flexible Nanocomposite Hydrogels from Cellulose Nanocrystals and Poly (Acrylic Acid). J Mater Chem, 22:22467–80. https://doi.org/10.1039/c2jm35498e
29. Siqueira G, Kokkinis D, Libanori R, et al., 2017, Cellulose Nanocrystal Inks for 3D Printing of Textured Cellular Architectures. Adv Funct Mater, 27:1604619. https://doi.org/10.1002/adfm.201604619
30. Yang J, Han CR, Duan JF, et al., 2013, Mechanical and Viscoelastic Properties of Cellulose Nanocrystals Reinforced Poly (Ethylene Glycol) Nanocomposite Hydrogels. ACS Appl Mater Interfaces, 5:3199–207. https://doi.org/10.1021/am4001997
31. Ching YC, Ershad Ali M, Abdullah LC, et al., 2016, Rheological Properties of Cellulose Nanocrystal-Embedded Polymer Composites: A Review. Cellulose, 23:1011–30.
32. Ma T, Yang R, Zheng Z, et al., 2017, Rheology of Fumed Silica/Polydimethylsiloxane Suspensions. J Rheol, 61:205–15. https://doi.org/10.1122/1.4973974
33. Song Y, Zheng Q, 2015, Linear Rheology of Nanofilled Polymers. J Rheol, 59:155–91.
34. Song Y, Zheng Q, 2016, A Guide for Hydrodynamic Reinforcement Effect in Nanoparticle-Filled Polymers. Crit Rev Solid State Mater Sci, 41:318–46. https://doi.org/10.1080/10408436.2015.1135415
35. Song Y, Zheng Q, 2016, Concepts and Conflicts in Nanoparticles Reinforcement to Polymers Beyond Hydrodynamics. Prog Mater Sci, 84:1–58.
36. Fan X, Xu H, Zhang Q, et al., 2019, Insight into the Weak Strain Overshoot of Carbon Black Filled Natural Rubber. Polymer, 167:109–17. https://doi.org/10.1016/j.polymer.2019.01.076
37. Lu HD, Charati MB, Kim IL, et al., 2012, Injectable Shear-Thinning Hydrogels Engineered with a Self-Assembling Dock-and-Lock Mechanism. Biomaterials, 33:2145–53. https://doi.org/10.1016/j.biomaterials.2011.11.076
38. Wang Q, Mynar JL, Yoshida M, et al., 2010, High-Water-Content Mouldable Hydrogels by Mixing Clay and a Dendritic Molecular Binder. Nature, 463:339. https://doi.org/10.1038/nature08693
39. Olsen BD, Kornfield JA, Tirrell DA, 2010, Yielding Behavior in Injectable Hydrogels from Telechelic Proteins. Macromolecules, 43:9094–9. https://doi.org/10.1021/ma101434a
40. Zhang Z, Ni J, Chen L, et al., 2011, Biodegradable and Thermoreversible PCLA-PEG-PCLA Hydrogel as a Barrier for Prevention of Post-Operative Adhesion. Biomaterials, 32:4725–36. https://doi.org/10.1016/j.biomaterials.2011.03.046