Plasma spheroidization of gas-atomized 304L stainless steel powder for laser powder bed fusion process
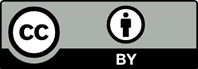
Particles of AISI 304L stainless steel powder were spheroidized by the induction plasma spheroidization process (TekSphero-15 spheroidization system) to assess the effects of the spheroidization process on powder and part properties. The morphology of both as-received and spheroidized powders was characterized by measuring particle size and shape distribution. The chemistry of powders was studied using inductively coupled plasma optical emission spectroscopy for evaluation of composing elements, and the powder’s microstructure was assessed by X-ray diffraction for phase identification and by electron backscattered diffraction patterns for crystallography characterization. The Revolution Powder Analyzer was used to quantify powder flowability. The mechanical properties of parts fabricated with as-received and spheroidized powders using laser powder bed fusion process were measured and compared. Our experimental results showed that the fabricated parts with plasma spheroidized powder have lower tensile strength but higher ductility. Considerable changes in powder chemistry and microstructure were observed due to the change in solidification mode after the spheroidization process. The spheroidized powder solidified in the austenite-toferrite solidification mode due to the loss of carbon, nitrogen, and oxygen. In contrast, the as-received powder solidified in the ferrite-to-austenite solidification mode. This change in solidification mode impacted the components made with spheroidized powder to have lower tensile strength but higher ductility.
Committee F42 on Additive Manufacturing Technologies. Available from: https://www.astm.org/COMMITTEE/F42. htm [Last accessed on 2021 Jan 02].
Behdani B, Senter M, Mason L, et al., 2020, Numerical study on the temperature-dependent viscosity effect on the strand shape in extrusion-based additive manufacturing. J Manuf Mater Process, 4: 46. https://doi.org/10.3390/jmmp4020046
Sehhat MH, Mahdianikhotbesara A, Hadad M, 2022, Formability investigation for perforated steel sheets. Int J Mater Manuf, 15: 12. https://doi.org/10.4271/05-15-02-0012
Mahdianikhotbesara A, Sehhat MH, Hadad M, 2022, A numerical and experimental study into thermal behavior of micro friction stir welded joints of Al 1050 and copper sheets. Adv Mater Res, 15: 1–15.
Mahdianikhotbesara A, Sehhat MH, Hadad M, 2021, Experimental study on micro-friction stir welding of dissimilar butt joints between Al 1050 and pure copper. Metallogr Microstruct Anal, 10: 1–16. https://doi.org/10.1007/S13632-021-00771-5
Yadegari F, Sehhat MH, Mahdianikhotbesara A, 2022, A Numerical Study of Automotive Body Panel Draw Dies Defects Using Finite Element Simulation. Research Square. https://doi.org/10.21203/RS.3.RS-1300589/V1
Sehhat MH, Behdani B, Hung CH, et al., 2021, Development of an empirical model on melt pool variation in laser foil printing additive manufacturing process using statistical analysis. Metallogr Microstruct Anal, 1: 1–8. https://doi.org/10.1007/S13632-021-00795-X
Hung CH, Turk T, Sehhat MH, et al., 2022, Development and experimental study of an automated laser-foil-printing additive manufacturing system. Rapid Prototyp J, ahead-of-print. https://doi.org/10.1108/RPJ-10-2021-0269
Turk T, Hung CH, Sehhat MH, et al., 2021, Methods of Automating the Laser-Foil-Printing Additive Manufacturing Process. International Solid Freeform Fabrication Symposium, University of Texas at Austin.
Sehhat MH, Mahdianikhotbesara A, Yadegari F, 2021, Impact of temperature and material variation on mechanical properties of parts fabricated with fused deposition modelling (FDM). Int J Adv Manuf Technol, 2021: 107984. https://doi.org/10.21203/RS.3.RS-1079840/V1
Sehhat MH, Mahdianikhotbesara A, Yadegari F, 2021, Verification of Stress Transformation in Anisotropic Material Additively Manufactured by Fused Deposition Modeling (FDM). Free Download Manager. https://doi.org/10.21203/RS.3.RS-1107949/V1
Hung CH, Chen WT, Sehhat MH, et al., 2020, The effect of laser welding modes on mechanical properties and microstructure of 304L stainless steel parts fabricated by laser-foil-printing additive manufacturing. Int J Adv Manuf Technol, 1: 1-11. https://doi.org/10.1007/s00170-020-06402-7
Jirandehi AP, Khonsari MM, 2021, General quantification of fatigue damage with provision for microstructure: A review. Fatigue Fract Eng Mater Struct, 1: 13515. https://doi.org/10.1111/ffe.13515
Liu T, Lough CS, Sehhat H, et al., 2021, In-Situ Thermographic Inspection for Laser Powder Bed Fusion. In: 2021 International Solid Freeform Fabrication Symposium, University of Texas at Austin.
Nezhadfar PD, Thompson S, Saharan A, et al., 2021, Fatigue and failure analysis of an additively manufactured contemporary aluminum alloy. In: The Minerals, Metals and Materials Series. Springer Science and Business Media Deutschland GmbH, Berlin. p212–219. https://doi.org/10.1007/978-3-030-65396-5_31
Sehhat MH, Mahdianikhotbesara A, Yadegari F, 2021, Experimental validation of conductive heat transfer theory: Thermal resistivity and system effects. Comput. Res Prog Appl Sci Eng, 7(1): 1–6. https://doi.org/10.52547/crpase.7.4.2415
Sehhat MH, Sutton AT, Hung CH, et al., 2021, Investigation of mechanical properties of parts fabricated with gas- and water-atomized 304L stainless steel powder in the laser powder bed fusion process. JOM, 2021: 1–8. https://doi.org/10.1007/S11837-021-05029-7
Sehhat MH, Mahdianikhotbesara A, 2021, Powder spreading in laser-powder bed fusion process. Granul Matter, 23: 89. https://doi.org/10.1007/s10035-021-01162-x
Kumar P, Jayaraj R, Zhu Z, et al., 2022, Role of metastable austenite in the fatigue resistance of 304L stainless steel produced by laser-based powder bed fusion. Mater Sci Eng A, 837: 142744. https://doi.org/10.1016/J.MSEA.2022.142744
Kumar P, Zhu Z, Nai SM, et al., 2021, Fracture toughness of 304L austenitic stainless steel produced by laser powder bed fusion. Script Mater, 202: 114002. https://doi.org/10.1016/J.SCRIPTAMAT.2021.114002
Kurzynowski T, Chlebus E, Kuźnicka B, et al., 2012, Parameters in Selective Laser Melting for Processing Metallic Powders. Proc SPIE, 2012: 823914. https://doi.org/10.1117/12.907292
Muñiz-Lerma JA, Nommeots-Nomm A, Waters KE, et al., 2018, A comprehensive approach to powder feedstock characterization for powder bed fusion additive manufacturing: A case study on AlSi7Mg, Materials (Basel), 11: 2386. https://doi.org/10.3390/ma11122386
Sun P, Fang ZZ, Zhang Y, et al., 2017, Microstructure and mechanical properties of Ti-6Al-4V fabricated by selective laser melting of powder produced by granulation-sintering-deoxygenation method. JOM, 69: 2731–2737. https://doi.org/10.1007/S11837-017-2584-3
Antony LV, Reddy RG, 2003, Processes for production of high-purity metal powders. JOM, 55: 14–18. https://doi.org/10.1007/s11837-003-0153-4
Rafi AH, Ahmed DH, 2022, Two-dimensional analogies to the deformation characteristics of a falling droplet and its collision. Arch Mech Eng, 69: 21–43. https://doi.org/10.24425/ame.2021.139649
Dolbec R, Boulos M, Bouchard E, et al., 2013, Nanopowders synthesis at industrial-scale production using the inductively-coupled plasma technology. In: Proceeding International Conference Advanced Nanotechnology for Environmental Engineering. p21–24. https://doi.org/10.1109/ICANMEET.2013.6609224
Sehhat MH, Chandler J, Yates Z, 2021, A review on ICP powder plasma spheroidization process parameters. Int J Refract Met Hard Mater, 2021: 105764. https://doi.org/10.1016/J.IJRMHM.2021.105764
Wang JJ, Hao JJ, Guo ZM, et al., 2015, Preparation of spherical tungsten and titanium powders by RF induction plasma processing. Rare Met, 34: 431–435. https://doi.org/10.1007/s12598-014-0293-4
Ji L, Wang C, Wu W, et al., 2017, Spheroidization by plasma processing and characterization of stainless steel powder for 3D printing. Metall Mater Trans A Phys Metall Mater Sci, 48: 4831–4841. https://doi.org/10.1007/s11661-017-4240-5
Park JY, Park KB, Kang JW, et al., 2020, Spheroidization behavior of water-atomized 316 stainless steel powder by inductively-coupled thermal plasma. Mater Today Commun, 2020: 101488. https://doi.org/10.1016/j.mtcomm.2020.101488
Li YL, Ishigaki T, 2004, Spheroidization of titanium carbide powders by induction thermal plasma processing. J Am Ceram Soc, 84: 1929–1936. https://doi.org/10.1111/j.1151-2916.2001.tb00939.x
Pan T, Karnati S, Zhang Y, et al., 2020, Experiment characterization and formulation estimation of tensile properties for selective laser melting manufactured 304L stainless steel. Mater Sci Eng A, 798: 140086. https://doi.org/10.1016/j.msea.2020.140086
Vigneau E, Loisel C, Devaux MF, et al., 2000, Number of particles for the determination of size distribution from microscopic images. Powder Technol, 107: 243–250. https://doi.org/10.1016/S0032-5910(99)00192-8
Strondl A, Lyckfeldt O, Brodin H, et al., 2015, Characterization and control of powder properties for additive manufacturing. JOM, 67: 549–554. https://doi.org/10.1007/s11837-015-1304-0
Revolution Powder Analyzer Mercury Scientific Inc, (n.d.). Available from: http://www.mercuryscientific.com/ instruments/revolution-powder-analyzer [Last accessed on 2021 Jan 02].
Najafizadeh N, Rajabi M, Hashemi R, Amini S, 2019, Improved microstructure and mechanical properties of sheet metals in ultrasonic vibration enhanced biaxial stretch forming. J Theor Appl Vibr Acoust, 5: 1–10. https://doi.org/10.22064/tava.2019.102421.1124
Karnati S, Hoerchler JL, Liou F, et al., 2017, Influence of Gage Length on Miniature Tensile Characterization of Powder Bed Fabricated 304L Stainless Steel. International Solid Freeform Fabrication Symposium.
Hilton ZT, Newkirk JW, O’malley RJ, 2017, Studying Chromium and Nickel Equivalency to Identify Viable Additive Manufacturing Stainless Steel Chemistries. International Solid Freeform Fabrication Symposium.
Korinko PS, Malene SH, 2001, Considerations for the weldability of types 304L and 316L stainless steel. J Fail Anal Prev, 1: 61–68. https://doi.org/10.1007/BF02715336.
Kelly TF, Cohen M, Sande JB, 12984, Rapid Solidification of a Droplet-processed Stainless Steel. Metall Trans A Phys Metall Mater Sci, 15: 819–833. https://doi.org/10.1007/BF02644556
Razumov NG, Popovich AA, Wang Q, 2018, Thermal plasma spheroidization of high-nitrogen stainless steel powder alloys synthesized by mechanical alloying. Met Mater Int, 24: 363–370. https://doi.org/10.1007/s12540-018-0040-8
Wang Y, Wu X, Li X, et al., 2020, Prediction and analysis of tensile properties of austenitic stainless steel using artificial neural network. Metals (Basel), 10: 234. https://doi.org/10.3390/met10020234
Jirandehi AP, Mehdizadeh M, Khonsari MM, 2020, Temperature-induced buckling of ductile metals during cyclic loading and the subsequent early fracture. Int J Mech Sci, 176: 105525. https://doi.org/10.1016/j.ijmecsci.2020.105525
Sente Software JMatPro®, (n.d.). Available from: https://www.sentesoftware.co.uk/jmatpro [Last accessed on 2014 Jan 04].