Design, simulation, and experiments for direct thixotropic metal 3D printing
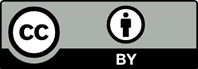
Compared with current powder-based 3D metal printing, thixotropic metal 3D printing has great potentials and advantages in equipment cost, product quality, and process efficiency. In this paper, detailed problem statement, technique challenge, and development method regarding thixotropic metal 3D printing are discussed. A shear mixing and extruding prototype machine for thixotropic alloy fabrication was designed. We developed a direct thixotropic metal 3D printing machine and conducted a modeling and simulation process for the system. The printability of this direct metal 3D printing machine was studied. At the end, conclusions and future directions are also presented.
Hong DH, Chou DT, Velikokhatnyi OI, et al., 2016, Binder-jetting 3D printing and alloy development of new biodegradable Fe-Mn-Ca/Mg alloys. Acta Biomater, 45: 375–386.
International Organization for Standardization, 2015, Additive Manufacturing General Principles Terminology. ISO/ASTM 52900, Geneva, Switzerland.
Roh S, Parekh DP, Bharti B, et al., 2017, 3D printing by multiphase silicone/water capillary inks. Adv Mater, 29: 1701554.
Goh GD, Yeong WY, 2018, Mode I Interlaminar Fracture Toughness of Additively Manufactured Carbon Fibre Thermoplastic. In: Proceedings of the 3rd International Conference on Progress in Additive Manufacturing, p505–510.
Zhou LY, Fu J, He Y, 2020, A review of 3D printing technologies for soft polymer materials. Adv Funct Mater, 30: 2000187.
Yu YZ, Liu FJ, Zhang RC, et al., 2017, Suspension 3D printing of liquid metal into self-healing hydrogel. Adv Mater Technol Us, 2: 1700173.
Ladd C, So JH, Muth J, et al., 2013, 3D printing of free standing liquid metal microstructures. Adv Mater, 25: 5081–5085.
Hashmi S, 2014, Comprehensive Materials Processing, Newnes.
Gao W, Zhang YB, Ramanujan D, et al., 2015, The status, challenges, and future of additive manufacturing in engineering. Comput Aided Design, 69: 65–89.
McKinley GH, Renardy M, 2011, Wolfgang von ohnesorge. Phys Fluids, 23:127101. https://doi.org/10.1063/1.3663616
Derby B, 2010, Inkjet printing of functional and structural materials: fluid property requirements, feature stability, and resolution. Annu Rev Mater Res, 40: 395–414.
Joshipura ID, Ayers HR, Majidi C, et al., 2015, Methods to pattern liquid metals. J Mater Chem C, 3: 3834–3841.
Kirkwood DH, Atkinson HV, Young KP, et al., 2010, SpringerLink (Online service), Semi-solid Processing of Alloys. Springer-Verlag Berlin Heidelberg, Berlin, Heidelberg.
Mohammed MN, Omar MZ, Salleh MS, et al., 2014, An overview of semi-solid metal processing. Aust J Basic Appl Sci, 8: 369–373.
Husain NH, Ahmad AH, Rashidi MM, 2017, An Overview of Thixoforming Process. IOP Conference Materials Science and Engineering.
Suh Y, Son G, 2008, A level-set method for simulation of a thermal inkjet process. Numer Heat Transf B Fundam, 54: 138–156.
Simlandi S, Barman N, Chattaopadhyay H, 2016, Behaviour of semisolid slurry flows through a channel. Solid State Phenomena, 256: 146–152. https://doi.org/10.4028/www.scientific.net/SSP.256.146
Koeune R, Ponthot JP, 2014, A one phase thermomechanical model for the numerical simulation of semi-solid material behavior. Application to thixoforming. Int J Plast, 58: 120–153. https://doi.org/10.1016/j.ijplas.2014.01.004
Dickey MD, Chiechi RC, Larsen RJ, et al., 2008, Whitesides, Eutectic gallium‐indium (EGaIn): A liquid metal alloy for the formation of stable structures in microchannels at room temperature. Adv Funct Mater, 18: 1097–1104.
Tabatabai A, Fassler A, Usiak C, et al., 2013, Liquid-phase gallium-indium alloy electronics with microcontact printing. Langmuir, 29: 6194–6200.
Boley JW, White EL, Chiu GT, et al., 2014, Direct writing of galliumwitdium alloy for stretchable electronics. Adv Funct Mater, 24: 3501–3507. https://doi.org/10.1002/adfm.201303220
Yin XY, Collins GS, 2012, The solubility of indium in liquid gallium supercooled to 12 K. Defect Diffus Forum, 323–325: 503–508.
Rugg BC, Chart TG, 1990, A critical-assessment of thermodynamic and phase-diagram data for the gallium-indium system. Calphad, 14: 115–123.
White CE, Okamoto H, 1992, Phase Diagrams of Indium Alloys and their Engineering Applications. ASM International, Metals Park, Ohio.