Porosity and density measurement of additively manufactured components: A comparative analysis of measurement methods across processes and materials
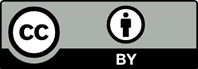
Part density and part porosity are important parameters for additively manufactured (AM) components, as they significantly influence mechanical properties and indicate printing process’s quality. Various measurement methods are available such as gas pycnometry, gravimetric density measurements (Archimedes’ principle), and micrograph analyses. This study compared these methods by analyzing test specimens made from different materials using diverse AM processes. AM components made of metal, ceramic, and plastic as well as composites were analyzed with regard to part density and porosity. The results provided new findings on part density and porosity in AM processes and materials. Furthermore, they demonstrated the suitability of the employed measurement methods for certain purposes. In this context, it is always important to distinguish between the determination of true and apparent density. Gas pycnometry is best suited for determining the true density and enables the most accurate density measurement. Gravimetric measurement according to Archimedes’ principle is generally best suited for determining the apparent density, which is more relevant for characterizing the technical properties of AM components. Micrograph analyses are the only investigated method that shows the position of the pores in the component. However, the method generally only allows statements to be made in the sectional plane under consideration. In addition, gas pycnometry is preferable for very dense AM components and the Archimedes method for porous parts. Finally, the results can be generalized and recommendations for measuring porosity and density can be concluded for other AM processes.

- Deutsches Institut für Normung, DIN EN ISO/ASTM 52900:2022-03, DIN Media GmbH, Berlin, 2022. doi: 10.31030/3290011
- Westphal E. Digital Quality Assurance System for Additive Manufacturing Based on Machine Learning Methods and Blockchain Technology. Dissertation, University of Rostock, 2023. doi: 10.18453/ROSDOK_ID00004605
- Wong KV, Hernandez A. A review of additive manufacturing. ISRN Mech Eng. 2012;2012:1-10. doi: 10.5402/2012/208760
- Thompson Y, Gonzalez-Gutierrez J, Kukla C, Felfer P. Fused filament fabrication, debinding and sintering as a low cost additive manufacturing method of 316L stainless steel. Addit Manuf. 2019;30:100861. doi: 10.1016/j.addma.2019.100861
- Mitteramskogler G, Gmeiner R, Felzmann R, et al. Light curing strategies for lithography-based additive manufacturing of customized ceramics. Addit Manuf. 2014;1-4:110-118. doi: 10.1016/j.addma.2014.08.003
- Spierings AB, Schneider M, Eggenberger R. Comparison of density measurement techniques for additive manufactured metallic parts. Rapid Prototyp J. 2011;17(5):380-386. doi: 10.1108/13552541111156504
- Slotwinski JA, Garboczi EJ, Hebenstreit KM. Porosity measurements and analysis for metal additive manufacturing process control. J Res Natl Inst Stand Technol. 2014;119:494-528. doi: 10.6028/jres.119.019
- Flodberg G, Pettersson H, Yang L. Pore analysis and mechanical performance of selective laser sintered objects. Addit Manuf. 2018;24:307-315. doi: 10.1016/j.addma.2018.10.001
- Bland S, Aboulkhair NT. Reducing porosity in additive manufacturing. Met Powder Rep. 2015;70(2):79-81. doi: 10.1016/j.mprp.2015.01.002
- Kruth JP, Levy G, Klocke F, Childs TH. Consolidation phenomena in laser and powder-bed based layered manufacturing. CIRP Ann. 2007;56(2):730-759. doi: 10.1016/j.cirp.2007.10.004
- Guddati S, Kiran ASK, Leavy M, Ramakrishna S. Recent advancements in additive manufacturing technologies for porous material applications. Int J Adv Manuf Technol. 2019;105(1-4):193-215. doi: 10.1007/s00170-019-04116-z
- Al-Maharma AY, Patil SP, Markert B. Effects of porosity on the mechanical properties of additively manufactured components: A critical review. Mater Res Express. 2020;7(12):122001. doi: 10.1088/2053-1591/abcc5d
- American Society for Testing and Materials, ASTM B276-21 - Standard Test Method for Apparent Porosity in Cemented Carbides, ASTM International, West Conshohocken, Pennsylvania, USA, 2023. doi: 10.1520/B0276-21
- Buffière JY, Savelli S, Jouneau PH, Maire E, Fougères R. Experimental study of porosity and its relation to fatigue mechanisms of model Al-Si7-Mg0.3 cast Al alloys. Mater Sci Eng. 2001;316(1-2):115-126. doi: 10.1016/S0921-5093(01)01225-4
- Damon J, Dietrich S, Vollert F, Gibmeier J, Schulze V. Process dependent porosity and the influence of shot peening on porosity morphology regarding selective laser melted AlSi10Mg parts. Addit Manuf. 2018;20:77-89. doi: 10.1016/j.addma.2018.01.001
- Heinl P, Müller L, Körner C, Singer RF, Müller FA. Cellular Ti-6Al-4V structures with interconnected macro porosity for bone implants fabricated by selective electron beam melting. Acta Biomater. 2008;4(5):1536-1544. doi: 10.1016/j.actbio.2008.03.013
- Wits WW, Carmignato S, Zanini F, Vaneker TH. Porosity testing methods for the quality assessment of selective laser melted parts. CIRP Ann. 2016;65(1):201-204. doi: 10.1016/j.cirp.2016.04.054
- Otto R, Kiener C, Küsters Y, Sørby K. Additive manufacturing of open porous functional structures: Roadmap from manufacturing to the application. Procedia CIRP. 2022;112:334-339. doi: 10.1016/j.procir.2022.09.102
- Deutsches Institut für Normung, DIN ISO 15901-1:2019-03, DIN Media GmbH, Berlin, 2019. doi: 10.31030/3031674
- Klobes P, Munro RG. Porosity and Specific Surface Area Measurements for Solid Materials; 2006. Available from: https://www.nist.gov/publications/porosity-and-specific-surface-area-measurements-solid-materials [Last accessed on 2025 Mar 20].
- Arvieu C, Galy C, Le Guen E, Lacoste E. Relative density of SLM-produced aluminum alloy parts: Interpretation of results. J Manuf Mater Process. 2020;4(3):83. doi: 10.3390/jmmp4030083
- Dupin S, Lame O, Barrès C, Charmeau JY. Microstructural origin of physical and mechanical properties of polyamide 12 processed by laser sintering. Eur Polym J. 2012;48(9):1611- 1621. doi: 10.1016/j.eurpolymj.2012.06.007
- Damon J, Dietrich S, Gorantla S, Popp U, Okolo B, Schulze V. Process porosity and mechanical performance of fused filament fabricated 316L stainless steel. Rapid Prototyp J. 2019;25(7):1319-1327. doi: 10.1108/RPJ-01-2019-0002
- Gong H, Snelling D, Kardel K, Carrano A. Comparison of stainless steel 316L parts made by FDM- and SLM-based additive manufacturing processes. JOM. 2019;71(3):880- 885. doi: 10.1007/s11837-018-3207-3
- Caminero MÁ, Romero A, Chacón JM, Núñez PJ, García- Plaza E, Rodríguez GP. Additive manufacturing of 316L stainless-steel structures using fused filament fabrication technology: Mechanical and geometric properties. Rapid Prototyp J. 2021;27(3):583-591. doi: 10.1108/RPJ-06-2020-0120
- Galarraga H, Lados DA, Dehoff RR, Kirka MM, Nandwana P. Effects of the microstructure and porosity on properties of Ti-6Al-4V ELI alloy fabricated by electron beam melting (EBM). Addit Manuf. 2016;10:47-57. doi: 10.1016/j.addma.2016.02.003
- Scharowsky T, Juechter V, Singer RF, Körner C. Influence of the scanning strategy on the microstructure and mechanical properties in selective electron beam melting of Ti-6Al-4V. Adv Eng Mater. 2015;17(11):1573-1578. doi: 10.1002/adem.201400542
- Homa J, Schwentenwein M. A novel additive manufacturing technology for high-performance ceramics. In: Advanced Processing and Manufacturing Technologies for Nanostructured and Multifunctional Materials. United States: John Wiley; 2014. p. 33-40. doi: 10.1002/9781119040354.ch4
- Llanos G. Additive Manufacturing of Zirconia: Chalmers University of Technology; 2018. Available from: https://odr. chalmers.se/handle/20.500.12380/255513 [Last accessed on 2025 Mar 20].
- Suominen JM, Frankberg EJ, Vallittu PK, et al. Three-dimensional printing of zirconia: Characterization of early stage material properties. Biomater Invest Dent. 2019;6(1):23-31. doi: 10.1080/26415275.2019.1640608
- Pellegrini A, Palmieri ME, Guerra MG. Evaluation of anisotropic mechanical behaviour of 316L parts realized by metal fused filament fabrication using digital image correlation. Int J Adv Manuf Technol. 2022;120(11-12):7951- 7965. doi: 10.1007/s00170-022-09303-z
- O’Connor H, Singh G, Kumar A, Paetzold R, Celikin M, O’Cearbhaill ED. Fused filament fabrication using stainless steel 316L‐polymer blend: Analysis and optimization for green density and surface roughness. Polym Composites. 2024;45(12):10632-10644. doi: 10.1002/pc.28496
- Reddy PK, Gandhi P, Singh G. Additive manufacturing of yttria-stabilized zirconia using digital light processing: Green density and surface roughness analysis. Ceram Int. 2024;50(13):22974-22988. doi: 10.1016/j.ceramint.2024.04.021
- Forward AM. Technologies GmbH. Ultrafuse® 316L: Stainless Steel Composite Metal Filament for 3D Printers. Available from: https://forward-am.com/material-portfolio/ultrafuse-filaments-for-fused-filaments-fabrication-fff/metal-filaments/ultrafuse-316l [Last accessed on 2024 Sep 04].
- Lithoz GmbH. Thermal Post Processing - LithaCon 3Y 230. V2; TPP201.209. Unpublished thermal post processing data sheet, 2020.
- Lithoz GmbH. Technical Data Sheet: LithaCon 3Y 230 D. Unpublished technical data sheet, 2019.
- Hughes S, Quintero Olaya S. Using pycnometry and Archimedes’ principle to measure the gross and air cavity volume of fruit. IOP SciNotes. 2021;2(2):25201. doi: 10.1088/2633-1357/abf33f
- De Terris T, Andreau O, Peyre P, et al. Optimization and comparison of porosity rate measurement methods of selective laser melted metallic parts. Addit Manuf. 2019;28:802-813. doi: 10.1016/j.addma.2019.05.035
- Kurose T, Abe Y, Santos MVA, et al. Influence of the layer directions on the properties of 316L stainless steel parts fabricated through fused deposition of metals. Materials (Basel). 2020;13(11):2493. doi: 10.3390/ma13112493
- Caminero MÁ, Romero Gutiérrez A, Chacón JM, García- Plaza E, Núñez PJ. Effects of fused filament fabrication parameters on the manufacturing of 316L stainless-steel components: Geometric and mechanical properties. Rapid Prototyp J. 2022;28(10):2004-2026. doi: 10.1108/RPJ-01-2022-0023
- Rosnitschek T, Seefeldt A, Alber-Laukant B, Neumeyer T, Altstädt V, Tremmel S. Correlations of geometry and infill degree of extrusion additively manufactured 316L stainless steel components. Materials (Basel). 2021;14(18):5173. doi: 10.3390/ma14185173
- BASF 3D Printing Solutions GmbH. Ultrafuse® Metal Filaments: User Guidelines for 3D Printing Metal Parts. Available from: https://forward-am.com/material-portfolio/ ultrafuse-filaments-for-fused-filaments-fabrication-fff/metal-filaments/ultrafuse-316l [Last accessed on 2023 Apr 27].
- MBF Bioscience. Glossary: Stereology Terms Stereology Information Center. Available from: https://www.stereology. info/glossary-terms [Last accessed on 2023 Apr 27].
- Carazzone JR, Martin CL, Cordero ZC. Crack initiation, propagation, and arrest in sintering powder aggregates. J Am Ceram Soc. 2020;103(9):4754-4773. doi: 10.1111/jace.17170