Multi-material structures of Ti6Al4V and Ti6Al4V-B4C through directed energy deposition-based additive manufacturing
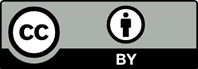
The demand for advanced materials has driven innovation in titanium alloy design, particularly in the aerospace, automotive, and biomedical sectors. Additive manufacturing (AM) enables the construction of multi-material structures, offering potential improvements in mechanical properties such as wear resistance and high-temperature capabilities, thus extending the service life of components such as Ti6Al4V. Directed energy deposition (DED)-based metal AM was used to manufacture radial multi-material structures with a Ti6Al4V (Ti64) core and a Ti6Al4V-5 wt.% B4C composite outer layer. X-ray diffraction analysis and microstructural observation suggest that distinct B4C particles are strongly attached to the Ti6Al4V matrix. The addition of B4C increased the average hardness from 313 HV for Ti6Al4V to 538 HV for the composites. The addition of 5 wt.% B4C in Ti6Al4V increased the average compressive yield strength (YS) to 1440 MPa from 972 MPa for the control Ti6Al4V, i.e., >48% increase without any significant change in the elastic modulus. The radial multi-material structures did not exhibit any changes in the compressive modulus compared to Ti6Al4V but displayed an increase in the average compressive YS to 1422 MPa, i.e., >45% higher compared to Ti6Al4V. Microstructural characterization revealed a smooth transition from the pure Ti6Al4V at the core to the Ti64-B4C composite outer layer. No interfacial failure was observed during compressive deformation, indicating a strong metallurgical bonding during multi-material radial composite processing. Our results demonstrated that a significant improvement in mechanical properties can be achieved in one AM build operation through designing innovative multi-material structures using DED-based AM.
- Pollock TM. Alloy design for aircraft engines. Nat Mater. 2016;15(8):809-815. doi: 10.1038/nmat4709
- Bandyopadhyay A, Traxel KD, Lang M, Juhasz M, Eliaz N, Bose S. Alloy design via additive manufacturing: Advantages, challenges, applications and perspectives. Mater Today. 2022;52:207-224. doi: 10.1016/J.MATTOD.2021.11.026
- Guo S, Li Y, Gu J, et al. Microstructure and mechanical properties of Ti6Al4V/B4C titanium matrix composite fabricated by selective laser melting (SLM). J Mater Res Technol. 2023;23:1934-1946. doi: 10.1016/j.jmrt.2023.01.126
- Peters M, Kumpfert J, Ward CH, Leyens C. Titanium alloys for aerospace applications. Adv Eng Mater. 2003;5(6): 419-427. doi: 10.1002/adem.200310095
- Zhang T, Liu CT. Design of titanium alloys by additive manufacturing: A critical review. Adv Powder Mater. 2022;1(1):100014. doi: 10.1016/j.apmate.2021.11.001
- Traxel KD, Bandyopadhyay A. Designing high-temperature oxidation-resistant titanium matrix composites via directed energy deposition-based additive manufacturing. Mater Des. 2021;212:110205. doi: 10.1016/j.matdes.2021.110205
- Boyer RR, Briggs RD. The use of β titanium alloys in the aerospace industry. J Mater Eng Perform. 2005;14:681-685. doi: 10.1361/105994905X75448
- Rack HJ, Qazi JI. Titanium alloys for biomedical applications. Mater Sci Eng C. 2006;26(8):1269-1277. doi: 10.1016/J.MSEC.2005.08.032
- Bandyopadhyay A, Dash A, Squires L, et al. Wire-arc directed energy deposition of monolithic and bimetallic structures of maraging 250 steel. Virtual Phys Prototyp. 2024;19(1):e2296127. doi: 10.1080/17452759.2023.2296127
- Anil Kumar V, Gupta RK, Prasad MJ, Narayana Murty SV. Recent advances in processing of titanium alloys and titanium aluminides for space applications: A review. J Mater Res. 2021;36(3):689-716. doi: 10.1557/s43578-021-00104-w
- Dash A, Bandyopadhyay A. 17-4 PH and SS316L bimetallic structures via additive manufacturing. Virtual Phys Prototyp. 2024;19(1):e2292695. doi: 10.1080/17452759.2023.2292695
- Squires L, Roberts E, Bandyopadhyay A. Radial bimetallic structures via wire arc directed energy deposition-based additive manufacturing. Nat Commun. 2023;14(1):3544. doi: 10.1038/s41467-023-39230-w
- Monisha K, Shariff SM, Raju R, Manonmani J, Jayaraman S. Titanium boride and titanium silicide phase formation by high power diode laser alloying of B4C and SiC particles with Ti: Microstructure, hardness and wear studies. Mater Today Commun. 2022;31103741. doi: 10.1016/j.mtcomm.2022.103741
- Traxel KD, Bandyopadhyay A. Selective laser melting of Ti6Al4V-B4C-BN in situ reactive composites. J Mater Res Technol. 2022;18:2654-2671. doi: 10.1016/j.jmrt.2022.03.092
- Han C, Babicheva R, Chua JD, et al. Microstructure and mechanical properties of (TiB+TiC)/Ti composites fabricated in situ via selective laser melting of Ti and B4C powders. Addit Manuf. 2020;36:101466. doi: 10.1016/j.addma.2020.101466
- Fereiduni E, Ghasemi A, Elbestawi M, Dinkar Jadhav S, Vanmeensel K. Laser powder bed fusion processability of Ti-6Al-4V powder decorated by B4C particles. Mater Lett. 2021;296:129923. doi: 10.1016/j.matlet.2021.129923
- Avila JD, Bandyopadhyay A. Niobium carbide reinforced- Ti6Al4V composites via directed energy deposition. Int J Appl Ceram Technol. 2022;19(2):1061-1073. doi: 10.1111/ijac.13907
- Pereira T, Kennedy JV, Potgieter J. A comparison of traditional manufacturing vs additive manufacturing, the best method for the job. In: Procedia Manufacturing. Vol 30. Netherlands: Elsevier; 2019. p. 11-18. doi: 10.1016/j.promfg.2019.02.003
- Su J, Jiang F, Tan C, et al. Additive manufacturing of fine-grained high-strength titanium alloy via multi-eutectoid elements alloying. Compos B Eng. 2023;249:110399. doi: 10.1016/J.COMPOSITESB.2022.110399
- Luu DN, Zhou W, Nai SM. Influence of Y2O3 reinforcement particles during heat treatment of IN718 composite produced by laser powder bed fusion. Mater Sci Addit Manuf. 2022;1(4):25. doi: 10.18063/msam.v1i4.25
- ASTM. Standard Test Methods of Compression Testing of Metallic Materials at Room Temperature. United States: ASTM; 2019. doi: 10.1520/E0009-19
- Narayana PL, Kim SW, Hong JK, Reddy NS, Yeom JT. Tensile properties of a newly developed high-temperature titanium alloy at room temperature and 650°C. Mater Sci Eng A. 2018;718:287-291. doi: 10.1016/j.msea.2018.01.113
- Dai J, Zhu J, Chen C, Weng F. High temperature oxidation behavior and research status of modifications on improving high temperature oxidation resistance of titanium alloys and titanium aluminides: A review. J Alloys Compd. 2016;685:784-798. doi: 10.1016/j.jallcom.2016.06.212
- Al-Maharma AY, Patil SP, Markert B. Effects of porosity on the mechanical properties of additively manufactured components: A critical review. Mater Res Express. 2020;7(12):122001. doi: 10.1088/2053-1591/abcc5d
- Toptan F, Rego A, Alves AC, Guedes A. Corrosion and tribocorrosion behavior of Ti-B4C composite intended for orthopaedic implants. J Mech Behav Biomed Mater. 2016;61:152-163. doi: 10.1016/J.JMBBM.2016.01.024
- Chen C, Feng X, Shen Y. Synthesis of Al-B4C composite coating on Ti-6Al-4V alloy substrate by mechanical alloying method. Surf Coat Technol. 2017;321:8-18. doi: 10.1016/J.SURFCOAT.2017.04.042
- Tijo D, Masanta M. Effect of Ti/B4C ratio on the microstructure and mechanical characteristics of TIG cladded TiC-TiB2 coating on Ti-6Al-4V alloy. J Mater Process Technol. 2019;266:184-197. doi: 10.1016/J.JMATPROTEC.2018.11.005
- Bandyopadhyay A, Ciliveri S, Guariento S, Zuckschwerdt N, Hogg WW. Fatigue behavior of additively manufactured Ti3Al2V alloy. Mater Sci Addit Manufact. 2023;2(3):1705. doi: 10.36922/msam.1705