Joint angle prediction for a cable-driven gripper with variable joint stiffness through numerical modeling and machine learning
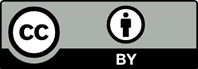
Soft grippers in automation, particularly those with variable joint stiffness, offer promising possibilities for precise manipulation tasks. However, accurately predicting finger joint bending angles in this field poses significant challenges due to the soft and complex nature of the grippers, making modeling and angle prediction difficult. This paper presents the development of a predictive model for precisely controlling bending angles in multi-material printed soft grippers with variable stiffness, which are pivotal for delicate manipulation tasks in automation. In particular, we explore a cable-driven gripper design made of thermoplastic polyurethane and conductive polylactic acid materials, featuring integrated resistive joints for stiffness modulation through controlled Joule heating. A data-driven modeling approach, combining numerical modeling of the gripper and machine learning techniques, was employed for the development of the predictive model. We performed static structural simulations using ANSYS Workbench to measure bending angles under various conditions for developing datasets for model training. In this work, we evaluated several machine learning models such as linear regression, decision tree, and K-nearest neighbor regression models to predict the correlation between temperature, pull distance, and bending angle. The K-nearest neighbor regression model demonstrated the highest accuracy, with a mean absolute error of approximately 11%. These findings underline the importance of precise angle prediction models in enhancing the functionality and reliability of soft grippers, paving the way for their broader application in automation and robotics.
- Shintake J, Cacucciolo V, Floreano D, Shea H. Soft robotic grippers. Adv Mater. 2018;30(29):1707035. doi: 10.1002/adma.201707035
- Walker J, Zidek T, Harbel C, et al. Soft robotics: A review of recent developments of pneumatic soft actuators. Actuators, 2020;9:3. doi: 10.3390/act9010003
- Tawk C, Alici G. A review of 3D‐printable soft pneumatic actuators and sensors: Research challenges and opportunities. Adv Intell Syst. 2021;3(6):2000223. doi: 10.1002/aisy.202000223
- Ruth DJS, Sohn JW, Dhanalakshmi K, Choi SB. Control aspects of shape memory alloys in robotics applications: A review over the last decade. Sensors (Basel). 2022;22(13):4860. doi: 10.3390/s22134860
- Rodrigue H, Wang W, Kim DR, Ahn SH. Curved shape memory alloy-based soft actuators and application to soft gripper. Compos. Struct. 2017;176:398-406. doi: 10.1016/j.compstruct.2017.05.056
- Bar-Cohen Y, Anderson IA. Electroactive polymer (EAP) actuators-background review. Mech Soft Mater. 2019;1(1):5. doi: 10.1007/s42558-019-0005-1
- Peng CJ, Seurre L, Cattan É, et al. Toward an electroactive polymer-based soft microgripper. IEEE Access. 2021;9:32188- 32195. doi: 10.1109/ACCESS.2021.3059926
- Su H, Hou X, Zhang X, et al. Pneumatic soft robots: Challenges and benefits. Actuators. 2022;11:92. doi: 10.3390/act11030092
- Nguyen VP, Dhyan SB, Han BS, Chow WT. Universally grasping objects with granular-tendon finger: Principle and design. Micromachines (Basel). 2023;14(7):1471. doi: 10.3390/mi14071471
- Slesarenko V, Engelkemier S, Galich PI, Vladimirsky D, Klein G, Rudykh S. Strategies to control performance of 3d-printed, cable-driven soft polymer actuators: From simple architectures to gripper prototype. Polymers. 2018;10(8):846. doi: 10.3390/polym10080846
- Tang D, Cheng C, Xiao L, et al. A review on wire-driven flexible robot manipulators. Recent Pat Eng. 2023;17(3):37-57. doi: 10.2174/1872212117666220623140652
- Nguyen VP, Dhyan SB, Mai V, Han BS, Chow WT. Bioinspiration and biomimetic art in robotic grippers. Micromachines (Basel). 2023;14(9):1772. doi: 10.3390/mi14091772
- Goh GL, Liang GG, Nguyen VP, et al. A 3D printing-enabled artificially innervated smart soft gripper with variable joint stiffness. Adv Mater Technol. 2023;8(24):2301426. doi: 10.1002/admt.202301426
- Goh GD, Goh GL, Lyu Z, et al. 3D printing of robotic soft grippers: Toward smart actuation and sensing. Adv Mater Technol. 2022;7(11):2101672. doi: 10.1002/admt.202101672
- Stork JA, Ek CH, Bekiroglu Y, Kragic D. Learning Predictive State Representation for In-Hand Manipulation. United States, IEEE, 2015, p3207-3214. doi: 10.1109/ICRA.2015.7139641
- Hassan A, Abomoharam M. Modeling and design optimization of a robot gripper mechanism. Robot Comput Integr Manuf. 2017;46:94-103. doi: 10.1016/j.rcim.2016.12.012
- Kuresangsai P, Cole MO, Hao G. Grasp stability and design analysis of a flexure-jointed gripper mechanism via efficient energy-based modeling. IEEE Robot Autom Lett. 2022;7(4):12499-12506. doi: 10.1109/LRA.2022.3220152
- Hussain I, Renda F, Iqbal Z, et al. Modeling and prototyping of an underactuated gripper exploiting joint compliance and modularity. IEEE Robot Autom Lett. 2018;3(4):2854-2861. doi: 10.1109/LRA.2018.2845906
- Yang Y, Chen Y. 3D Printing of Smart Materials for Robotics with Variable Stiffness and Position Feedback. United States, IEEE, 2017, p418-423. doi: 10.1109/AIM.2017.8014053
- Jiao J, Guo Y, Tong Q, et al. Stiffness-tunable and shape-locking soft actuators based on 3D-printed hybrid multi-materials. Soft Sci. 2022;2(4):20. doi: 10.20517/ss.2022.19
- Al-Rubaiai M, Pinto T, Qian C, Tan X. Soft actuators with stiffness and shape modulation using 3D-printed conductive polylactic acid material. Soft Robot. 2019;6(3):318-332. doi: 10.1089/soro.2018.0056
- Yeong WY, Goh GL, Goh GD, et al. 3D printing of soft grippers with multimaterial design: Towards shape conformance and tunable rigidity. Mater Today Proceed. 2022;70:525-530. doi: 10.1016/j.matpr.2022.09.552
- Goh GD, Lee JM, Goh GL, Huang X, Lee S, Yeong WY. Machine learning for bioelectronics on wearable and implantable devices: Challenges and potential. Tissue Eng Part A. 2023;29(1-2):20-46. doi: 10.1089/ten.tea.2022.0119
- Goh GL, Zhang H, Goh GD, Yeong WY, Chong TH. Multi-objective optimization of intense pulsed light sintering process for aerosol jet printed thin film. MSAM. 2022;1(2):10. doi: 10.18063/msam.v1i2.10
- Goh GL, Goh GD, Pan JW, Teng PSP, Kong PW. Automated service height fault detection using computer vision and machine learning for badminton matches. Sensors (Basel). 2023;23(24):9759. doi: 10.3390/s23249759
- Zhang H, Cao R, Zilberstein S, Wu F, Chen X. Toward Effective Soft Robot Control Via Reinforcement Learning. Germany, Springer, 2017, p173-184. doi: 10.1007/978-3-319-65289-4_17
- Kim D, Kim SH, Kim T, et al. Review of machine learning methods in soft robotics. PLoS One. 2021;16(2):e0246102. doi: 10.1371/journal.pone.0246102
- Chin K, Hellebrekers T, Majidi C. Machine learning for soft robotic sensing and control. Adv Intell Syst. 2020;2(6):1900171. doi: 10.1002/aisy.201900171
- Zhou C, Guo H, Li J, et al. Temperature dependence of poly (lactic acid) mechanical properties. RSC Adv. 2016;6(114):113762-113772. doi: 10.1039/C6RA23610C
- Al-Rubaiai M, Pinto T, González DT, Sepulveda N, Tan X. Characterization of a 3d-Printed Conductive Pla Material with Electrically Controlled Stiffness. New York, American Society of Mechanical Engineers, 2017, pV001T01A003. doi: 10.1115/SMASIS2017-3801