Increasing density and mechanical performance of binder jetting processing through bimodal particle size distribution
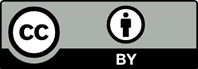
Binder jetting is an additive manufacturing (AM) technology that has gained popularity and attention in recent years for production applications in tooling, biomedical, energy, and defense sectors. When compared to other powder bed fusion-based AM methods, binder jetting processes powder feedstock without the need of an energy source during printing. This avoids defects associated with melting, residual stresses, and rapid solidification within the parts. However, one of the challenges of this process is the relatively lower densities which impacts part density, and subsequently, sintering and mechanical properties. In this study, we investigated the influence of bimodal powder size distributions (a mixture of coarse to fine particles) as a method for increasing part density and mechanical strength, and used stainless steel (SS) 316L bimodal mixtures in this case. Four unimodal and two bimodal groups were evaluated under similar AM processing conditions for sintered density measurements and flexural strengths. Our results demonstrated that bimodal size distributions showed a statistically significant increase in density by 20% and ultimate flexural strength by 170% when compared to the highest performing unimodal group. In addition to experimental findings, reactive molecular dynamics simulations showed that the presence of finer powders along with coarser particles in the bimodal particle mixture contribute to additional bonds that are stronger across the particle interfaces. Findings from this study can be used to design bimodal particle size distributions to achieve higher density and better mechanical properties in binder jetting AM process.
Guha Manogharan serves as the Editorial Board Member of the journal, but did not in any way involve in the editorial and peer-review process conducted for this paper, directly or indirectly.
Mirzababaei S, Pasebani S, 2019, A review on binder jet additive manufacturing of 316L stainless steel. J Manuf Mater Process, 3: 82. https://doi.org/10.3390/JMMP3030082
Bai Y, Williams C, 2015, An exploration of binder jetting of copper. Rapid Prototyp J, 21: 177–185. https://doi.org/10.1108/RPJ-12-2014-0180
Liravi F, Vlasea M, 2018, Powder bed binder jetting additive manufacturing of silicone structures. Addit Manuf, 21: 112–124. https://doi.org/10.1016/j.addma.2018.02.017
Sama SR, Badamo T, Manogharan G, 2020, Case studies on integrating 3D sand-printing technology into the production portfolio of a sand-casting foundry. Int J Met, 14: 12–24. https://doi.org/10.1007/s40962-019-00340-1
Mariani M, Beltrami R, Brusa P, et al., 2021, 3D printing of fine alumina powders by binder jetting. J Eur Ceram Soc, 41: 5307–5315. https://doi.org/10.1016/j.jeurceramsoc.2021.04.006
Cramer CL, Aguirre TG, Wieber NR, et al., 2020, Binder jet printed WC infiltrated with pre-made melt of WC and Co. Int J Refract Met Hard Mater, 87: 105137. https://doi.org/10.1016/j.ijrmhm.2019.105137
Manogharan G, Kioko M, Linkous C, 2015, Binder jetting: A novel solid oxide fuel-cell fabrication process and evaluation. JOM, 67: 660–667. https://doi.org/10.1007/s11837-015-1296-9
Ke D, Bose S, 2018, Effects of pore distribution and chemistry on physical, mechanical, and biological properties of tricalcium phosphate scaffolds by binder-jet 3D printing. Addit Manuf, 22: 111–117. https://doi.org/10.1016/j.addma.2018.04.020
Martinez D, Bate C, Manogharan GP, 2020, Towards functionally graded sand molds for metal casting: Engineering thermo-mechanical properties using 3D sand printing. JOM, 72: 1340–1354. https://doi.org/10.1007/s11837-019-03975-x
Xia M, Sanjayan J, 2016, Method of formulating geopolymer for 3D printing for construction applications. Mater Des, 110: 382–390. https://doi.org/10.1016/j.matdes.2016.07.136
Rojas-Nastrucci EA, Nussbaum JT, Crane NB, et al., 2017, Ka-band characterization of binder jetting for 3-D printing of metallic rectangular waveguide circuits and antennas. IEEE Trans Microw Theory Tech, 65: 3099–3108. https://doi.org/10.1109/TMTT.2017.2730839
Lecis N, Mariani M, Beltrami R, et al., 2021, Effects of process parameters, debinding and sintering on the microstructure of 316L stainless steel produced by binder jetting. Mater Sci Eng A, 828: 142108.https://doi.org/10.1016/J.MSEA.2021.142108
Li M, Du W, Elwany A, et al., 2019, Binder Jetting Additive Manufacturing of Metals: A Literature Review. Vol. 1. In: ASME 2019 14th International Manufacturing Science and Engineering Conference. https://doi.org/10.1115/MSEC2019-2994
Bai Y, Wagner G, Williams CB, 2015, Effect of bimodal powder mixture on powder packing density and sintered density in binder jetting of metals: In Annual International Solid Freeform Fabrication Symposium (2015), 62.
Li M, Du W, Elwany A, et al., 2020, Metal binder jetting additive manufacturing: A literature review. J Manuf Sci Eng Trans ASME, 142: 090801. https://doi.org/10.1115/1.4047430/1084395
Gibson I, Rosen D, Stucker B, et al., 2020, Binder jetting. In: Additive Manufacturing Technologies., Champaign: Springer International Publishing. p237–252.
Ziaee M, Tridas EM, Crane NB, 2017, Binder-jet printing of fine stainless steel powder with varied final density. JOM, 69: 592–596. https://doi.org/10.1007/s11837-016-2177-6
Meenashisundaram GK, Xu Z, Nai ML, et al., 2020, Binder jetting additive manufacturing of high porosity 316L stainless steel metal foams. Materials, 13: 3744. https://doi.org/10.3390/MA13173744
Vogt J, Friedrich H, Stepanyan M, et al., 2021, Improved green and sintered density of alumina parts fabricated by binder jetting and subsequent slurry infiltration. Prog Addit Manuf, 7: 161–171. https://doi.org/10.1007/S40964-021-00222-1
Porter Q, Pei Z, Ma C, 2022, Binder jetting and infiltration of metal matrix nanocomposites. J Manuf Sci Eng, 144: 074502. https://doi.org/10.1115/1.4053156
Kumar AY, Bai Y, Eklund A, et al., 2018, The effects of hot isostatic pressing on parts fabricated by binder jetting additive manufacturing. Addit Manuf, 24: 115–124. https://doi.org/10.1016/J.ADDMA.2018.09.021
Kumar A, Bai Y, Eklund A, et al., 2017, Effects of hot isostatic pressing on copper parts fabricated via binder jetting. Procedia Manuf, 10: 935–944. https://doi.org/10.1016/J.PROMFG.2017.07.084
Dahmen T, Henriksen NG, Dahl KV, et al., 2021, Densification, microstructure, and mechanical properties of heat-treated MAR-M247 fabricated by binder jetting. Addit Manuf, 39: 101912. https://doi.org/10.1016/J.ADDMA.2021.101912
Shrestha S, Manogharan G, 2017, Optimization of binder jetting using taguchi method. JOM, 69: 491–497. https://doi.org/10.1007/s11837-016-2231-4
Du W, Singh M, Singh D, 2020, Binder jetting additive manufacturing of silicon carbide ceramics: Development of bimodal powder feedstocks by modeling and experimental methods. Ceram Int, 46: 19701–19707. https://doi.org/10.1016/j.ceramint.2020.04.098
Du W, Ren X, Chen Y, et al., 2018, Model Guided Mixing of Ceramic Powders with Graded Particle Sizes in Binder Jetting Additive Manufacturing. Vol. 1. In: ASME 2018 13th International Manufacturing Science and Engineering Conference. p9. https://doi.org/10.1115/MSEC2018-6651
Du W, Roa J, Hong J, et al., 2021, Binder jetting additive manufacturing: Effect of particle size distribution on density. J Manuf Sci Eng, 143: 091002. https://doi.org/10.1115/1.4050306
Clares AP, Manogharan G, (2021), Discrete-element Simulation of Powder Spreading Process in Binder Jetting, and the Effects of Powder Size. In: ASME 2021 16th International Manufacturing Science and Engineering Conference.
Standard, ASTM, 2012, ISO/ASTM 52900: 2015 Additive manufacturing-General principles-terminology. ASTM F2792-10e1.
Bai Y, Wagner G, Williams CB, 2017, Effect of particle size distribution on powder packing and sintering in binder jetting additive manufacturing of metals. J Manuf Sci Eng Trans ASME, 139: 081019. https://doi.org/10.1115/1.4036640
Chen H, Zhao YF, 2016, Process parameters optimization for improving surface quality and manufacturing accuracy of binder jetting additive manufacturing process. Rapid Prototyp J, 22: 527–538. https://doi.org/10.1108/RPJ-11-2014-0149/FULL/PDF
Utela B, Storti D, Anderson R, et al., 2008, A review of process development steps for new material systems in three dimensional printing (3DP). J Manuf Process, 10: 96–104. https://doi.org/10.1016/J.JMAPRO.2009.03.002
Mostafaei A, Elliott AM, Barnes JE, et al., 2020, Binder jet 3D printing-Process parameters, materials, properties, and challenges. Prog Mater Sci, 119: 100707. https://doi.org/10.1016/j.pmatsci.2020.100707
Gao Y, Clares AP, Manogharan G, et al., 2022, A reactive molecular dynamics study of bi-modal particle size distribution in binder-jetting additive manufacturing using stainless-steel powders. Phys Chem Chem Phys, 24: 11603–11615. https://doi.org/10.1039/D2CP00630H.
Miyanaji H, Momenzadeh N, Yang L, 2019, Effect of powder characteristics on parts fabricated via binder jetting process. Rapid Prototyp J, 25: 332–342. https://doi.org/10.1108/RPJ-03-2018-0069/FULL/PDF
Verlee B, Dormal T, Lecomte-Beckers J, 2013, Density and porosity control of sintered 316L stainless steel parts produced by additive manufacturing. Powder Metallurgy, 55: 260–267. https://doi.org/10.1179/0032589912Z.00000000082
Miao G, Du W, Moghadasi M, et al., 2020, Ceramic binder jetting additive manufacturing: Effects of granulation on properties of feedstock powder and printed and sintered parts. Addit Manuf, 36: 101542. https://doi.org/10.1016/j.addma.2020.101542
Ji CH, Loh NH, Khor KA, et al., 2001, Sintering study of 316L stainless steel metal injection molding parts using Taguchi method: Final density. Mater Sci Eng A, 311: 74–82. https://doi.org/10.1016/S0921-5093(01)00942-X
Sridhar TM, Mudali UK, Subbaiyan M, 2003, Sintering atmosphere and temperature effects on hydroxyapatite coated type 316L stainless steel. Corros Sci, 45: 2337–2359. https://doi.org/10.1016/S0010-938X(03)00063-5
Jost EW, Miers JC, Robbins A, et al., 2021, Effects of spatial energy distribution-induced porosity on mechanical properties of laser powder bed fusion 316L stainless steel. Addit Manuf, 39: 101875. https://doi.org/10.1016/J.ADDMA.2021.101875
Masuo H, Tanaka Y, Morokoshi S, et al., 2017, Effects of defects, surface roughness and HIP on fatigue strength of Ti-6Al-4V manufactured by additive manufacturing. Procedia Struct Integr, 7: 19–26. https://doi.org/10.1016/J.PROSTR.2017.11.055
Du W, Ren X, Pei Z, et al., 2020, Ceramic binder jetting additive manufacturing: a literature review on density. J Manuf Sci Eng, 142: 040801. https://doi.org/10.1115/1.4046248