Study of Operating Parameters on the Optimum Hydrogen Yield Through the Ethanol Steam Reforming
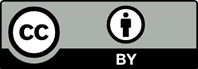
This work presents a detailed study of the effects of reaction parameters on the 7.5Ni-7.5La/Ce-Zr catalyst in catalytic steam reforming of ethanol (SRE). The study of the collective effect of reaction parameters on the product yield will help to design an efficient catalyst system for the reforming process. The catalyst morphology and properties were analysed by different techniques such as FESEM, XRD, BET, and TPR. The catalyst activity test was performed in a tubular reactor with different S/C ratios, temperatures, and flow rates. The catalyst showed an optimum hydrogen yield (3.8) and ethanol conversion (98 %) at a S/C ratio of 4.5, a feed flow rate of 2.5 g/gcat-h, and a temperature of 600 ℃. The exit flow rate of H2 is found to be 10 mmol/min at the same reaction condition. The present catalyst shows superior catalytic performance and resistance to carbon deposition during SRE.
Abd El-Hafiz, D.R. and M.A. Ebiad (2015). A study to develop nano-spray freeze dried Co/Ce–La catalyst for the production of hydrogen from bio-renewable feedstock. Journal of Natural Gas Science and Engineering, 27: 1158-1164. https://doi.org/10.1016/J.JNGSE.2015.09.060
Alberton, A.L., Souza, M.M.V.M. and M. Schmal (2007). Carbon formation and its influence on ethanol steam reforming over Ni/Al2O3 catalysts. Catalysis Today, 123: 257-264. https://doi.org/10.1016/j.cattod.2007.01.062
Alptekin, F.M. and M.S. Celiktas (2022). Review on catalytic biomass gasification for hydrogen production as a sustainable energy form and social, technological, economic, environmental, and political analysis of catalysts. ACS Omega, 7: 24918-24941. https://doi. org/10.1021/acsomega.2c01538
Bej, B., Bepari, S., Pradhan, N.C. and S. Neogi (2017). Production of hydrogen by dry reforming of ethanol over alumina supported nano-NiO/SiO2 catalyst. Catalysis Today, 291: 58-66. https://doi.org/10.1016/j. cattod.2016.12.010
Calles, J.A., Carrero, A. and A.J. Vizcaíno (2009). Ce and La modification of mesoporous Cu-Ni/SBA-15 catalysts for hydrogen production through ethanol steam reforming. Microporous and Mesoporous Materials, 119: 200-207. https://doi.org/10.1016/j.micromeso.2008.10.028
Frusteri, F., Freni, S., Spadaro, L., Chiodo, V., Bonura,G., Donato, S. and S. Cavallaro (2004). H2 production for MC fuel cell by steam reforming of ethanol over MgO supported Pd, Rh, Ni and Co catalysts. Catalysis Communications, 5: 611-615. https://doi.org/10.1016/j. catcom.2004.07.015
Hernández, I.P., Gochi-Ponce, Y., Contreras Larios, J.L. and A.M. Fernández (2010). Steam reforming of ethanol over nickel-tungsten catalyst. International Journal of Hydrogen Energy, 35: 12098-12104. https://doi. org/10.1016/j.ijhydene.2009.09.069
Li, M., Wang, X., Li, S., Wang, S. and X. Ma (2010). Hydrogen production from ethanol steam reforming over nickel based catalyst derived from Ni/Mg/Al hydrotalcite- like compounds. International Journal of Hydrogen Energy, 35: 6699-6708. https://doi.org/10.1016/j. ijhydene.2010.04.105
Liu, J.Y., Su, W.N., Rick, J., Yang, S.C., Pan, C.J., Lee, J.F., Chen, J.M. and B.J. Hwang (2016). Rational design of ethanol steam reforming catalyst based on analysis of Ni/La2O3 metal-support interactions. Catalysis Science and Technology, 6: 3449-3456. https://doi.org/10.1039/ c5cy00410a
Mondal, T., Pant, K.K. and A.K. Dalai (2015). Oxidative and non-oxidative steam reforming of crude bio-ethanol for hydrogen production over Rh promoted Ni/CeO2-ZrO2 catalyst. Applied Catalysis A: General, 499: 19-31. https:// doi.org/10.1016/j.apcata.2015.04.004
Mortensen, P.M. and I. Dybkjær (2015). Industrial scale experience on steam reforming of CO2-rich gas. Applied Catalysis A: General, 495: 141-151. https://doi.org/https:// doi.org/10.1016/j.apcata.2015.02.022
Ni, M., Leung, D.Y.C. and M.K.H. Leung (2007). A review on reforming bio-ethanol for hydrogen production. International Journal of Hydrogen Energy, 32: 3238-3247. https://doi.org/10.1016/j.ijhydene.2007.04.038
Niazi, Z., Irankhah, A., Wang, Y. and H. Arandiyan (2020). Cu, Mg and Co effect on nickel-ceria supported catalysts for ethanol steam reforming reaction. International Journal of Hydrogen Energy, 45: 21512-21522. https:// doi.org/10.1016/j.ijhydene.2020.06.001
Ong, J.L., Loy, A.C.M., Teng, S.Y. and B.S. How (2022). Future paradigm of 3D printed Ni-based metal organic framework catalysts for dry methane reforming: Techno- economic and environmental analyses. ACS Omega, 7: 15369-15384. https://doi.org/10.1021/acsomega.1c06873
Phaahlamohlaka, T.N., Kumi, D.O., Dlamini, M.W., Forbes, R., Jewell, L.L., Billing, D.G. and N.J. Coville (2017). Effects of Co and Ru intimacy in Fischer-Tropsch catalysts using hollow carbon sphere supports: Assessment of the hydrogen spillover processes. ACS Catalysis, 7: 1568-1578. https://doi.org/10.1021/acscatal.6b03102
Quan, C., Xu, S. and C. Zhou (2017). Steam reforming of bio- oil from coconut shell pyrolysis over Fe/olivine catalyst. Energy Conversion and Management, 141: 40-47. https:// doi.org/10.1016/j.enconman.2016.04.024
Sanchez-Sanchez, M.C., Yerga, R.M.N., Kondarides, D.I., Verykios, X.E. and J.L.G. Fierro(2010). Mechanistic aspects of the ethanol steam reforming reaction for hydrogen production on Pt, Ni, and PtNi catalysts supported on γ-Al 2O3. Journal of Physical Chemistry A, 114: 3873-3882. https://doi.org/10.1021/jp906531x
Trane-Restrup, R., Dahl, S. and A.D. Jensen (2013). Steam reforming of ethanol: Effects of support and additives on Ni-based catalysts. International Journal of Hydrogen Energy, 38: 15105-15118. https://doi.org/10.1016/j. ijhydene.2013.09.027
Vizcaíno, A.J., Carrero, A. and J.A. Calles (2007). Hydrogen production by ethanol steam reforming over Cu-Ni supported catalysts. International Journal of Hydrogen Energy, 32: 1450-1461. https://doi.org/10.1016/j. ijhydene.2006.10.024
Xiao, Z., Wu, C., Wang, L., Xu, J., Zheng, Q., Pan, L., Zou, J., Zhang, X. and G. Li (2021). Boosting hydrogen production from steam reforming of ethanol on nickel by lanthanum doped ceria. Applied Catalysis B: Environmental, 286:119884https://doi.org/10.1016/j.apcatb.2021.119884