Multi-objective optimization of intense pulsed light sintering process for aerosol jet printed thin film
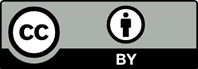
The sintering of printed nanoparticle films is a necessary processing step for most nanoparticle inks to make the printed film functional. The sintering of nanoparticle is usually performed through thermal sintering, photonic sintering, induction sintering, etc. Intense pulsed light (IPL) sintering method is one of the most popular sintering methods for nanoparticle inks due to the fast and effective process, but it may yield mediocre performance if improper sintering parameters are used. In this work, we investigate the correlation between the two factors which are the print passes of aerosol jet printing and the sintering distance of the samples on the effect of the surface morphology and sheet resistance. A contradictory correlation between the two factors was observed and a multi-objective optimization was carried out using machine learning method to identify the most optimum conditions for both factors. We found that multi-objective optimization approach is effective in reducing the conflicting responses, thus the sintered thin film can have low sheet resistance and low surface roughness. This work provides an essential guide for achieving conductive films with electrical conductivity and low surface roughness using IPL sintering process for fast fabrication of multi-layered electronics such as electrochemical electrodes.
Wai Yee Yeong serves as the Editorial Board Member of the journal, but did not in any way involve in the editorial and peer-review process conducted for this paper, directly or indirectly.
Tan H, Tran T, Chua C, 2016, A review of printed passive electronic components through fully additive manufacturing methods. Virtual Phys Prototyp, 11: 271–288. https://doi.org/10.1080/17452759.2016.1217586
Saengchairat N, Tran T, Chua CK, 2017, A review: Additive manufacturing for active electronic components. Virtual Phys Prototyp, 12: 31–46. https://doi.org/10.1080/17452759.2016.1253181
Fisher G, Seacrist MR, Standley RW, 2012, Silicon crystal growth and wafer technologies. Proc IEEE, 100: 1454–1474. https://doi.org/10.1109/jproc.2012.2189786
Tan HW, An J, Chua CK, et al., 2019, Metallic nanoparticle inks for 3D printing of electronics. Adv Electron Mater, 5: 1800831. https://doi.org/10.1002/aelm.201800831
Saidina D, Eawwiboonthanakit N, Mariatti M, et al., 2019, Recent development of graphene-based ink and other conductive material-based inks for flexible electronics. J Electron Mater, 48: 3428–3450. https://doi.org/10.1007/s11664-019-07183-w
Yang W, List-Kratochvil EJ, Wang C, 2019, Metal particle-free inks for printed flexible electronics. J Mater Chem C, 7: 15098–15117. https://doi.org/10.1039/c9tc05463d
Bhat KS, Ahmad R, Wang Y, et al., 2016, Low-temperature sintering of highly conductive silver ink for flexible electronics. J Mater Chem C, 4: 8522–8527. https://doi.org/10.1039/c6tc02751b
Xu Z, Dong Q, Qtieno B, et al., 2016, Real-time in situ sensing of multiple water quality related parameters using micro-electrode array (MEA) fabricated by inkjet-printing technology (IPT). Sens Actuators B Chem, 237: 1108–1119. https://doi.org/10.1016/j.snb.2016.09.040
Zhang H, Moon SK, Ngo TH, 2020, 3D printed electronics of non-contact ink writing techniques: status and promise. Int J Precis Eng Manuf Green Technol, 7: 511–524. https://doi.org/10.1007/s40684-019-00139-9
Goh GL, Zhang H, Chong TH, et al., 2021, 3D printing of multilayered and multimaterial electronics: A review. Adv Electron Mater, 7: 2100445. https://doi.org/10.1002/aelm.202100445
Goh GL, Ma J, Chua KL, et al., 2016, Inkjet-printed patch antenna emitter for wireless communication application. Virtual Phys Prototyp, 11: 289–294. https://doi.org/10.1080/17452759.2016.1229802
Goh GL, Shweta A, Yeong WY, 2018, High resolution aerosol jet printing of conductive ink for stretchable electronics. In: Proceedings of the 3rd International Conference on Progress in Additive Manufacturing (PRO-AM). Nanyang Technological University, Singapore, p109–114.
Agarwala S, Goh GL, Yeong WY, 2018, Aerosol jet printed pH sensor based on carbon nanotubes for flexible electronics. In: Proceedings of the 3rd International Conference on Progress in Additive Manufacturing (Pro-AM 2018), Singapore.
Goh GL, Agarwala S, Yeong WY, 2018, High resolution aerosol jet printing of conductive ink for stretchable electronics. In: Proceedings of the 3rd International Conference on Progress in Additive Manufacturing (Pro-AM 2018), Singapore.
Goh GL, Dikshit V, Koneru R, et al., 2022, Fabrication of design-optimized multifunctional safety cage with conformal circuits for drone using hybrid 3D printing technology. Int J Adv Manuf Technol, 120: 2573–2586. https://doi.org/10.1007/s00170-022-08831-y
Jiang P, Ji Z, Zhang X, et al., 2018, Recent advances in direct ink writing of electronic components and functional devices. Prog Addit Manuf, 3: 65–86. https://doi.org/10.1007/s40964-017-0035-x
Wilkinson N, Smith M, Kay R, et al., 2019, A review of aerosol jet printing a non-traditional hybrid process for micro-manufacturing. Int J Adv Manuf Technol, 105: 4599–4619. https://doi.org/10.1007/s00170-019-03438-2
Zeng M, Kuang W, Khan I, et al., 2020, Colloidal nanosurfactants for 3D conformal printing of 2D van der waals materials. Adv Mater, 32: 2003081. https://doi.org/10.1002/adma.202003081
Aleeva Y, Pignataro B, 2014, Recent advances in upscalable wet methods and ink formulations for printed electronics. J Mater Chem C, 2: 6436–6453. https://doi.org/10.1039/c4tc00618f
Hoeng F, Denneulin A, Bras J, 2016, Use of nanocellulose in printed electronics: A review. Nanoscale, 8: 13131–13154. https://doi.org/10.1039/c6nr03054h
Goh GL, Tay MF, Lee JM, et al., 2021, Potential of printed electrodes for electrochemical impedance spectroscopy (EIS): Toward membrane fouling detection. Adv Electron Mater, 7: 2100043. https://doi.org/10.1002/aelm.202100043
Jiang J, Bao B, Li M, et al., 2016, Fabrication of transparent multilayer circuits by inkjet printing. Adv Mater, 28: 1420–1426. https://doi.org/10.1002/adma.201503682
Agarwala S, Goh GL, Le TS, et al., 2018, Wearable bandage-based strain sensor for home healthcare: Combining 3D aerosol jet printing and laser sintering. ACS Sensors, 4: 218–226. https://doi.org/10.1021/acssensors.8b01293
Pan H, Ko SH, Grigoropoulos CP, 2008, Thermal sintering of solution-deposited nanoparticle silver ink films characterized by spectroscopic ellipsometry. Appl Phys Lett, 93: 234104. https://doi.org/10.1063/1.3043583
Allen ML, Aronniemi M, Mattila T, et al., 2008, Electrical sintering of nanoparticle structures. Nanotechnology, 19: 175201. https://doi.org/10.1088/0957-4484/19/17/175201
Tan HW, Saengchairat N, Goh GL, et al., 2020, Induction sintering of silver nanoparticle inks on polyimide substrates. Adv Mater Technol, 5: 1900897. https://doi.org/10.1002/admt.201900897
Nam HJ, Kang SY, Park JY, et al., 2019, Intense pulse light sintering of an Ag microparticle-based, highly stretchable, and conductive electrode. Microelectron Eng, 215: 111012. https://doi.org/10.1016/j.mee.2019.111012
Jang YR, Joo SJ, Chu JH, et al., 2020, A review on intense pulsed light sintering technologies for conductive electrodes in printed electronics. Int J Precis Eng Manuf Green Technol, 8: 327–363. https://doi.org/10.1007/s40684-020-00193-8
Moores A, Goettmann F, 2006, The plasmon band in noble metal nanoparticles: an introduction to theory and applications, New J Chem, 30: 1121–1132. https://doi.org/10.1039/b604038c
Kelly KL, Coronado E, Zhao LL, et al., 2003, The optical properties of metal nanoparticles: The influence of size, shape, and dielectric environment. J Phys Chem B, 107: 668–677. https://doi.org/10.1021/jp026731y
Zhang JZ, Noguez C, 2008, Plasmonic optical properties and applications of metal nanostructures. Plasmonics, 3: 127–150. https://doi.org/10.1007/s11468-008-9066-y
Lee DJ, Park SH, Jang S, et al., 2011, Pulsed light sintering characteristics of inkjet-printed nanosilver films on a polymer substrate. J Micromech Microeng, 21: 125023.https://doi.org/10.1088/0960-1317/21/12/125023
Moon CJ, Kim I, Joo SJ, et al., 2017, Flash light sintering of ag mesh films for printed transparent conducting electrode. Thin Solid Films, 629: 60–68. https://doi.org/10.1016/j.tsf.2017.03.049
Kang J, Ryu J, Kim H, et al., 2011, Sintering of inkjet-printed silver nanoparticles at room temperature using intense pulsed light. J Electron Mater, 40: 2268–2277. https://doi.org/10.1007/s11664-011-1711-0
Niittynen J, Abbel R, Mäntysalo M, et al., 2014, Alternative sintering methods compared to conventional thermal sintering for inkjet printed silver nanoparticle ink. Thin Solid Films, 556: 452–459. https://doi.org/10.1016/j.tsf.2014.02.001
Hösel M, Krebs FC, 2012, Large-scale roll-to-roll photonic sintering of flexo printed silver nanoparticle electrodes. J Mater Chem, 22: 15683–15688. https://doi.org/10.1039/c2jm32977h
Chung WH, Hwang HJ, Lee SH, et al., 2012, In situ monitoring of a flash light sintering process using silver nano-ink for producing flexible electronics. Nanotechnology, 24: 035202. https://doi.org/10.1088/0957-4484/24/3/035202
Yung KC, Gu X, Lee C, et al., 2010, Ink-jet printing and camera flash sintering of silver tracks on different substrates, J Mater Process Technol, 210: 2268–2272. https://doi.org/10.1016/j.jmatprotec.2010.08.014
Tobjörk D, Aarnio H, Pulkkinen P, et al., 2012, IR-sintering of ink-jet printed metal-nanoparticles on paper. Thin Solid Films, 520: 2949–2955. https://doi.org/10.1016/j.jmatprotec.2010.08.014
Goh GL, Agarwala S, Yeong WY, 2019, Aerosol-jet-printed preferentially aligned carbon nanotube twin-lines for printed electronics, ACS Appl Mater Interfaces, 11: 43719–43730. https://doi.org/10.1021/acsami.9b15060
Keyence. Surface Roughness Parameters. Keyence. Available from: https://www.keyence.com/ss/products/ microscope/roughness/line/parameters.jsp [Last accessed on 2021 Dec 20].
Zhang H, Choi JP, Moon SK, et al., 2020, A hybrid multi-objective optimization of aerosol jet printing process via response surface methodology., Addit Manuf, 33: 101096. https://doi.org/10.1016/j.addma.2020.101096
Srinivas M, Patnaik LM, 1994, Genetic algorithms: A survey. Computer, 27: 17–26.
Chen JH, Ho SY, 2005, A novel approach to production planning of flexible manufacturing systems using an efficient multi-objective genetic algorithm. Int J Mach Tools Manuf, 45: 949–957. https://doi.org/10.1016/j.ijmachtools.2004.10.010
Saravanan R, Asokan P, Sachidanandam M, 2002, A multi-objective genetic algorithm (GA) approach for optimization of surface grinding operations. Int J Mach Tools Manuf, 42: 1327–1334. https://doi.org/10.1016/s0890-6955(02)00074-3
Jain NK, Jain V, Deb K, 2007, Optimization of process parameters of mechanical type advanced machining processes using genetic algorithms. Int J Mach Tools Manuf, 47: 900–919. https://doi.org/10.1016/j.ijmachtools.2006.08.001
Deb K, Pratap A, Agarwal S, et al., 2002, A fast and elitist multiobjective genetic algorithm: NSGA-II. IEEE Trans Evol Comput, 6: 182–197. https://doi.org/10.1109/4235.996017
Srinivas N, Deb K, 1994, Muiltiobjective optimization using nondominated sorting in genetic algorithms. Evol Comput, 2: 221–248. https://doi.org/10.1162/evco.1994.2.3.221
Frey BJ, Dueck D, 2007, Clustering by passing messages between data points. Science, 315: 972–976. https://doi.org/10.1126/science.1136800