Analyzing occupational risks of pharmaceutical industry under uncertainty using a Bow-Tie analysis
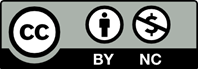
Risk analysis is a systematic and widespread methodology to analyze and evaluate risks which are exposed in many working areas. One of the Quantitative Risk Analysis (QRA) methods for risk assessment is Bow-Tie analysis which combines features of fault-tree analysis and event-tree analysis to identify the top event; its causes and consequences (outcomes); and possible preventive and protective control measures or barriers. This study proposes an occupational risk assessment approach, which is known as Fuzzy Bow-Tie analysis, for pharmaceutical industry processes and work units. The aim is to evaluate critical risks and risky pharmaceutical work units and take safety precautions against accidents which caused by risky conditions. Thus, this methodology combines the concept of uncertainty which comes from different (Decision Maker) DM’s evaluations and the whole performance of the Bow-Tie analysis for hazard identification and risk assessment. To apply and validate the proposed method, a case study is performed for pharmaceutical industry processes and work units. Based on the computed risk score, which is calculated by multiplying probability ranking and impact ranking of criterion, the risks are prioritized and some measures are suggested for management to prevent accidents occur in the industry.
[1] Attaianese, E. &Duca, G. (2012). The integrated assessment of occupational risks in a pharmaceutical manufacturing plant. Work, IOS press, 41, 1733-1738. DOI: 10.3233/WOR-2012-0377-1733.
[2] Keith, T. (1998). Encyclopaedia of Occupational Health and Safety. Fourth Edition Edited Jeanne Mager Stelman, International Labour Office, Chapter 79.
[3] Naumann, B., Sargent, EV., Starkman, BS., Fraser, WJ . Becker, GT & Kirk, GD. (1996). Performance- based exposure control limits for pharmaceutical active ingredients. American Industrial Hyjgiene Association Journal, 57: 33-42.
[4] Evelyn, N., Cristophe, R., Nathalie, B. & Alessandro, S. (2018). Chemical Risk Assessment Screening Tool of a Global Chemical Company. Safety and Health at Work, 9(1) 84-94.
[5] Binks, S.P. (2003). Occupational toxicology and the control of exposure to pharmaceutical agents at work. Occupational Medicine, 53:363-370.
[6] Shahriar , A., Sadiq, R. Tesfamariam, S. (2012). Risk analysis for oil & gas pipelines: A sustainability assessment approach using fuzzy based Bow-Tie analysis.Journal of Loss Prevention in the Process Industries, 25(3), 505-523.
[7] Khan, FI., Abbasi SA. (2001). Risk analysis of a typical chemical industry using ORA procedure. Journal of Loss Prevention in the Process Industries, 14, 43-59.
[8] Sklet S. (2004). Comparison of some selected methods for accident investigation. Journal of Hazardous Materials. 111 (1-3), 29-37.
[9] Couronneau, J.C., Tripathi, A. (2003). Implementation of the new approach of risk analysis in France. Proceedings of the 41st International Petroleum Conference, Bratislava, Slovakia.
[10] Jacinto, C., Silva, C. (2010). A semi-quantitative assessment of occupational risks using Bow-Tie representation. Safety Science, 48, 973–979.
[11] Khan FI, Abbasi SA. (1998). Techniques and methodologies for risk analysis in chemical process industries. Journal of Loss Prevention in the Process Industries, 11: 261–277.
[12] Delvosalle, C., Fievez, C., Pipart, A., Fabreg, C.J., Debray, B. (2006). ARAMIS project: a comprehensive methodology for the identification of reference accident scenarios in process industries. Journal of Hazardous Materials, 130, 200–219.
[13] Montano, D. (2014). Chemical and biological work- related risks across occupations in Europe: a review. Montano Journal of Occupational Medicine and Toxicology 2014, 9:28.
[14] Gowland, R. (2006). The accidental risk assessment methodology for industries (ARAMIS)/layer of protection analysis (LOPA) methodology: a step forward towards convergent practices in risk assessment? Journal of Hazardous Materials, 130,307–310.
[15] Khan, F. (2001). Use maximum-credible accident scenario for realistic and reliable risk assessment. Chemical Engineering Progress, 11, 56–64.
[16] Chevreau, F. R., Wybo, J. L., & Cauchois, D. (2006). Organizing learning processes on risks by using the Bow-Tie representation. Journal of Hazardous Materials, 130(3), 276. doi:10.1016/j.jhazmat.2005.07.018.
[17] Khakzad, N., Khan, F., Amyotte, P. (2013). Quantitative risk analysis of offshore drilling operations: a Bayesian approach. Safety Science, 57, 108-117.
[18] Deacon, T., Amyotte, P.R., Khan, F.I. (2013). A framework for human error analysis of offshore evacuations. Safety Science, 51 (1), 319-327.
[19] Deacon, T., Amyotte, P.R., Khan, F.I. (2010). Human error risk analysis in offshore emergencies. Safety Science, 48 (6), 803-818.
[20] Khakzad, N., Khan, F., Amyotte, P. (2012). Dynamic risk analysis using Bow-Tie approach. Reliability Engineering and System Safety, 104, 36- 44.
[21] Cockshott, J.E. (2005). Probability Bow-Ties: a transparent risk management tool. Process Safety and Environmental Protection, 83 (4), 307-316.
[22] Duijm, N. J. (2009). Safety-barrier diagrams as a safety management tool. Reliability Engineering & System Safety, 94(2), 332-341. doi:10.1016/j.ress.2008.03.031.
[23] Badreddine, A., Ben HajKacem, M.A., Ben Amor,N. (2014). A three stages to implement barriers in Bayesian-based Bow-Tie diagram. 27rd International Conference on Industrial Engineering and Other Applications of Applied Intelligent Systems, IEA/AIE 2014, 32-41.
[24] Dianous, V., Fivez, C. (2006). ARAMIS project: a more explicit demonstration of risk control through the use of Bow-Tie diagrams and the evaluation of safety barrier performance. Journal of Hazardous Materials, 130(3), 220-233.
[25] Mokhtari, K., Ren, J., Roberts, C., Wang, J. (2011). Application of a generic Bow-Tie based risk analysis framework on risk management of sea ports and offshore terminals. Journal of Hazardous Materials, 192(2), 465-475.
[26] Preeda S., Min A. (2015). Development of Risk Assessment and Occupational Safety Management Model for Building Construction Projects. World Academy of Science. Engineering and Technology International Journal of Civil and Environmental Engineering Vol.9, No.9.
[27] Agarwal, H., Renaud, J. E., Preston, E. L., & Padmanabhan, D. (2004). Uncertainty quantification using evidence theory in multidisciplinary design optimization. Reliability Engineering & System Safety, 85(1-3), 281-294. doi:10.1016/j.ress.2004.03.017.
[28] Ayyub, B. M., & Klir, G. J. (2006). Uncertainty modeling and analysis in engineering and the sciences. Boca Raton, FL 33487-2742, US: Chapman & Hall.
[29] Wilcox, C.R., Ayyub, M.B. (2003). Uncertainty modeling of data and uncertainty propagation for risk studies. IEEE Proceedings on Uncertainty Modeling and Analysis, 184–191.
[30] Bae, H., Grandhi, R. V., & Canfield, R. A. (2004). An approximation approach for uncertainty quantification using evidence theory. Reliability Engineering & System Safety, 86(3), 215. doi:10.1016/j.ress.2004.01.011.
[31] Boudraa, A., Bentabet, A., Salzenstein, F., & Guillon, L. (2004). Dempster-Shafer’s basic probability assignment based on fuzzy membership functions. Electronic Letters on Computer Vision and Image Analysis, 4(1), 1-10.
[32] Sentz, K., & Ferson, S. (2002). Combination of evidence in Dempster-Shafer theory. Technical US Department of Energy. Sandia National Laboratories.
[33] Gentile, M., Rogers, W. J., & Mannan, M. S. (2003). Development of an inherent safety index based on fuzzy logic. Process Safety and Environmental Protection, 81(6), 444-456.
[34] Markowski, A. S. (2006). Layer of protection analysis for the process industry. Lodz: PAN, ISBN 83-86-492-36-8.
[35] Salzano, E., & Cozzani, V. (2006). A fuzzy set analysis to estimate loss intensity following blast wave interaction with process equipment. Journal of Loss Prevention in the Process Industries, 19, 343-352.
[36] Abrahamsson, M. (2002). Uncertainty in Quantitative Risk Analysis—Characterization and Methods of Treatment. Department of Fire Safety Engineering. Lund University, Sweden.
[37] Ferdous, R., Khan, F., Sadiq, R., Amyotte, P., Veitch, B. (2009). Methodology for computer aided fuzzy fault tree analysis. Process Safety and Environment Protection, 87(4), 217–226.
[38] Ferdous, R., Khan, F., Sadiq, R., Amyotte, P., Veitch, B. (2010). Fault and event tree analyses for process systems risk analysis: uncertainty handling formulations. Risk Analysis: An International Journal, 31(1), 86–107.
[39] Markowski, A., Sam Mannan, M., Kotynia, A. (Bigoszewska)., Siuta, D (2010). Uncertainty aspects in process safety analysis. Journal of Loss Prevention in the Process Industries, 23, 446-464.
[40] Ferdous, R., Khan, F., Sadiq, R., Amyotte, P., Veitch, B. (2011). Analyzing system safety and risks under uncertainty using a Bow-Tie diagram: an innovative approach. Process Safety and Environmental Protection, doi:10.1016/j.psep.2011.08.010.
[41] Tanaka, H., Fan, T.L., Lai, F.S., Toughi, K. (1983). Fault tree analysis by fuzzy probability. IEEE Transactions on Reliability 32(5), 455–457.
[42] Singer, D. (1990). A fuzzy approach to fault tree and reliability analysis. Fuzzy Sets and Systems 34, 145– 155.
[43] Aqlan, F., Mustafa Ali, E. (2014). Integrating lean principles and fuzzy Bow-Tie analysis for risk assessment in chemical industry. Journal of Loss Prevention in the Process Industries, 29, 39-48.
[44] Markowski, A. S., Mannan, M. S., & Bigoszewska, A. (2009). Fuzzy logic for process safety analysis.Journal of Loss Prevention in the Process Industries,22(6), 695-702. doi:10.1016/j.jlp.2008.11.011.
[45] Bhusnure, O. G., Dongare, R. B., Gholve, S. B., Giram, P. S. (2018). Chemical hazards and safety management in pharmaceutical industry. Journal of Pharmacy Research, Vol. 12, Issue 3.
[46] Gathuru, I.M., Buchanich, J., Marsh, G., Dolan, D.(2015). Health Hazards in the Pharmaceutical Industry. Pharmaceutical Regulatory Affairs, 4:3, DOI: 10.4172/2167-7689.1000145.
[47] Kumar, P., Shukla,J. (2010). Rısk Analysis and Risk Management In Pharmaceutıcal Industry.Internatıonal Journal of Pharma World Research,Vol. 1, Issue 1.
[48] Urushihara H, Kobashi G, Masuda H, Taneichi S, Yamamoto M, Nakayama T, Kawakami K, Matsuda T, Ohta K, Sugimori H. (2014). Pharmaceutical company perspectives on current safety risk communications in Japan. SpringerPlus, 3:51.
[49] Bhowmik, D., Durai Vel, S., Rajalakshmi A.N, Sampath Kumar, K. (2014). Recent Trends in Hazards in the Pharmaceutical Industry and Safety Precaution. Elixir Pharmacy, 69, 23688-23691.
[50] Patrick T.W., Guchelaar, H., Guchelaar, H. (2003). Risk assessment in clinical pharmacy. Pharmacy World and Science; 25(3), 98–103.
[51] Anthony P. Acfield and Dr. Robert A. Weaver(2012). Integrating Safety Management through the Bow-Tie Concept A move away from the Safety Case focus. Australian System Safety Conferrence (ASSC 2012).
[52] Shuang, C., Jinqiu, H., Laibin, Z. (2016). Risk analysis of refining equipment based on fuzzy theory and Bow-Tie model. Proceedings of the 35th Chinese Control Conference July 27-29, 2016, Chengdu, China.
[53] Zadeh, L.A. (1965). Fuzzy sets. Information and Control, 8, 339-353, 1965.
[54] Zadeh, L.A. (1978). Fuzzy sets as a basis for a theory of possibility. Fuzzy sets and systems, 1, 3-28.
[55] Lin, C., Wang, M.J. (1997). Hybrid fault tree analysis using fuzzy sets. Reliability Engineering and System Safety, 58, 205–213.
[56] Lee, K. (2005). First Course on Fuzzy Theory and Applications. Springer, ISBN 978-3-540-32366-2.
[57] L.X. Wang, (1997). A Course in Fuzzy Systems and Control. Prentice-Hall International Inc.
[58] Cheliyan, A.S., Bhattacharyya, S.K. (2018). Fuzzy fault tree analysis of oil and gas leakage in subsea production systems. Journal of Ocean Engineering and Science, 3(1), 38-48.
[59] Tyagi, S., Pandey D., Tyagi, R. (2010). Fuzzy set theoretic approach to fault tree analysis.International Journal of Engineering, Science and Technology, 2(5), 276-283.
[60] Sangaiah, A., Kumar, A., Thangavelu, A. (2013). An exploration ofFMCDM approach for evaluating the outcome/success of GSD projects. Central European Journal of Engineering, 3(3), 419-435. DOI: 10.2478/s13531-012-0070-9.
[61] Tsenga, T., Konadaa , U., Kwon Y. (2016). A novel approach to predict surface roughness in machining operations using fuzzy set theory. Journal of Computational Design and Engineering, 3, 1–13.