Modeling and experimental investigation of fiber orientation in cast and 3D-printed cementitious composites
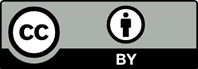
Fiber orientation is process-related and has significant impacts on material performance. However, existing studies only consider the impact of individual factors on the fiber orientation, either boundary impacts or flow field impacts. This work aims to study fiber orientation by considering the combined impact of these two factors. Analytical models were first constructed, which revealed that when the flow of material is negligible, fiber orientation is impacted by the boundary conditions. When the flow field is non-negligible, fiber orientation is affected by the direction of flow streamlines. Specimens were then prepared using fluorescence image processing and μ-computed tomography scanning for fiber orientation analysis. The results indicate that fiber orientation could be controlled by varying boundary constraints and flow fields. Mechanical results reveal that when the designed condition achieves directional-orientated fibers, the mechanical property of specimens could be enhanced with the applied stress direction being the same as the fiber orientation. This work provides a novel insight to tailor fiber-reinforced cementitious material properties by designing the boundary constraints and flow fields in the cast and printing processes.
- Weng Y, Li M, Tan MJ, et al., 2018, 3D Printable High Performance Fiber Reinforced Cementitious Composites for Large-scale Printing. In: Proceedings of the 3rd International Conference on Progress in Additive Manufacturing (Pro-AM 2018). p. 19–24. https://doi.org/10.25341/D4B591
- Wu HC, Li VC, 1992, Snubbing and bundling effects on multiple crack spacing of discontinuous random fiber-reinforced brittle matrix composites. J Am Ceram Soc, 75: 3487–3489. https://doi.org/10.1111/j.1151-2916.1992.tb04457.x
- Kanda T, Li VC, 1998, Interface property and apparent strength of high-strength hydrophilic fiber in cement matrix. J Mater Civ Eng, 10: 5–13. https://doi.org/10.1061/(ASCE)0899-1561(1998)10:1(5)
- Kaufmann J, Frech K, Schuetz P, et al., 2013, Rebound and orientation of fibers in wet sprayed concrete applications. Constr Build Mater, 49: 15–22. https://doi.org/10.1016/j.conbuildmat.2013.07.051
- Segura-Castillo L, Cavalaro SH, Goodier C, et al., 2018, Fibre distribution and tensile response anisotropy in sprayed fibre reinforced concrete. Mater Struct, 51: 29. https://doi.org/10.1617/s11527-018-1156-5
- Shao Y, Qiu J, Shah SP, 2001, Microstructure of extruded cement-bonded fiberboard. Cem Concr Res, 31: 1153–1161. https://doi.org/10.1016/S0008-8846(01)00535-X
- Stähli P, Custer R, van Mier JG, 2008, On flow properties, fibre distribution, fibre orientation and flexural behaviour of FRC. Mater Struct, 41: 189–196. https://doi.org/10.1617/s11527-007-9229-x
- Peled A, Shah SP, 2003, Processing effects in cementitious composites: Extrusion and casting. J Mater Civ Eng, 15: 192–199. https://doi.org/10.1061/(ASCE)0899-1561(2003)15:2(192)
- Lu C, Leung CK, 2017, Theoretical evaluation of fiber orientation and its effects on mechanical properties in engineered cementitious composites (ECC) with various thicknesses. Cem Concr Res, 95: 240–246. https://doi.org/10.1016/j.cemconres.2017.02.024
- Hambach M, Volkmer D, 2017, Properties of 3D-printed fiber-reinforced Portland cement paste. Cem Concr Compos, 79: 62–70. https://doi.org/10.1016/j.cemconcomp.2017.02.001
- Figueiredo SC, Rodriguez CR, Ahmed ZY, et al., 2020, Mechanical behavior of printed strain hardening cementitious composites. Materials (Basel), 13: 2253. https://doi.org/10.3390/ma13102253
- Aveston J, Kelly A, 1973, Theory of multiple fracture of fibrous composites. J Mater Sci, 8: 352–362. https://doi.org/10.1007/BF00550155
- Panton RL, 2006, Incompressible Flow. Hoboken: John Wiley and Sons.
- Lao W, Li M, Wong TN, et al., 2020, Improving surface finish quality in extrusion-based 3D concrete printing using machine learning-based extrudate geometry control. Virtual Phys Prototyp, 15: 178–193. https://doi.org/10.1080/17452759.2020.1713580
- Weng Y, Li M, Liu Z, et al., 2019, Printability and fire performance of a developed 3D printable fibre reinforced cementitious composites under elevated temperatures. Virtual Phys Prototyp, 14: 284–292. https://doi.org/10.1080/17452759.2018.1555046
- Li VC, Bos FP, Yu K, et al., 2020, On the emergence of 3D printable engineered, strain hardening cementitious composites (ECC/SHCC). Cem Concr Res, 132: 106038. https://doi.org/10.1016/j.cemconres.2020.106038
- Weng Y, Lu B, Li M, et al., 2018, Empirical models to predict rheological properties of fiber reinforced cementitious composites for 3D printing. Constr Build Mater, 189: 676–685. https://doi.org/10.1016/j.conbuildmat.2018.09.039
- Weng Y, Li M, Tan MJ, et al., 2018, Design 3D printing cementitious materials via Fuller Thompson theory and Marson-Percy model. Constr Build Mater, 163: 600–610. https://doi.org/10.1016/j.conbuildmat.2017.12.112
- Weng Y, Ruan S, Li M, et al., 2019, Feasibility study on sustainable magnesium potassium phosphate cement paste for 3D printing. Constr Build Mater, 221: 595–603. https://doi.org/10.1016/j.conbuildmat.2019.05.053
- Li M, Weng Y, Liu Z, et al., 2022, Optimizing of chemical admixtures for 3D printable cementitious materials by central composite design. Mater Sci Addit Manuf, 1: 16. https://doi.org/10.18063/msam.v1i3.16
- Weng Y, Li M, Zhang D, et al., 2021, Investigation of interlayer adhesion of 3D printable cementitious material from the aspect of printing process. Cem Concr Res, 143: 106386. https://doi.org/10.1016/j.cemconres.2021.106386
- Weng Y, Li M, Ruan S, et al., 2020, Comparative economic, environmental and productivity assessment of a concrete bathroom unit fabricated through 3D printing and a precast approach. J Clean Prod, 261: 121245. https://doi.org/10.1016/j.jclepro.2020.121245
- Weng Y, Li M, Wong TN, et al., 2021, Synchronized concrete and bonding agent deposition system for interlayer bond strength enhancement in 3D concrete printing. Autom Constr, 123: 103546. https://doi.org/10.1016/j.autcon.2020.103546
- Weng Y, Ahamed NA, Lee BJ, et al., 2021, Extracting BIM information for lattice Toolpath planning in digital concrete printing with developed dynamo script: A case study. J Comput Civ Eng, 35: 05021001. https://doi.org/10.1061/(ASCE)CP.1943-5487.0000964
- Ranade R, Stults MD, Lee B, et al., 2012, Effects of fiber dispersion and flaw size distribution on the composite properties of PVA-ECC. In: High Performance Fiber Reinforced Cement Composites. Dordrecht: Springer. p. 107–114.
- Torigoe S, Horikoshi T, Ogawa A, et al., 2003, Study on evaluation method for PVA fiber distribution in engineered cementitious composite. J Adv Concr Technol, 1: 265–268. https://doi.org/10.3151/jact.1.265
- Suuronen JP, Kallonen A, Eik M, et al., 2013, Analysis of short fibres orientation in steel fibre-reinforced concrete (SFRC) by X-ray tomography. J Mater Sci, 48: 1358–1367. https://doi.org/10.1007/s10853-012-6882-4
- Tosun-Felekoǧlu K, Felekoǧlu B, Ranade R, et al., 2014, The role of flaw size and fiber distribution on tensile ductility of PVA-ECC. Compos B Eng, 56: 536–545. https://doi.org/10.1016/j.compositesb.2013.08.089
- Ruan S, Qiu J, Weng Y, et al., 2019, The use of microbial induced carbonate precipitation in healing cracks within reactive magnesia cement-based blends. Cem Concr Res, 115: 176–188. https://doi.org/10.1016/j.cemconres.2018.10.018
- Lee BY, Kim JK, Kim JS, et al., 2009, Quantitative evaluation technique of polyvinyl alcohol (PVA) fiber dispersion in engineered cementitious composites. Cem Concr Compos, 31: 408–417. https://doi.org/10.1016/j.cemconcomp.2009.04.002
- Weng Y, Lu B, Tan MJ, et al., 2016, Rheology and Printability of Engineered Cementitious Composites-a Literature Review. In: Proceedings of the 2nd International Conference on Progress in Additive Manufacturing (Pro-AM 2016). p. 427–432.