A review of advances in additive manufacturing and the integration of high-performance polymers, alloys, and their composites
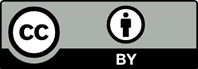
In recent years, additive manufacturing (AM) has emerged as the most revolutionary technology in manufacturing, playing an indispensable role in many important areas due to its outstanding precision, ability to fabricate complex structures, and short production cycles. At the same time, the development of this technology has been accompanied by a constant search for materials suitable for it. These materials play important roles in the industry, have excellent properties but are difficult to process using traditional manufacturing methods, or are newly developed materials specifically for AM. While these explorations are being undertaken, attention to standards in the field will ensure that research is accelerated and on the right track. This paper presents each of the seven technique categories of AM. The focus of this paper is on the emerging materials for AM, such as polyetheretherketone, polyimide, high entropy alloys, and composites. Finally, international standards in the field of AM with perspectives on research in this area are also presented.
- Gao W, Zhang Y, Ramanujan D, et al., 2015, The status, challenges, and future of additive manufacturing in engineering. Comput Aided Des, 69: 65–89. https://doi.org/10.1016/j.cad.2015.04.001
- Herzog D, Seyda V, Wycisk E, et al., 2016, Additive manufacturing of metals. Acta Mater, 117: 371–392. https://doi.org/10.1016/j.actamat.2016.07.019
- Yeong WY, Goh GL, Goh GD, et al., 2022, 3D printing of soft grippers with multimaterial design: Towards shape conformance and tunable rigidity. Mater Today Proc, 70: 525–530. https://doi.org/10.1016/j.matpr.2022.09.552
- ISO/TC 261 and ASTM Committee F42, 2021, ISO/ASTM 52900:2021 Additive Manufacturing - General Principles - Fundamentals and Vocabulary. United Kingdom: ISO.
- Lores A, Azurmendi N, Agote I, et al., 2019, A review on recent developments in binder jetting metal additive manufacturing: Materials and process characteristics. Powder Metall, 62: 267–296. https://doi.org/10.1080/00325899.2019.1669299
- Li M, Du W, Elwany A, et al., 2020, Metal binder jetting additive manufacturing: A literature review. J Manuf Sci Eng, 142: 090801. https://doi.org/10.1115/1.4047430
- Gaytan SM, Cadena MA, Karim H, et al., 2015, Fabrication of barium titanate by binder jetting additive manufacturing technology. Ceram Int, 41: 6610–6619. https://doi.org/10.1016/j.ceramint.2015.01.108
- Oropeza D, Roberts R, Hart AJ, 2022, A rapid development workflow for binder inks for additive manufacturing with application to polymer and reactive binder ink formulation. J Manuf Process, 73: 471–482. https://doi.org/10.1016/j.jmapro.2021.10.068
- Do T, Kwon P, Shin CS, 2017, Process development toward full-density stainless steel parts with binder jetting printing. Int J Mach Tools Manuf, 121: 50–60. https://doi.org/10.1016/j.ijmachtools.2017.04.006
- Wu S, Yang Y, Huang Y, et al., 2023, Study on powder particle behavior in powder spreading with discrete element method and its critical implications for binder jetting additive manufacturing processes. Virtual Phys Prototyp, 18: e2158877. https://doi.org/10.1080/17452759.2022.2158877
- Grant LO, Higgs CF 3rd, Cordero ZC, 2023, Sintering mechanics of binder jet 3D printed ceramics treated with a reactive binder. J Eur Ceram Soc, 43: 2601–2613. https://doi.org/10.1016/j.jeurceramsoc.2022.12.017
- Oropeza D, Hart AJ, 2021, Reactive binder jet additive manufacturing for microstructural control and dimensional stability of ceramic materials. Addit Manuf, 48: 102448. https://doi.org/10.1016/j.addma.2021.102448
- Bai Y, Williams CB, 2018, Binder jetting additive manufacturing with a particle-free metal ink as a binder precursor. Mater Des, 147: 146–156. https://doi.org/10.1016/j.matdes.2018.03.027
- Du W, Ren X, Ma C, et al., 2019, Ceramic binder jetting additive manufacturing: Particle coating for increasing powder sinterability and part strength. Mater Lett, 234: 327–330. https://doi.org/10.1016/j.matlet.2018.09.118
- Saboori A, Gallo D, Biamino S, et al., 2017, An overview of additive manufacturing of titanium components by directed energy deposition: Microstructure and mechanical properties. Appl Sci, 7: 883. https://doi.org/10.3390/app7090883
- Dass A, Moridi A, 2019, State of the art in directed energy deposition: From additive manufacturing to materials design. Coatings, 9: 418. https://doi.org/10.3390/coatings9070418
- Piscopo G, Iuliano L, 2022, Current research and industrial application of laser powder directed energy deposition. Int J Adv Manuf Technol, 119: 6893–6917. https://doi.org/10.1007/s00170-021-08596-w
- Svetlizky D, Das M, Zheng B, et al., 2021, Directed energy deposition (DED) additive manufacturing: Physical characteristics, defects, challenges and applications. Mater Today, 49: 271–295. https://doi.org/10.1016/j.mattod.2021.03.020
- Kim MJ, Saldana C, 2020, Thin wall deposition of IN625 using directed energy deposition. J Manuf Process, 56: 1366–1373. https://doi.org/10.1016/j.jmapro.2020.04.032
- Aversa A, Saboori A, Marchese G, et al., 2019, Application of directed energy deposition-based additive manufacturing in repair. Appl Sci, 9: 3316. https://doi.org/10.3390/app9163316050
- Zhang Y, Jing H, Xu L, et al., 2021, Effects of different scanning patterns on nickel alloy-directed energy deposition based on thermal analysis. Virtual Phys Prototyp, 16: S98–S115. https://doi.org/10.1080/17452759.2021.1896173
- Feenstra DR, Banerjee R, Fraser HL, et al., 2021, Critical review of the state of the art in multi-material fabrication via directed energy deposition. Curr Opin Solid State Mater Sci, 25: 100924. https://doi.org/10.1016/j.cossms.2021.100924
- Li C, Hodgson P, Preuss M, et al., 2023, Rolling‐assisted direct energy deposited Inconel 718: Microstructural evolution and mechanical properties after optimized heat treatment. J Mater Sci Technol, 144: 118–127. https://doi.org/10.1016/j.jmst.2022.10.021
- Loh GH, Pei E, Gonzalez-Gutierrez J, et al., 2020, An overview of material extrusion troubleshooting. Appl Sci, 10: 4776. https://doi.org/10.3390/app10144776
- 3D Bioprinting Processes: A Perspective on Classification and Terminology-publicly Available Content Database- ProQuest. Available from: https://www.proquest.com/ publiccontent/docview/2667821253?parentsessionid=g5 su4k00jcjidvwri1of%2fvos6r6xqgutqyvil8iniw4%3d&pq-origsite=360link&accountid=13876 [Last accessed on 2022 Dec 20].
- Spoerk M, Arbeiter F, Koutsamanis I, et al., 2021, Personalised urethra pessaries prepared by material extrusion-based additive manufacturing. Int J Pharm, 608: 121112. https://doi.org/10.1016/j.ijpharm.2021.121112
- Davis AY, Zhang Q, Wong JP, et al., 2019, Characterization of volatile organic compound emissions from consumer level material extrusion 3D printers. Build Environ, 160: 106209. https://doi.org/10.1016/j.buildenv.2019.106209
- Vidakis N, Petousis M, Michailidis N, et al., 2023, Polyethylene glycol and polyvinylpyrrolidone reduction agents for medical grade polyamide 12/silver nanocomposites development for material extrusion 3D printing: Rheological, thermomechanical, and biocidal performance. React Funct Polym, 190: 105623. https://doi.org/10.1016/j.reactfunctpolym.2023.105623
- Yang H, Lim JC, Liu Y, et al., 2017, Performance evaluation of ProJet multi-material jetting 3D printer. Virtual Phys Prototyp, 12: 95–103. https://doi.org/10.1080/17452759.2016.1242915
- Mora S, Pugno NM, Misseroni D, 2022, 3D printed architected lattice structures by material jetting. Mater Today, 59: 107–132. https://doi.org/10.1016/j.mattod.2022.05.008
- Gülcan O, Günaydın K, Tamer A, 2021, The state of the art of material jetting-a critical review. Polymers (Basel), 13: 2829. https://doi.org/10.3390/polym13162829
- Moore JP, Williams CB, 2015, Fatigue properties of parts printed by PolyJet material jetting. Rapid Prototyp J, 21: 675–685. https://doi.org/10.1108/RPJ-03-2014-0031
- Milovanović A, Sedmak A, Golubović Z, et al., 2021, The effect of time on mechanical properties of biocompatible photopolymer resins used for fabrication of clear dental aligners. J Mech Behav Biomed Mater, 119: 104494. https://doi.org/10.1016/j.jmbbm.2021.104494
- Golhin AP, Srivastava C, Strandlie A, et al., 2023, Effects of accelerated aging on the appearance and mechanical performance of materials jetting products. Mater Des, 228: 111863. https://doi.org/10.1016/j.matdes.2023.111863
- Sing SL, Yeong WY, 2020, Laser powder bed fusion for metal additive manufacturing: Perspectives on recent developments. Virtual Phys Prototyp, 15: 359–370. https://doi.org/10.1080/17452759.2020.1779999
- Sing SL, An J, Yeong WY, et al., 2016, Laser and electron-beam powder-bed additive manufacturing of metallic implants: A review on processes, materials and designs. J Orthop Res, 34: 369–385. https://doi.org/10.1002/jor.23075
- Awad A, Fina F, Goyanes A, et al., 2021, Advances in powder bed fusion 3D printing in drug delivery and healthcare. Adv Drug Deliv Rev, 174: 406–424. https://doi.org/10.1016/j.addr.2021.04.025
- Goodridge RD, Ziegelmeier S, 2017, Powder bed fusion of polymers. In: Laser Additive Manufacturing. United Kingdom: Woodhead Publishing. p. 181–204. https://doi.org/10.1016/B978-0-08-100433-3.00007-5
- Grasso ML, Colosimo BM, 2017, Process defects and in situ monitoring methods in metal powder bed fusion: A review. Meas Sci Technol, 28: 044005. https://doi.org/10.1088/1361-6501/aa5c4f
- Liverani E, Toschi S, Ceschini L, et al., 2017, Effect of selective laser melting (SLM) process parameters on microstructure and mechanical properties of 316L austenitic stainless steel. J Mater Process Technol, 249: 255–263. https://doi.org/10.1016/j.jmatprotec.2017.05.042
- Zhong Y, Rännar LE, Wikman S, et al., 2017, Additive manufacturing of ITER first wall panel parts by two approaches: Selective laser melting and electron beam melting. Fusion Eng Des, 116: 24–33. https://doi.org/10.1016/j.fusengdes.2017.01.032
- Romedenne M, Pillai R, Kirka M, et al., 2020, High temperature air oxidation behavior of Hastelloy X processed by electron beam melting (EBM) and selective laser melting (SLM). Corros Sci, 171: 108647. https://doi.org/10.1016/j.corsci.2020.108647
- Bhavar V, Kattire P, Patil V, et al., 2014, A Review on Powder Bed Fusion Technology of Metal Additive Manufacturing. Boca Raton: CRC Press.
- Zhao X, Li S, Zhang M, et al., 2016, Comparison of the microstructures and mechanical properties of Ti-6Al-4V fabricated by selective laser melting and electron beam melting. Mater Des, 95: 21–31. https://doi.org/10.1016/j.matdes.2015.12.135
- Monti C, Turani M, Papis K, et al., 2023, A new Al-Cu alloy for LPBF developed via ultrasonic atomization. Mater Des, 229: 111907. https://doi.org/10.1016/j.matdes.2023.111907
- Xiao F, Shu D, Wang D, et al., 2023, Effect of Zn content on the formability and aging precipitation of Al-Zn-Mg-Cu-Nb alloys prepared by LPBF. J Mater Res Technol, 25: 6338–6355. https://doi.org/10.1016/j.jmrt.2023.07.057
- Pilipović A, 2022, Chapter 11-sheet lamination. In: Izdebska- Podsiadły J, editor. Polymers for 3D Printing, Plastics Design Library. Norwich, NY: William Andrew Publishing. p. 127–136. https://doi.org/10.1016/B978-0-12-818311-3.00008-2
- Gibson I, Rosen DW, Stucker B, 2010, Sheet lamination processes. In: Additive Manufacturing Technologies: Rapid Prototyping to Direct Digital Manufacturing. Boston, MA: Springer US. p. 223–252. https://doi.org/10.1007/978-1-4419-1120-9_8
- Gibson I, Rosen D, Stucker B, et al., 2021, Sheet lamination. In: Khorasani M, editor. Additive Manufacturing Technologies. Cham: Springer International Publishing. p. 253–283. https://doi.org/10.1007/978-3-030-56127-7_9
- You X, Tan Y, Takeyama M, et al., 2023, Fabrication of a turbine disk alloy by electron beam sheet lamination and investigation on the improved high temperature creep performance. J Mater Sci Technol, 143: 216–233. https://doi.org/10.1016/j.jmst.2022.10.013
- Piedra-Cascón W, Krishnamurthy VR, Att W, et al., 2021, 3D printing parameters, supporting structures, slicing, and post-processing procedures of vat-polymerization additive manufacturing technologies: A narrative review. J Dent, 109: 103630. https://doi.org/10.1016/j.jdent.2021.103630
- Pagac M, Hajnys J, Ma QP, et al., 2021, A review of vat photopolymerization technology: Materials, applications, challenges, and future trends of 3D printing. Polymers (Basel), 13: 598. https://doi.org/10.3390/polym13040598
- Maines EM, Porwal MK, Ellison CJ, et al., 2021, Sustainable advances in SLA/DLP 3D printing materials and processes. Green Chem, 23: 6863–6897. https://doi.org/10.1039/D1GC01489G
- Tai XY, Zhakeyev A, Wang H, et al., 2019, Accelerating fuel cell development with additive manufacturing technologies: State of the art, opportunities and challenges. Fuel Cells, 19: 636–650. https://doi.org/10.1002/fuce.201900164
- Sampson KL, Deore B, Go A, et al., 2021, Multimaterial vat polymerization additive manufacturing. ACS Appl Polym Mater, 3: 4304–4324. https://doi.org/10.1021/acsapm.1c00262
- Zhang F, Zhu L, Li Z, et al., 2021, The recent development of vat photopolymerization: A review. Addit Manuf, 48: 102423. https://doi.org/10.1016/j.addma.2021.102423
- Ng WL, Lee JM, Zhou M, et al., 2020, Vat polymerization-based bioprinting-process, materials, applications and regulatory challenges. Biofabrication, 12: 022001. https://doi.org/10.1088/1758-5090/ab6034
- Milton LA, Viglione MS, Ong LJ, et al., 2023, Vat photopolymerization 3D printed microfluidic devices for organ-on-a-chip applications. Lab Chip, 23: 3537–3560. https://doi.org/10.1039/D3LC00094J
- Bucciarelli A, Paolelli X, De Vitis E, et al., 2022, VAT photopolymerization 3D printing optimization of high aspect ratio structures for additive manufacturing of chips towards biomedical applications. Addit Manuf, 60: 103200. https://doi.org/10.1016/j.addma.2022.103200
- Najeeb S, Zafar MS, Khurshid Z, et al., 2016, Applications of polyetheretherketone (PEEK) in oral implantology and prosthodontics. J Prosthodont Res, 60: 12–19. https://doi.org/10.1016/j.jpor.2015.10.001
- Zhang Z, Breidt C, Chang L, et al., 2004, Wear of PEEK composites related to their mechanical performances. Tribol Int, 37: 271–277. https://doi.org/10.1016/j.triboint.2003.09.005
- Tariverdian T, Navaei T, Milan PB, et al., 2019, Chapter 16-functionalized polymers for tissue engineering and regenerative medicines. In: Mozafari M, Chauhan NP, editors. Advanced Functional Polymers for Biomedical Applications. Netherlands: Elsevier. p. 323–357. https://doi.org/10.1016/B978-0-12-816349-8.00016-3
- McKeen LW, 2009, Chapter 10-high-temperature polymers. In: The Effect of Creep and Other Time Related Factors on Plastics and Elastomers, in Plastics Design Library. 2nd ed. Boston: William Andrew Publishing. p. 337–372. https://doi.org/10.1016/B978-0-8155-1585-2.50012-1
- Siewert B, Plaza-Castro M, Sereno N, et al., 2019, Chapter 20-applications of PEEK in the dental field. In: Kurtz SM, editor. PEEK Biomaterials Handbook, in Plastics Design Library. 2nd ed. Norwich, NY: William Andrew Publishing, p. 333–342. https://doi.org/10.1016/B978-0-12-812524-3.00020-X
- Katzer A, Marquardt H, Westendorf J, et al., 2002, Polyetheretherketone--cytotoxicity and mutagenicity in vitro. Biomaterials, 23: 1749–1759. https://doi.org/10.1016/S0142-9612(01)00300-3
- Kurtz SM, 2019, Chapter 1-an overview of PEEK biomaterials. In: PEEK Biomaterials Handbook, in Plastics Design Library. 2nd ed. Norwich, NY: William Andrew Publishing. p. 3–9. https://doi.org/10.1016/B978-0-12-812524-3.00001-6
- Monich PR, Henriques B, de Oliveira AP, et al., 2016, Mechanical and biological behavior of biomedical PEEK matrix composites: A focused review. Mater Lett, 185: 593–597. https://doi.org/10.1016/j.matlet.2016.09.005
- Verma S, Sharma N, Kango S, 2021, Developments of PEEK (polyetheretherketone) as a biomedical material: A focused review. Eur Polym J, 147: 110295. https://doi.org/10.1016/j.eurpolymj.2021.110295
- Singh R, Singh G, Singh J, et al., 2020, 3D Printing of polyether-ether-ketone functional prototypes for engineering applications. In: Hashmi S, Choudhury IA, editors. Encyclopedia of Renewable and Sustainable Materials. Oxford: Elsevier. p. 207–214. https://doi.org/10.1016/B978-0-12-803581-8.11543-7
- Haleem A, Javaid M, 2019, Polyether ether ketone (PEEK) and its manufacturing of customised 3D printed dentistry parts using additive manufacturing. Clin Epidemiol Glob Health, 7: 654–660. https://doi.org/10.1016/j.cegh.2019.03.001
- Cicala G, Latteri A, Del Curto B, et al., 2017, Engineering thermoplastics for additive manufacturing: A critical perspective with experimental evidence to support functional applications. J Appl Biomater Funct Mater, 15: 10–18. https://doi.org/10.5301/jabfm.5000343
- Manzoor F, Golbang A, Jindal S, et al., 2021, 3D printed PEEK/HA composites for bone tissue engineering applications: Effect of material formulation on mechanical performance and bioactive potential. J Mech Behav Biomed Mater, 121: 104601. https://doi.org/10.1016/j.jmbbm.2021.104601
- Stepashkin AA, Chukov DI, Senatov FS, et al., 2018, 3D-printed PEEK-carbon fiber (CF) composites: Structure and thermal properties. Compos Sci Technol, 164: 319–326. https://doi.org/10.1016/j.compscitech.2018.05.032
- Arif MF, Alhashmi H, Varadarajan KM, et al., 2020, Multifunctional performance of carbon nanotubes and graphene nanoplatelets reinforced PEEK composites enabled via FFF additive manufacturing. Compos B Eng, 184: 107625. https://doi.org/10.1016/j.compositesb.2019.107625
- Zhang J, Su Y, Rao X, et al., 2022, Additively manufactured polyether ether ketone (PEEK) skull implant as an alternative to titanium mesh in cranioplasty. Int J Bioprint, 9: 634. https://doi.org/10.18063/ijb.v9i1.634
- Zhang W, Liu L, Zhou H, et al., 2023, Surface bisphosphonation of polyetheretherketone to manipulate immune response for advanced osseointegration. Mater. Des, 232: 112151. https://doi.org/10.1016/j.matdes.2023.112151
- Gao W, Han X, Sun D, et al., 2023, Antibacterial properties of antimicrobial peptide HHC36 modified polyetheretherketone. Front Microbiol, 14: 1103956. https://doi.org/10.3389/fmicb.2023.1103956
- Liaw DJ, Wang KL, Huang YC, et al., 2012, Advanced polyimide materials: Syntheses, physical properties and applications. Prog Polym Sci, 37: 907–974. https://doi.org/10.1016/j.progpolymsci.2012.02.005
- Polyimides. Available from: https://books.google.com/ books/about/polyimides.html?hl=zh-cn&id=n7eigaukutic [Last accessed on 2022 Dec 07].
- Weyhrich CW, Long TE, 2022, Additive manufacturing of high-performance engineering polymers: Present and future. Polym Int, 71: 532–536. https://doi.org/10.1002/pi.6343
- Guo Y, Ji Z, Zhang Y, et al., 2017, Solvent-free and photocurable polyimide inks for 3D printing. J Mater Chem A, 5: 16307–16314. https://doi.org/10.1039/C7TA01952A
- Hegde M, Meenakshisundaram V, Chartrain N, et al., 2017, 3D Printing all-aromatic polyimides using mask-projection stereolithography: Processing the nonprocessable. Adv Mater, 29: 1701240. https://doi.org/10.1002/adma.201701240
- Qin S, Jiang Y, Yang C, et al., 2021, Three-dimensional printing of high-performance polyimide by direct ink writing of hydrogel precursor. J Appl Polym Sci, 138: 50636. https://doi.org/10.1002/app.50636
- Liu Z, Cai Y, Song F, et al., 2022, Study on chemical graft structure modification and mechanical properties of photocured polyimide. ACS Omega, 7: 9582–9593. https://doi.org/10.1021/acsomega.1c06933
- Gouzman I, Grossman E, Verker R, et al., 2019, Advances in polyimide-based materials for space applications. Adv Mater, 31: 1807738. https://doi.org/10.1002/adma.201807738
- Ye W, Wu W, Hu X, et al., 2019, 3D printing of carbon nanotubes reinforced thermoplastic polyimide composites with controllable mechanical and electrical performance. Compos Sci Technol, 182: 107671. https://doi.org/10.1016/j.compscitech.2019.05.028
- Yeh JW, Chen SK, Lin SJ, et al., 2004, Nanostructured high-entropy alloys with multiple principal elements: Novel alloy design concepts and outcomes. Adv Eng Mater, 6: 299–303. https://doi.org/10.1002/adem.200300567
- Wu Z, Bei H, Pharr GM, et al., 2014, Temperature dependence of the mechanical properties of equiatomic solid solution alloys with face-centered cubic crystal structures. Acta Mater, 81: 428–441. https://doi.org/10.1016/j.actamat.2014.08.026
- Dewangan SK, Mangish A, Kumar S, et al., 2022, A review on High-Temperature Applicability: A milestone for high entropy alloys. Eng Sci Technol Int J, 35: 101211. https://doi.org/10.1016/j.jestch.2022.101211
- Rong Z, Wang C, Wang Y, et al., 2022, Microstructure and properties of FeCoNiCrX (X=Mn, Al) high-entropy alloy coatings. J Alloys Compd, 921: 166061. https://doi.org/10.1016/j.jallcom.2022.166061
- Yeh JW, 2016, Overview of high-entropy alloys. In: Gao MC, Liaw PK, Zhang Y, et al., editors. High-entropy Alloys: Fundamentals and Applications. Cham: Springer International Publishing. p. 1–19. https://doi.org/10.1007/978-3-319-27013-5_1
- Senkov ON, Miracle DB, Chaput KJ, et al., 2018, Development and exploration of refractory high entropy alloys-a review. J Mater Res, 33: 3092–3128. https://doi.org/10.1557/jmr.2018.153
- Iroc LK, Tukac OU, Tanrisevdi BB, et al., 2022, Design of oxygen-doped TiZrHfNbTa refractory high entropy alloys with enhanced strength and ductility. Mater Des, 223: 111239. https://doi.org/10.1016/j.matdes.2022.111239
- Senkov ON, Wilks GB, Scott JM, et al., 2011, Mechanical properties of Nb25Mo25Ta25W25 and V20Nb20Mo20Ta20W20 refractory high entropy alloys. Intermetallics, 19: 698–706. https://doi.org/10.1016/j.intermet.2011.01.004
- Senkov ON, Senkova SV, Woodward C, 2014, Effect of aluminum on the microstructure and properties of two refractory high-entropy alloys. Acta Mater, 68: 214–228. https://doi.org/10.1016/j.actamat.2014.01.029
- Senkov ON, Woodward CF, 2011, Microstructure and properties of a refractory NbCrMo0.5Ta0.5TiZr alloy. Mater Sci Eng A, 529: 311–320. https://doi.org/10.1016/j.msea.2011.09.033
- Liu D, Yu Q, Kabra S, et al., 2022, Exceptional fracture toughness of CrCoNi-based medium- and high-entropy alloys at 20 kelvin. Science, 378: 978–983. https://doi.org/10.1126/science.abp8070
- Chen S, Tong Y, Liaw PK, 2018, Additive manufacturing of high-entropy alloys: A review. Entropy, 20: 937. https://doi.org/10.3390/e20120937
- Chen Y, Zhou Q, 2022, Directed energy deposition additive manufacturing of CoCrFeMnNi high-entropy alloy towards densification, grain structure control and improved tensile properties. Mater Sci Eng A, 860: 144272. https://doi.org/10.1016/j.msea.2022.144272
- Zhou R, Liu Y, Zhou C, et al., 2018, Microstructures and mechanical properties of C-containing FeCoCrNi high-entropy alloy fabricated by selective laser melting. Intermetallics, 94: 165–171. https://doi.org/10.1016/j.intermet.2018.01.002
- Ren J, Zhang Y, Zhao D, et al., 2022, Strong yet ductile nanolamellar high-entropy alloys by additive manufacturing. Nature, 608: 62–68. https://doi.org/10.1038/s41586-022-04914-8
- Lin D, Xu L, Li X, et al., 2020, A Si-containing FeCoCrNi high-entropy alloy with high strength and ductility synthesized in situ via selective laser melting. Addit Manuf, 35: 101340. https://doi.org/10.1016/j.addma.2020.101340
- Gao X, Yu Z, Hu W, et al., 2020, In situ strengthening of CrMnFeCoNi high-entropy alloy with Al realized by laser additive manufacturing. J. Alloys Compd, 847: 156563. https://doi.org/10.1016/j.jallcom.2020.156563
- Zhang M, Zhou X, Wang D, et al., 2022, Additive manufacturing of in-situ strengthened dual-phase AlCoCuFeNi high-entropy alloy by selective electron beam melting. J. Alloys Compd, 893: 162259. https://doi.org/10.1016/j.jallcom.2021.162259
- Karthik GM, Panikar S, Ram GD, et al., 2017, Additive manufacturing of an aluminum matrix composite reinforced with nanocrystalline high-entropy alloy particles. Mater Sci Eng A, 679: 193–203. https://doi.org/10.1016/j.msea.2016.10.038
- Li J, Xiang S, Luan H, et al., 2019, Additive manufacturing of high-strength CrMnFeCoNi high-entropy alloys-based composites with WC addition. J Mater Sci Technol, 35: 2430–2434. https://doi.org/10.1016/j.jmst.2019.05.062
- Amar A, Li J, Xiang S, et al., 2019, Additive manufacturing of high-strength CrMnFeCoNi-based high entropy alloys with TiC addition. Intermetallics, 109: 162–166. https://doi.org/10.1016/j.intermet.2019.04.005
- AMS4999: Titanium Alloy Laser Deposited Products-6al-4v- Annealed-SAE International. Available from: https://www.sae. org/standards/content/ams4999 [Last accessed on 2022 Dec 10].
- AMS4999A: Titanium Alloy Direct Deposited Products 6Al-4V Annealed-SAE International. Available from: https://www.sae.org/standards/content/ams4999a [Last accessed on 2022 Dec 10].
- Committee F42 on Additive Manufacturing Technologies. Available from: https://www.astm.org/committee-f42 [Last accessed on 2022 Dec 10].
- Committee F42 Subcommittees. Available from: https://www. astm.org/get-involved/technical-committees/committee-f42/ subcommittee-f42 [Last accessed on 2022 Dec 10].
- ASTM Committee F42, 2021, ASTM F3049-14 (2021) Standard Guide for Characterizing Properties of Metal Powders Used for Additive Manufacturing Processes. United States: ASTM. https://doi.org/10.1520/F3049-14R21
- ASTM Committee F42, 2021, ASTM F3091/ F3091M-14(2021) Standard Specification for Powder Bed Fusion of Plastic Materials. United States: ASTM. https://doi.org/10.1520/F3091_F3091M-14R21
- ASTM Committee F42, 2021, ASTM F3055-14a(2021) Standard Specification for Additive Manufacturing Nickel Alloy (UNS N07718) with Powder Bed Fusion. United States: ASTM. https://doi.org/10.1520/F3055-14AR21
- ASTM Committee F42, 2021, ASTM F3056-14(2021) Standard Specification for Additive Manufacturing Nickel Alloy (UNS N06625) with Powder Bed Fusion. United States: ASTM. https://doi.org/10.1520/F3056-14R21
- ASTM Committee F42, 2021, ASTM F2924-14(2021) Standard Specification for Additive Manufacturing Titanium-6 Aluminum-4 Vanadium with Powder Bed Fusion. United States: ASTM. https://doi.org/10.1520/F2924-14R21
- ASTM Committee F42, 2021, ASTM F3001-14(2021) Standard Specification for Additive Manufacturing Titanium-6 Aluminum-4 Vanadium ELI (Extra Low Interstitial) with Powder Bed Fusion. United States: ASTM. https://doi.org/10.1520/F3001-14R21
- ASTM Committee F42, 2016, ASTM F3187-16 Standard Guide for Directed Energy Deposition of Metals. United States: ASTM. https://doi.org/10.1520/F3187-16
- ISO/TC 261-Additive Manufacturing. ISO. Available from: https://www.iso.org/committee/629086.html [Last accessed on 2022 Dec 10].
- Additive manufacturing-material Extrusion-based Additive Manufacturing of Plastic Materials-part 1: Feedstock Materials. Available from: https://www.astm.org/f3241-20. html [Last accessed on 2022 Dec 10].
- CORDIS European Commission. Available from: https:// cordis.europa.eu/project/id/319167/reporting [Last accessed on 2022 Dec 10].
- TC562NationalAdditiveManufacturingStandardizationTechnical Committee. Available from: https://std.samr.gov.cn/search/ orgdetailviewcnf?data_id=da4c780fa8756d08e05397be0a0a6dff [Last accessed on 2022 Dec 10].
- Dubov A, Ruben S, 2022, Material development standards and methods for additive manufacturing in construction to meet building code requirements for certification. In: Progress in Additive Manufacturing 2020. United States: ASTM International. p. 375–385. https://doi.org/10.1520/STP163720200103
- Erps T, Foshey M, Luković MK, et al., 2021, Accelerated discovery of 3D printing materials using data-driven multiobjective optimization. Sci Adv, 7: eabf7435. https://doi.org/10.1126/sciadv.abf7435
- Goh GD, Huang X, Huang S, et al., 2023, Data imputation strategies for process optimization of laser powder bed fusion of Ti6Al4V using machine learning. Mater Sci Addit Manuf, 2: 50. https://doi.org/10.36922/msam.50
- Bagheri A, Cremona C, 2020, Formulation of mix design for 3D printing of geopolymers: A machine learning approach. Mater Adv, 1: 720–727. https://doi.org/10.1039/D0MA00036A
- Analytical Investigation of Aerosol Jet Printing. Available from: https://www-tandfonline-com.libproxy1.nus.edu.sg/doi/full/10 .1080/02786826.2014.940439 [Last accessed on 2023 Sep 04].
- Goh GL, Zhang H, Goh GD, et al., 2022, Multi-objective optimization of intense pulsed light sintering process for aerosol jet printed thin film. Mater Sci Addit Manuf, 1: 10.https://doi.org/10.36922/msam.26
- Jiang P, Ji Z, Zhang X, et al., 2018, Recent advances in direct ink writing of electronic components and functional devices. Prog Addit Manuf, 3: 65–86. https://doi.org/10.1007/s40964-017-0035-x