Additive manufacturing: A machine learning model of process-structure-property linkages for machining behavior of Ti-6Al-4V
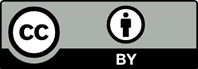
Prior studies in metal additive manufacturing (AM) of parts have shown that various AM methods and post-AM heat treatment result in distinctly different microstructure and machining behavior when compared with conventionally manufactured parts. There is a crucial knowledge gap in understanding this process-structure-property (PSP) linkage and its relationship to material behavior. In this study, the machinability of metallic Ti-6Al-4V AM parts was investigated to better understand this unique PSP linkage through a novel data science-based approach, specifically by developing and validating a new machine learning (ML) model for material characterization and material property, that is, machining behavior. Heterogeneous material structures of Ti-6Al-4V AM samples fabricated through laser powder bed fusion and electron beam powder bed fusion in two different build orientations and post-AM heat treatments were quantitatively characterized using scanning electron microscopy, electron backscattered diffraction, and residual stress measured through X-ray diffraction. The reduced dimensional representation of material characterization data through chord length distribution (CLD) functions, 2-point correlation functions, and principal component analysis was found to be accurate in quantifying the complexities of Ti-6Al-4V AM structures. Specific cutting energy was the response variable for the Taguchi-based experimentation using force dynamometer. A low-dimensional S-P linkage model was established to correlate material structures of metallic AM and machining properties through this novel ML model. It was found that the prediction accuracy of this new PSP linkage is extremely high (>99%, statistically significant at 95% confidence interval). Findings from this study can be seamlessly integrated with P-S models to identify AM processing conditions that will lead to desired material behaviors, such as machining behavior (this study), fatigue behavior, and corrosion resistance.
Frazier WE, 2014, Metal additive manufacturing: A review. J Mater Eng Perform, 23: 1917–1928. https://doi.org/10.1007/s11665-014-0958-z
Trelewicz JR, Halada GP, Donaldson OK, et al., 2016, Microstructure and corrosion resistance of laser additively manufactured 316L stainless steel. JOM, 68: 850–859.
Bostanabad R, Bui AT, Xie W, et al., 2016, Stochastic microstructure characterization and reconstruction via supervised learning. Acta Mater, 103: 89–102. https://doi.org/10.1016/j.actamat.2015.09.044
Kalidindi SR, 2015, Data science and cyberinfrastructure: Critical enablers for accelerated development of hierarchical materials. Int Mater Rev, 60: 150–168. https://doi.org/10.1179/1743280414Y.0000000043
Popova E, Rodgers TM, Gong X, et al., 2017, Process-structure linkages using a data science approach: Application to simulated additive manufacturing data. Integr Mater Manuf Innov, 6: 54–68. https://doi.org/10.1007/s40192-017-0088-1
Greitemeier D, Donne CD, Schoberth A, et al., 2015, Uncertainty of additive manufactured Ti-6Al-4V: Chemistry, microstructure and mechanical properties. Appl Mech Mater, 807: 169–180. https://doi.org/10.4028/www.scientific.net/amm.807.169
Markl M, Körner C, 2016, Multiscale modeling of powder bed-based additive manufacturing. Annu Rev Mater Res, 46: 93–123. https://doi.org/10.1146/annurev-matsci-070115-032158
Li J, Zhou X, Brochu M, et al., 2020, Solidification microstructure simulation of Ti-6Al-4V in metal additive manufacturing: A review. Addit Manuf, 31: 100989. https://doi.org/10.1016/j.addma.2019.100989
Liu S, Shin YC, 2019, Additive manufacturing of Ti6Al4V alloy: A review. Mater Des, 164: 107552. https://doi.org/10.1016/j.matdes.2018.107552
Corson PB, 1974, Correlation functions for predicting properties of heterogeneous materials. I. Experimental measurement of spatial correlation functions in multiphase solids. J Appl Phys, 45: 3159–3164. https://doi.org/10.1063/1.1663741
Lu B, Torquato S, 1992, Lineal-path function for random heterogeneous materials. Phys Rev A, 45: 922–929. https://doi.org/10.1103/PhysRevA.45.922
Gan Z, Li H, Wolff SJ, et al., 2019, Data-driven microstructure and microhardness design in additive manufacturing using a self-organizing map. Engineering, 5: 730–735. https://doi.org/10.1016/j.eng.2019.03.014
Thijs L, Verhaeghe F, Craeghs T, et al., 2010, A study of the microstructural evolution during selective laser melting of Ti-6Al-4V. Acta Mater, 58: 3303–3312. https://doi.org/10.1016/j.actamat.2010.02.004
Li GC, Li J, Tian XJ, et al., 2017, Microstructure and properties of a novel titanium alloy Ti-6Al-2V-1.5Mo- 0.5Zr-0.3Si manufactured by laser additive manufacturing. Mater Sci Eng A, 684: 233–238. https://doi.org/10.1016/j.msea.2016.11.084
Paulson NH, Priddy MW, McDowell DL, et al., 2019, Reduced-order microstructure-sensitive protocols to rank-order the transition fatigue resistance of polycrystalline microstructures. Int J Fatigue, 119: 1–10. https://doi.org/10.1016/j.ijfatigue.2018.09.011
Fernandez-Zelaia P, Nguyen V, Zhang H, et al., 2019, The effects of material anisotropy on secondary processing of additively manufactured CoCrMo. Addit Manuf, 29: 100764. https://doi.org/10.1016/j.addma.2019.06.015
Yang Z, Yabansu YC, Al-Bahrani R, et al., 2018, Deep learning approaches for mining structure-property linkages in high contrast composites from simulation datasets. Comput Mater Sci, 151: 278–287. https://doi.org/10.1016/j.commatsci.2018.05.014
Manogharan G, Wysk R, Harrysson O, et al., 2015, AIMS-a metal additive-hybrid manufacturing system: System architecture and attributes. Proc Manuf, 1: 273–286.
Zhang W, Qin P, Wang Z, et al., 2019, Superior wear resistance in EBM-Processed TC4 alloy compared with SLM and forged samples. Materials (Basel), 12: 2–13. https://doi.org/10.3390/ma12050782
Edwards P, Ramulu M, 2014, Fatigue performance evaluation of selective laser melted Ti-6Al-4V. Mater Sci Eng A, 598: 327–337. https://doi.org/10.1016/j.msea.2014.01.041
Matouš K, Geers MG, Kouznetsova VG, et al., 2017, A review of predictive nonlinear theories for multiscale modeling of heterogeneous materials. J Comput Phys, 330: 192–220. https://doi.org/10.1016/j.jcp.2016.10.070
Breiman L, 2001, Random forests. Mach Learn, 45: 5–32. https://doi.org/10.1007/978-3-662-56776-0_10
Gong X, Manogharan G, 2020, Machining behavior and material properties in additive manufacturing Ti-6Al-4V parts. International Manufacturing Science and Engineering Conference, Vol. 84256, p. V001T01A055. https://doi.org/10.1115/MSEC2020-8487
Ren S, Chen Y, Liu T, et al., 2019, Effect of build orientation on mechanical properties and microstructure of Ti-6Al-4V manufactured by selective laser melting. Metall Mater Trans A Phys Metall Mater Sci, 50: 4388–4409. https://doi.org/10.1007/s11661-019-05322-w
Goh GD, Sing SL, Yeong WY, 2021, A review on machine learning in 3D printing: Applications, potential, and challenges. Artif Intell Rev, 54: 63–94.
Nasiri S, Khosravani MR, 2021, Machine learning in predicting mechanical behavior of additively manufactured parts. J Mater Res Technol, 14: 1137–1153.
Sing SL, Kuo CN, Shih CT, et al., 2021, Perspectives of using machine learning in laser powder bed fusion for metal additive manufacturing. Virtual Phys Prototyp, 16: 372–386.
Chen T, Guestrin C, 2016, XGBoost: A Scalable Tree Boosting System. KDD’16, August 13-17, San Francisco, CA, USA.
Przybyla CP, Mcdowell DL, 2012, Microstructure-sensitive extreme-value probabilities of high-cycle fatigue for surface vs. subsurface crack formation in duplex Ti-6Al-4V. Acta Mater, 60: 293–305. https://doi.org/10.1016/j.actamat.2011.09.031
Turner DM, Niezgoda SR, Kalidindi SR, 2016, Efficient computation of the angularly resolved chord length distributions and lineal path functions in large microstructure datasets. Model Simul Mater Sci Eng, 24: 075002. https://doi.org/10.1088/0965-0393/24/7/075002
Paulson NH, Priddy MW, McDowell DL, et al., 2018, Data-driven reduced-order models for rank-ordering the high cycle fatigue performance of polycrystalline microstructures. Mater Des, 154: 170–183. https://doi.org/10.1016/j.matdes.2018.05.009
Hansen M, 1958, Constitution of Alloys. McGraw-Hill Company Inc., New York. p678.
Telrandhe SV, Saxena AK, Mishra S, 2017, Effect of microstructure and cutting speed on machining behavior of Ti6Al4V alloy. J Mech Sci Technol, 31: 2177–2184. https://doi.org/10.1007/s12206-017-0413-9
Luo Q, Yang S, 2017, Uncertainty of the X-ray diffraction (XRD) sin2 ¬ technique in measuring residual stresses of physical vapor deposition (pvd) hard coatings. Coatings, 7: 128. https://doi.org/10.3390/coatings7080128
Demir E, Mercan C, 2018, A physics-based single crystal plasticity model for crystal orientation and length scale dependence of machining response. Int J Mach Tools Manuf, 134: 25–41. https://doi.org/10.1016/j.ijmachtools.2018.06.004
Huang ZW, Jin SB, Zhou H, et al., 2018, Evolution of twinning systems and variants during sequential twinning in cryo-rolled titanium. Int J Plast, 112: 52–67. https://doi.org/10.1016/j.ijplas.2018.08.008
Hémery S, Villechaise P, 2018, Investigation of size effects in slip strength of titanium alloys: α nodule size dependence of the critical resolved shear stress. Metall Mater Trans A Phys Metall Mater Sci, 49: 4394–4397. https://doi.org/10.1007/s11661-018-4678-0
Demir E, 2008, Taylor-based model for micro-machining of single crystal FCC materials including frictional effects- Application to micro-milling process. Int J Mach Tools Manuf, 48: 1592–1598. https://doi.org/10.1016/j.ijmachtools.2008.07.002
Kline WA, DeVor RE, 1993, The effect of runout on cutting geometry and forces in end milling. Int J Mach Tool Des Res, 23: 123–140. https://doi.org/10.1016/0020-7357(83)90012-4
Priddy MW, Paulson NH, Kalidindi SR, et al., 2017, Strategies for rapid parametric assessment of microstructure-sensitive fatigue for HCP polycrystals. Int J Fatigue, 104: 231–242. https://doi.org/10.1016/j.ijfatigue.2017.07.015
Demir E, 2009, A Taylor-based plasticity model for orthogonal machining of single-crystal FCC materials including frictional effects. Int J Adv Manuf Technol, 40: 847–856. https://doi.org/10.1007/s00170-008-1409-5
Zhang D, Qian L, Mao B, et al., 2018, A data-driven design for fault detection of wind turbines using random forests and XGboost. IEEE Access, 6: 21020–21031. https://doi.org/10.1109/ACCESS.2018.281867
Dhaliwal SS, Al Nahid A, Abbas R, 2018, Effective intrusion detection system using XGBoost. Information, 9: 149. https://doi.org/10.3390/info9070149